Time to read: 5 min
One of the most important factors in machining is the geometry of the cutting tool, and one component of that is the rake angle. A tool’s rake angle will affect how much material can be removed, how easily chips form and break, the horsepower required to cut, and even the tool’s life. It must be noted that cutting-tool geometry is a complex topic with many nuances and special cases. However, this article will focus on describing what a cutting tool’s rake angle is, the different types of rake angles, their advantages and disadvantages, and which is better suited to specific materials.
What Is the Rake Angle for CNC Machining?
The rake angle is a pivotal part of the design of a cutting tool. It is defined as the angle of the face of the cutting tool in reference to a line that is perpendicular to the feed direction. There are three main types of rake angles:
- Positive
- Neutral (sometimes called zero)
- Negative
Various rake angles can be measured from different reference planes. However, machinability is typically measured at the true rake angle—the rake angle on which the chip slides. For single-point turning tools, this is often the side rake angle. There are generally radial rake and axial rake angles for milling cutters. See Figure 1, which illustrates the rake angle for single-point turning tools, with a positive rake angle on the left and a negative rake angle on the right.
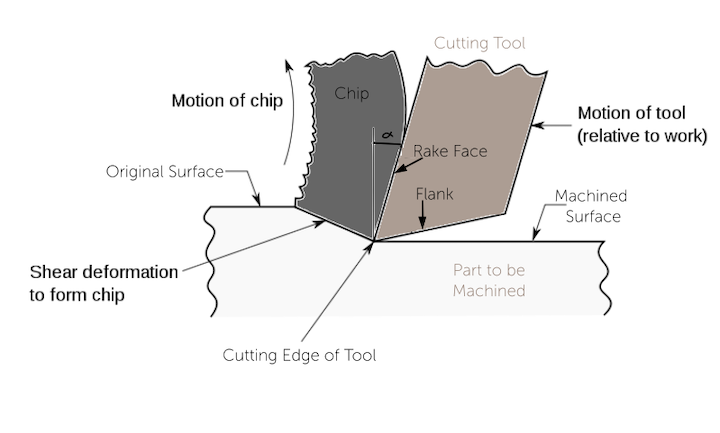
Positive Rake Angle
A tool has a positive rake angle when the sum of the flank or relief angle Figure 2 and wedge angle is less than 90 degrees. Ultimately, this means the tool has a sharper edge because it comes down to a point, and the tool face is angled toward the workpiece. This allows for the removal of material via shearing. A positive rake angle is better suited to cutting ductile materials like low-carbon steel, copper, and aluminum.
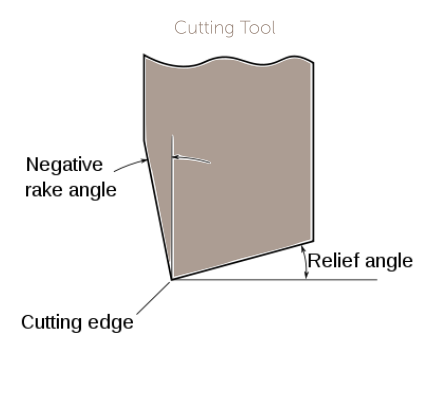
Advantages of Positive Rake Angle
The advantages of a positive rake angle include:
- Improved Chip Evacuation: Chips are directed away from the workpiece. This means that there is a reduced chance of chips being re-cut, improving tool life and part surface finish.
- Lower Power Usage: A positive rake angle results in less power usage when compared to negative and neutral rake angles. This is because of lower cutting forces due to the shearing action created by the sharp tool edge.
- High Ductile Material Removal Rate (MRR): A positive rake angle allows for increased feeds and speeds, resulting in a higher MRR. This is primarily due to the reduced cutting forces experienced.
Disadvantages of Positive Rake Angle
The disadvantages of a positive rake angle include:
- Increased Wear: The cutting edge has a sharper wedge angle when compared to negative or neutral rake angles. This means there is less material supporting the cutting edge. This ultimately results in the tool wearing more quickly and being more susceptible to sudden shock loads.
- Poor Chip Breakage: Positive rake angles result in continuous chips that are generally harder to break when compared to chips formed by neutral and negative rake angles.
Negative Rake Angle
A tool has a negative rake angle when the sum of the flank and wedge angle is larger than 90 degrees. This means the tool has a supported cutting edge because it has a large wedge angle when compared to a positive rake angle tool. These types of tools also remove material using a compressive and shearing action as the tool plows through the material. A negative rake angle is better suited to cutting brittle materials like high-carbon steel.
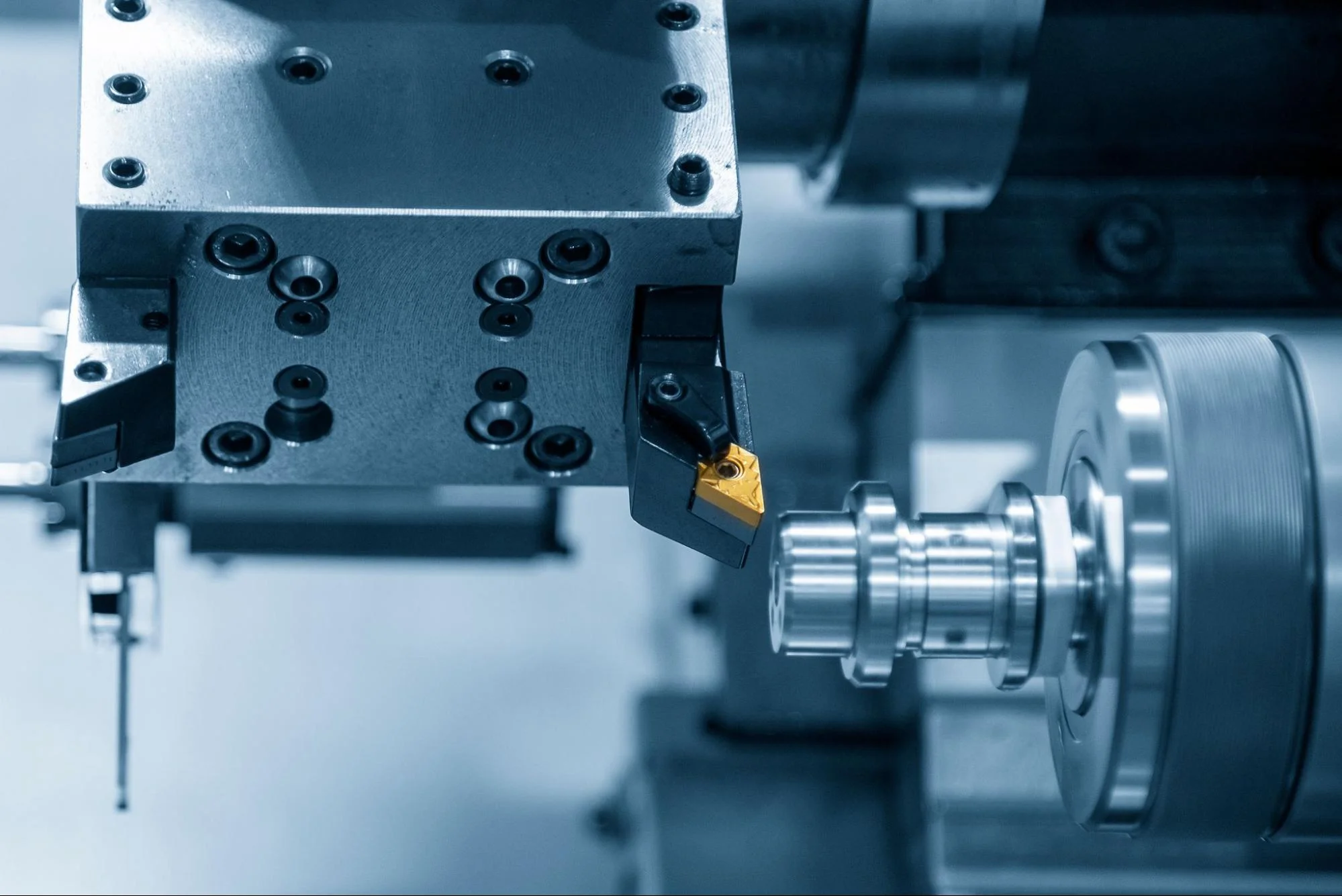
Advantages of Negative Rake Angle
The advantages of a negative rake angle include:
- Stronger Cutting Edge: The reinforced nature of a negative rake angle tool means that the cutting edge is more resistant to wear and shock loads.
- High Brittle Material Removal Rate (MRR): Negative rake angles are preferred for brittle materials as they can remove large amounts of material without excessive wear on the tool.
- Better Chip Removal: While a negative rake angle does not evacuate chips as well as a positive rake angle, the chips it does produce are generally thicker and tend to break more easily.
Disadvantages of Negative Rake Angle
The disadvantages of a negative rake angle include:
- Higher Power Usage: A negative rake angle tool will require much higher cutting forces due to increased shear deformation and increased friction. This ultimately results in increased power requirements when compared to positive and neutral rake angle tools.
- Increased Heat Generation: Higher amounts of heat are generated at the cutting edge of negative rake angle tools. This is primarily due to the way the material is compressively sheared off. This increased heat build-up can reduce the material removal rate and increase tool wear.
Neutral Rake Angle
As the name suggests a neutral rake angle, or zero rake angle, refers to a cutting face that is perpendicular to the direction of the feed. A neutral rake angle is not the most optimal configuration but can have better properties when compared to negative rake angle tool geometries.
Advantages of Neutral Rake Angle
The advantages of a neutral rake angle include:
- Ease of Manufacture: A tool with a zero rake angle is simple and therefore easy to manufacture. This also means that these tools are generally cheaper when compared to more complex negative and positive tool geometries.
- Sharpening: Sharpening a zero rake angle tool is trivial compared to a negative or positive rake angle. Coupled with its low cost, this makes it a good option for beginners and cost-conscious machinists.
Disadvantages of Neutral Rake Angle
A disadvantage of a neutral rake angle is chip evacuation. The chips formed during cutting will cause cratering on the cutting face as the chips are not effectively removed from the cut. This also reduces machine efficiency and increases power consumption.
Rake Angles for Different Materials
Choosing the correct rake angle for your specific application can be challenging as it depends on a number of factors, including:
- Material: Brittle materials generally require a negative rake angle, whereas ductile materials are better suited to a positive rake angle.
- Machining Strategy: The type of machining can determine the optimal rake angle. Anegative rake angle might be better suited to finishing. However, for rough cutting, a positive rake angle is able to remove more material.
- Production Volumes: If high production volumes are required, a tool with improved edge strength and durability is better suited.
- Machine Horsepower: Higher machine horsepower means that tools can be pushed to their limits, resulting in larger MRR.
Table 1 below lists some common materials and their generally recommended rake angles. However, it is always best to engage with a tool supplier for the optimal tool.
Material | Rake Angle (degrees) |
Aluminum | Positive 20 |
Titanium | Positive 10 |
Inconel® | Positive 10 |
Low-Carbon Steel | Positive 5 |
High-Carbon Steel | Negative -5 |
Table 1: Common Materials and Their Recommended Rake Angles
If you are looking for complex CNC machined parts at ridiculous speeds, create a free account with Fictiv or upload your design for a free, instant quote. Our team of experts understands the fine balance between all the above-mentioned factors and can produce machined parts with excellent surface finish precision without you ever having to worry about which rake angle is best suited for your application.