Time to read: 4 min
Do you love the customizability, speed, ease, and simplicity you get with 3D printing but dislike the roughness of the resulting parts? Well, there are a few common finishing methods to smooth out 3D printed parts, to give you a pleasing aesthetic, along with the production benefits mentioned above.
One of the common types of 3D printing is MJF or Multi Jet Fusion — an industrial 3D printing process where powdered thermoplastic is infused with ink that promotes the absorption of infrared light to fuse the inked areas together. The MJF printing process allows for printing parts up to 10 times faster than other printing methods on the market today. A raw, MJF 3D printed part is fit for end-use but can have a rough, slightly porous surface finish that feels like fine grit sandpaper.
Vapor smoothing is a finishing technique for MJF 3D printed parts that provides a more aesthetically pleasing surface. Read on to learn more about vapor smoothing 3D printed parts and why it’s a good option for MJF 3D printed parts.
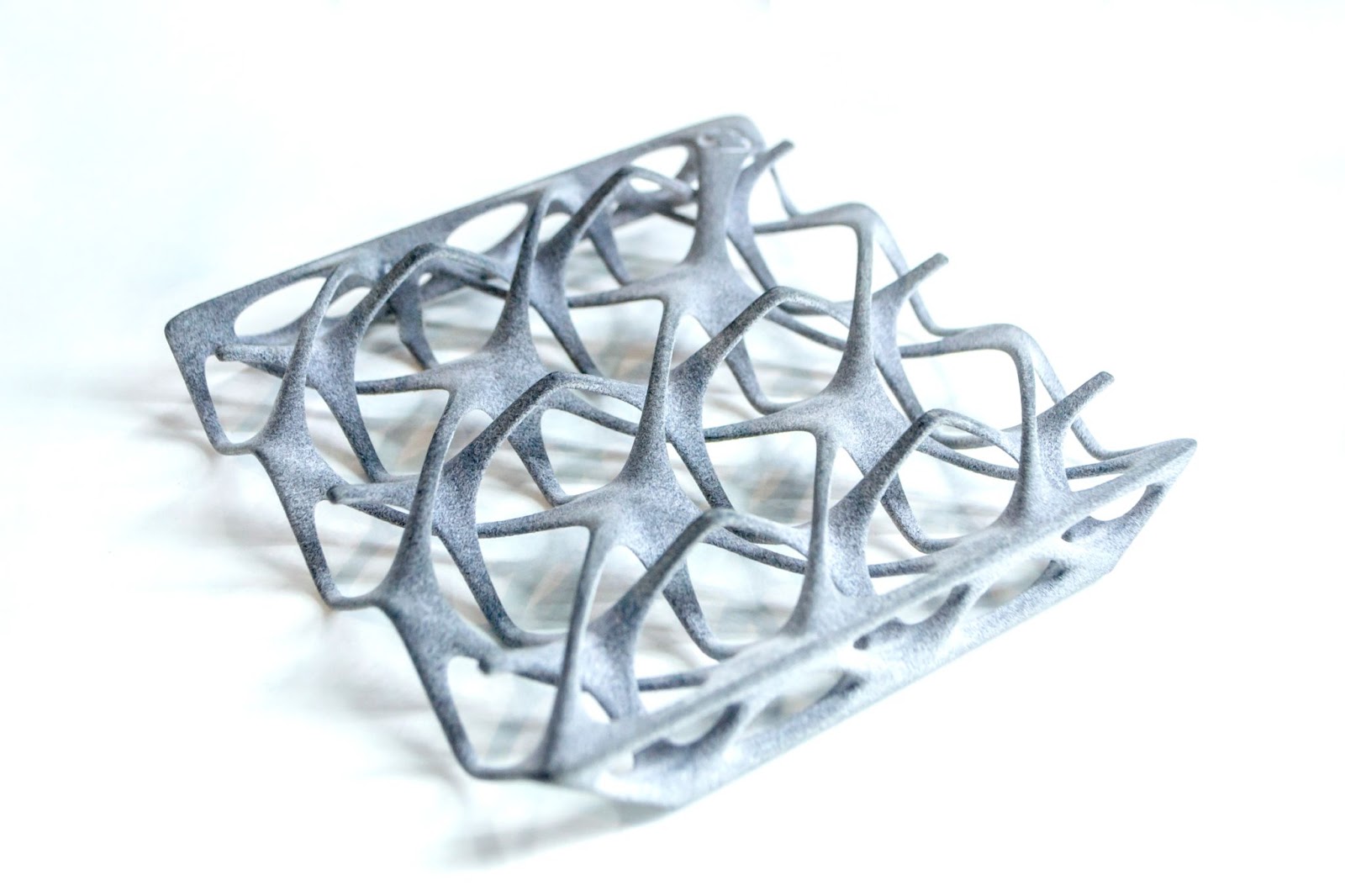
What is Vapor Smoothing and How Does Vapor Smoothing Work?
Vapor smoothing is a finishing process for 3D printed parts that uses a vaporized solvent to smooth the surface of a printed part without adding or removing material. This process gives parts an injection-molded look and feel without the injection molding costs.
The vapor smoothing process begins by placing unfinished parts in a chamber (or a vapor smoothing machine). The chamber is then flooded with chemical vapor that encapsulates every surface of the part, which makes it a non-line of sight process — meaning vapor smoothing alters part surfaces that cannot be seen, which differentiates it from grinding or bead blasting.
When the chemical vapors make contact with the part’s surfaces, a reaction occurs called chemical melt. This chemical melt reaction smooths out the rough surface of the part by leveling the peaks and valleys left by the printing process. This leveling occurs when the surface material liquefies, flows into low points, and resolidifies as a more even surface.
This chemical melt process also provides these benefits:
- The chemical melt process doesn’t remove a significant amount of material like other smoothing techniques do (i.e. bead blasting or sanding) — the total material loss is much less than 1%
- The chemical melt process also provides a shiny surface finish
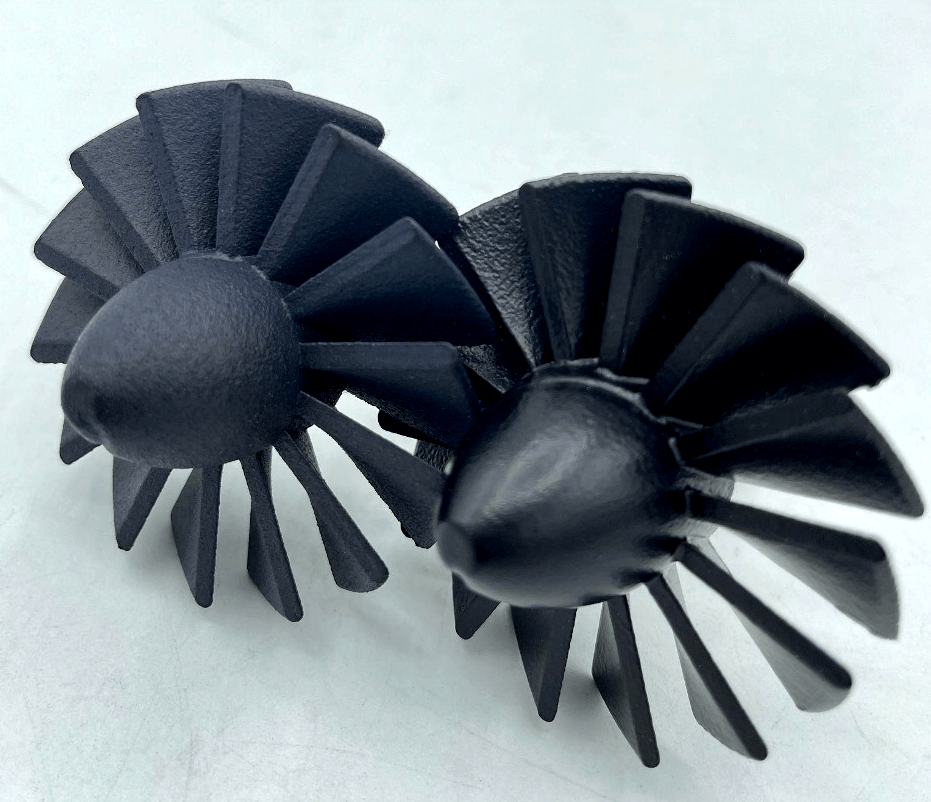
Does Vapor Smoothing Create a Hydrophobic Surface?
The vapor smoothing process also creates a hydrophobic surface that causes water to bead up and roll off of the part. This hydrophobic characteristic is a result of the reduction in surface roughness that would otherwise cause droplets of liquid to fill the peaks and valleys.
Vapor smoothing also improves the surface appearance of printed parts. Vapor smoothing is used to reduce or remove visual layer lines and natural imperfections that occur during printing, leaving a smooth, glossy finish — smoothing a raw MJF part also gives it a deeper color.
Pro-tip: Fictiv offers MJF 3D printing in grey or black.
Does Vapor Smoothing Increase Strength?
While the jury is still out on whether or not vapor smoothing increases a part’s mechanical strength, it does provide some benefits to mechanical properties. Studies from AMT have shown that vapor smoothing 3D prints improves the Elongation at Break (EAB) and tear resistance, without a sacrifice in ultimate tensile strength. This is a logical outcome since the smoothing nature of the chemical melt process reduces the stress concentrations at rigid peaks and valleys naturally found on the surface of an MJF 3D printed part.
Vapor Smoothing for the Medical Industry – An Innovative Application
Vapor smoothing has unlocked quick medical device prototyping thanks to its ability to provide injection molding quality surface finishes with the speed and simplicity of additive manufacturing. The hydrophobic nature of a vapor smoothed, 3D printed part not only repels water but also prevents bacteria penetration and makes parts easy to clean and sanitize — which are all key to the medical industry sector. We saw these characteristics factor in heavily during the COVID-19 panemic when many companies rushed to find alternative materials for PPE. Some found success with 3D printed PPE using vapor smoothed PA 12 (aka Polyamide 12 or Nylon 12), for example.
What is Vapor Smoothing Not Suitable for?
While vapor smoothing is an excellent process for most MJF 3D printed parts, many materials from different processes can be vapored smoothed including: PA 12, PMMA, TPE, TPE, PA6, PLA, and others. But vapor smoothing is not suitable for all materials, so check your material supplier’s data sheet or consult with a materials expert at your supplier before specifying the finish requirement.
Additionally, vapor smoothing may not be appropriate for all geometric features or surfaces. Remember that vapor smoothing is not based on line of sight, so exercise caution when specifying vapor smoothing for parts with these features:
- Hinges
- Sharp Edges
- Small, Intricate Details or Features
Sourcing Simplified – Start Your Next Project With Fictiv
At Fictiv, we are here to help source all your custom manufactured parts, and we have a variety of finishing capabilities, including vapor smoothing for Multi Jet Fusion parts! Coupled with our high quality and quick lead times, look no further than Fictiv as your strategic sourcing partner for all your 3D printing and finishing needs.
Fictiv is your operating system for custom manufacturing that makes part procurement faster, easier, and more efficient. In other words, Fictiv lets engineers, like you, engineer. Create an account and upload your part to see what our instant quote process, design for manufacturability feedback, and intelligent platform can do for you.