Time to read: 6 min
CNC or Computer Numerical Control is, by itself, useless. Without hardware to execute the commands, CNC is nothing more than an array of vectors stored on a drive. Once CNC is married to a machine operation, however, the manufacturing possibilities are practically limitless!
What is CNC?
What exactly is Computer Numerical Control? Essentially, it’s when a computer generates the coding for all the paths, geometries, patterns, and tooling that a machine will use to remove or add material. CNC is a powerful evolution of numerical control, or “NC”. NC requires a human programmer to figure out the tool paths to create the final product. Both NC and CNC operate with cartesian coordinate programming, meaning they create tool paths using X, Y, and Z positions using what is known as g-code.
Both CNC and NC are applications, and should not be confused with operations. Operations include milling and turning, while the applications dictate the way those operations are performed.
Milling
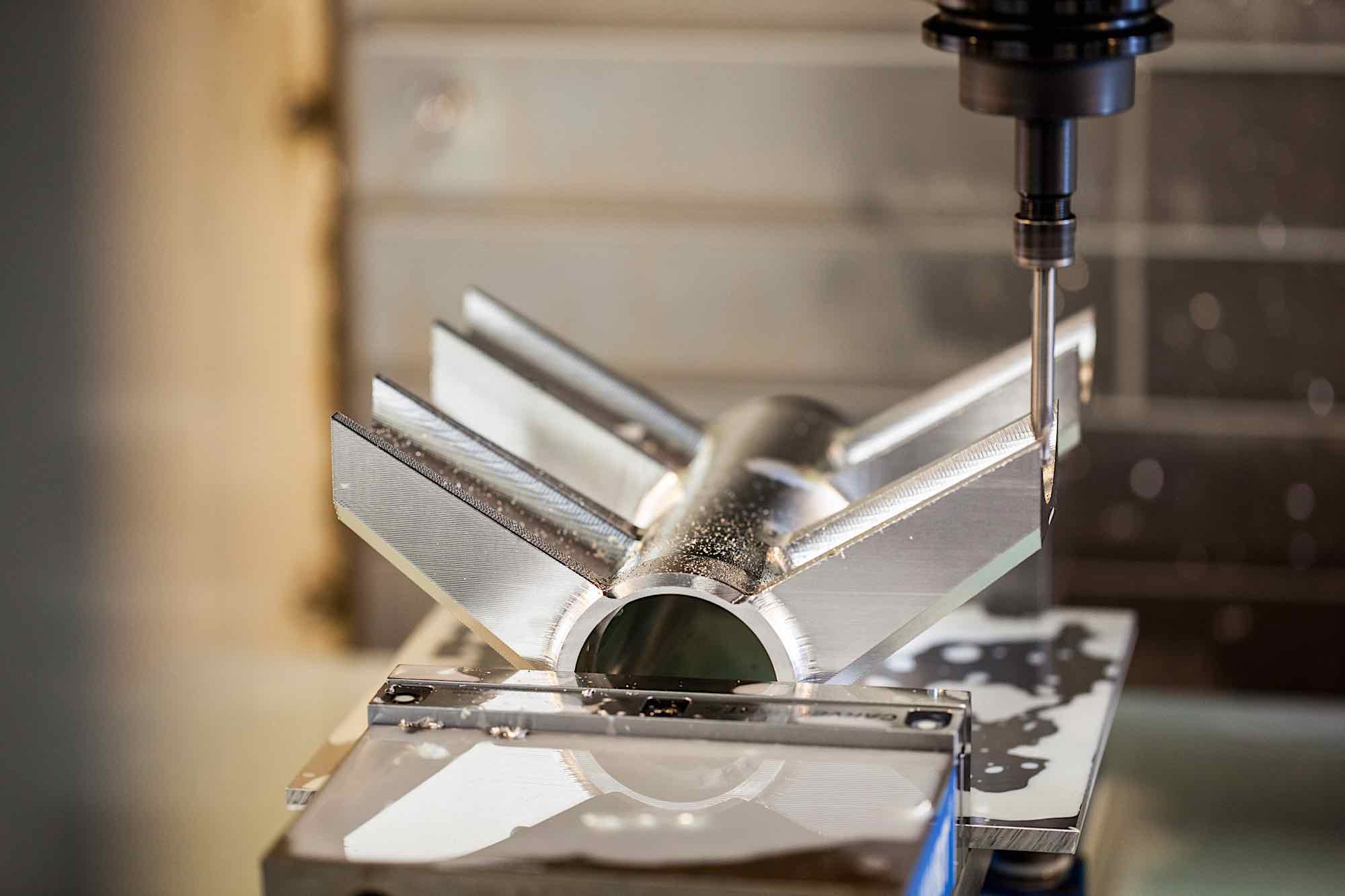
The most common operation associated with CNC is milling, which is the process of removing material from a fixed part using spinning tooling — for example, creating wrench flats on a shaft. CNC milling begins with a computer generating a tool path from a CAD model that identifies the material to remove, the material to avoid, and any tooling changes if applicable. This computer-generated g-code tells the head of the machine where to move, and how to move linearly along the X, Y, and Z planes. Depending upon the number of features and setups required, CNC milling can be quite a time-consuming process.
3-axis vs. 5-axis CNC machines
The milling process above describes a 3-axis CNC milling process, but advancements in technology have created 5-axis CNC machines. These machines not only move linearly along the X, Y, and Z planes, but can also rotate about the A, B, and C axes. This additional range of motion enables more efficient run times, creates more complex parts, and can perform single setup operations that simply cannot be done by human hands. If the part requires a flat surface or a series of blind holes, CNC milling is the way to go!
Turning
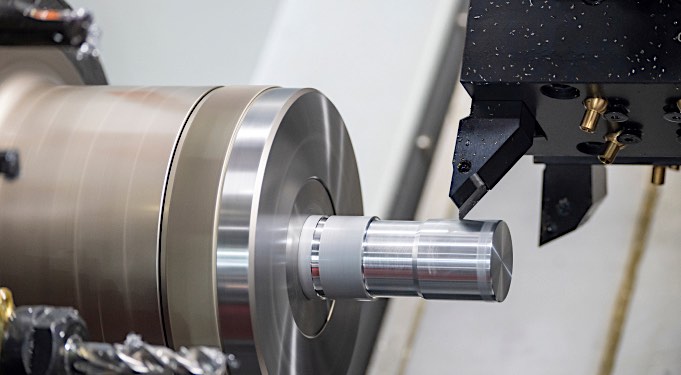
Turning, or machining by lathe is different from milling because it only utilizes two planes: the X and Z. X dictates the position along the part (typically left to right), and Z articulates distance from the center of rotation. Since the height is a constant for this operation, there is no control for Y-axis movement. Turning is used when a part needs absolute concentricity. Table and chair legs, shafts with varying diameters, and rollers are commonly machined via lathe.
While the part is stationary in a milling operation, when turning, the part is placed in a chuck vice so it spins while the tooling remains stationary. G-code tells the chuck how fast to spin, and tells the tooling where to move laterally and how deep to cut into the material during rotation.
Getting the g-code right is especially critical when turning patterned geometries like external threads. Threads need absolute precision in timing and depth to achieve a perfect, repeatable outcome.
Laserjet and Waterjet Cutting
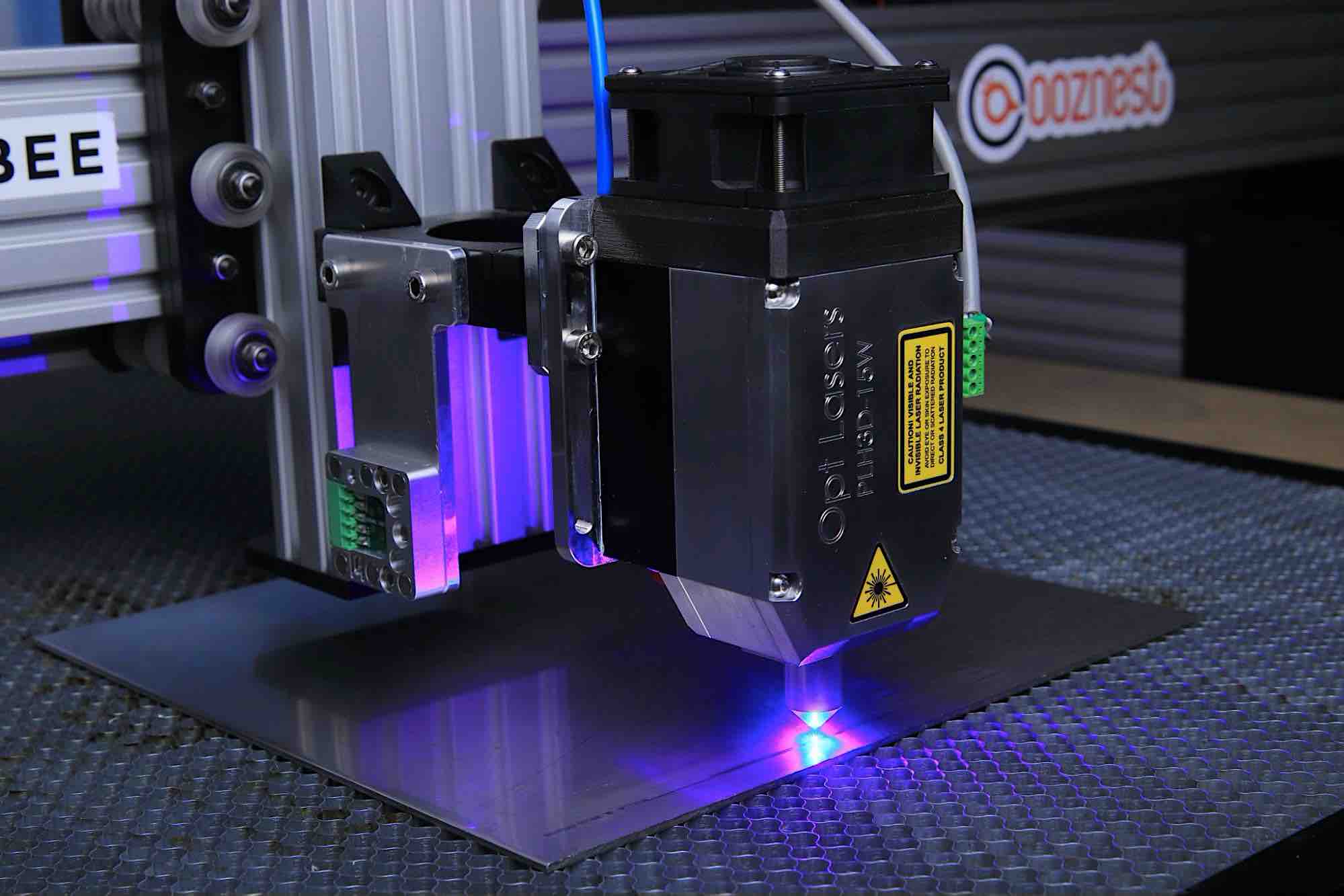
If a geometry is based only in the X and Y plane, laserjet or waterjet becomes the operation of choice — assuming the material is only 12 inches thick or less if you’re using a waterjet. For these machines, the control code is generated by a process called nesting, where the part geometries are placed into a 2D software that positions them for maximum coverage and minimal scrap.
The CNC generates the cut lines and how to move between them. Once the material thickness is provided to the machine, the head’s path follows the given coordinates. The CNC program also powers the head on or off as it moves to cut different sections of the part.
Jet cutting is quick and cost-effective but comes with some drawbacks. With laserjets, if the cut-out is large enough, it may become warped due to heat from the laser, or from imperfections in the material. Meanwhile, waterjets have what is known as a “Kerf,” which means the water can only penetrate so deep before it loses pressure and creates a slope along the bottom seam of the cut. This creates rough edge finishes and can require post-processing to clean up.
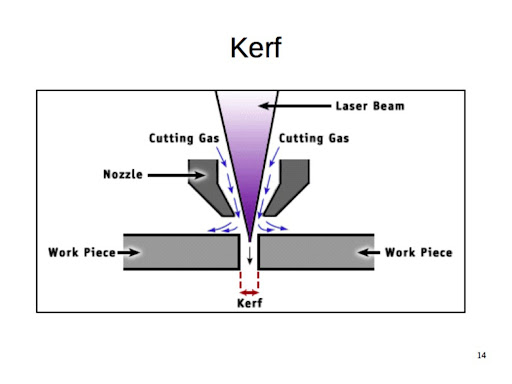
If the waterjet has a “tilt head”, then most of the kerf can be removed, but it doesn’t eliminate the rough finish of the cut. Waterjets and laserjets work only in 2D, like puzzle pieces, or through-hole patterns. If a part’s geometry is only in the X and Y planes, and a precise finish is not a requirement, then using laser or waterjets is a great option to blast parts out super fast!
Electrical Discharge Machining (EDM)
EDM, or electrical discharge machining, is a less common method of manufacturing as the machines have a relatively high up-front cost and high operating costs. EDM is used when an ultra-high precision fit is required that milling or jetting cannot achieve. It utilizes electrodes that have been machined into a specific shape, to slowly erode, or “spark”, microns of material away. Imagine a completed puzzle that would be almost impossible to see the lines between each piece.
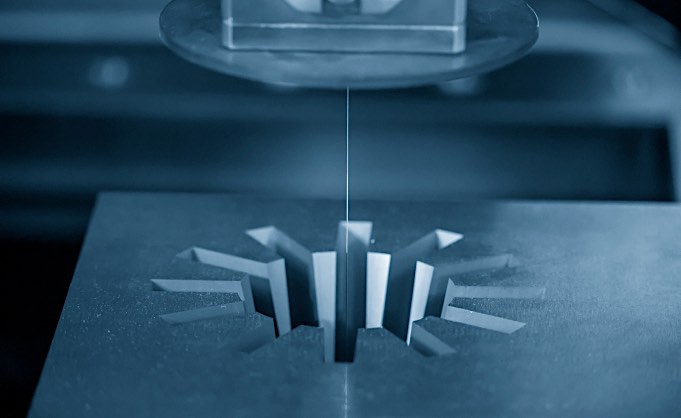
Various materials can be used as electrodes; copper, brass, tungsten alloys, and graphite are among the most common. This adds additional production time since the electrode needs to be machined to begin or a new one made once the electrode wears.
Each electrode has its own unique properties depending on the job or budget. Brass and low-cost alloys are cheaper and easier to machine, but can wear out quickly and have less conductivity. Tungsten (and its alloys) provide excellent conductivity and significant erosion resistance, making it the perfect candidate for long-term use.
The CNC is utilized by locating the electrode in the X and Z planes, then quickly raising and lowering in the Y plane, as well as telling the machine to turn the charge on or off. The precision of motion required and the complex toolpaths would prove too difficult to do by hand.
3D Printing
Another use for CNC is with fused deposition modeling (FDM) 3D printers. Note that this manufacturing method stands apart from the rest because it’s an additive manufacturing method, as opposed to the subtractive methods elsewhere in this article. It creates parts by adding material, rather than cutting material away from a workpiece, significantly reducing waste in the process.
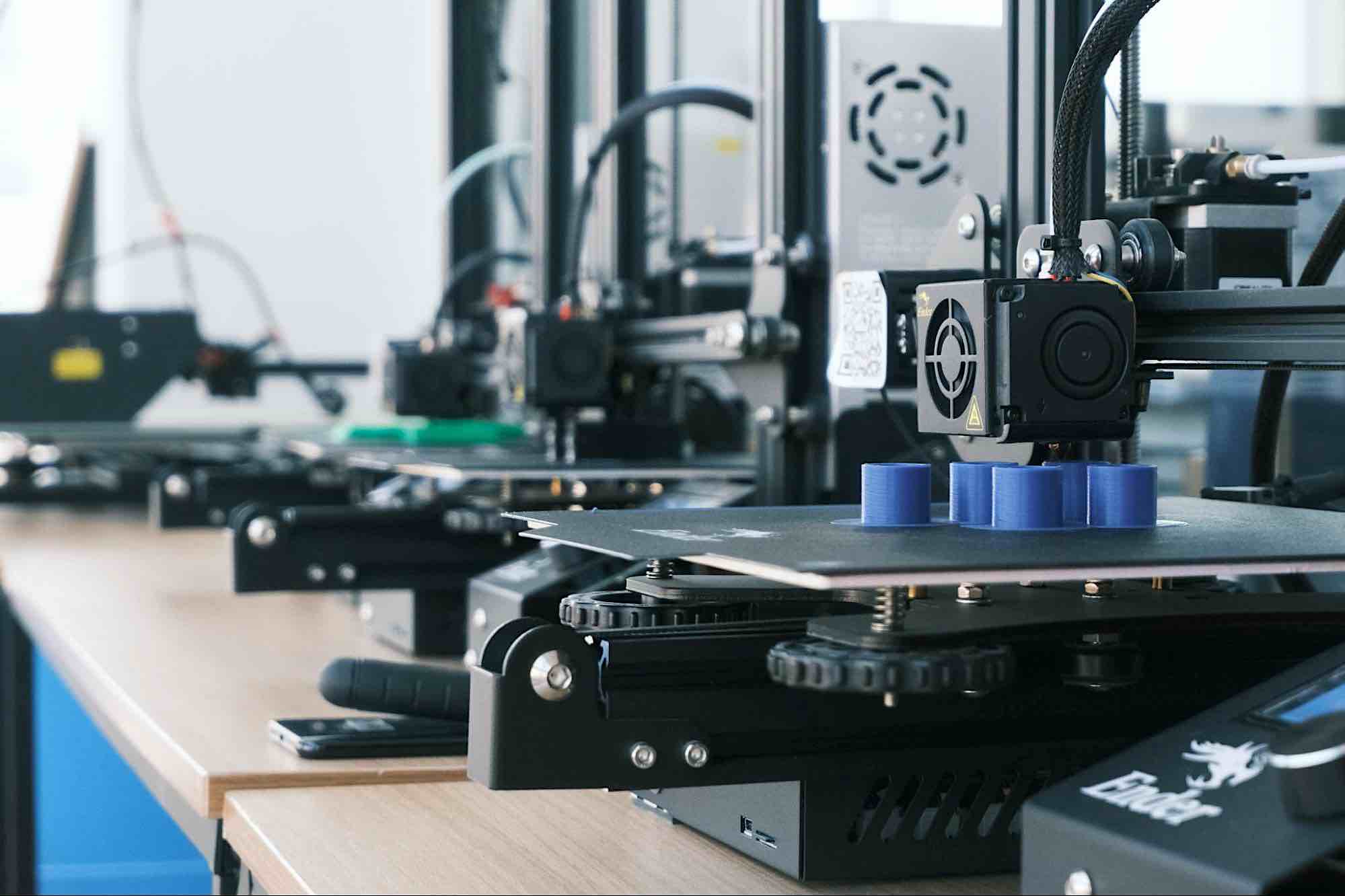
FDM printers utilize g-code to tell the print nozzle exactly what position to be in, and how to get there. Additionally, 3D printing requires an additional variable, flow, to be introduced into the code. The flow code must tell the motor how far to push out or retract filament, given the speeds set by the software.
The Applications for CNC are Endless
Fundamentally CNC does the same thing for every machine — control the output of the tooling and tell it where to go and how to get there. Given the flexibility and capability of this technology, new, innovative uses of CNC are being discovered all the time. In recent years CNC has enabled gardening robots, automated 3D scanning, new construction techniques, and automated warehouse operations!
Everything from simple two-dimensional patterns to ultra-complex machined components can be made using CNC. If there is a point of action that follows a path, geometry, or pattern, CNC is there to expedite the process.
Have questions about Fictiv’s CNC capabilities? Not a problem! Our team has experts on CNC machining and 3D printing, and they’re here to help you find the right solution. Create an account today, then upload your part and we’ll help you find the right process for your project.