Time to read: 5 min
Color matching for injection molding makes it possible to get plastic parts in a specific color or combination of colors. That’s important if you’re designing parts that need to look a certain way, whether it’s for aesthetic appeal, safety reasons, or to match a larger assembly. Perceptions of color are subjective, however, and the way that people see color depends on the light source, viewing angle, and their own visual acumen. The presence of strong nearby colors can also affect color perception.
If you’ve ever painted a room and brought a paint chip home from the store, you probably know this from experience. If the store was brightly lit and your room at home was dark, the paint chip won’t look the same. Taping the paint chip to the wall and walking around the room to look at it can also change your perception of the paint chip’s color, depending on where you stand. If the tape holding the chip is bright blue instead of light brown, the chip’s appearance can change again.
Fictiv can help you get injection molded parts with accurate and consistent colors. Our manufacturing partners offer a choice of plastic coloring methods and can even support multi-color injection molding, a process where two or more colors or materials are injected simultaneously into a mold. If you need painted parts instead, you can get that with color matching as well. Keep reading to learn more or create a Fictiv account and request a quote.
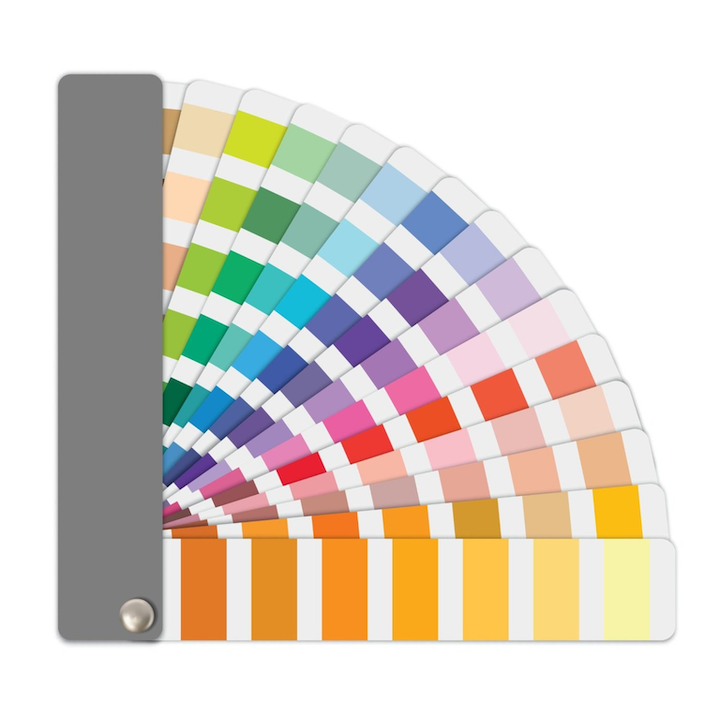
Injection molders and material suppliers have colored chips that are similar to the ones you get when you pick out paint for a home improvement project. Typically, these chips consist of a white background with Pantone colors, each with an alphanumeric identifier. In Europe, the RAL system is used. Both systems provide a standardized way to identify, describe, and match colors. With injection molding, there are also specialized references for colors with a surface finish that’s glossy or textured, since the type of finish can affect color perception.
As a part designer, choosing the right color is important, but so is getting accurate color when you receive part samples or production volumes. Understanding color matching for injection molding helps, and there’s a role to play for both the molder and the designer. You might not have a spectrophotometer for color measurement, but you can still use Pantone injection molding references to specify colors. You can also perform physical comparisons of color chips against samples under carefully controlled conditions (like in a lightbox).
You can also control injection molding costs with some of the design decisions that you make. For example, can your plastic parts use an existing Pantone or RAL color, or do you need a custom color? Stock colors cost less and, in the case of the Pantone Matching System (PMS), you have approximately 2000 choices. With a custom color, your molder will probably have to work with a material supplier, and they’ll both need to perform color testing.
Even if you use a stock color, there’s still color matching involved to ensure that the color of your injection molded parts matches the color specified in your design. You’ll also want to monitor that plastic parts in the same batch (or across batches) to ensure a consistent color.
Molding Colors and Painting Parts
There are several ways to add color to injection molded plastic. Each has its advantages and disadvantages, and some are more cost-effective than others, depending on part volume. Injection molders can use pre-formulated resins, masterbatch colorants, or mix pigments and uncolored pellets together. They can also paint parts after injection molding. No matter the method, accurate color matching and color consistency are cosmetic goals for every project. For food or medical applications, you may also need to ensure that both the plastic and the colorant are FDA-compliant.
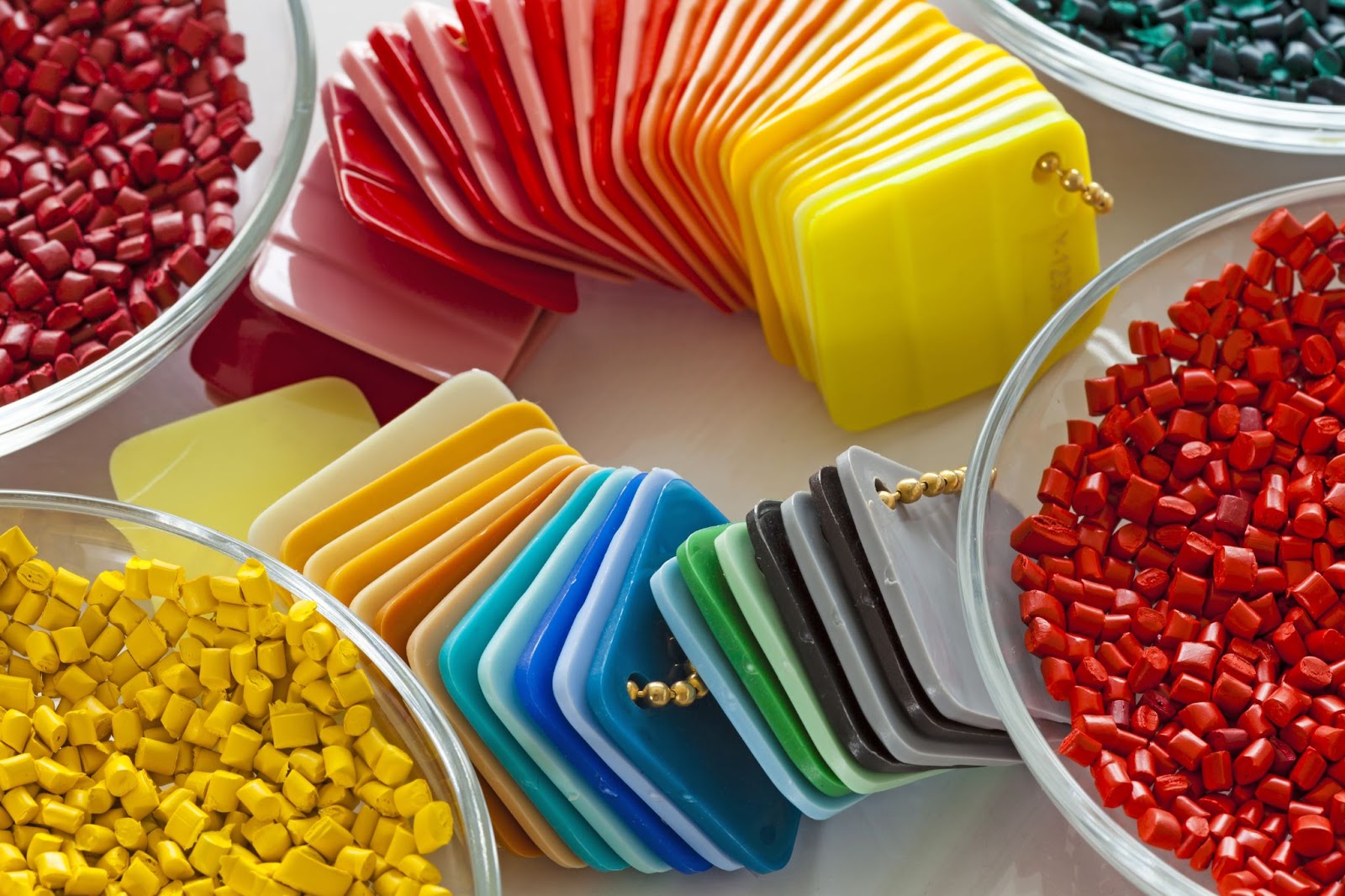
Pre-Formulated Resins
Compounders sell injection molding materials where the granules fed into an injection molding machine already contain pigments. In other words, there’s no mixing required at the machine or before molding. Pre-compounded resins provide fairly consistent color between batches, but they’re only cost-effective for high-volume injection molding. That’s because pre-formulated resins typically come with the highest compounding costs per unit of measure, usually kilograms (kg).
Masterbatch Colorants
Masterbatch colorants can also be used to add color to plastic parts. These liquid colorants are highly concentrated, and the ratio of the uncolored pellets to the masterbatch colorant is 24:1. The advantages of using color concentrates for plastics are twofold. First, liquid color provides consistent results. Second, the compounding costs per kilogram are relatively low. Masterbatch colorants are only economical for very high volumes, however, and they often have a minimum order quantity (MOQ) of two metric tons.
Machine Hopper Mixing
Molders can also mix uncolored pellets with colored pigments in the injection molding machine’s hopper. This rotating drum is where materials are poured before injection molding begins. The advantages of machine hopper mixing are relatively low costs and support for low-volume injection molding. Potential disadvantages include: inconsistent mixing due to weak electrostatic attraction, pigment burning that produces black spots on parts, and humidity issues. By using a sealed system from the drier to the hopper to the machine barrel, however, it’s possible to keep moisture from entering the material.
Painting Parts
Painting does not occur before or during the injection molding process. Instead, it occurs after molding is complete. Spray painting is the simplest option and can use self-curing paints that air dry. Powder coating applies powdered plastic and requires curing with ultraviolet (UV) light. Silk screening is used when parts need multiple colors and provides an alternative to multi-color injection molding.
Painting has downsides, however. As a form of post-processing, it adds costs and extends lead times, and there can be adhesion issues as well. Painted parts can also fade, though this is an issue for colored plastic parts as well. In general, painting is not recommended if the molding process can achieve a color match.
Here’s a quick breakdown of the three ways to add colors during injection molding.
Method | Mixed By | Compounding Cost | Part Volume |
Pre-Formulated Resins | Material Supplier | High | High |
Masterbatch Colorants | Injection Molder | Lower | Very High |
Machine Hopper Mixing | Injection Molder | Lowest | Low |
Color Matching, Color Consistency, and Injection Molded Parts
When you receive samples of injection molded parts, you should compare them to the values (Pantone or RAL) in your design. For best results, use a lighting booth and remove all color pollution from the area — both when you choose the color and check your part samples. You can also put the part sample and the color chip within a neutral-colored frame to eliminate any shaded areas.
Of course, if you didn’t use a light booth when you first selected a color, what you see now may look different. Pantone injection molding references that are old or worn can also cause discrepancies, so make sure you’re working with accurate references!
Before starting your next plastics project, consider the importance of color and what you need to achieve within your design. Whether you’re using part color for beauty, safety, consistency, or something else, Fictiv provides design for manufacturability (DFM) assistance that can ensure your project is a success. You’ll get DFM feedback when you receive our response to your request for a quote, and we’ll support you every step of the way.
To start your injection molding journey, create a Fictiv account today.