Time to read: 5 min
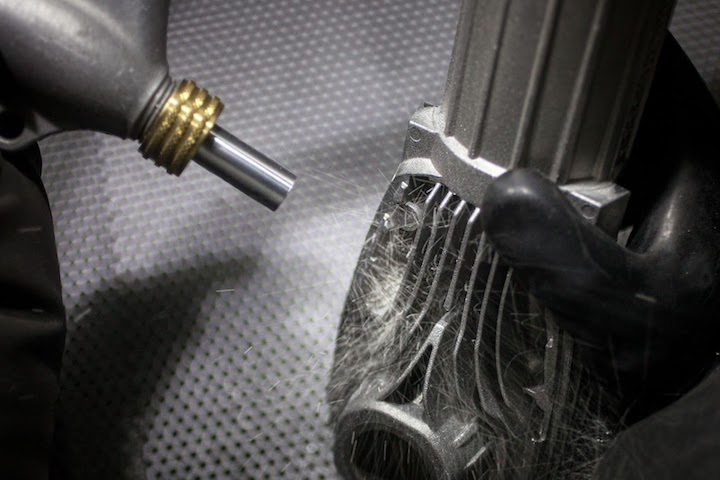
It’s a given that you need to take your time to perfectly CNC machine a part. But what happens afterwards? Freshly machined parts are covered in machining marks and have edges so sharp that you could use them to carve your overcooked turkey at Thanksgiving dinner — but this is where bead blasting is useful! Bead blasting provides a uniform finish and knocks down those sharp edges all in one process.
In the article, we’ll give you the rundown on everything you need to know about bead blasting and how you can apply this knowledge to your products.
What is Bead Blasting?
Bead blasting is a mechanical process used to create a desired surface finish or surface texture on parts, whether they are urethane cast, CNC machined, 3D printed, or injection molded. The process of bead blasting is carried out with a machine that propels a stream of media at high speeds onto the part surfaces using compressed air. Typically, an operator directs the flow of media on the part, and parts can be masked so certain surfaces are not impacted by the bead blasting. The resulting finish is controlled by the size and shape of the media, the pressure of the air, and the angle of the nozzle to the part.
Bead blasting, or blasting, is also called media blasting because it can use a variety of different media depending on your end goal. Media blasting is typically called out as the name of its media as well — for example, sand blasting, walnut shell blasting, and glass bead blasting.
The process is similar no matter what kind of media is used, and depending on the media, it affects the surface in different ways. Aluminum oxide sandblasting is highly abrasive and can easily strip paint, while shot peening — which utilizes small metal “shot” — results in a work hardened surface that is stronger and more resistant to cracks, fatigue, and corrosion.
When is Bead Blasting Used?
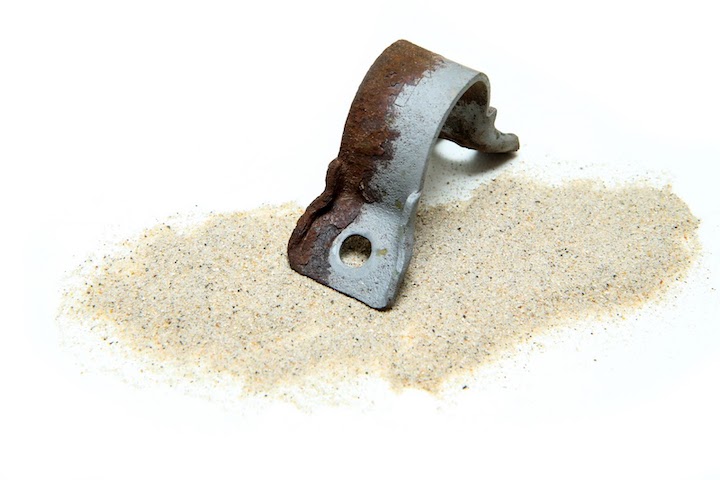
Bead blasting is used to quickly remove coatings or corrosion, clean up cosmetic defects, prepare surfaces for coatings, deburr surfaces, modify machined surface finishes, and improve the uniformity of surfaces for cosmetic and mechanical needs. For example, the machining marks from an end-mill can leave unsightly swirl tool marks with scratches and nicks. By bead blasting the surface, you can achieve a satin-like surface that covers up the imperfections and leaves a clean and professional aesthetic finish.
What Media is Used in Bead Blasting?
There are several types of media utilized in bead blasting processes. What follows are the main groups of media and several different variations that can be used to achieve your desired purpose.
Glass Beads
Glass beads are spherical beads typically manufactured from lead-free, soda-lime glass which allows for non-aggressive cleaning and micro-peening to create a bright satin finish. Glass beads come in a variety of grain sizes depending upon the starting condition of the part, and the aggressiveness required to achieve the desired finish. Glass beads are easy to re-use and can be recycled.
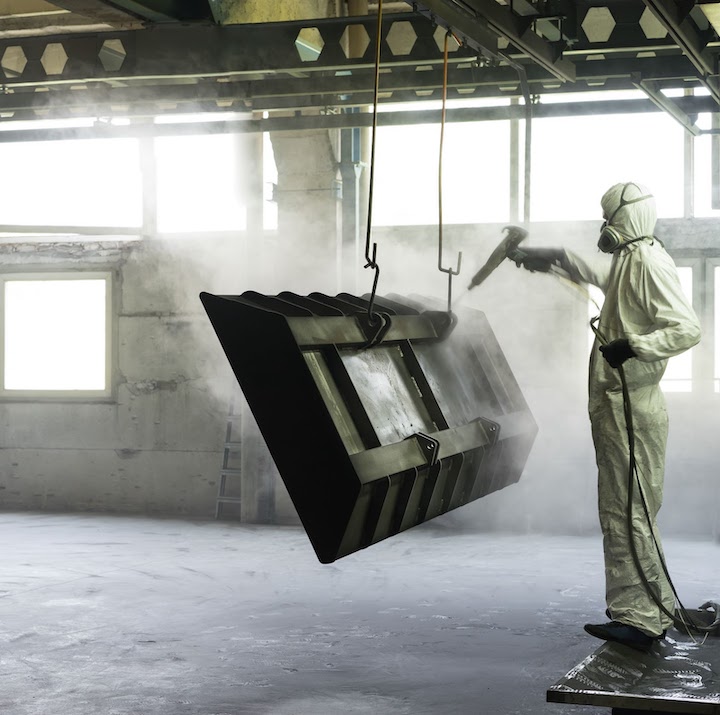
Sand
The typical sandblasting material is small particles of aluminum oxide, which have sharp and angular edges that result in an aggressive material removal. Sandblasting is typically aggressive enough to cause dimensional distortion and material removal, if you’re not careful. This method is typically used to remove contaminants embedded in surfaces, corrosion, paint, and other coatings, and make as-machined surfaces uniform. Sand media is also highly recyclable, though contamination in the media is common due to the high material removal rate.
Pro-Tip: Don’t allow cross-contamination of media for different metal families. For example, do not use media that came into contact with stainless steel on aluminum parts and vice-versa. Cross-contamination may cause issues such as intergranular corrosion, issues with plating adhesion, or loss of integrity in metal joining practices such as welding or brazing.
Shot
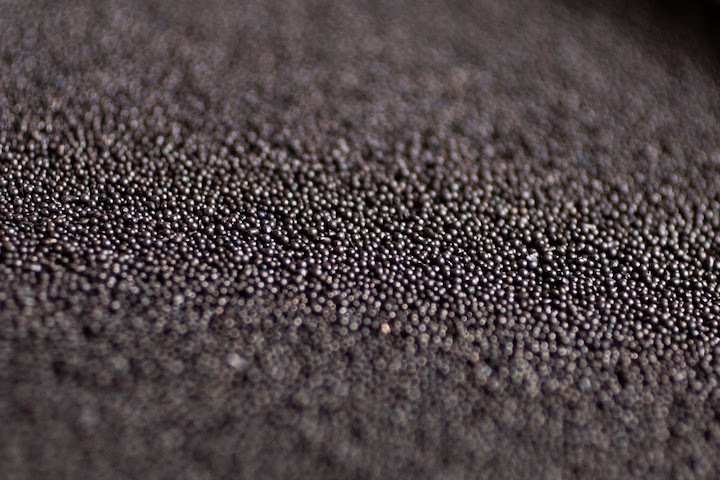
Shot is typically made of stainless steel, and produces a smoother, more polished surface than glass or sand blasting media. Shot can also be found in varying sizes to produce a smoother or coarser finish. Steel shot can also cause a more significant peening effect on a part and is a cleaner process — it creates less dust because the peening effect removes less substrate material and shot is more durable than glass beads. It’s also critical to check that your material is compatible with using stainless steel media, as not all materials are.
Pro-Tip: Always consider the next step after bead blasting. If you’re going to finish or coat your parts, make sure your media can be cleaned off the parts first. Also, it’s a bad idea to use silicone-based media prior to plating (you’ll thank me for this tip later). Lastly, be careful when blasting prior to welding or metal joining — like brazing or soldering — because impurities in the media can cause adhesion issues during the metal joining process.
Equipment
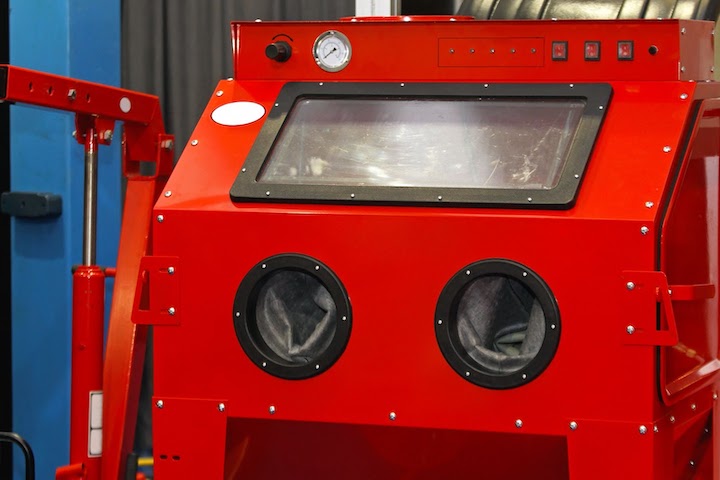
The equipment required for blasting is fairly straightforward. In the most simple set up, you need an air compressor to provide the high-pressure air to shoot the media and a nozzle to direct the media at the part. Other items can improve the process, such as a blast cabinet to contain the blast media and moisture traps to remove water that can contaminate the media.
Personal protective equipment (PPE) is essential for operators, as the media can easily remove skin or get into your nose, eyes, and lungs. A respirator, gloves, safety goggles, and thick clothing are the minimum protection necessary to prevent short and long term health issues.
Applications for a Bead Blasting Finishes
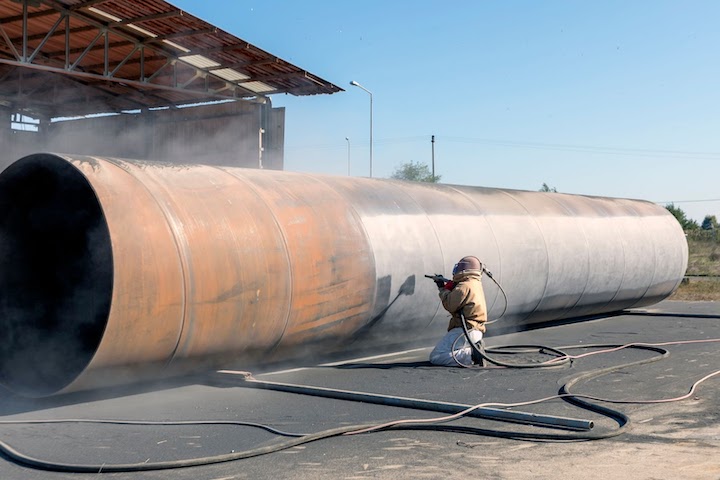
There are a wide range of uses for a bead blasting finish, and the most common ones are listed below:
- Peening
- Deburring
- Cleaning
- Aesthetics
- Paint and Coating Removal
- Paint and Coating Surface Preparation
Pros and Cons of Bead Blasting
The pros for bead blasting typically outweigh the cons. Bead blasting is a relatively cheap and fast process that removes minimal material, the media can be re-used quite a few times before needing to be replaced (depending on the media), it’s eco-friendly, and can cover a large surface area very efficiently. And bead blasting is ideal for a wide variety of materials, including aluminum, steel, titanium, brass, copper, and various plastics.
On the other hand, bead blasting relies on access to the material via line-of-sight, which means it has a tough time fully covering highly detailed parts with small pockets, internal cavities, and undercut features. Also, if your product has tight tolerances, the material removal can cause dimensional issues. So, it’s a good idea to analyze your part’s tolerances using our free Tolerance Analysis Calculator before blasting. It’s also advisable to mask threaded features to avoid compromising the thread profile.
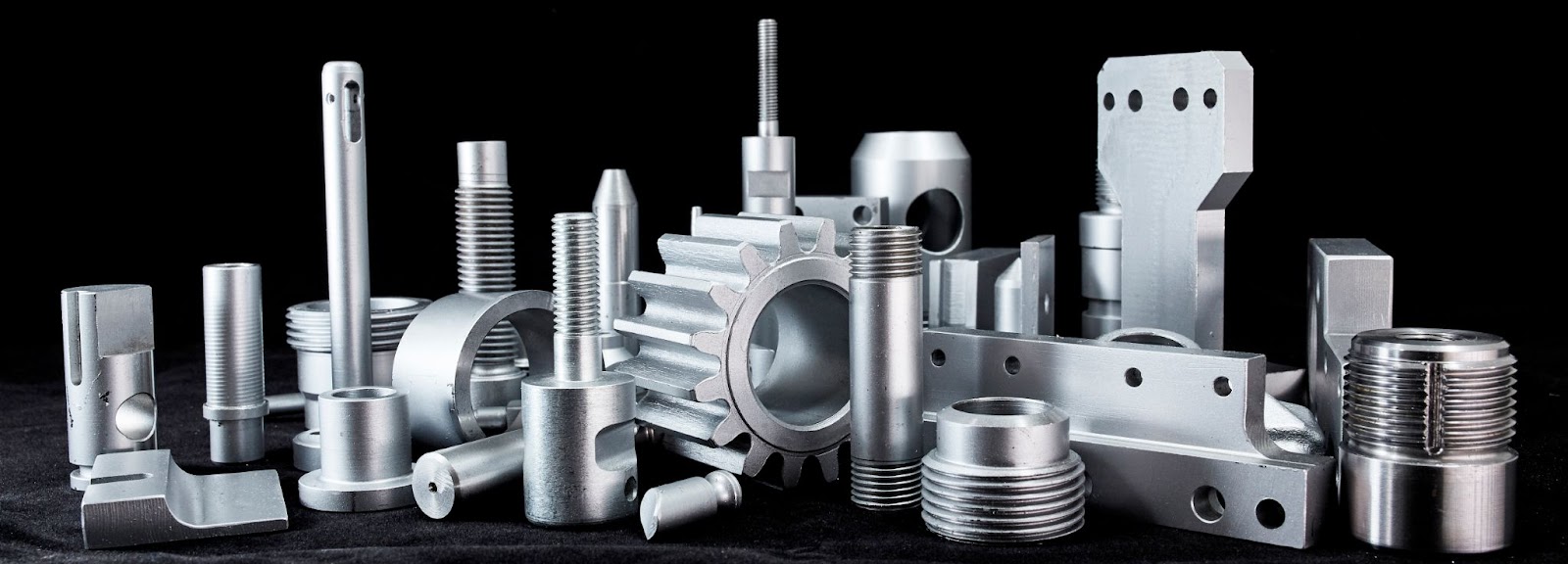
For products requiring repeatable finishes, a skilled operator, special fixturing jigs, or automated systems may also be required — and there are different techniques and media choices, which means using a trial-and-error process to figure out your finish can get expensive. It’s better to contact an expert, like those at Fictiv, to develop and recommend solutions for your particular application quickly and efficiently.
Conclusion
Bead blasting is a tried-and-true, versatile process that offers several advantages with minimal downsides. Fictiv is your operating system for custom manufacture that offers the guidance you need to ensure that media blasting is the right process for your project, so create an account and get a free instant online CNC quote today!