Time to read: 5 min
PEI injection molding is used to produce plastic parts that resist high temperatures and harsh environments. Polyetherimide (PEI), a high-performance engineering thermoplastic, also provides superior dielectric strength for dependable electrical insulation. Ultem® is a well-known brand of PEI from SABIC Global Technologies and comes in nearly 100 different grades, including both filled and unfilled materials.
PEI is relatively expensive and offers less wear resistance than polyether ether ketone (PEEK), polytetrafluoroethylene (PTFE), or ultra-high-molecular-weight polyethylene (UHMWPE). PEI also has a high processing temperature and tends to crack when exposed to corrosive environments while under sustained loads. Specifically, chlorinated solvents, strong alkalis, and some concentrated acids increase the chances of environmental stress cracking or crazing.
Because of its high cost and material properties, PEI is used mainly for specific types of challenging applications. For example, Ultem® injection molding is used to produce infusion pumps and medical respiratory devices that need to withstand repeated high-temperature sterilization. Injection molded PEI is used in electrical connectors and chip test sockets, both of which need to withstand electric fields without a breakdown in insulation.
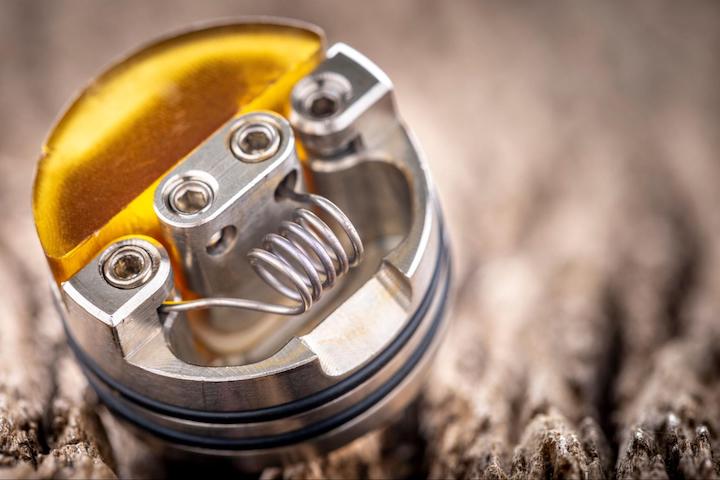
Advantages of PEI Injection Molding
PEI has many valuable properties:
Temperature Resistance
PEI has excellent high-temperature resistance. It can withstand a continuous operating temperature of 170°C and has a heat deflection temperature of 200°C to 210°C. Beyond 210°C, PEI begins to deform under a specified load.
Creep Resistance
PEI has good creep resistance, a measure of deformation at static loads, when exposed to higher temperatures. Along with excellent dimensional stability, PEI has a uniform coefficient of thermal expansion for more predictable changes in size when heat is applied.
Can Be Sterilized
Because of its high-temperature resistance, injection molded PEI can be sterilized in a steam autoclave. In addition, PEI resists gamma rays, which are also used to sterilize medical devices and surgical tools.
Environmental Resistance
PEI has good resistance to ultraviolet (UV) light, but its UV resistance can be enhanced with the addition of UV stabilizers. PEI’s resistance to sunlight, high temperature, and water make it a good choice for outdoor applications such as building-mounted electrical meters.
Dielectric Strength
PEI has the highest dielectric strength of any plastic and is an excellent insulator for applications such as electrical housings and capacitors. By definition, dielectric strength is the maximum voltage required to produce a dielectric breakdown through a material. Once dielectric breakdown is reached, the material becomes electrically conductive rather than electrically insulating.
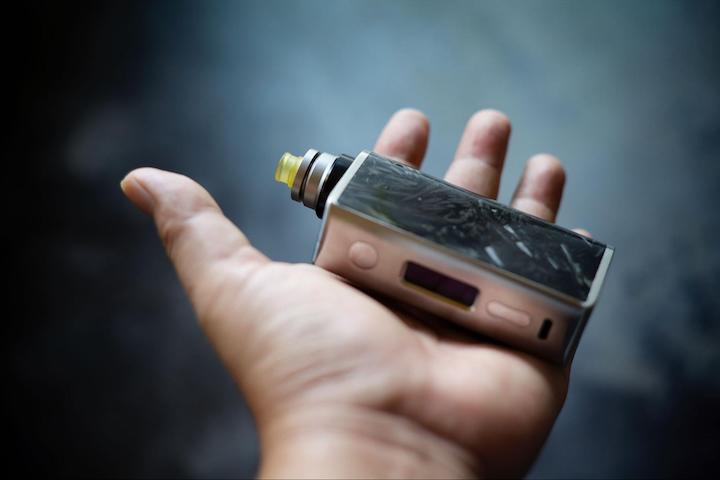
Design Guidelines for PEI Injection Molding
Part designers who follow injection molding design guidelines can promote manufacturability, control costs, and minimize defects. Fictiv’s Injection Molding Design Guide provides an overview of key design considerations. Download it here.
The following sections are specific to PEI injection molding.
Wall Thickness
The optimal wall thickness for injection molded PEI is between 0.060 and 0.1 inches. Wall thicknesses beyond this range are possible, but at the expense of reduced flow length (aka the distance covered by the melt until it solidifies when injected into the mold).
For best results, use a uniform wall thickness. If your part has walls with different thicknesses, make sure that these thicknesses are within 25% of each other and have a smooth transition between them.
Radii
With molded thermoplastic components, it’s important to avoid sharp radii that can increase stress concentrations and cause parts to fail. For injection molded PEI, use a corner radius greater than 0.015 inches. Larger radii are ideal, and radii that are 25% or 50% of the wall thickness are recommended. Large radii also improve the flow of plastic through the mold.
Draft Angle
Draft angles are the amount of taper that you apply to a part’s vertical walls so that it’s easier to eject the part from the mold. In general, PEI parts need a draft angle of 1°. PEEK parts with smoother finishes require less draft and parts with textured finishes require more draft. For every 0.001 inch in texture depth, apply 1.5° of draft per side.
Part Tolerance
PEI is capable of holding part tolerances of +- 0.001 inches. Note, however, that tighter tolerances increase tooling and processing costs. In general, PEI tolerances between 0.003 and 0.005 inches are common.
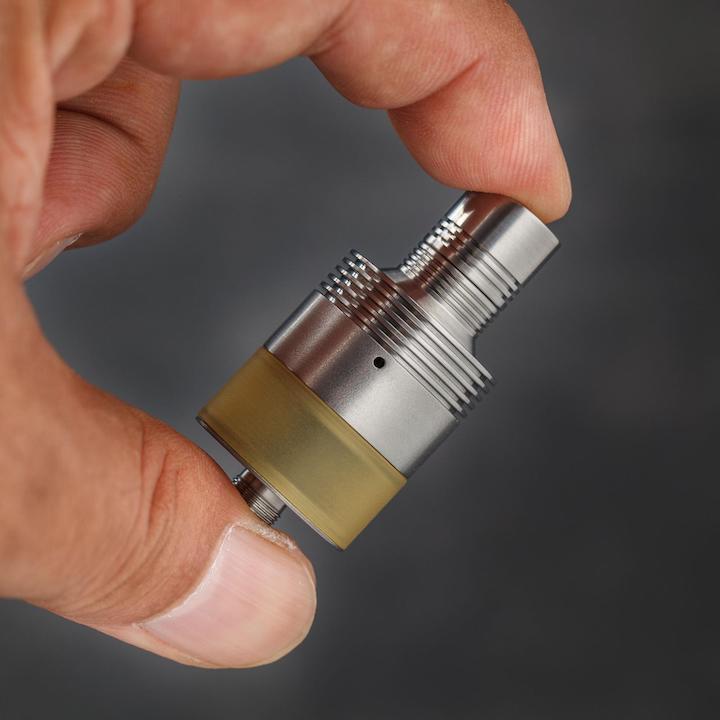
The table below lists the material properties of various grades of filled and unfilled PEI. The two glass-filled (GF) grades have higher flexural and tensile strength, but at the expense of reduced flexibility.
Ultem 1000 | Ultem 2200 (20% GF) | Ultem 2300 (30% GF) | RTP 2100 LF | ||
---|---|---|---|---|---|
Physical | Density (g/cm3) | 1.27 | 1.42 | 1.51 | 1.27 |
Shrinkage Rate (%) | 0.5–0.7 | 0.3–0.5 | 0.2–0.4 | 0.8 | |
Rockwell Hardness (M) | 106 | 114 | 114 | ||
Mechanical | Tensile Stress (MPa) | 110 @ Yield | 131 @ Break | 175 @ Break | 105 @ Yield |
Elongation @ Break (%) | 50 | 4 | 2.4 | 60 | |
Flexural Modulus (GPa) | 3.3 | 6.89 | 9.6 | 3.31 | |
Flexural Stress (MPa) | 160 @ Yield | 227 @ Break | 240 @ Break | 145 | |
Electrical | Dielectric Strength (in Oil) kV/mm | 25 (1.6 mm) | 26.3 (1.6 mm) | 26 (1.6 mm) | 19.7 (S/T) |
Volume Resistivity (Ω. cm) | 1.E+15 | 7.E+16 | 1E+15 | 1.E+12 | |
Injection Molding | Drying Temperature (°C) | 150 | 150 | 150 | 149 |
Drying Time (hrs) | 4–6 | 4–6 | 4–6 | 4 | |
Melt Temperature (°C) | 350–410 | 350–400 | 350–410 | 354–399 | |
Mold Temperature (°C) | 135–180 | 135–165 | 135–180 | 135–177 |
Material Properties of Common PEI Grades
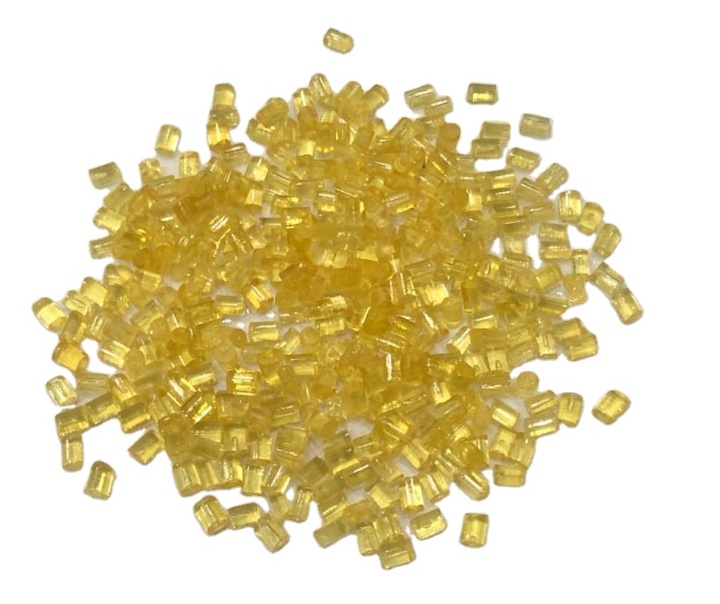
PEI Material Processing
PEI requires proper material processing to avoid injection molding defects. The following sections contain processing guidelines for injection molders to follow and for part designers to understand.
Moisture
PEI must be dried thoroughly before use. For unfilled grades of PEI, a four-hour dry time is recommended. Reinforced grades must be dried for up to 6 hours before use. A drying temperature of 150°C is recommended.
Temperature Control
PEI requires very high processing temperatures both inside the barrel and in the mold. A melt temperature between 350°C and 410°C is typical. Note, however, that temperatures above 382°C can cause changes in pigmented PEI. Molds require temperature control and are kept between 135°C and 180°C — excessively high mold temperatures may result in part defects.
Injection Pressure
The exact injection pressure depends on many factors, including part design, wall thicknesses, and processing temperatures. In general, however, PEI is injection molded at pressures between 70 and 150 MPa.
Shrinkage
Unfilled grades of PEI will shrink isotropically, meaning that they exhibit the same behavior in all directions. Once glass fibers are added, however, the shrinkage will become anisotropic and can lead to unwanted results. Mold shrinkage can be reduced by lowering the mold temperature and by increasing the injection pressure and rate.
Succeeding With PEI Injection Molding
PEI is an expensive material that is used for specific types of demanding applications. That’s why it’s important to design for manufacturability (DFM) and work with a skilled injection molder.
Fictiv provides expert DFM feedback along with your quote, and we work with a carefully-vetted network of manufacturing partners. As your operating system for custom manufacturing, Fictiv’s team and technology provides expert guidance and support to take you from part design through prototyping and production.
Create your free Fictiv account and request an injection molding quote today—we mold complex parts at ridiculous speeds!