Time to read: 6 min
Com⠂plex
adjective: complex
/ˌkämˈpleks,kəmˈpleks,ˈkämˌpleks/
not easy to analyze or understand; complicated or intricate.
“a complex personality”
Similar: complicated, involved, intricate, convoluted, tangled, elaborate
What comes to mind when you hear the word complex? Maybe particle physics, the vast size of our universe, the enormity and reach of the world wide web, nuclear reactors, supplier sourcing? Any human relationship… ever? Perhaps you’re thinking of a complex issue with a design or manufacturing process. Regardless of what comes to mind when you think of complexity, the word probably evokes a negative connotation — and that’s especially true in engineering design and when designing CNC machining components.
Complex CNC parts have intricate geometries which often require multiple operations in order to machine. These parts are typically made from materials such as aluminum, stainless steel, brass, or plastics. Complex CNC parts require a high degree of precision and accuracy in order to satisfy the required (and often complicated) specifications. Machining complex parts means that a CNC machine must be programmed to cut the material to produce the part’s geometric features.
Complex CNC machined parts can often be discerned by analyzing their geometric features. For example, a complex CNC part may require a series of contours, holes, and grooves to be cut in order to achieve the desired shape and size. Read on to learn more about complexity in CNC-machined part geometry and some of our best tips for reducing complexity in your designs.
Why Should You Care About Complexity?
Other than upsetting your boss by designing an unnecessarily complex part, what other reasons are there to care about complexity? While you cannot eliminate complexity in all applications, you should consider complexity each time you design a new part. Ultimately, you should care about complexity because it impacts:
- Lead time – In general, the more complicated the part, the longer it will take to manufacture, which can cause project deadline delays for you and your team.
- Cost – Highly complex parts cost anywhere from 2X to 10X higher than their low complexity counterparts.
- Quality – When you add complexity to a design, quality issues are more likely — and quality issues increase costs and lead time. Also, the cost of achieving the more intensive quality requirements is higher.
- Manufacturability – If a part is more complex, it typically isn’t easily manufactured — whether you’re outsourcing production or machining components in-house, reducing complexity means increasing manufacturability.
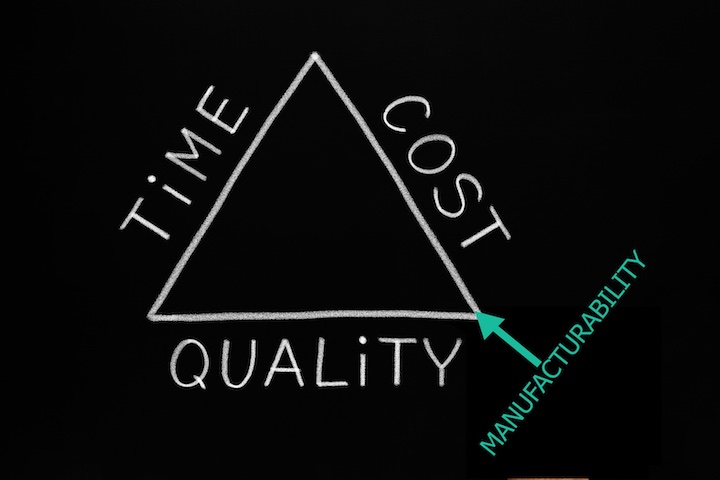
Why Should You Care About Complexity?
For the purposes of this article, we will consider a part to be either: high, medium, or low complexity. A part is medium complexity if all the complexity levels established are a mixture of medium and low complexity. A part is high complexity if any of the high complexity levels are established. A low complexity part doesn’t have any medium or high complexity levels established. Here are some rendered examples of parts to give you a visual comparison:
Low Complexity | Medium Complexity | High Complexity |
![]() | ![]() | ![]() |
Part Size
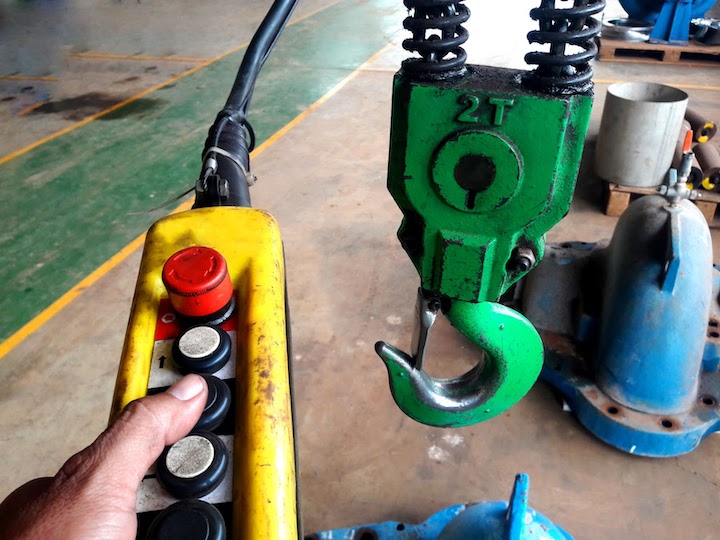
Part handling becomes more difficult as parts get bigger, so bigger parts requirs special transporting equipment and special machinery. Bigger can mean dimensional size or weight. Bigger parts also usually means special ordering of materials, more machining time, and more material cost.
High Complexity for Part Size:
- Part weight >70 lbs
- and/or largest part dimension >48”
How to Reduce this Complexity:
- Break large parts into smaller, assembled parts
- When possible, choose materials with lower densities; sometimes applying a finish to a less dense material can provide all the material properties you need
Holes
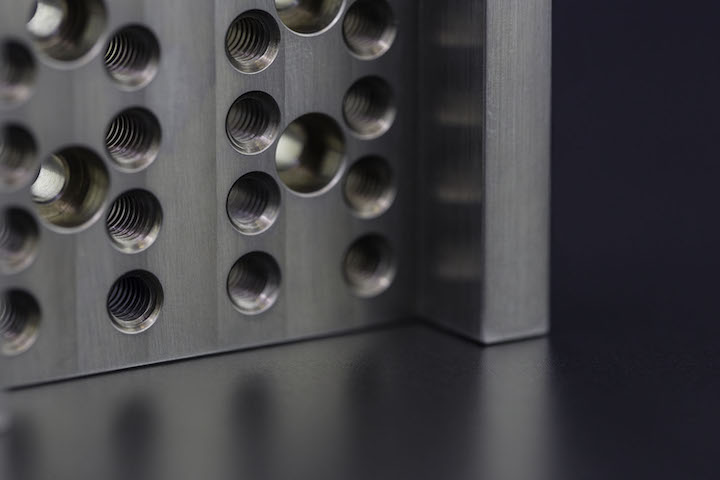
Machining deep holes, cavities, or taps also requires specialized tooling, an experienced machinist, and cautionary machining settings. These deep features also are more likely to cause tool breakage.
High Complexity Holes:
- Deep holes, cavities, or taps defined by a depth: diameter of ≥10:1
- and/or more than 15 individual holes
How to Reduce this Complexity:
- Reduce the depth-to-diameter ratio
- and/or reduce the number of holes
Threads
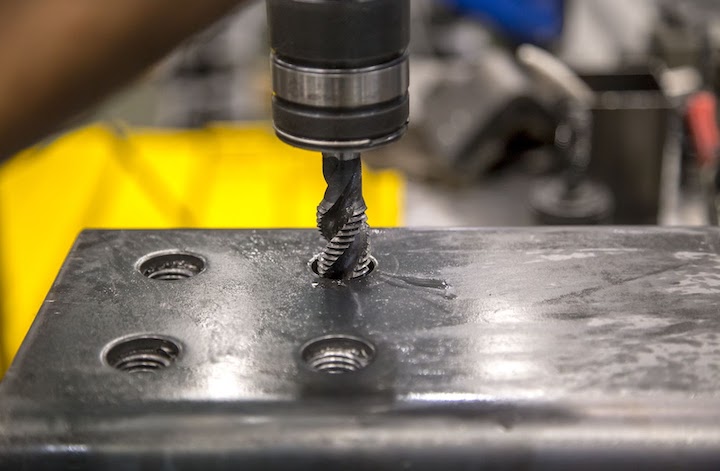
One of the simplest methods for producing threads is via a CNC machine using a pre-set thread milling program. The program guides the CNC machine to cut or tap the thread profile into the material, typically after drilling a hole. Thread milling programs also account for the diameter of the thread, the thread pitch, the thread angle, and the length of the thread. Standardized threads have readily available tooling that conforms to UNC, UNF, M, MF, and ACME standards. Non-standardized threads require special tooling and custom thread milling programs.
High Complexity Threads:
- Non-standardized: custom, proprietary, obsolete, or industry-specific
How to Reduce this Complexity:
- Choose only standardized threads (this makes life much easier)
- Provide tooling for non-standardized threads
Surface Curvature
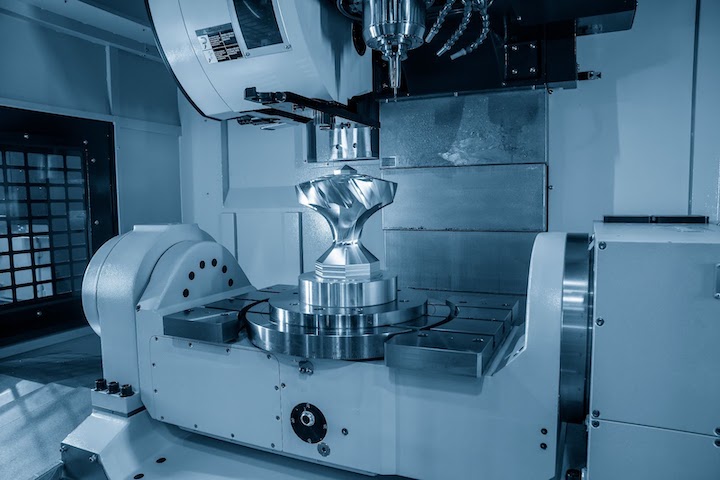
Curved surfaces are more difficult to inspect and can be more difficult to machine. A curve is defined as a continuous line without any straight segments. For example, circles, ellipses, parabolas, and hyperbolas.
High Complexity Surface Curvature:
- Compound curves or a significant amount of angled machining
Medium Complexity Surface Curvature:
- Less than 30% of the surface area is angled
Low Complexity Surface Curvature:
- Exclusively vertical and horizontal walls and <10% of the surface area has slanted sizes, no compound curves
How to Reduce this Complexity:
- Reduce the number of surfaces with angles
Wall Thickness
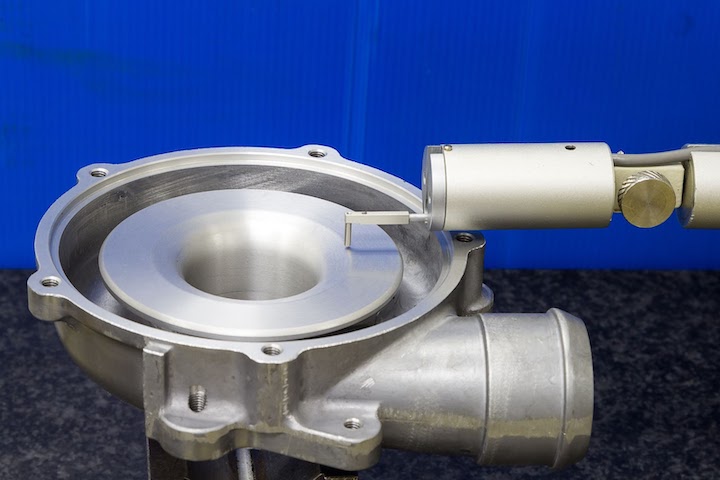
High Complexity Wall Thickness:
- Thin walls defined as ≤0.5 mm for metal or ≤1mm for plastic
How to Reduce this Complexity:
- Increase wall thickness of your component
- Decrease wall thickness of mating components
Tolerancing
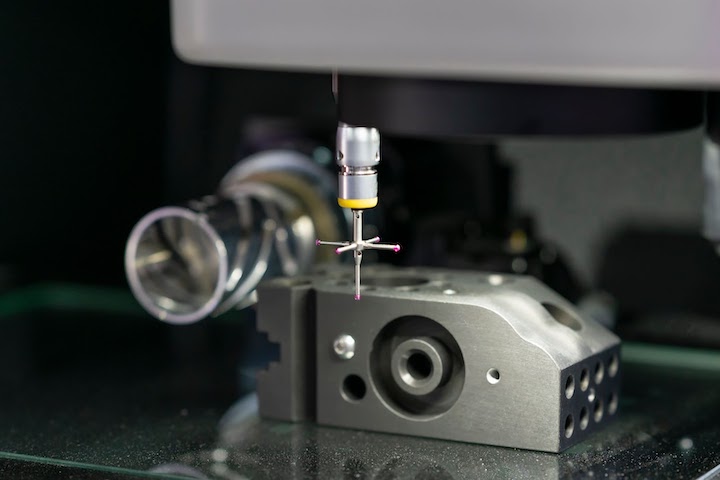
Tolerances have the biggest impact on part complexity. Tight tolerances means more precise machining, more intensive quality control measures, more sophisticated measuring equipment, and typically more inspections.
Pro-Tip: Check out our tolerance analysis calculator to perform a tolerance stack up analysis with just a few clicks.
High Complexity Tolerances:
- Any tolerance is <0.002 mm
Medium Complexity Tolerances:
- All tolerances are >0.002mm
Low Complexity Tolerances:
- All tolerance values are >0.06mm
How to Reduce this Complexity:
- Only use tight tolerances where absolutely necessary
Number of Setups
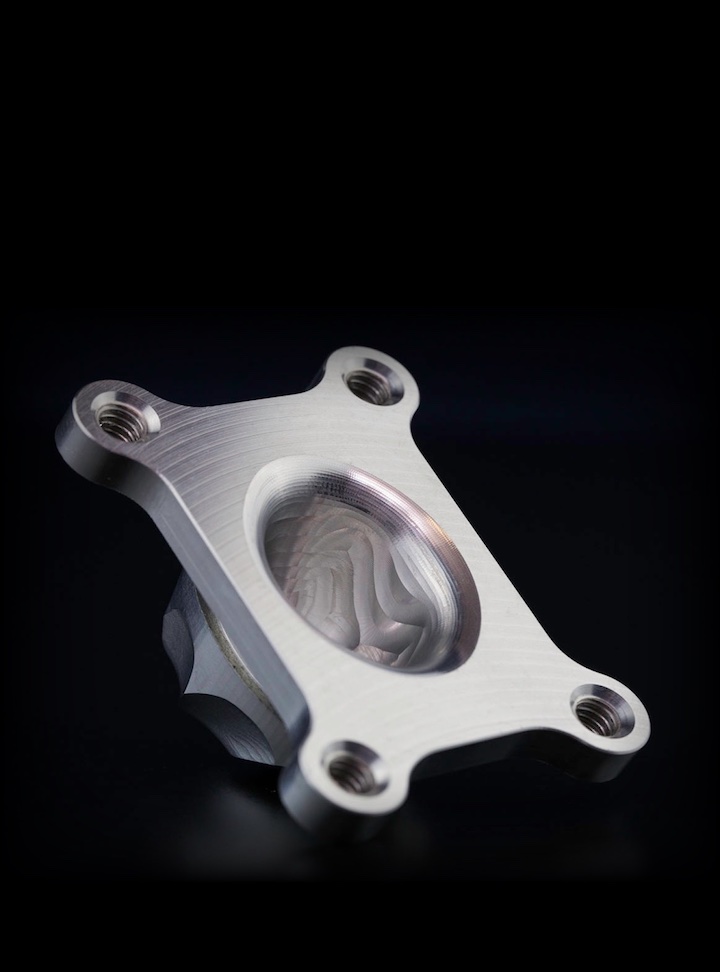
Number of part setups increases complexity because each setup involves not only labor, but also cost for fixturing equipment. The number of setups is based on the part complexity, fixturing, and the machine and tooling you choose. There are many variables involved, so finding the right balance is difficult and subject to equipment availability. Best practice is to start with a typical machining setup in mind and consider the number of surfaces that can be machined, especially surfaces opposite of each other.
High Complexity Number of Setups:
- Part requires more than 4 CNC machining setups
How to Reduce this Complexity:
- Try to limit the number of faces (surfaces) on your part that require machining
- Limit the amount of types of machining that are required to produce your part
Finishing
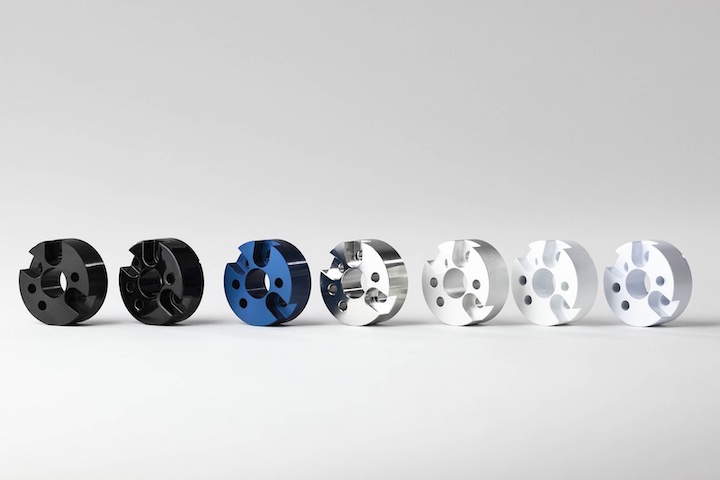
Often, material options aren’t ideal for your application. Maybe your parts must withstand a corrosive environment, high wear, extreme temperatures, or just water. Finishing encompasses all surface modification of parts to provide them with extra benefits or altered properties. Finishing includes: passivation, anodizing, painting, plating, bead blasting, heat treating, and many more.
Pro-Tip: Check out the Ultimate Guide to Finishing CNC Machined Parts , it’ll help you pick the best finish for your application!
High Complexity for Finishing:
- Any finishing requirements
How to Reduce this Complexity:
- There’s a whole world of materials; many new materials don’t require finishing
- When necessary, choose simple finishing processes or ones that are more environmentally friendly (they tend to cost less)
Determine the Complexity of Your CNC Part
Complexity is a key consideration in CNC part manufacturing, since it’s among the biggest cost and lead time drivers – complex parts take more skill and time, after all.
But what makes a part complex? Part size, weight, non-standard features, tolerancing, wall thickness, surface curvature, and part finishing all factor into complexity.
So, we created a quiz that makes it easy to find out how complex your part is, and therefore how easy (or complex) it is to manufacture.
Fictiv: Complex Parts at Ridiculous Speeds
As a general rule, it’s always a good exercise to see how to simplify your designs. But sometimes complexity is required, and complex designs can be elegant, too. Fictiv delivers even the most complex parts 2-5X faster than your average machine shop. We have a proven track record of delivering 95.4% of orders on-time and to-spec, thanks to our network of highly-vetted partners, on-site quality engineers, and robust quality management system. And, you get an inspection report with every part.
Create an account and upload your design today to see what our instant quote process, DFM feedback, and intelligent platform can do for you — we deliver complex parts at ridiculous speeds!