Time to read: 6 min
Creating innovative mechanical designs is hard (I should know—I do it for a living). Sometimes, you’re pushed to the very limit to imagine a concept or mechanism that could actually work. At times like this, manufacturing is a distant utopia that we can only hope to reach, so we ignore it. But, at the end of the day, we’re only fooling ourselves if we dream up uneconomical designs. The most brilliant machine ever conceived is nothing if it doesn’t make financial sense to produce and operate. For example, why aren’t water desalination, electric cars, and solar photovoltaics more prevalent? Why are we thirsty in the middle of an ocean, making tiny explosions to turn wheels, and drilling for oil when the sun shines all day? Because all ideas are subject to the constraints of available technology, and the benefits must always outweigh the costs. Just because something is possible does not mean it is economical.
There are often many ways to perform the same exact task, each with different manufacturing costs. As designers and engineers, it’s our job to find the least expensive ways to design for manufacturing. To that end, here are some practical tips to increase your manufacturing efficiency through design.
Manufacturing Efficiency
Manufacturing is all about efficiency. This is achieved through specialization—the more dedicated a tool or process is, the better and faster it generally is. Generally speaking, versatility comes at the cost of specialization. Humans, being very versatile creatures, are usually not the best factory workers: We take time to train; we’re slow; we need breaks; and we make mistakes. That’s why we turn to customized machinery to replace human labor—it’s overwhelmingly faster, more precise, and longer-lasting.
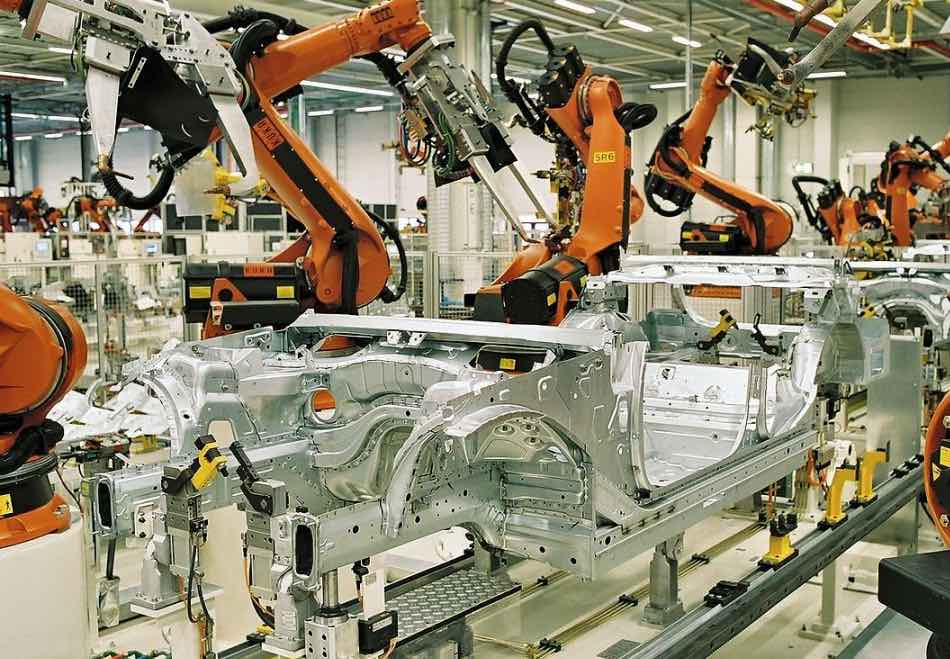
Of course, creating dedicated tooling and machinery requires up-front human labor. The cost of custom tooling must be weighed against its long-term gains. This is why it can be useful to amortize tooling cost into a “piece price” (price per unit) in the pursuit of calculating the time it takes to achieve ROI (return on investment). Naturally, production volumes are central to this equation—if you’re going to crank out millions of widgets a year, your customized tooling will pay for itself. This is common in the automotive industry. On the other hand, manual manufacturing processes can make more sense than customized tooling for low-volume production. For example, sailboat and airplanes are largely assembled by hand. These are all commercial decisions driven by the free market. Designers and engineers must have their company’s financial abilities and expectations clearly communicated, so that they’re able to make prudent manufacturing decisions.
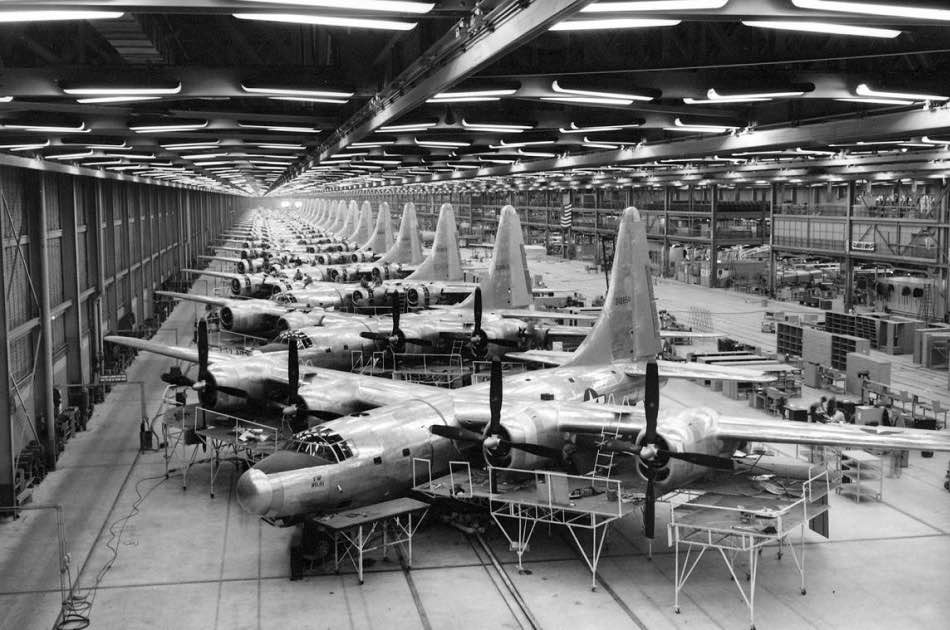
Make vs. Buy
An extremely attractive, best-of-both-worlds approach is to use off-the-shelf solutions. In other words, don’t reinvent the wheel! Thanks to capitalism, there is an absolute wealth of pre-made parts available to inventors and innovators, to the point where you can almost design a product the same way a chef makes a sandwich. Why kill the cow when there are butchers who can do it for you, faster and more cheaply than you ever could? Likewise, it often makes much more sense to buy pre-made components than design them yourself. This is intuitive for bolts, bearings, motors, etc. Other categories, like gears and housings, can be a toss-up, as the need for customization begins to exceed what is available off-the-shelf. Keep this in mind next time you find yourself wading into uncharted design territory—chances are, somebody else already offers a pre-made solution (Google is your friend).
Manufacturing methods
There’s more than one way to skin a cat. I’m not sure why you’d want to skin a cat, but if you find yourself in that situation, you should use a cat-skinning knife, rather than a spoon or chainsaw (sorry). Let’s apply that same logic to manufacturing methods. Here are some of the most common manufacturing methods, their (dis)advantages, and relative costs.
Casting/molding
Casting involves the liquid pouring or injection of hot materials into a mold. This process is often used for making very complex shapes. Casting creates a “rough” shape and is a somewhat imprecise process. That’s OK, though, because precision is not always needed. Casting is a versatile process that can produce many different materials, from metals to plastic. This method is extremely popular and is used everywhere from automotive housings (transmission, engine, etc.) to toys. Molds and their associated tooling are expensive and complex; they’re often the best method to achieving many general, three-dimensional shapes with a larger volume/surface area ratio.
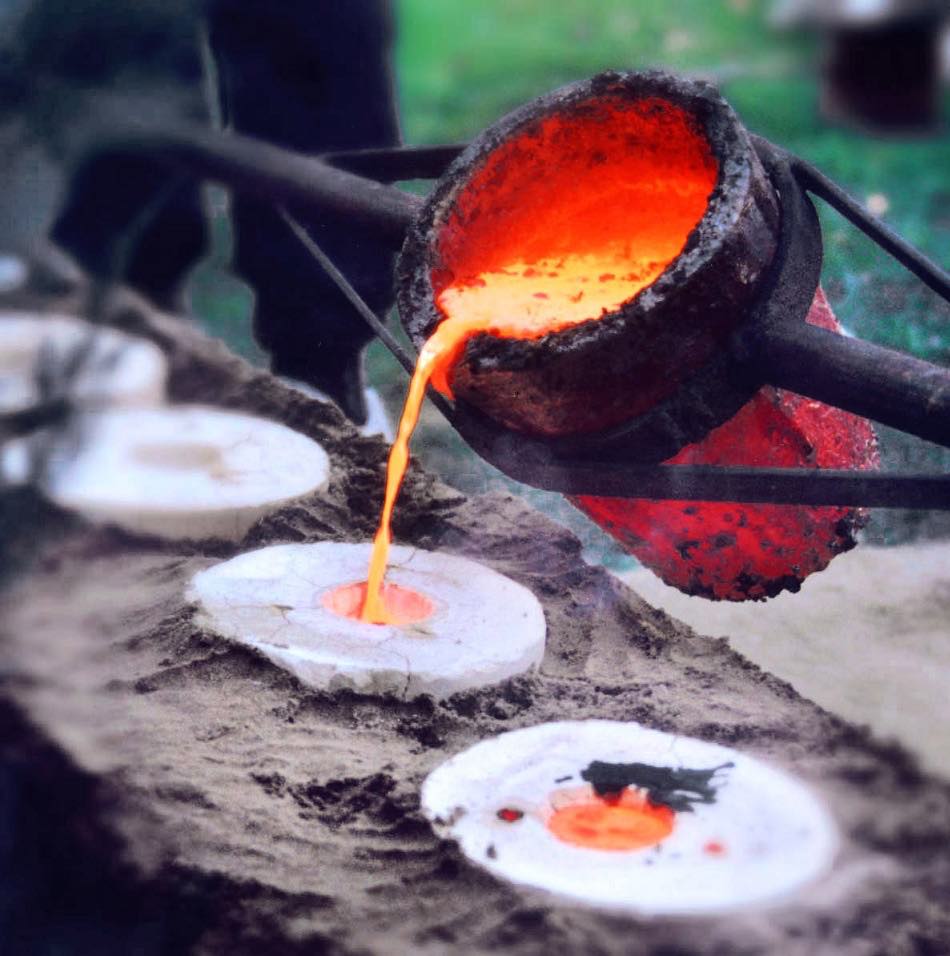
Sheet metal
Sheet metal forming, a sub-process of cold-forming (as opposed to the hot-forming of casting) is a process used to create thin metal enclosures that don’t need to be pretty or watertight. For thin, complex shapes, forming makes more sense than casting because of the difficulty of forcing a molten material around tight corners and into long, thin channels. It also takes much less energy to deform a thin piece of metal than it does to melt the metal into a liquid state. Stamping is a forming process that uses dies under massive load to crush metal into a desired shape, and is extremely common for automotive outer parts (hood, door panels, etc.). Electrical boxes are made by stamping a blanket sheet to add cuts and holes, and then bending to form the box into its final shape.

Machining
Machining, whether CNC or manual, is the process of removing material from an object, usually with rotating cutters or drills. The machining process can achieve extreme precision and is often used to place accurate holes and make smooth, flat planes. The more axes (no lumberjack) of a CNC machine, the more versatility it has. Machining is an expensive process and should only be used when the necessary precision (location, size, surface finish) of features cannot be achieved any other way. EDM is another machining method that removes material via electrical discharge (sparks). It’s great for extremely small, delicate features that a cutting tool would have difficulty achieving. However, EDM is also slow and expensive.
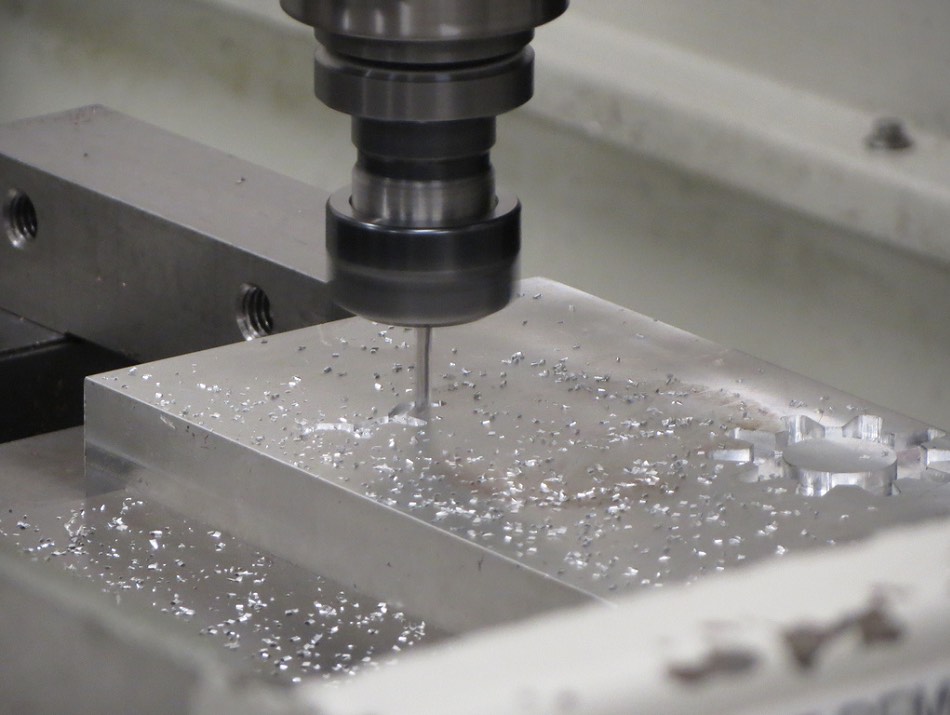
2D cutting
Plasma, lasers, drills, and even water can be used to precisely cut 2D shapes out of flat sheets of material. This method shines when precise and/or deep cuts are needed. Like machining, 2D cutting provides great results but is but slower and more expensive than stamping.
3D printing
3D printing is the futuristic holy grail of manufacturing. Also known as additive manufacturing, this method is prized for its ease of use and versatility in creating impossibly complex shapes with remarkable precision. Internal cooling channels, undercuts, and an Eiffel tower that fits on your hand are all commonplace and easy to make. 3D printing is extremely useful for quick prototypes. While 3D printing is relatively slow and expensive in manufacturing, it is currently being investigated and adopted by companies for mass production.
Plastic thermoforming
As an analogy to metal processes, plastic thermoforming falls somewhere between casting and cold-forming. (Note: The word “Plastic” can refer to a specific material, or be a synonym for “permanent”, ie. plastic deformation = permanent deformation. In this case, we are referring to permanent deformation of plastic material). A thin sheet of material is heated and then formed to a one-sided mold to create a basic shape. Tooling cost is lower than injection molding, but the process is more laborious, making it good for lower volume production.
Tolerances
These days, tolerance is a virtue; intolerance will not be tolerated! Tolerance refers to the allowable deviation from an ideal state. In manufacturing, the less tolerant you are, the more precise your manufacturing must be, and thus more expensive. This is central to choosing your method of manufacturing. For example, imagine that we must mount two objects together using bolts. The location, size, and direction of the bolt holes are all important, as is the parallelism of the two mounting faces. GD&T (geometric dimensioning and tolerancing) is a field dedicated to establishing quantifiable geometric constraints on 3D features. Tolerances should be back-calculated as the greatest allowable deviation, while still maintaining function (plus some safety factor). There are various tricks you can use to make manufacturing easier and cheaper (they’d literally throw gearboxes together, if they could) while still maintaining functionality. For example, “bonus tolerances” allow greater deviations in one aspect if a corresponding relevant variable is adjusted (for bolt thru-holes, positional misalignment can increase if hole size increases as well).
Do it
In the wise words of Shia LaBeouf, “Don’t let your dreams just be dreams.” You are attempting to give birth to your brainchild, and cost-effective manufacturing is the final, painful gauntlet that you must pass through if we want your ideas to ever see the light of day. In general, we should use manufacturing constraints to guide our design decisions—that is, if you want to save $$$ and be rich. You want to be rich, right? Then share this article with your colleagues and help your engineers design with manufacturing efficiency in mind.