Time to read: 9 min
CNC Machining for Aerospace: An Overview
The aerospace industry is different from others because the consequences of a given part’s failure are dire. No need to go into details, but in general, everything needs to work perfectly every time. This means every gear needs to turn, every bracket needs to stay in place, and it all needs to fit together perfectly.
Getting it right starts with the design and manufacturing process — using the right tools with the right materials. Precision fits and holding tight tolerances are critical, because quality is paramount above cost and lead time. This is why CNC machining is ideal for aerospace applications.
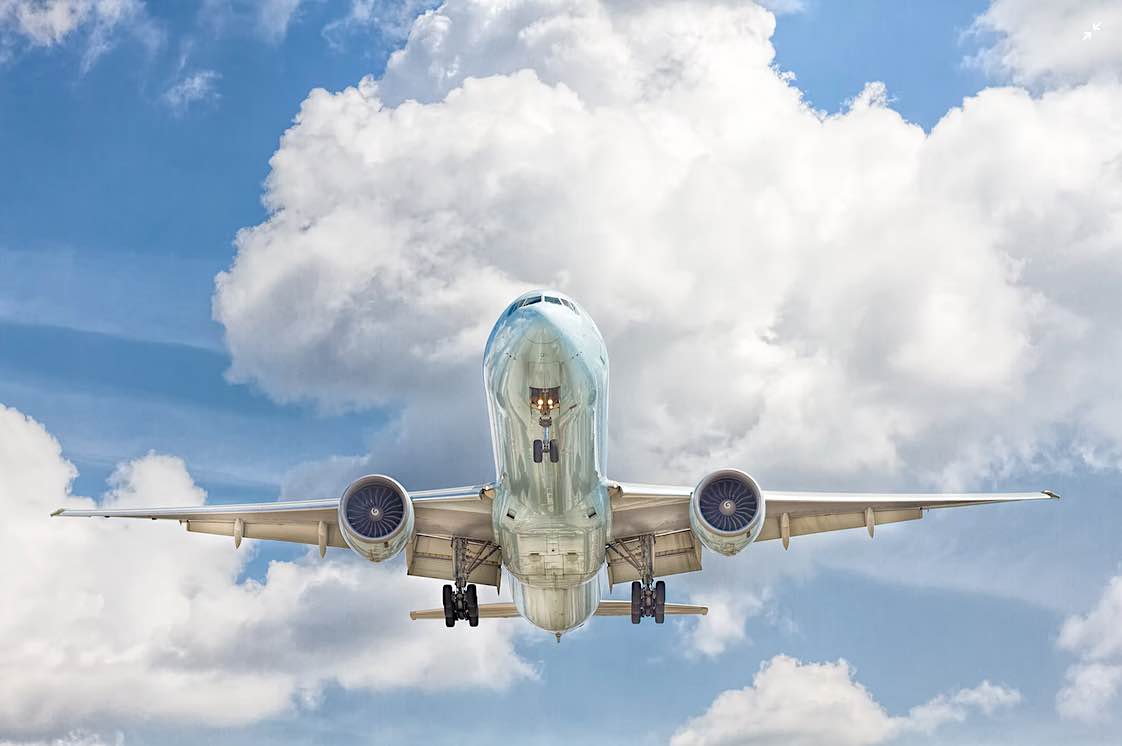
Automated CNC machining limits the possibility of human error, and enables the highly precise nature of this manufacturing method. CNC machining is also fast, especially when it comes to parts in lower quantities. Unlike consumer electronics, not everyone has an airplane for their personal use. For example, in 2019, 1,377 aircraft were delivered. In comparison, 40.8 million iPhones were sold in 2019. Aircraft are made in much lower quantities than consumer products, and these lower quantities lend themselves well to CNC machining.
Components Made Using CNC Machining
CNC machining is used to manufacture components throughout modern planes, from the landing gear (components such as braces and torque links) to the engine (compressors and turbines). Structural components can also be CNC machined, like parts of the fuselage, bulkhead, and airframe. Gears, shafts, and housings, which are important for moving components, are commonly CNC machined parts. Finally, in helicopters specifically, the piston engine housings are generally CNC machined.
Materials Used in Aerospace Components
CNC machining is also well equipped to handle the materials necessary for aerospace components. The extreme environments and use cases that airplanes, helicopters, and spaceships experience require specialty materials. These materials include titanium, specifically Grades 2 and 5, which is used for engine components due to its heat resistance and strength. However, titanium is an expensive material, so it can’t be used for every part of an aircraft.
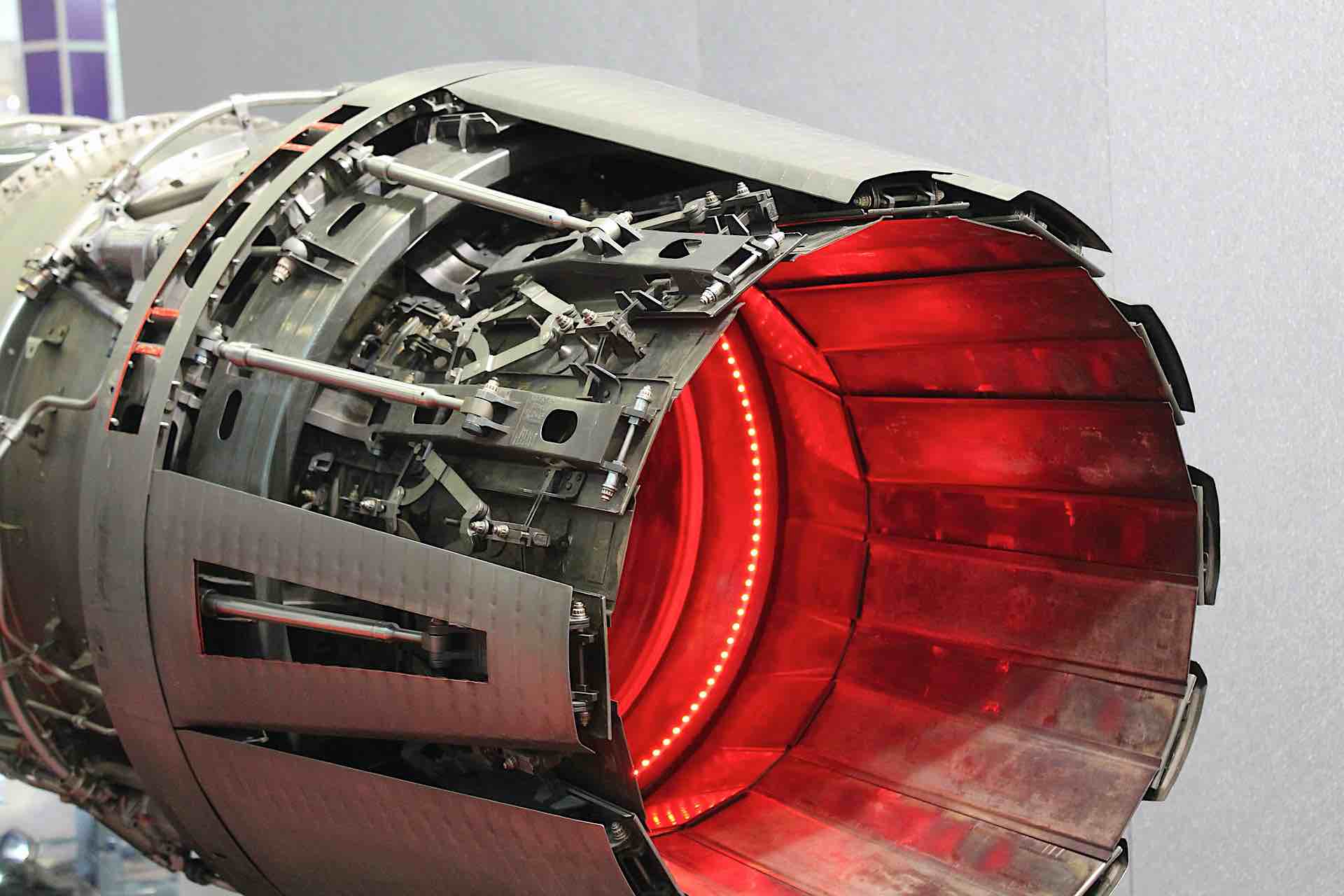
Alloy steel, particularly 4340 and 4130, is also used to manufacture aerospace components. 4340 steel is tough and strong, with high potential hardness, making it ideal for the high loads experienced by aircraft landing gear. 4130 steel also has high tensile strength and is used in gears, fasteners, and exterior components. Steel’s strength to cost ratio, particularly compared to titanium, is advantageous, but steel is a much denser and heavier material, which limits its use in aerospace applications. Also unlike titanium, steel tends to corrode, so must be coated if it will be exposed to moisture.
Finally, aluminum (7075, 2024, and 6061), is used for its high strength to weight ratio thanks to its low density. It is also easy to machine — two to three times faster to machine than steel. Aluminum 2024 has good fatigue resistance, meaning that it can withstand many load cycles (ideal for airplanes that are in use for years). Aluminum 6061 is a precipitation-hardened aluminum alloy that has good corrosion resistance and can be found in airplane wings and fuselages. Aluminum 7075 has both good fatigue resistance and corrosion resistance, which has led to its common usage in aircraft structural components.
Unique Challenges in Aerospace Manufacturing
CNC machining isn’t always a straightforward and easy process in any application, and that’s the case for aerospace components, too. Here are seven different obstacles commonly encountered when making aerospace components, along with solutions to tackle them.
Machining large components with thin walls
Some components, such as engine or compressor housings, have large internal cavities. For example, to manufacture the transmission housing for helicopter blades, a CNC machine must core out a large block of material. This takes a lot of time, creates a lot of scrap material, and also leads to residual stresses in the part. These residual stresses can lead to deformation or warping — which are problematic when you’re working with tight tolerances and high standards.
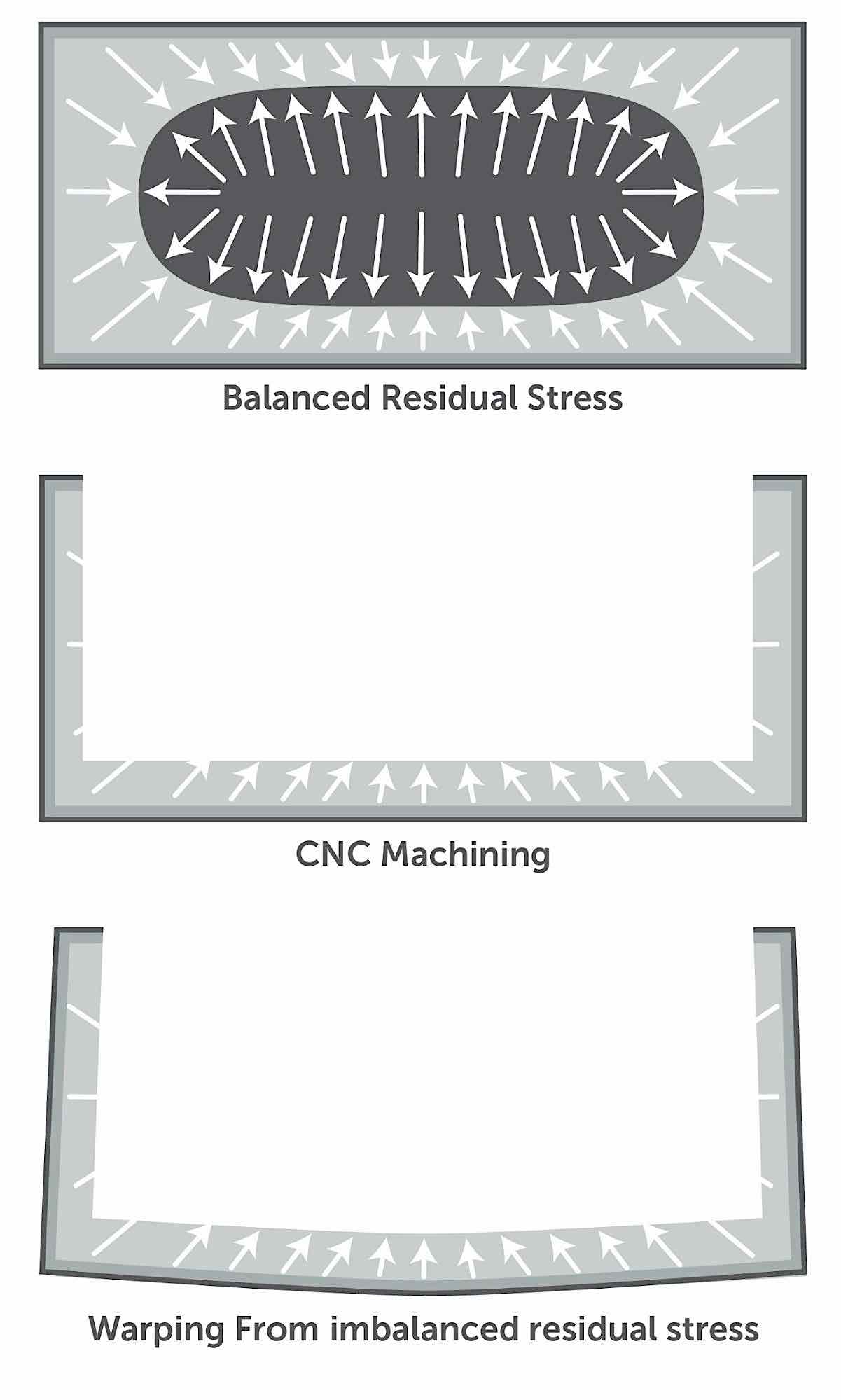
In order to determine beforehand if removing a lot of material will be a problem, there’s a pair of formulas you can use. You’ll need to check both the IRMR (Internal Removed Material Ratio) and the ERMR (External Removed Material Ratio). The formulas for both are shown below.
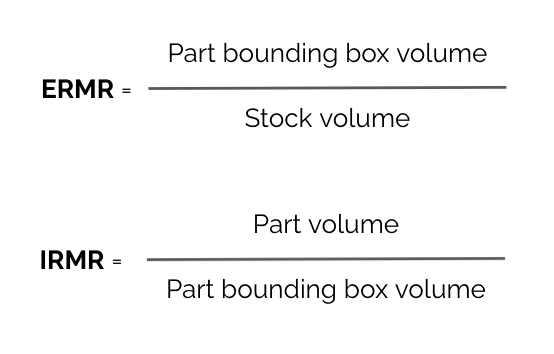
The IRMR should be greater than 85%, which indicates that you’ve removed less than 15% of the internal part volume. The ERMR, which compares the final part bounding box volume to the stock volume, should be greater than 30%. If both of these pass the test, you can move forward with prototyping and testing. However, if one or both of these values is beyond the acceptable limit, your part may be difficult to manufacture within tolerance or you may run into performance issues.
In those cases, you have a few options. If the quantity of parts needed is low, you can machine one and test it, then proceed (and continue testing each part) if the first part turns out to be in spec.
Sometimes parts like this can be cast, which is a process better suited to creating large components with thin walls. With casting, you’ll waste less material and experience less warping. CNC machining will probably still be necessary for finishing and meeting tolerances.
Finally, you can use a special high-performance 5-axis CNC machine, which has more ability to control the force, power, and speed. By using a lower force, power, and speed, you can machine a part with thin walls without exerting so much force that it will deform. Additionally, you can use an ADOC (axial depth of cut) or RDOC (radial depth of cut) to machine parts symmetrically in order to distribute the force, resulting in less residual stress.
Dealing with Complex Geometries
Due to the unique needs of aerospace components, these parts often have complex geometries in order to reduce weight while maximizing strength or to promote airflow over the surface of the part (#justflyingthings).
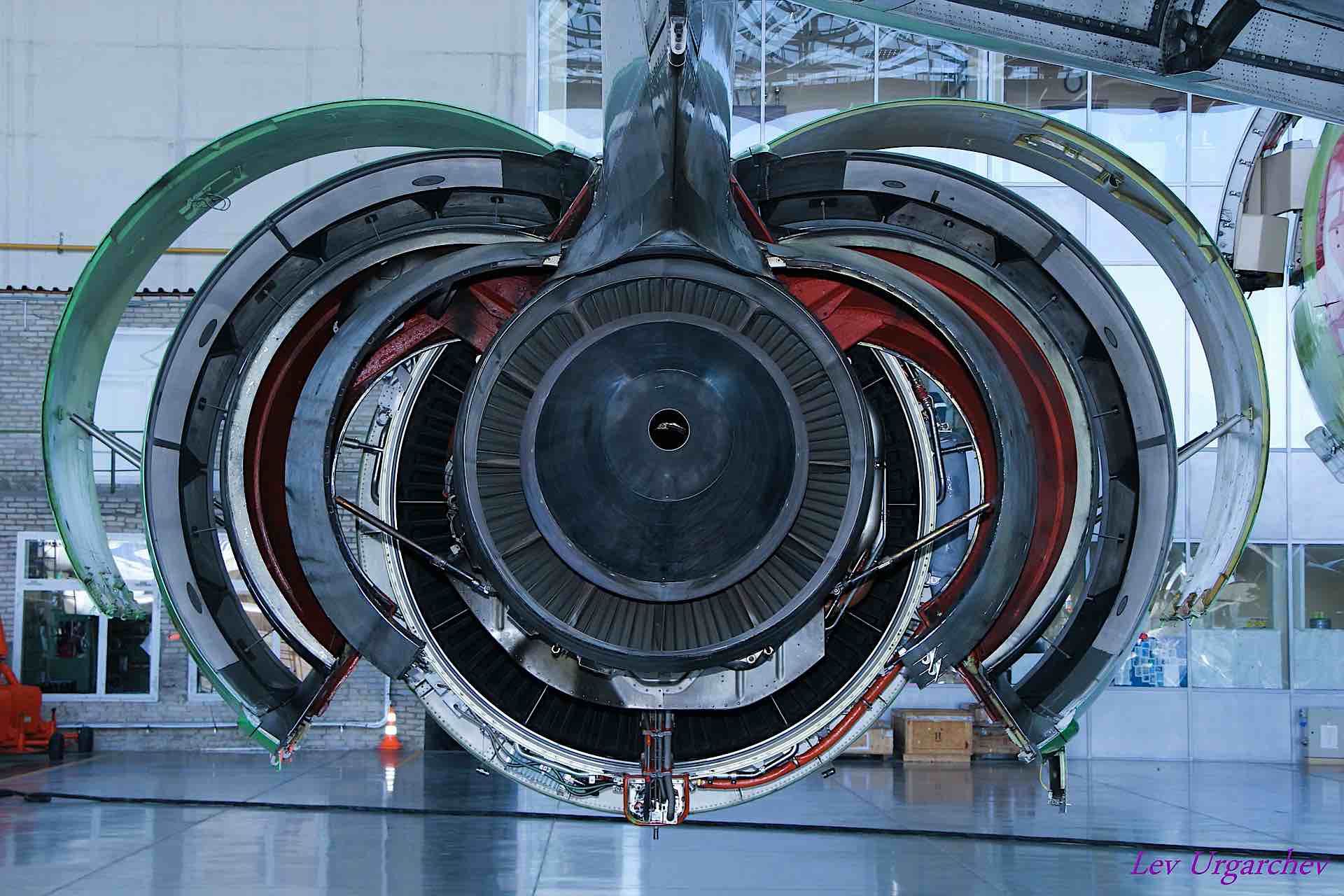
However, sometimes these complex geometries are needlessly complex. For example, when an internal component is designed with complex organic surface geometry. Since more complexity means more machining time and potentially more time finding a supplier who has the capabilities, it’s best to simplify part designs whenever possible.
Sometimes all that’s necessary to mitigate this is to promote design for manufacturability (DFM) among designers and engineers. DFM takes into account the limitations of manufacturing and looks at the feasibility, time, and cost of a design from the machining perspective. This can help engineers think about where the complexity is truly necessary, and where it’s not as important. For example, internal components are not critical for airflow and don’t require fancy curved surfaces.
With aerospace applications, however, complex geometry is often unavoidable, and in those cases, you can use a 5-axis (or more) machine.
Part Size: CNC Limitations
The final part geometry challenge is part size. Aircraft are huge assemblies made of millions of parts. While many of those parts are small, some large components are required. Typical machine beds are only a few feet long, which is not sufficient for structural components or other sizable parts. This means it can be challenging to find suppliers with this capability.
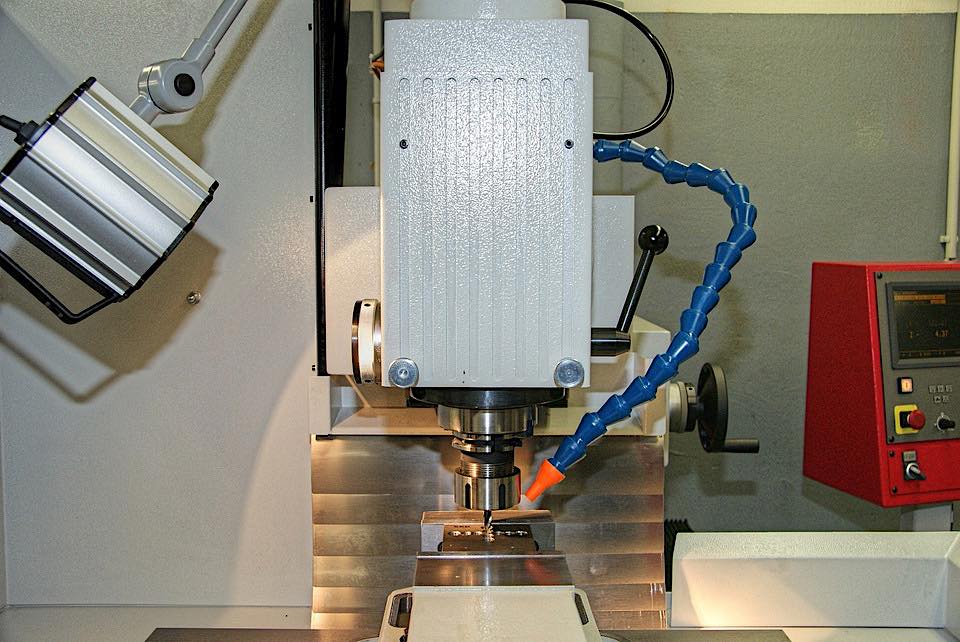
To solve this problem, you’ll need to find a new supplier with large CNC machines that can handle the part size. Otherwise, you’ll have to redesign the part to fit. This may involve breaking a larger component into smaller parts. However, this will likely increase the overall weight due to the additional fasteners required to assemble the multiple smaller sections.
Another possible solution is to change the manufacturing method. Casting can produce larger parts all in one piece, but may still require CNC machining to post-process. Casting takes longer because the design and manufacturing of the mold are necessary before any parts can be made. This also makes it a less cost-effective option than CNC machining for small quantities of parts.
Attaining the Appropriate Material Properties
It can be difficult to achieve the highly specific material properties required for aerospace applications. The metals will often need to be heat-treated to reach the desired hardness and strength. Heat treating is a common process but presents its own challenges.
Heat treating before machining will make the material significantly harder and stronger, so it can hold tighter tolerances. But, machining hardened material is more time-consuming and wears down the cutting tools faster, so is more expensive to machine. If you must heat treat before machining, investing in tools made out of a harder material like titanium, rather than carbide or high-speed steel, can help ameliorate those issues.
Of course, heat-treating after machining has its own issues, since it may affect the dimensions of the part. This negates the precision of the CNC process, and can even push the part out of spec. You can mitigate this by choosing the most effective heat-treating process.
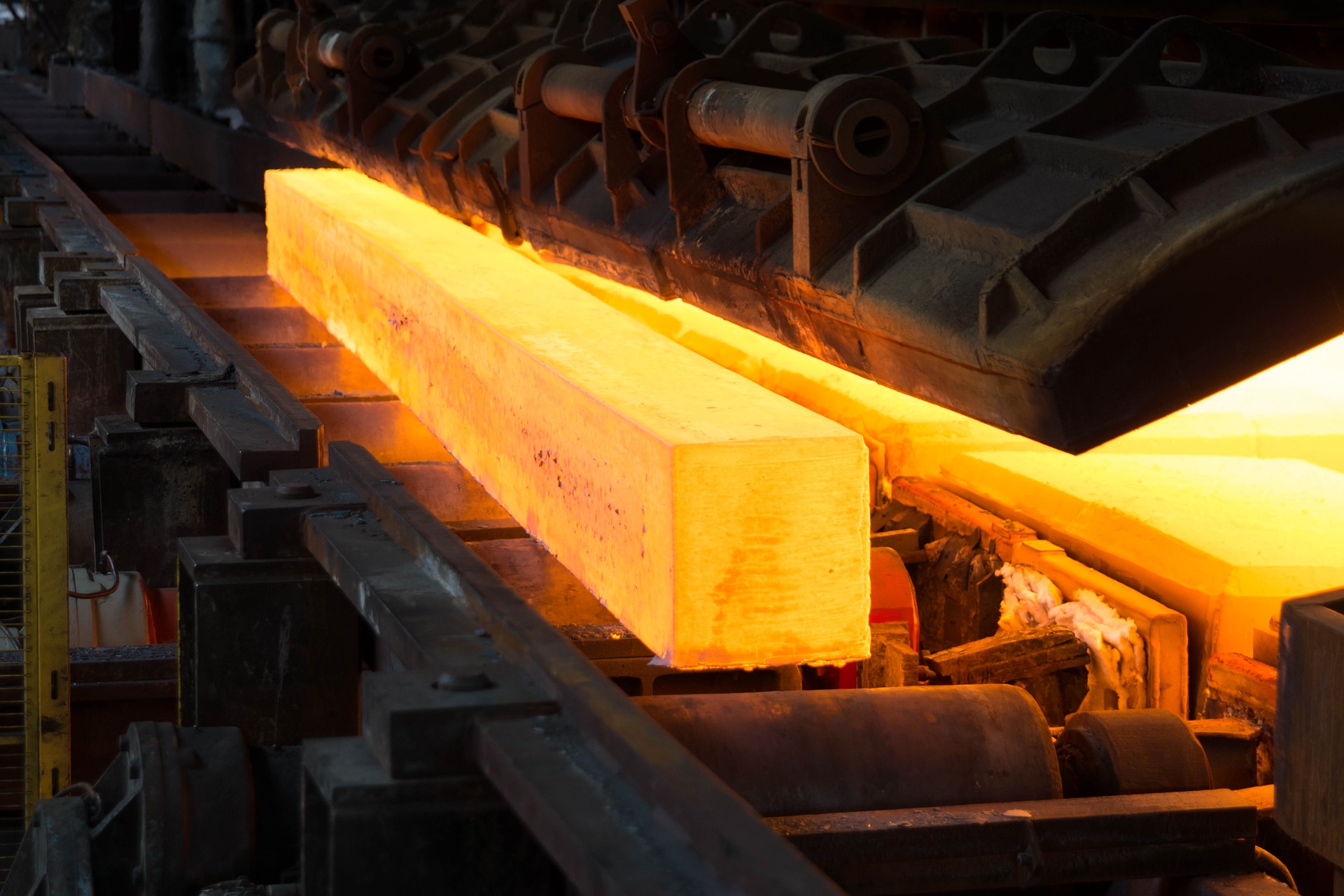
Tempering and aging involve heating the metal to a lower temperature than other processes, so the dimensions won’t change as much. Additionally, at the end of the heat-treating process, you can use press quenching rather than oil quenching. Oil quenching causes the material to shrink more quickly, which results in larger dimensional changes.
The simplest way to get the right properties is to accept the increased cost and lead time of heat treating before machining. Again, quality is key for CNC machining, and getting that quality entails sacrifices in speed and cost. Another option in some cases is to perform a small amount of final machining after the hardening process. This lets you do most of the machining on the pre-hardened material, and finish the hardened material to get within the tolerances needed for the final part.
Sourcing Materials
Before treating or machining your material, though, you have to find the right stuff. Superalloys and specialized plastics can be difficult to source and are expensive and time-consuming to ship. These materials include titanium, nickel alloys (like nickel silver alloy), and Ultem, which is a plastic used in aerospace applications. Aerospace components always need these materials, due to the specific needs of aerospace components, so this will be a long-lasting challenge.
To get around those constraints, aerospace companies can leverage digital manufacturing ecosystems (DME) like Fictiv that have access to a large pool of manufacturers. Working with a DME means that there’s a higher chance that one of the manufacturing partners can source the necessary materials. Additionally, this leaves sourcing up to the manufacturer, so the engineers can focus on the design.
Sourcing Manufacturers
Speaking of sourcing, it’s critical to find the right manufacturing partner. Because of the special requirements in the aerospace industry, most aerospace companies require their manufacturers and suppliers to have AS9100 certification. AS9100 is based on ISO 9001, which regulates quality management systems and controls quality and safety that are paramount in the industry.
However, not all manufacturers have this certification, and it can be difficult to find those that do. The certification is expensive and takes time, and the quantities for aerospace components are not always worth it (more on that later). But a digital manufacturing company can solve that problem. There’s a better chance they have access to suppliers with the necessary certifications in their wide pool of partners.
High Mix, Low Quantity Production
As mentioned above, aircraft are not produced in the same quantity as other physical items, like consumer products or electronics. That means that a lot of aerospace components are not mass-produced. Airplanes require a lot of different parts, but they may only need a few hundred or less of a given part. This is referred to as high mix, low quantity production.
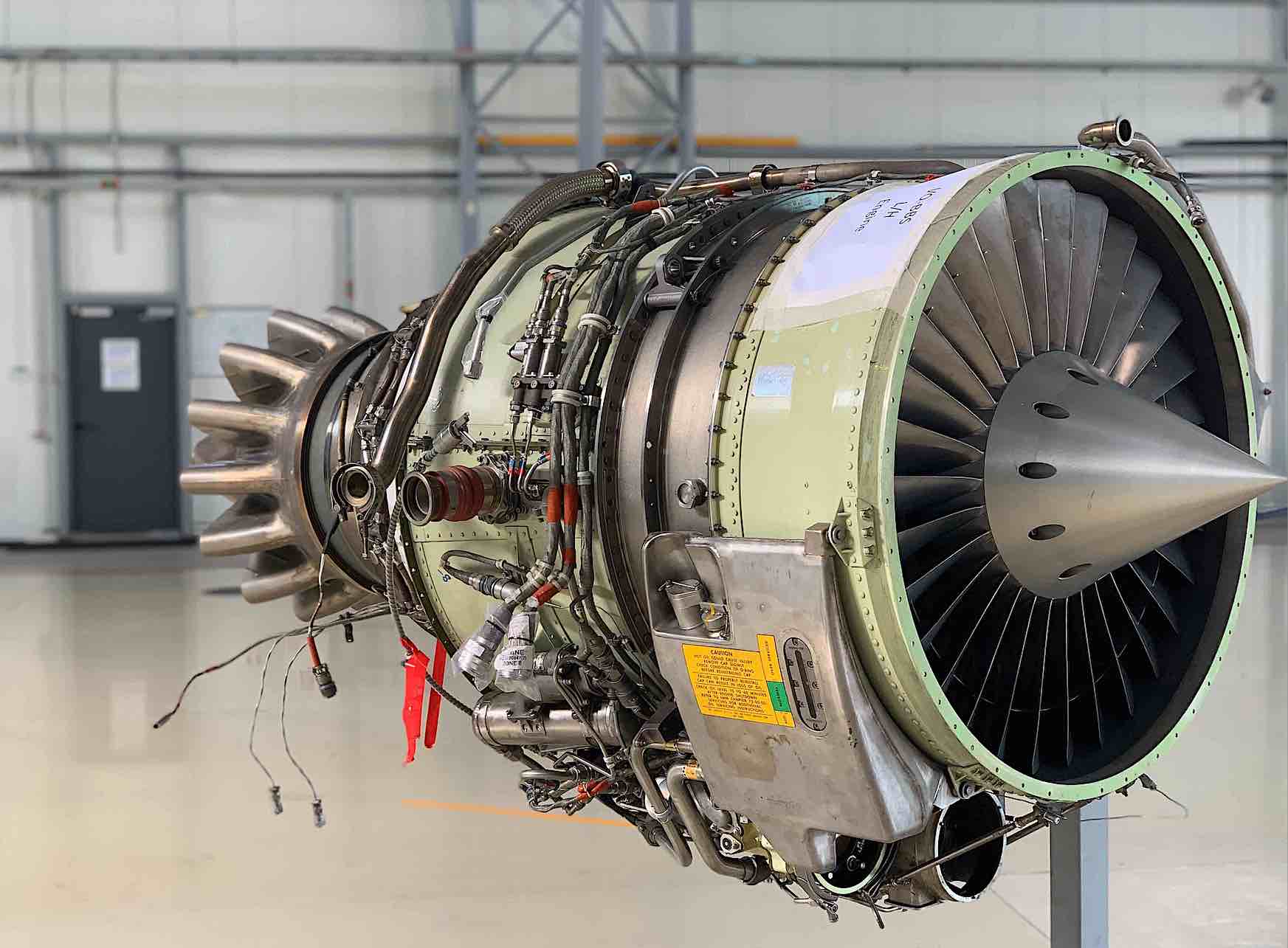
Unfortunately, high mix, low quantity production is the opposite of what manufacturers like to do. It takes time and effort to review and set up a manufacturing process to produce each part, so those projects are much less efficient and cost-effective. Some manufacturing partners simply won’t take on projects that require them to spend time developing a process for complex geometry to make just a few parts.
In some cases, it’s possible to order larger quantities, which mitigates the problem. If post-processing can be added to a part, such as a coating, this may allow you to increase the order quantity and store excess parts for later. But this option is only applicable to lasting designs that can be used in future aircraft models and also requires space for storing inventory.
Another option is to work with a digital manufacturing company. The company can connect you with manufacturing partners who can slot your orders into their free machines, benefitting both you and the MP.
Final Thoughts
If you work as an engineer or manufacturer in the aerospace industry, chances are you have run into one of these challenges. Even in other industries, engineers may run into similar issues and can apply these lessons.
Whether you’re an aerospace engineer or working in another field, Fictiv holds the keys to unlocking your innovation. So, create an account and upload your part today to leverage our network of highly skilled CNC machining service partners to turn your vision into reality!