Time to read: 5 min
If you’ve ever designed and 3D printed a part that required high dimensional accuracy, you were probably disappointed with the outcome. Maybe a bolt didn’t fit into a 3D printed hole, or a 3D printed bracket didn’t fit into its intended recess. Whatever the dimensional intention, it’s likely that the 3D printed part didn’t serve its function because the 3D printer lacked the dimensional accuracy to manufacture it as designed.
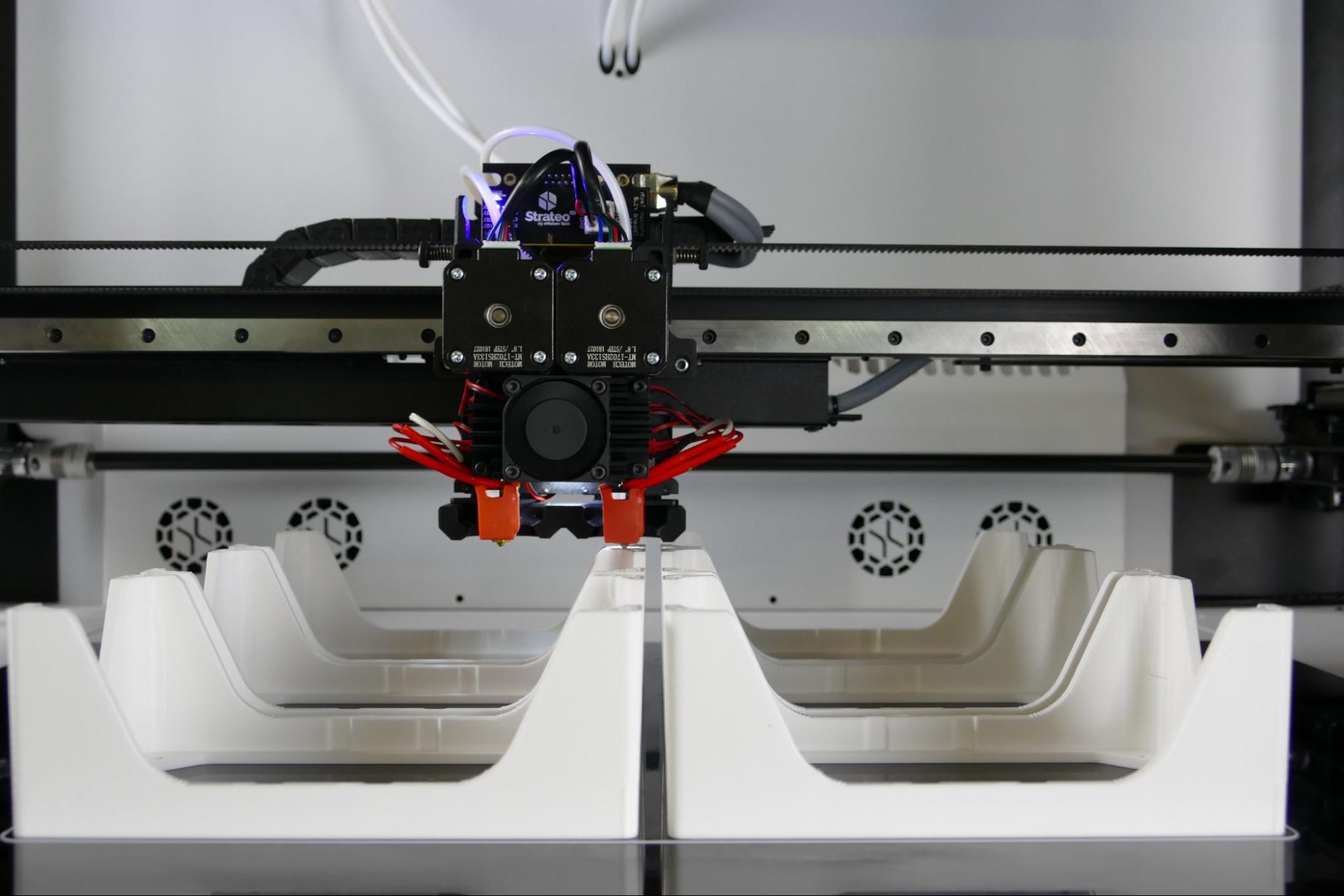
Does that mean you need to change your manufacturing process? Not necessarily. Sometimes 3D printing a part is the right choice, but some features need to be fine tuned with post processing. Using 3D printing as your primary manufacturing process makes sense if you’re producing low to mid-volume quantities or want the flexibility to change your design even when you’re in the midst of making parts.
Instead of changing your manufacturing process entirely or designing a complex, manual post-processing workflow, this article explores the benefits of CNC machining your 3D printed parts. Doing so can improve dimensional accuracy, reduce waste material, and save time and money in your manufacturing operation.
Improving Dimensional Accuracy & Precision
CNC Machining can achieve a much higher degree of dimensional accuracy and precision than 3D Printing due to fundamental differences between the two manufacturing processes. If you have certain features on your 3D printed part that need to be manufactured exactly according to your specifications (high accuracy) and/or you need certain features to be manufactured exactly the same every time (high precision), then CNC machining your 3D printed part in post could be a great option.
What kind of features on your 3D printed part might require improved accuracy or precision? Here are a few examples:
- Holes. Both circular through-holes and cylindrical recesses. A hole, of course, is typically meant for something to fit into it or pass through it. However, 3D printed holes are often slightly deformed or dimensionally inaccurate by as much as 0.5mm depending on the machine and 3D printing technology used.
- Edges/extents of your part. Dimensional inaccuracies and lack of precision in 3D printing often make fitting 3D printed parts into assemblies challenging. If your 3D printed part is intended to fit somewhere, particularly in a tight recess, CNC machining the edges to trim it exactly to your specifications could be the key to making the part fit!
- Recesses in part. Similar to edge finishing parts to get a good fit in assemblies, CNC machining in post can create accurate recesses in parts that are needed to provide the fit you’re looking for. This process can be particularly helpful for product design, as products often rely on snap-fits or interference fits to keep unique parts of the product together as a unit.
In order to incorporate CNC machining into your 3D Printing workflow to improve dimensional accuracy and precision, you need to consider a few design points. First, you need to make sure that the CNC mill can reach all desired features and that nothing obstructs the tool path. Also, you need to build excess into the part so that the CNC mill can cut away material to meet the part’s spec. Finally, build in flat surfaces for fixturing if possible — doing so will enable the CNC mill to achieve maximum precision and mitigate potential failures in the manufacturing process.
Reducing Waste Material and Overall Material Cost
Fully switching from 3D printing to CNC machining for your part would likely drive up the cost of production. A hybrid approach can minimize manufacturing costs while delivering a part that exactly suits your needs.
In general, 3D printing materials cost less than stock for CNC machining, so using 3D printing for the bulk of your part is likely to be significantly cheaper than machining a part from scratch. Furthermore, since 3D printing is an additive method, it produces much less waste material than CNC machining — which lowers material cost and makes for a more sustainable operation. And since lean, sustainable manufacturing operation is the way of the future, using a hybrid approach can be an effective way to stay ahead of the curve!
Avoiding manual post-processing
Often dimensional accuracy is achieved in 3D printed parts by manually drilling, sanding, or carving parts to achieve the dimensions and fits that are required. This takes a great deal of time and attention to detail, and so is expensive and inefficient. By eliminating manual post-processing entirely, CNC machining in post can significantly reduce the time and money it takes to produce a part.
Let’s consider an exemplary case study:
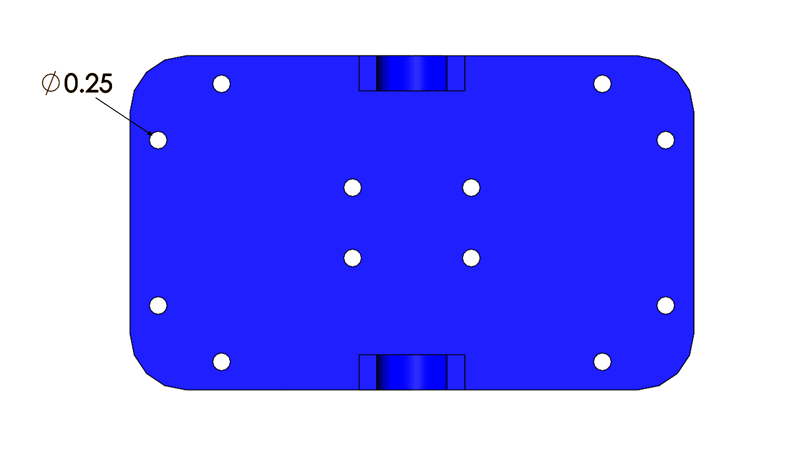
- You have a 3D printed part with a dozen 0.25” mounting holes (see images above for reference). 200 parts need to be shipped out within 1 week.
- It takes 1 person 6 minutes to drill out all of the holes on the part so that the fasteners fit properly. To get the parts ready by the end of the week, the person will need to spend 1200 minutes or 20 hours drilling parts to hit the deadline.
- Alternatively, an engineer spends 4 hours of work prepping a CNC machine tool path to drill out the parts. The CNC machine can drill out all holes in 2 minutes, cutting the overall post-processing time from 20 hours to under 7 hours. All in all, the CNC post-processing workflow takes under 11 hours vs. the 20 hour manual post-processing, making for a far quicker and more efficient production process.
Cutting out manual post-processing is a sure-fire way to keep your manufacturing costs low and produce your parts on time every time. CNC machining your 3D printed parts can help you stay true to your timelines while freeing up human resources to do more important tasks!
Conclusion
3D printing and CNC machining are two vastly different manufacturing technologies with vastly different strengths and weaknesses. However, if you utilize them together, you can develop a manufacturing method that delivers the strengths of both and the weaknesses of neither. A hybrid approach can manufacture your part with high dimensional accuracy, low material cost/minimal waste material, and without painstaking manual post-processing.
Fictiv doesn’t currently offer CNC machining services for 3D printed parts, but our CNC machining services can deliver tolerances as tight as .05mm for other plastic materials. And, Fictiv provides ways to increase dimensional accuracy by using different types of additive manufacturing. SLA (stereolithography), SLS (selective laser sintering), and MJF (multi-jet fusion) can be used for functional prototypes or even end-use production parts. Fictiv can help you unlock innovation with these 3D printing processes and more, so sign up and get started today!