Time to read: 5 min
Injection molding sliders and lifters are mechanisms that release a molded plastic part when an injection mold opens. Slides, or sliders, release external undercuts, recesses or projections on a part’s outer surface that prevent the part’s direct removal from the mold cavity. Lifters, on the other hand release internal undercuts, recesses or projections on the inside surfaces of parts.
Sliders and lifters are automatic devices that are part of the mold, but injection molded parts can also be released with hand loads — inserts placed manually into a mold and then removed when the part is ejected. For part designers, it’s important to understand that undercut placement isn’t the only consideration when it comes to injection molding sliders and lifters vs. handloads. Typically, sliders and lifters are used for higher part volumes because these actions add costs to molds.
Hand loads cost less during the initial tool build, but they add a labor cost to each part. Hand loads must be manually removed from a molded part and then returned to the tool during the next molding cycle. That’s why hand loads are used mainly with prototypes and low volumes, but they can still support complex geometries such as threads. When you request an injection molding quote from Fictiv, you’ll receive design for manufacturability (DFM) feedback you can use to make decisions about part features like undercuts and, by extension, release mechanisms. Because you’ll receive DFM feedback when we respond to your request for a quote, you can address design issues sooner rather than later. Create a Fictiv account to get an injection molding quote and discover the difference that getting early DFM feedback can make. Along with shorter project timelines, you can identify ways to reduce injection molding costs, too.
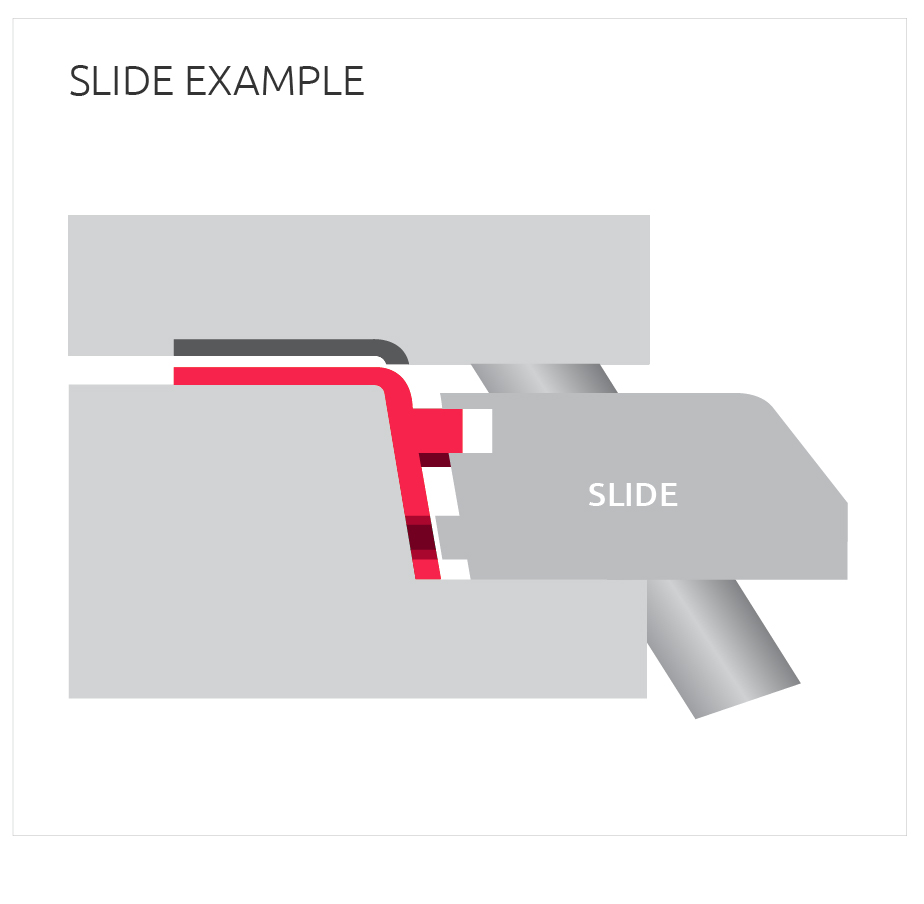
Image Credit: Tenere
How Do Injection Molding Sliders Work?
Injection molding sliders usually consist of a guide pin, slider body, forming surface, press block, wear plate, and wedge. Also, a locking mechanism is needed to hold the slide in place against molding pressures that can exceed many thousands of pounds per square inch (psi). Slider cooling channels are also used to prevent warping. Typically, sliders are purchased as off-the-shelf parts and then assembled by the mold maker.
During the injection molding process, the part is molded around features (such as undercuts) within the slider body. After cooling is complete and the mold opens, the guide pin and slider body move laterally away from the part so it can be ejected. To drive this motion, different slide actions can be used.
Slide Action Types
Cam pin slides (angle pins, horn pins) are the most common type of slide action. They have an angled guide pin that withdraws from an angled hole inside the slider body. This metal pin is mounted on the stationary side of the mold and uses an angle block to lock the slide in place. When the mold closes for the next cycle, the slider returns automatically to the proper position.
Hydraulic slides can be used if pins risk exerting too much pressure on the gibs that control the slide’s linear motion. If there are undercuts in the cavity side of the tool, locking hydraulic cylinders can be used instead. All of these slider actions have a built-in delay to control the sequencing of slide pulls as necessary.
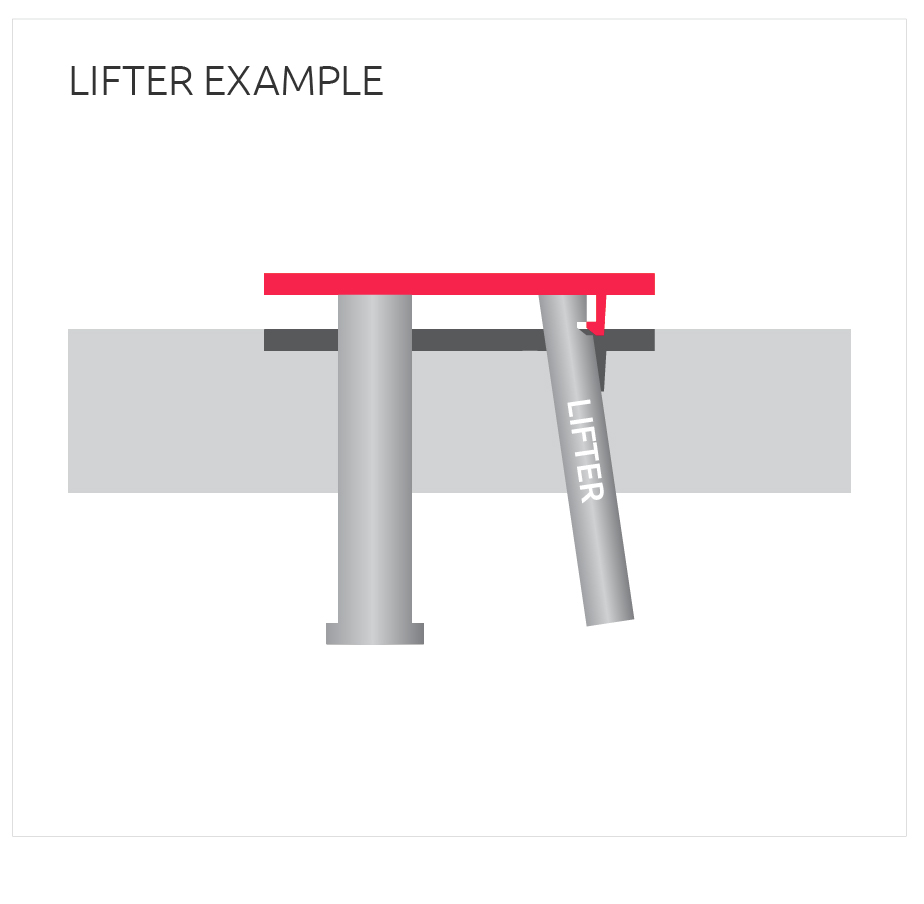
Image Credit: Tenere
How Do Injection Molding Lifters Work?
Injection molding lifters consist of a blade-like or pin-like lifting mechanism, an ejector plate, and a retainer plate. There’s also a block-like locking mechanism. Unlike a slider, which pushes the injection molded part to one side, a lifter pushes the part upward and at an angle. The ejector plate moves in the same upward direction as the lifter, which is angled rather than perpendicular to the plate. The distance that the lifter moves corresponds with the internal undercut, and an ejector pin may be used to ensure that the part doesn’t remain on the lifter. Because the lifter enters and exits a metal block repeatedly, hardened steel is often used because of its abrasion resistance — though this type of steel is relatively expensive and requires machining.
Lifter Types
Lifters in injection molding can be categorized as integral or non-integral. Integral lifters are a single unit and non-integral lifers combine two separate units. Generally, integral lifters are used for molding smaller parts while non-integral lifters are used for injection molding larger parts.
Lifters can also vary by shape. Cylindrical lifters have a simpler design and are generally easier to produce. T-shaped lifters are used with larger parts that also require a greater degree of precision. With each of these different lifter types, there’s a combination of vertical and horizontal motion during lifter action.
How Do Handloads Work?
Hand loads in injection molding are inserts that are manually placed, or hand-loaded, into the mold to achieve features such as undercuts. Before the mold cavity is filled, a worker loads the insert by hand. This hand-loaded piece is ejected with the finished part and removed so it can be reinserted during the next injection molding cycle. Although hand load inserts add labor costs to projects, they’re economical for lower volumes of injection molded parts.
As an extension of the injection mold, handloads require precise temperatures for molding quality and part-to-part consistency. If an injection molded part requires multiple hand-loaded inserts, consistent cycling may be challenging.
Fictiv’s Manufacturing Partners build hand loads that support proper cooling between cycles and can create these hand-loaded inserts from softer, lower-cost steels. By building multiple hand loads, an injection molder can also maintain proper production cycle times. Hand load features such as grippers can also support greater production efficiency.
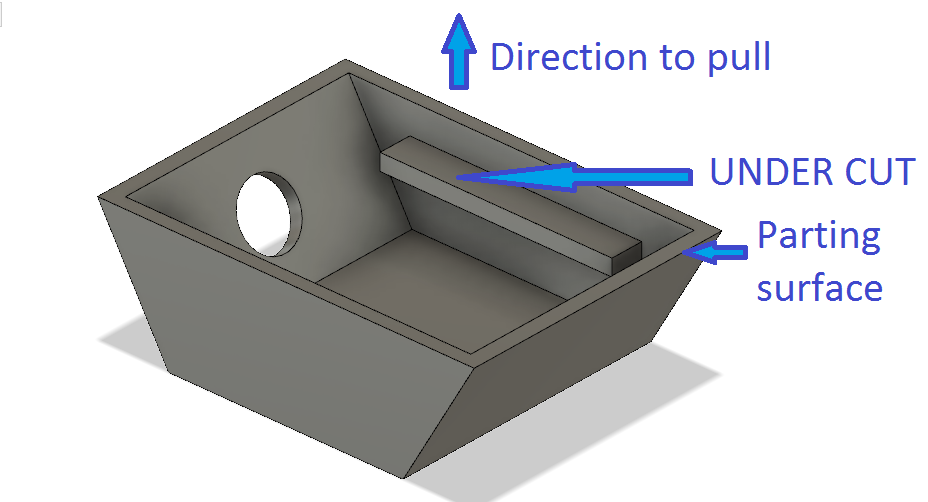
Image Source: Autodesk
When to Use Sliders, Lifters, and Handloads
Undercut location is important, but it’s not the only consideration with sliders, lifters, and handloads. Slides are used to release external undercuts and lifters are used to release internal undercuts — generally with high-volume production of injection molded parts. For prototyping and low volumes where it’s not practical to invest in automatic devices, hand loads are more cost-effective.
Hand loads also can create complex features such as undercuts and threads that can’t be formed in the line of draw (the point at which two halves of an injection mold separate). Hand loads can also be used to eliminate the need for secondary operations, such as drilling-out air holes or channels.
It’s critical for your molder to follow best practices, however, such as using a low-pressure mold close to minimize potential hand load damage and special fixtures to facilitate the extraction of complex parts.
Sourcing Simplified – Start Your Next Project With Fictiv
Fictiv is your operating system for custom manufacturing. We provide designers with DFM feedback about undercuts, threads, and other part features that can affect the choice of a release mechanism — and our expert injection molding guidance will help you make the right choice. Regardless of your order volume, Fictiv will help you streamline your workflows to reduce costs and shorten timelines. So, whether your mold needs sliders, lifers, or hand loads, Fictiv can help. To get started, create an account and request an injection molding quote today.