Time to read: 4 min
Injection molding is a widely used process to produce consumer goods from plastic, and many of our manufactured products are injection molded. From auto parts to appliance housings and cell phone cases, injected molded plastic parts are all around us.
Plastic injection molding has been around since before 1900, and there have been many improvements along the way, but it still works by pushing molten material into a cavity to form a part. When it comes to the process of injecting material into a mold, there are two main types of tools: hot runner molds and cold runner molds.
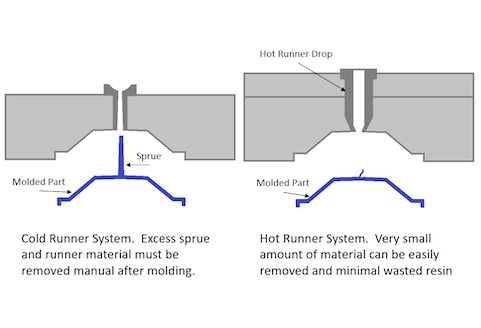
Cold runner systems and hot runner systems produce different amounts of waste.
How Cold Runner Molds Work
In cold runner molds, plastic is injected from a nozzle on the injection molding press into a sprue bushing, where the material flows through unheated channels and then finally through an injection molding gate. Because the material from the nozzle is not heated along the way, this type of mold is called a cold runner. The entire sprue is many times larger than the part, which is cooled and ejected from the mold with excess material attached. Known as scrap, this excess material must be cut away and reground to be reused or thrown away. Compared to hot runner molds, cold runner molds produce significantly more scrap.
How Hot Runner Molds Work
With hot runner molds, plastic material is injected from into a heated plate and nozzle system called a manifold. This material is then kept at its melting temperature until it reaches the mold. This approach allows for better temperature control and supports greater control over parameters such as pressure and time. Hot runner molds produce considerably less scrap then cold runner molds, and when valve gating is used, there’s almost no scrap at all.
Like cold runner molds, hot runner molds have their advantages and disadvantages. The next section in this article explains.
Comparing Hot Runner and Cold Runner Molds
That said, you’ve got to consider more than just scrap when determining whether to use a hot runner or a cold runner for your injection molding project.
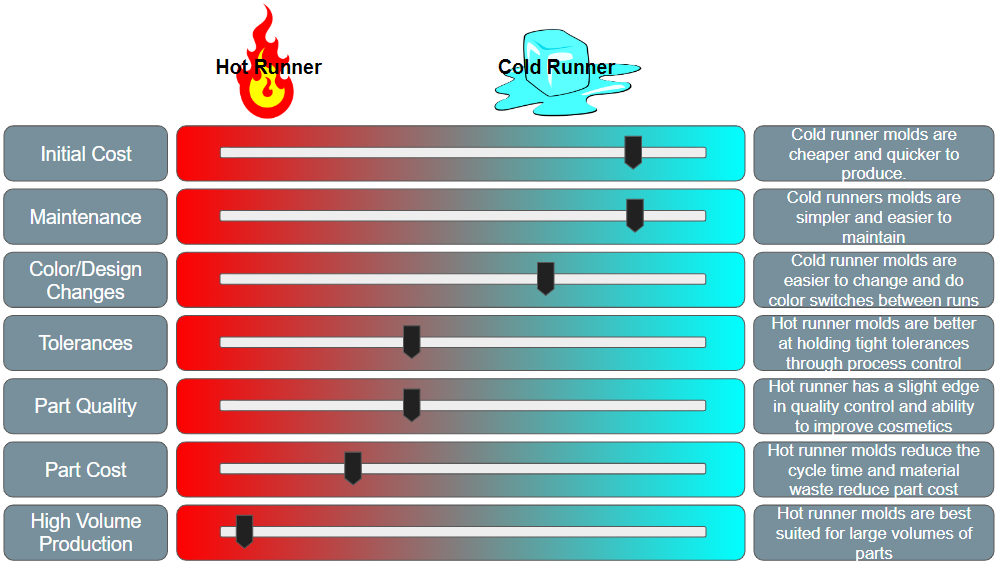
How hot runner molds and cold runner molds differ in terms of more than just waste.
The following sections examine each basis for comparison.
Initial Cost
In terms of their initial cost, cold runner molds are usually less expensive because they’re simpler in design and don’t require secondary equipment from a speciality supplier. Also, cold runner molds are generally faster and easier to produce since all of the pieces of the mold can be made and assembled in one facility.
Mold Maintenance
The simplicity of cold runner molds makes them easier to clean and maintain between molding cycles. Because these molds are less complex, an injection molder with an in-house mold shop can usually maintain them without sending anything out for repair. Hot runner molds, on the other hand, have many pieces and parts that can wear and break. New pieces may need to be ordered, and it may be necessary to send out the entire manifold for cleaning.
Color and Design Changes
When it comes to changing colors during a molding cycle, cold runner molds have an advantage. Because of their simplicity, there are fewer places to clean. This makes it easier to switch over to a new color without any bleeding from the previous pigment. Plus, changes to the tool are easier to make. Mold makers don’t have to account for the manifold, and they don’t have to consider where hot drops can and cannot be updated.
Tight Part Tolerances
With hot runner molds, the ability to control the pressure and temperature of the plastic material provides better control over injection molding tolerances. Cold runners can also support tight tolerances, but the advantage still goes to hot runner molds — for difficult and intricate difficult parts, it helps to have greater control over more parameters during molding.
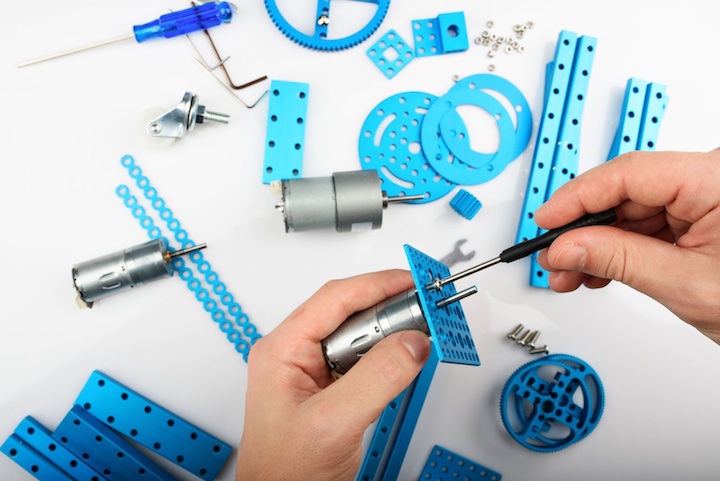
Hot runner molds provide greater control over more parameters.
Part Quality and Aesthetic Concerns
Hot runner molds preserve aesthetic intent by controlling injection molding defects such as sink marks and weld lines. When injection molded parts have thin walls or many different small features, the hot drops in hot runner molds can make it easier to fill and mold better parts.
Part Cost
Hot runner systems also have the advantage in terms of part cost because they produce less scrap and have faster cycle times. For parts that are very small or very large, the amount of scrap can be significantly higher than if a cold runner mold was used. Because a hot runner mold has higher initial costs, however, part volumes are a key consideration before investing in one.
High Volume Production
When you want to make tens of thousands of parts, the initial cost of a hot drop in a hot runner system can be offset by the savings on individual part pricing, as noted above. Also, hot runner molds typically don’t require someone to clean the gate and remove scrap. This makes for a much easier-running tool with high volume production.
Hotter Runners vs. Cold Runners for Your Project
Do you need a hot runner mold or a cold runner mold for your next injection molding project? This decision is a lot easier to make when you explain to your manufacturing partner which factors are most important, and the expected number of parts that you’ll run at a given time.
Fictiv: Your Injection Molding Partner
Fictiv is the right partner who can help you to make the right choice when it comes to hot runners or cold runners for your next project. Our injection molding experts provide guidance to make sure your designs are optimized and our manufacturing partners are incredibly skilled. So, create a free account and upload your injection molding part design and get a free quote and DFM feedback today!