Time to read: 6 min
Is your injection molding project ready for success? Sure, you’ve thought about most of the injection molding manufacturing process. You’ve designed your mold with care, researched and selected the right material, and finished your CAD file or part drawing.
But have you considered the type of injection molding gate to use? A gate might seem like a small detail, but it affects tooling costs, cycle times, and part quality. The good news is that this article will help you to choose the right injection molding gate for your next project.
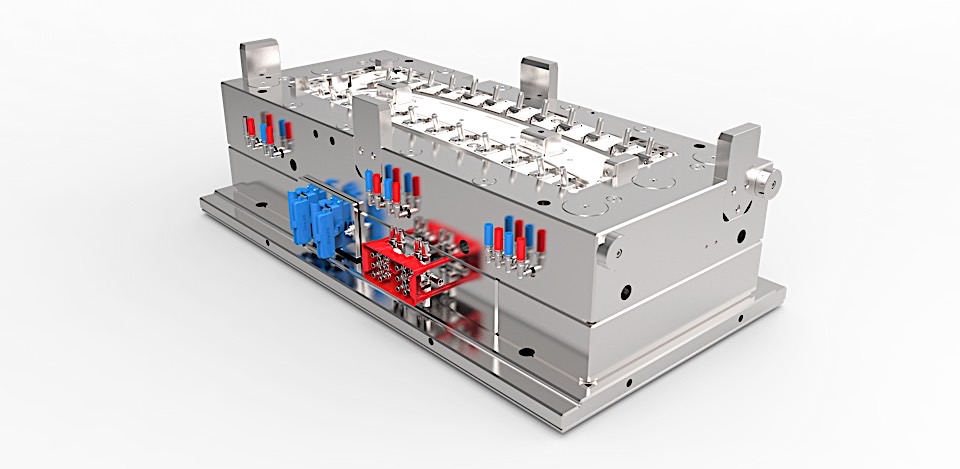
What is an Injection Molding Gate?
Injection molding forces molten plastic toward and through a gate, an opening that lets the material enter the mold cavity. Sprues and runners allow this material to flow, but it’s the gate that controls access to where molding happens. Because the size of the gate affects the pressure of the plastic, proper gate sizing is critical.
If the gate in an injection mold is too large, molten plastic fills the cavity unevenly, and makes defects such as shrinking and weld lines more likely. If the gate is too small, short shots and high levels of residual stress at the gate may result. The shape of the gate also affects the flow and can contribute to or help minimize part defects.
In addition to size and shape, injection molding gates differ in terms of thickness. Typically, large, thick-walled plastic parts require thicker gates to accommodate a higher volume of flow. Smaller injection molded parts usually require thinner gates, but not at the expense of adequate pressure.
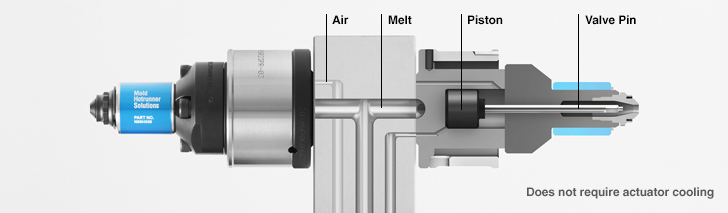
Injection Molding Gate Basics
Gates can be located along mold parting lines or at various points along the mold cavity. These openings can be wide or narrow and may feature tapered or consistent dimensions to help control flow. Because gates extend from the mold, gates also have a depth. The number of gates in a cavity and their complexity contribute to mold costs. Gates also affect cycle times and the cosmetic appearance of parts.
During injection molding, most of the molten plastic material cools and solidifies inside of the mold cavity to form the finished part. However, some plastic solidifies at the gate and protrudes from the part’s surface. De-gating, the process of trimming this excess material, is important for part quality and can be performed either manually or automatically.
Manual vs. Automatically Trimmed Gates
With gates that are manually trimmed, a worker separates the molded parts from the runners after each production cycle. This increases labor costs and may result in inconsistent cycle times. With gates that are trimmed automatically, human intervention is not required. Instead, excess gate material is sheared from the runner when the part is ejected.
Different types of gates are designed specifically for manual or automatic trimming, and while gates that are automatically trimmed might always seem like the best choice, sometimes they aren’t. For example, thick gates require manual trimming because they’re susceptible to damage from the shearing associated with automatic trimming.
Manually Trimmed Injection Molding Gates
Manually trimmed gates include edge, fan, tab, direct, disc, ring, and spoke gates.
- Edge or standard gates are recommended for flat parts. The gate’s cross-section is rectangular and can be tapered between the part and the runner.
- Fan gates have a large opening with a variable thickness. They permit the rapid filling of large parts and fragile mold sections.
- Tab gates are used with thin, flat parts that require low shear stresses. A tab-like feature confines these stresses to the gate area.
- Direct or sprue gates are used with large, cylindrical parts. A sprue feeds material directly and rapidly into the cavity.
- Disc or diaphragm gates are used with round or cylindrical parts that require concentricity. Typically, these injection molding gates are difficult to remove and expensive to trim.
- Ring gates allow material to flow freely before moving into a uniform, tube-like extension for mold filling.
- Spoke gates are round gates that have a cross in the middle. They’re used to produce tube-shaped parts, but perfect concentricity is difficult to achieve.
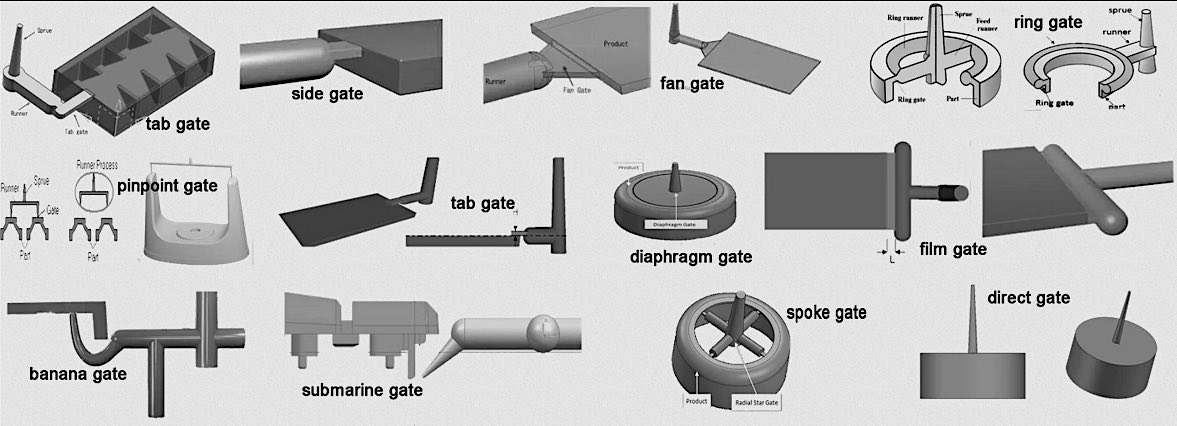
Automatically Trimmed Gates
Automatically trimmed gates include hot tip, submarine or sub gates, and pin gates.
- Hot tip gates support conical or round shapes that require uniform flow into the mold cavity. They are used in hot runner systems that keep the plastic in a molten state until it enters the cavity.
- Submarine or sub gates have a tapered channel and can help hide gate blemishes. These openings are sometimes called tunnel gates instead.
- Pin gates are used with fast-flowing resins and when a part’s cosmetic appearance is important. Pin gates are used typically with parts that cannot have vestiges on either side of the parting line.
Depending on the mold system, other types of gates can be used instead. For example, hot runner systems can use valve gates where mechanical action causes a valve stem to move and then seal the gate opening. Valve gates cost more than other types of gates but can improve part quality by reducing defects such as witness marks. Valve gates also improve productivity because they support automatic trimming for faster cycle times.
Choosing Gate Location, Size and Geometry
The location of an injection molding gate affects part quality. For best results, gates should be placed away from pins or cores because these obstructions can cause molten plastic to flow around them and form weld marks. To ensure complete filling of the mold cavity, it’s best to locate gates closest to the thick-walled areas of parts. However, because gates may leave blemishes, you should avoid placing openings near visible part surfaces.
Different types of gates also require different locations. Many gates can be located near mold parting lines, but hot tip gates are usually located at the top of the part instead. Submarine gates can also be moved away from the parting lines, which provides additional flexibility during mold design. Pin gates are usually found on the B-side of the mold where the ejector pins are located.
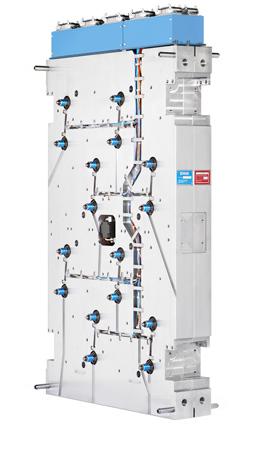
Gate size is another important consideration. In general, the width of the gate is based on the volume of the mold cavity and the depth of the gate is based on nominal wall size. However, because different materials have different flow rates, the type of plastic is a factor. For example, because polyethylene (PE) and polypropylene (PP) flow readily, gate depths may be based on only 50% of the part wall thickness.
The geometry, or shape of the gate also affects performance. For example, cashew-shaped sub gates are commonly used but not always the best choice in terms of flow restriction and fill pressure. For best results, gates should always taper down to the orifice to avoid flow restrictions. Otherwise, you may get flow imbalances and an increase in fill pressures.
Additional Considerations: Injection Speeds
High injection speeds through a gate can cause friction-induced increases in temperature, and if there’s enough additional heat, damage to the molecular structure of the plastic may occur. Yet slowing down the injection speed to avoid degradation may reduce a part’s mechanical strength and result in weld lines. Plus, slower cycle times mean fewer parts per hour and higher processing costs.
Knowing when to increase or decrease the injection speed isn’t just about gate size, however, which is why injection molders use a relative viscosity vs. shear rate curve to find the right balance.
Optimize Your Gates and Set Up Your Project for Success
Injection molding gates do more than affect fill rates. They also help drive tooling costs, cycle times, and part quality. For designers and engineers, it’s important to understand how injection molders can optimize the gates that connect sprues and runners to mold cavities. Gate type, trimming method, location, size, and geometry also determine quality and performance.
Fictiv has the application experience and technical expertise to optimize the gates in your injection molds, and you can learn all about our injection molding capabilities here. Whether you’re just getting started with injection molding or have been shooting plastic for years, we’re ready to help you manage the entire process to deliver quality injection molded parts on time. Create an account and get a quote today!