Time to read: 4 min
Weld lines in injection molding are a type of cosmetic defect that detracts from a plastic part’s appearance. In some cases, a weld line can also cause a loss of strength and impact resistance. Known also as knit lines and weld marks, weld lines are difficult to eliminate completely, especially if your injection molded part requires holes. Yet there are ways for designers to minimize the appearance of knit lines and their effects on injected molded products.
Part design is important, but the construction of the mold and the skill of the injection molder can also help to reduce weld line defects. Fictiv works with a global network of carefully vetted Manufacturing Partners and we provide quality tooling that’s also cost-effective, and our platform offers design for manufacturing (DFM) feedback when you request a quote. Keep reading to learn more about how to avoid weld marks in injection molding and create a Fictiv account to request an injection molding quote today.
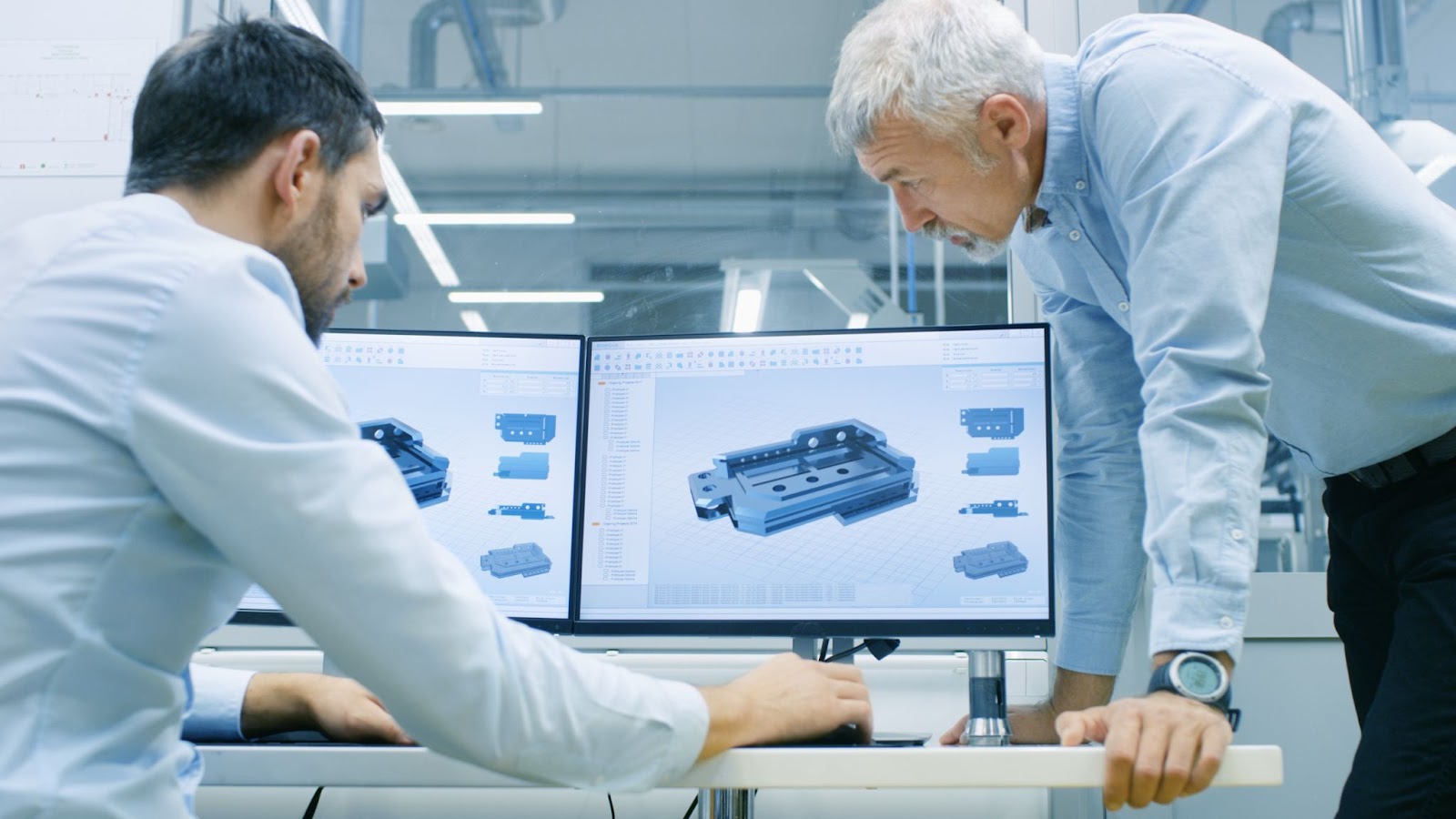
What Are Weld Lines and What Causes Them?
During plastic injection molding, molten material flows through an opening called a gate and fills a mold cavity. The leading edge of the flow, or the melt front, may encounter obstacles such as the core pins that are used to mold holes in plastic parts. If the melt front encounters an obstacle, the flow separates and moves past it in two different streams. These streams come together again once they’ve passed the obstacle, but they might not mix. If that happens, the point of contact forms a weld line.
Sometimes, the two flows don’t mix because some cooling and re-solidification of the plastic material have occurred. Alternatively, the flows may meet in a way that their orientation to each other doesn’t readily support mixing. As the plastic flow continues through the cavity, it mixes and becomes one melt front again, but the knit line remains near the obstruction, and issues with tooling construction or plastic processing may cause it to weaken the plastic part.
How to Avoid Weld Lines in Injection Molding
To avoid weld lines completely, you could machine features such as holes after injection molding is complete — but that adds costs and is likely extend project timelines. If machining isn’t an option, consider how part design, mold design, and plastic processing can minimize and reduce knit lines instead. There may be some tradeoffs to consider, but Fictiv provides expert DFM feedback to support your decision-making.
Part Design
Your choice of a color for an injection molded part can make weld lines seem more or less pronounced. That’s why when part designers ask for silver or another metallic color, Fictiv recommends painting the parts instead of adding a colorant to the plastic. Within metallic colorants, there are flakes that tend to make weld marks more prominent. Using thinner wall sections and lighter colors, such as white, can also help reduce weld mark visibility.
For most part designs, the features that create weld lines (such as core pins for holes) are necessary and cannot be eliminated. Imagine an injection molded wheel without a hole for a fastener, or an injection molded nozzle without an opening for fluid flow. For products like these, weld lines are typically unavoidable, but changes to mold design and plastic processing can minimize their appearance or change their location so that cosmetic defects are less prominent.
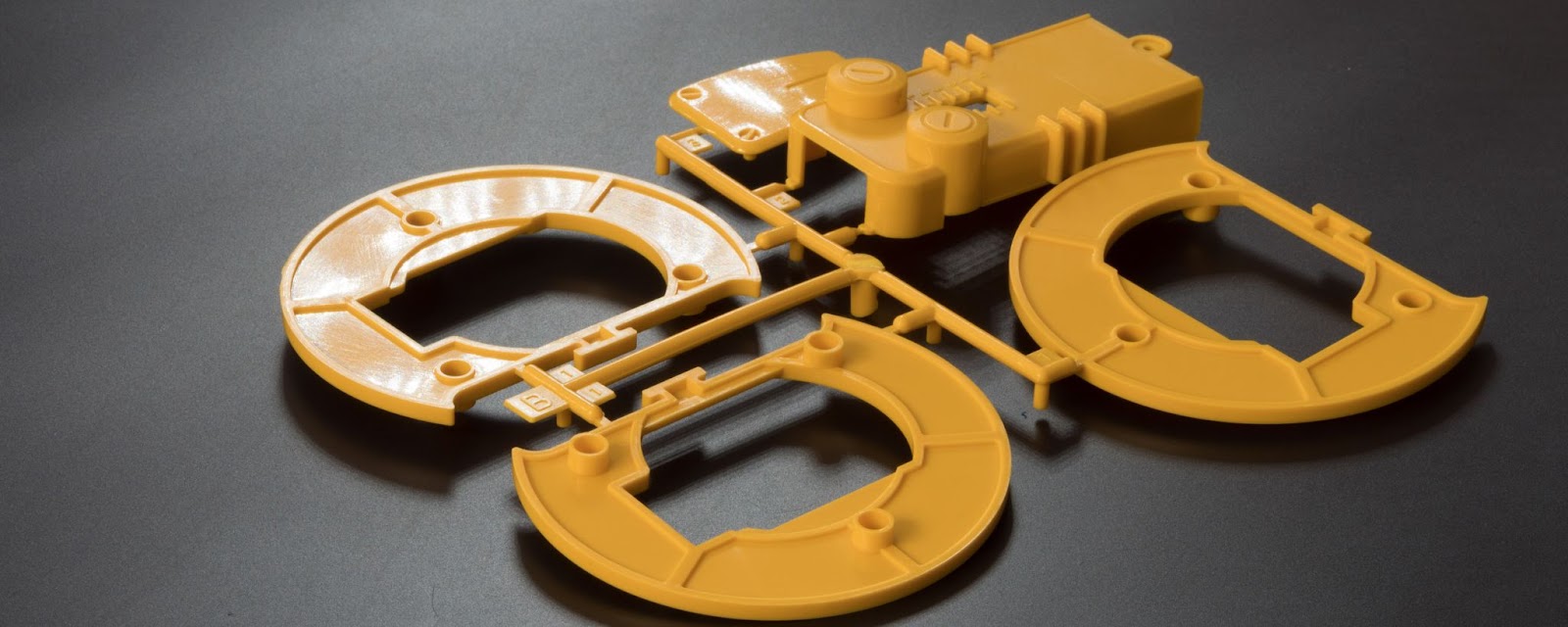
Mold Design
There are three ways to modify an injection mold design to minimize weld lines:
- Gating
- Runner Type
- Venting
Gating
Gate location is the point where molten plastic enters the mold cavity, and moving the position of the gate can change the flow and move weld lines away from prominent surfaces. Consider an injection molded flashlight case. If the case is a box and sits flat, a designer could move the gate so that the weld line appears on the bottom of the case, where it’s less visible.
Runner Type
Using a mold with a hot runner system instead of a cold runner system provides greater control over the material. In a hot runner system, the plastic remains in a molten state until it flows into the mold cavity. In a cold runner system, both the runners and the mold remain at the same temperature. Ultimately, hot runner systems provide greater temperature control, which enables a skilled injection molder to reduce part defects.
Venting
Because weld lines aren’t always just cosmetic defects, proper venting is important. Otherwise, trapped air can restrict the flow of the material and weaken the strength of the plastic where weld lines form. This makes correct venting essential for producing good mechanical properties, and not just a clean appearance.
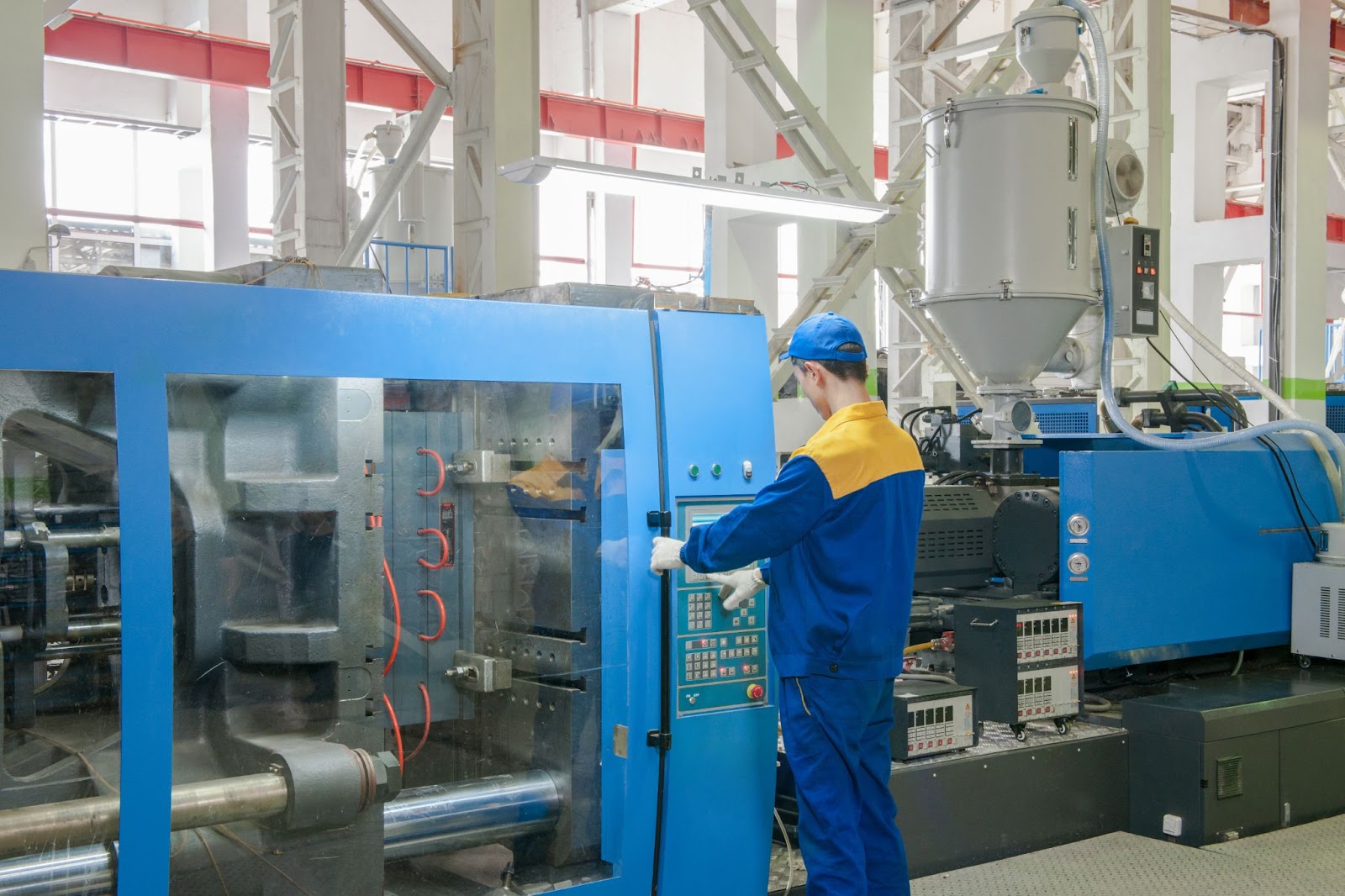
Plastic Processing
Plastic processing has two key aspects that affect weld lines.
- Plastic melt and mold temperature
- Injection speed and pressure
Plastic Melt and Mold Temperature
Increasing the temperature of the metal mold or the plastic material helps reduce weld lines because hotter temperatures allow for the two melt fronts to fuse together more completely. But it’s important to keep temperatures within the recommended range of the plastic manufacturer’s material data sheet. Otherwise, plastic degradation may occur.
Injection Speed and Pressure
Increasing the injection speed and/or pressure during injection molding causes the melt fronts to remain hotter because the mold cavity fills more quickly. This approach can shorten the length of the weld lines that appear and support better fusing overall.
Weld Line Injection Molding Help and More
A great part design is important, but having the right tooling manufacturer and injection molder are critical to the success of your project, too. Fictiv is your operating system for custom manufacturing and our technical experts are ready to help guide you through the entire injection molding process to minimize weld lines and ensure you get quality parts.
We provide everything you need for a successful injection molding project, from DFM feedback to tooling oversight and quality assurance. To get started, create a Fictiv account and request a quote today.