Time to read: 7 min
Your CNC machining process is only as good as your workholding setup! CNC work holding methods keep your part rigidly in place and reduce the stiffness. You can also refer to work holding as fixturing. A good CNC workholding setup is key for locating the next part to be machined. Fixturing is also important for safety!
The Importance of a Strong CNC Workholding Method
When machining anything, the stiffness of the entire operation is extremely important. Reduced stiffness will cause vibration and a significant decrease in the accuracy and precision of your machining process. The “chain of stiffness” is made up of the machine itself, the tool, your part, and the fixture holding your part.
If your part is able to move while being machined, there is no way you will be able to maintain any tolerances set forth by the design or drawing. Even a slight movement during machining results in poor accuracy. If you try to machine multiple parts with a poor setup, each part will be significantly different from the rest, resulting in low precision.
Manufacturing effort also comes into play when thinking about your workholding setup. For one, with an insufficient setup you will most likely have to remake the part. With a thoughtful workholding solution, you can reduce the number of machining setups. By designing useful features for fixturing into your part, you can reduce the effort and cost of machining.
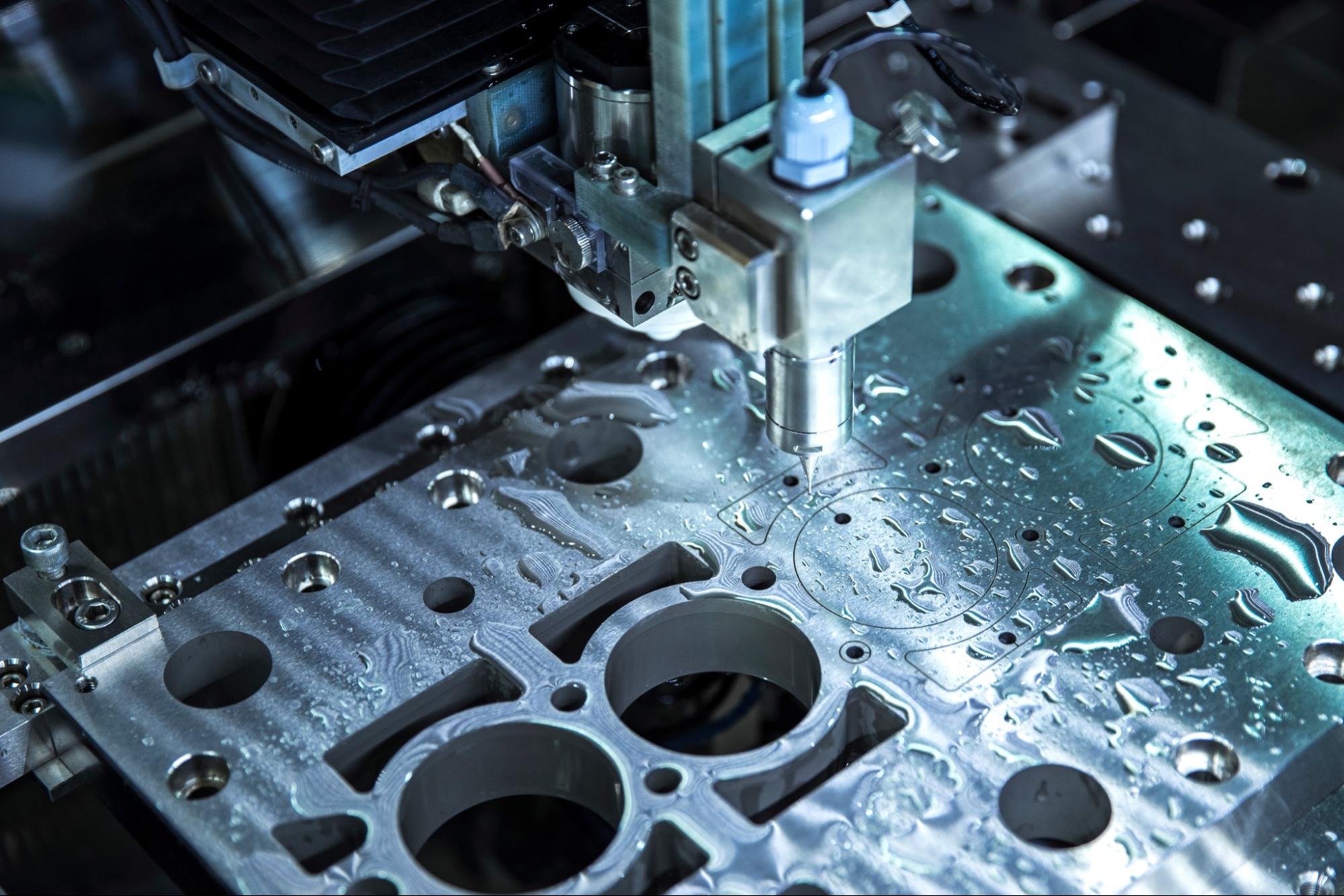
Finally, a good CNC workholding setup is necessary for safety. Oftentimes, the part will be enclosed inside an industrial CNC machine to protect people from flying objects, but what if it’s not? Terrible things have happened when your parts or pieces of a broken tool go flying. Even aside from your safety, you want to think about the safety of your machine. Disasters can happen when a part comes loose or a tool crashes into something. Your part needs to stay in one place, even under the tremendous forces of a CNC machine. You also need to ensure that the fixture is not going to get in the way of the tool.
In short, it is well worth thinking about how you are going to hold your material in place while it is being machined.
Things to Think About For Your Workholding Setup
Certain materials are easier to machine than others. Similarly, certain features are going to be easier to machine. For instance, brass is one of the softest metals, and removing material is going to take a lot less effort than a material like steel. The amount of material you are removing is also important to think about. With knowledge of the potential load, you can start narrowing down options for CNC workholding solutions. If you are machining a small brass part, you may be able to use a slightly less sturdy but also less invasive workholding method. With a large steel part, you’ll want more substantial fixturing.
Another important consideration is where your fixturing method is going to hold on to your part. Is it a standard block with parallel edges that can be placed in a vice? Do you need to have multiple sides reachable by the tool in order to avoid an extra operation? Is your part a funky shape that requires a creative method to fixture it in your machine? These are all good questions to ask yourself when choosing a CNC workholding device.
Finally, you want to consider how many parts you will need to make with your fixture. If it is going to be a high volume operation, it may be worth it to invest some more time and effort to create a custom fixture that can hold many parts at once. If you’re only making a few parts, you may want to stick with one of the other fixturing options we’ll get into below.
Examples of Workholding Solutions
Vise
We’ll start with the classic machinist’s vise. A vise can be clamped down to the table of your CNC machine. A vise won’t work for every part, though. There is a sweet spot in sizing because of limitations on how large your part can be – a vise can only open so much. Thickness matters as well – a very thin part may be warped when you tighten the vise. You can also only use a vise for parts with parallel edges. When using a vise, make sure that your part is level, and that it is tightened down fully. If set up correctly, a vise can be extremely repeatable and accurate!
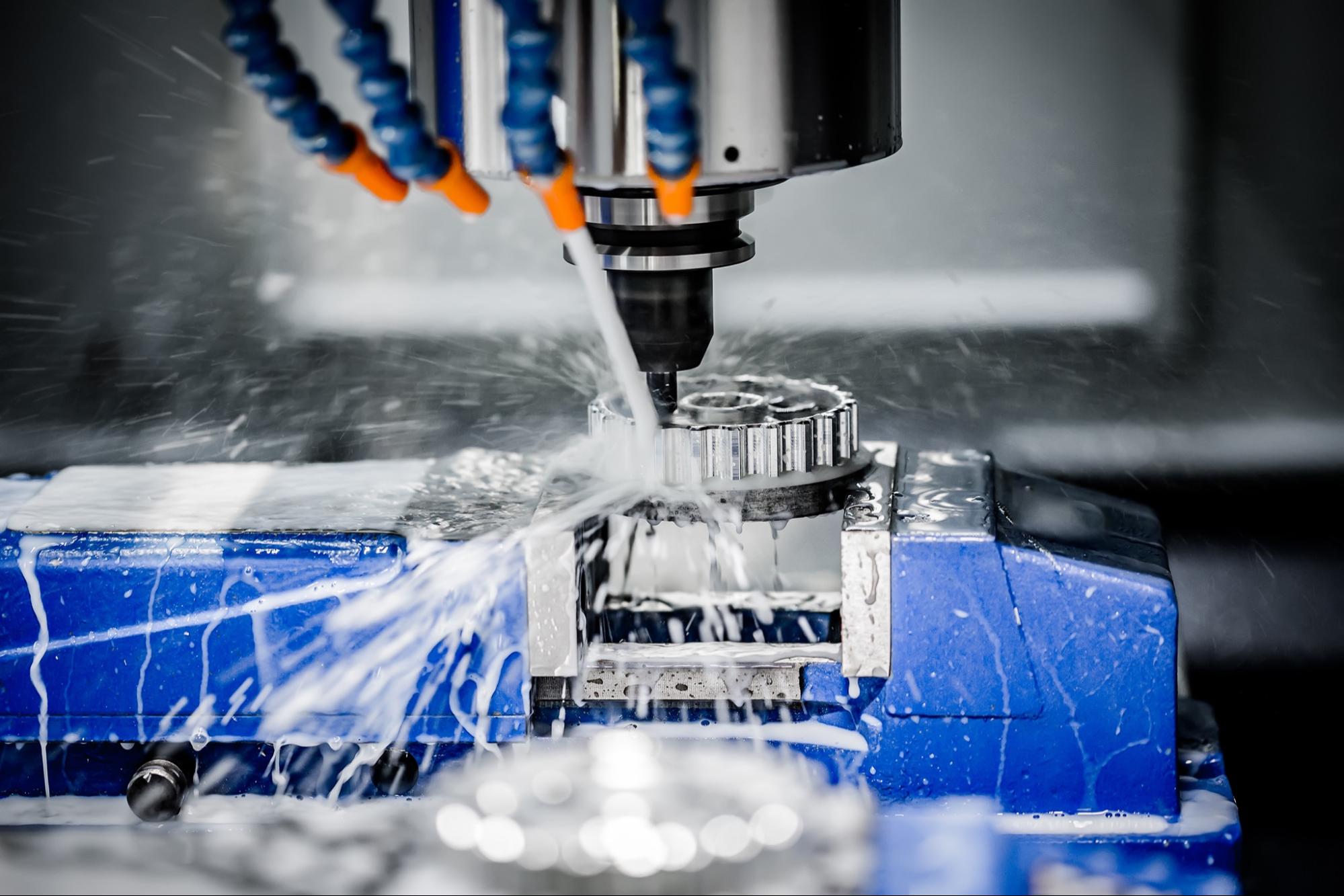
Soft Jaws
A good work holding method for any part that needs to be held securely but has an irregular form factor are soft jaws. Soft jaws refer to a set of two parts machined out of aluminum. Each part is flat and straight on one side (to align with one side of the vise) and has the profile of your part machined into the other side. This way, you can hold your part in a vise even if it is round or has non-parallel sides. Each soft jaw is bolted to a side of the vise once it’s ready to be used. Soft jaws are useful because aluminum is quick and easy to machine. You can also machine them over and over again to work for different parts. Soft jaws can be reused if you are machining multiple units of the same design.
However, soft jaws are not well suited for high volumes of parts. They tend to wear out after many uses. If you are making thousands of parts, you can use steel jaws, which are the same concept, but made from steel. However, steel is much harder and more time consuming to machine than aluminum. When you move into large production volumes, it may be more efficient to create a fixture than can hold many parts in one machine. With either of these machined jaws (aluminum or steel) you are limited by the number of vises that can fit into a machine.
Step Clamps
Step clamps, also known as toe clamps, are a very common workholding method for manual milling. This clamping system utilizes the T-slots on a machine’s bed. They are an extremely firm way of holding down your workpiece and are another effective CNC workholding solution. However, there are some downsides that make other workholding devices a better choice. Step clamps can be time consuming to set up, although they are adaptable to a variety of parts (as long as you have a flat surface to clamp on. They are not as repeatable as other workholding fixtures. As soon as you loosen the clamp, it no longer stays in the same location. You then have to reconfigure the setup again for the next part. Step clamps are good for holding big plates to be machined and for clamping down fixture plates.
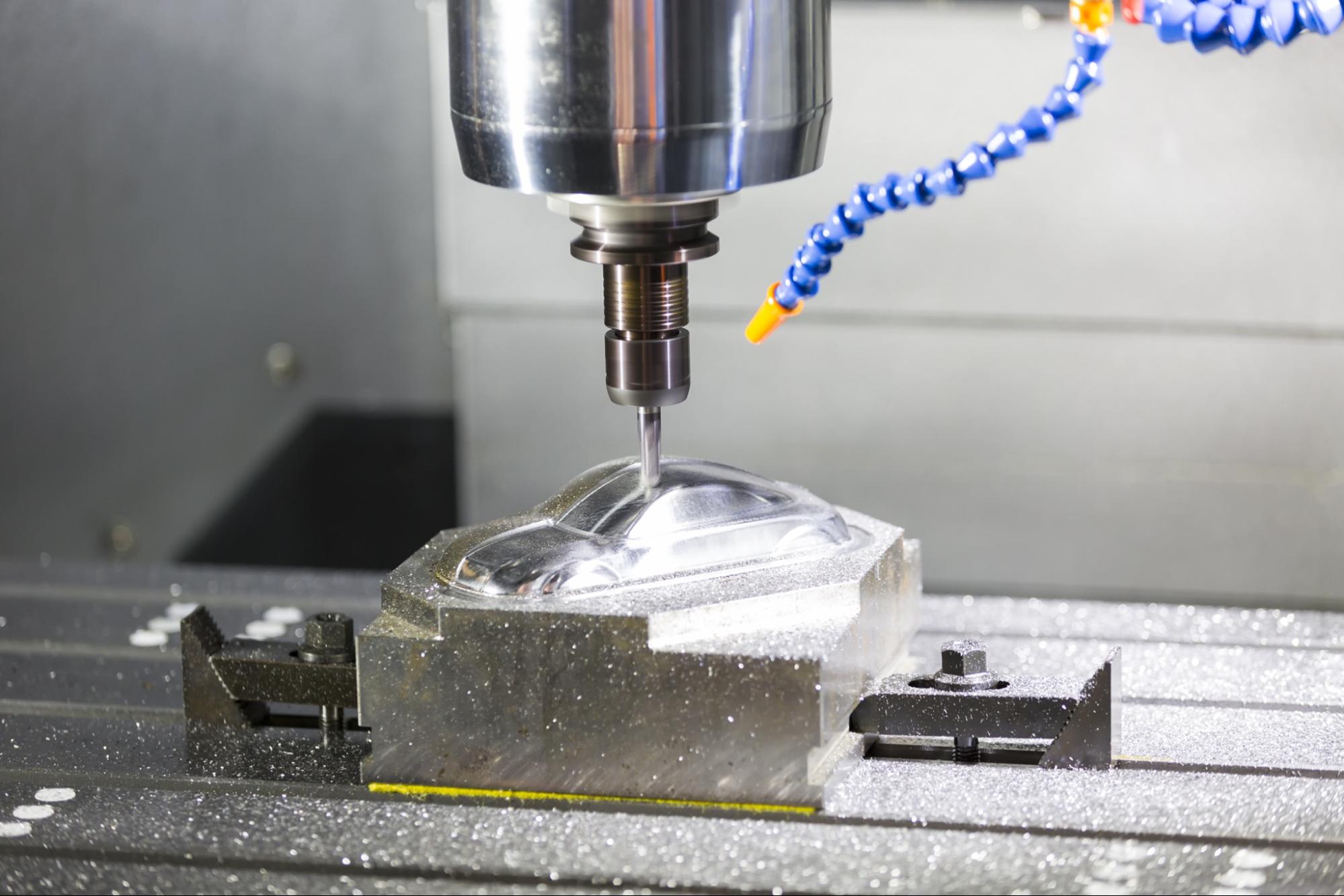
Fixture Plates
Fixture plates can be used to mount a wide range of parts to be CNC machined. You may also hear them referred to as tooling plates. They are made of aluminum or steel and have a grid of holes. Some of these holes are intended for dowel pins and some are threaded for bolts. Fixture plates are a very useful workholding method due to their repeatability; each hole has a known location and won’t move once the plate is installed. The dowel pin holes are useful for locating your fixture or part on the plate. The threaded holes are good for bolting down your fixture or part.
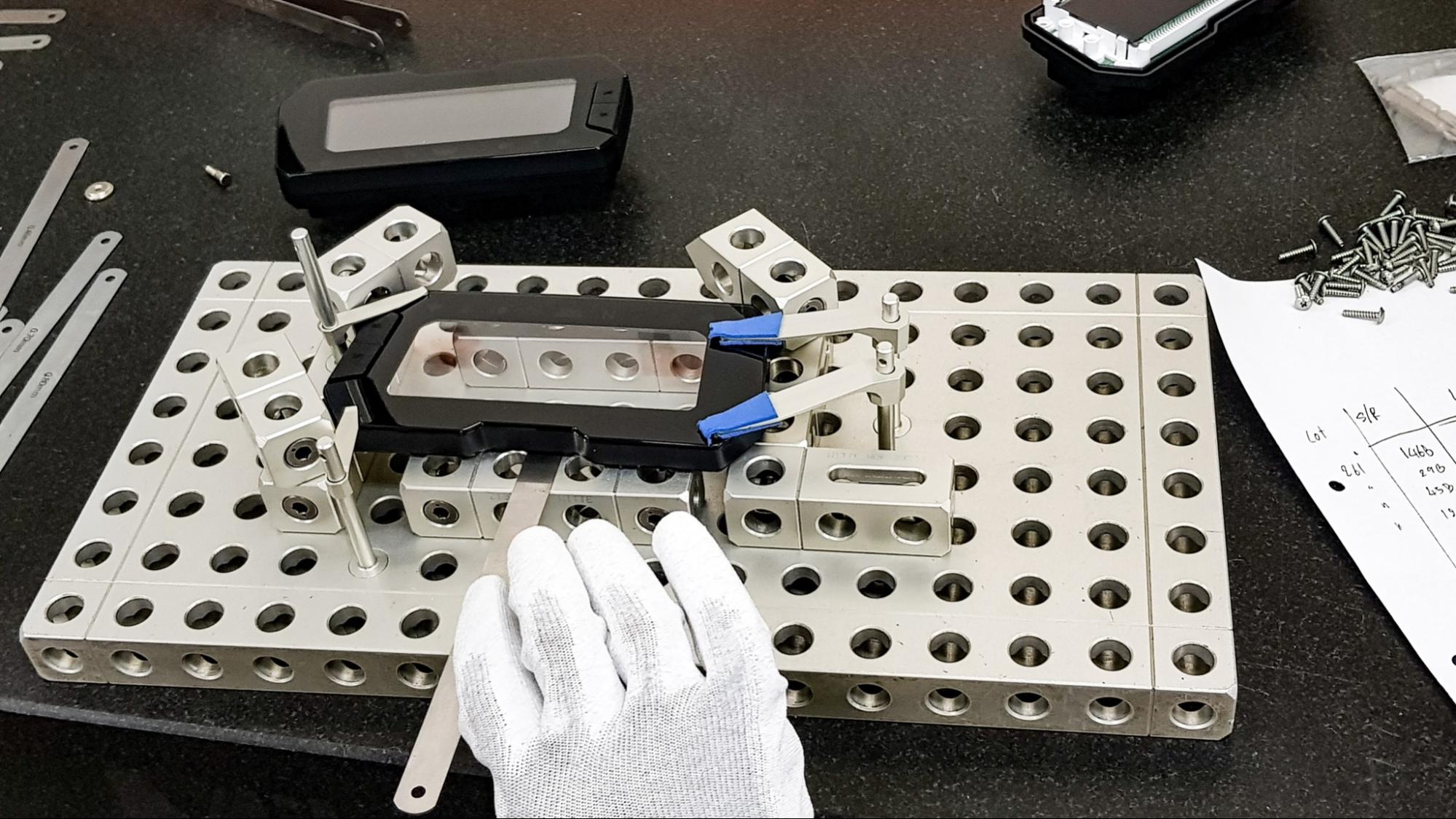
There are a couple different ways to use a fixture plate. One method is to design in bolting holes to your part. This workholding method allows you to have access to multiple sides of the part and machine interesting geometries or surfaces. However, it will require post-processing to remove the fixture holes.
Another method is to design a custom fixture that holds your part. Then, you then bolt that fixture to the fixture plate. This takes advantage of the locating features of the fixture plate. Fixture plates also protect the table of your CNC machine from a wayward tool. There are many options for nuts, bolts and other tools to use with a fixture plate, so get out there and explore!
Advanced Applications
The CNC workholding methods that I have reviewed so far are great for a standard 3-axis CNC milling machine. These machines have many capabilities, and with creative fixturing you can machine a lot of different geometries. However, there are some limits to what a 3-axis machine can do. You may find yourself machining something more complex on a 4- or 5-axis machine. 5th axis workholding is a whole different story. With the additional range of motion, the machine has much greater access to the workpiece. More axes means more fun but also more potential for crashing! Pay extra attention to allowing access to multiple surfaces. You also need to leave clearance around the workpiece and machine table for the cutting tools to move.
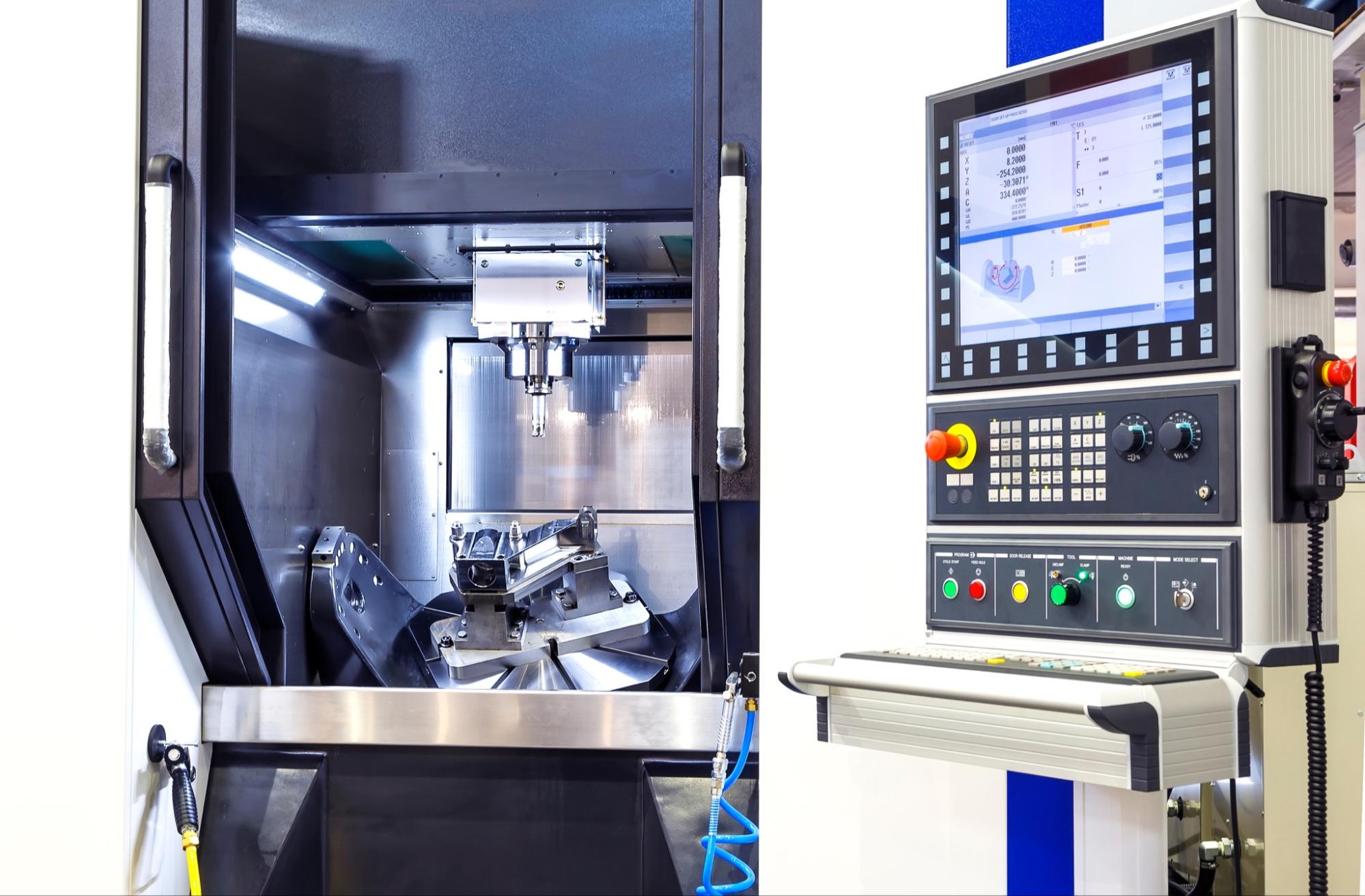
I hope that this article has, at the very least, convinced you to pay attention to your CNC workholding solution. Your workholding fixture can affect the design of your part, and vice versa (engineering and manufacturing go hand in hand). Fixturing your part is also important for precision, accuracy, and safety!
You can significantly reduce manufacturing effort if you design your part to be easily fixtured during machining. Check out our DFM for CNC Masterclass to learn more, or get an online CNC quote. And if you found this article helpful, share it on LinkedIn!