Time to read: 3 min
3D printing is a fantastic solution for building fast, cheap prototypes. Small enclosures? Piece of cake. 5 variations of a door handle? No problem. But what happens when your dimensions surpass that of a 3D printer build bed?
Here are a few alternative methods for building prototypes larger than 1-2 ft.
1. 2-Dimensional Cutters
CNC routing, water jet, plasma cutting or laser cutting are all great options for building large prototypes. These processes are primarily 2D in nature, but can offer a greater level of automation for creating multiple prototypes and prototypes with more intricate geometries.
You can also choose from a large assortment of materials, including metals, plastics, and wood.
The biggest challenge when using this approach will likely be joining the parts and this may require some creative design solutions. Here’s a handy guide from Make Magazine to help you out.
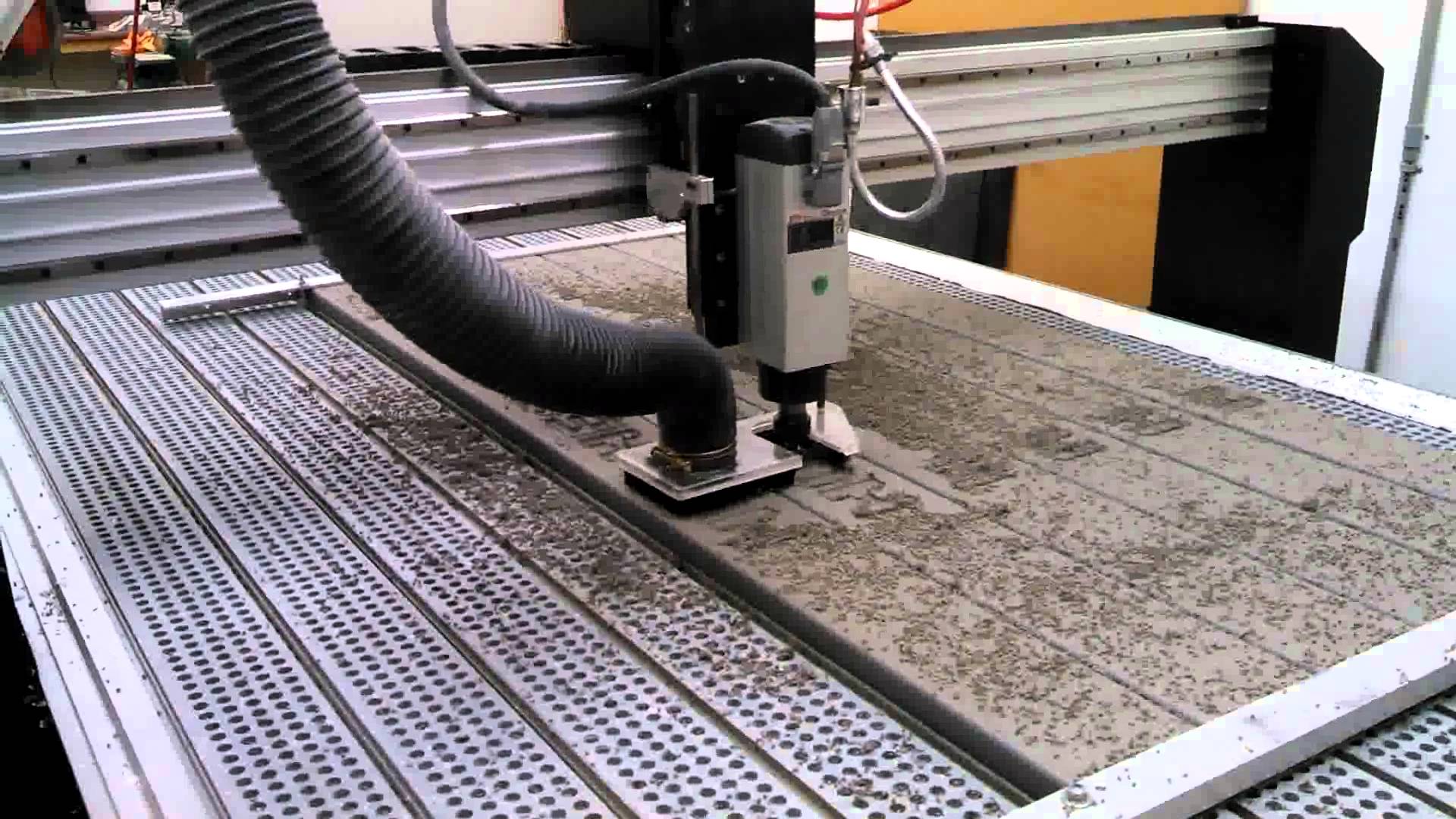
2. Aluminum Extrusions
Aluminum extrusions are a great off-the-shelf solution for building large prototypes. The material is strong, light and relatively easy to procure, cut and join.
Aluminum extrusions can be found in a large number of profile shapes and sizes and there are also plenty of fasteners to make different types of corners and joints using cnc machining aluminum.
3 Popular options for sourcing aluminum extrusion are 8020.net, McMaster Carr and Misumi.
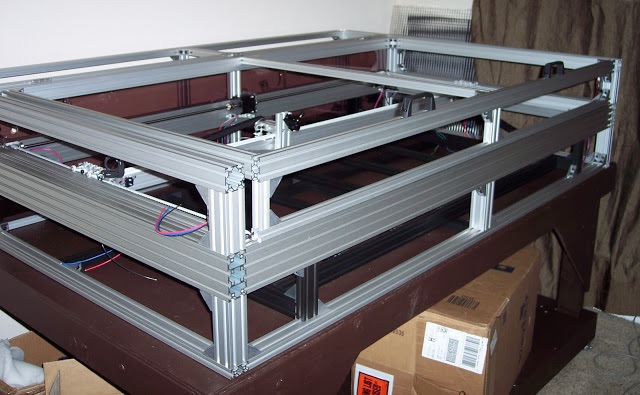
3. Clay
Clay is a popular choice in the automotive industry for creating full size models. Using clay obviously won’t result in a functional prototype, but it’s a great material for iterating on form and much easier to work with, and cheaper, than metal.
By using a cheaper, more malleable material in the early prototyping stages, you can iteratively develop the form of your product before turning to more expensive and time consuming processes and materials.
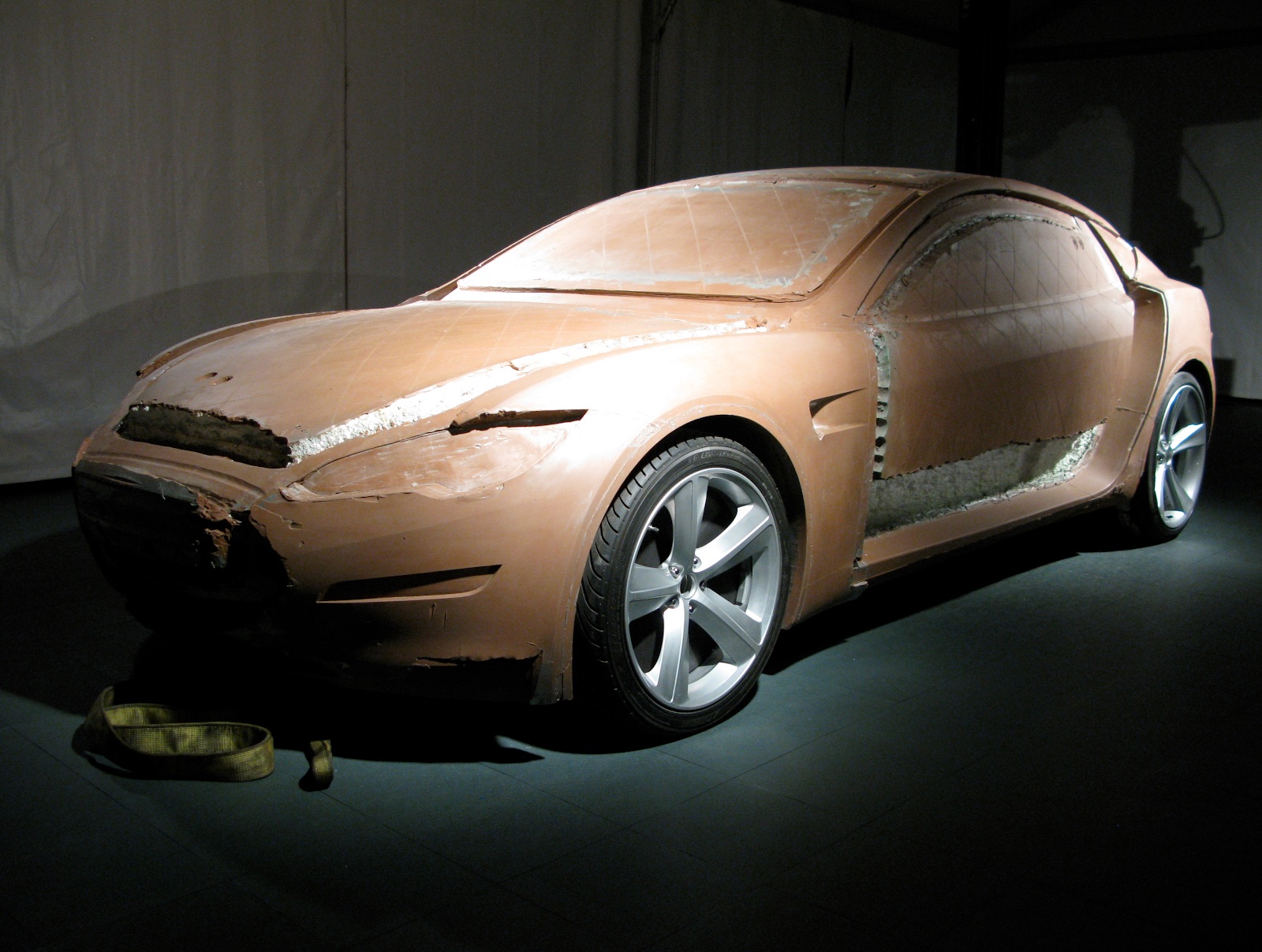
4. Foam
The other main option for creating large scale cosmetic models is foam. Foam is really easy to work with for rough, early stage prototypes to get a basic sense of the product form.
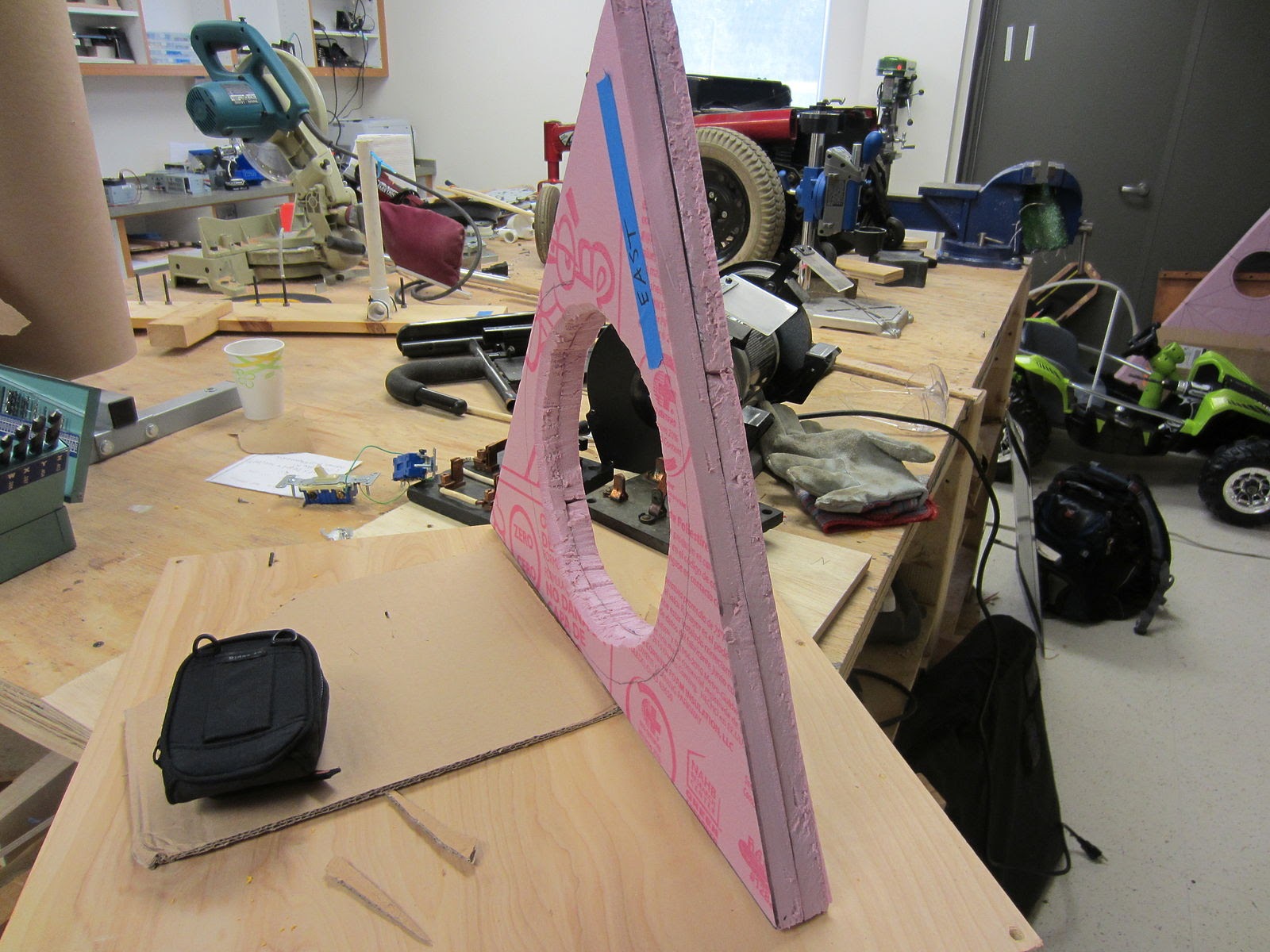
5. 3D Printing
While 3D printing provides some clear size limitations depending on the build bed, you can actually split your model into multiple pieces so it can either fit better on one build bed or fit onto multiple build beds, reducing print time.
For example, we recently built a pretty awesome Daft Punk Helmet by splitting the model into multiple pieces and then welding the parts together.
With large scale parts, FDM will be your most cost effective 3D printing option, but SLA and SLS printing are also viable options if your project requires a higher resolution finish.
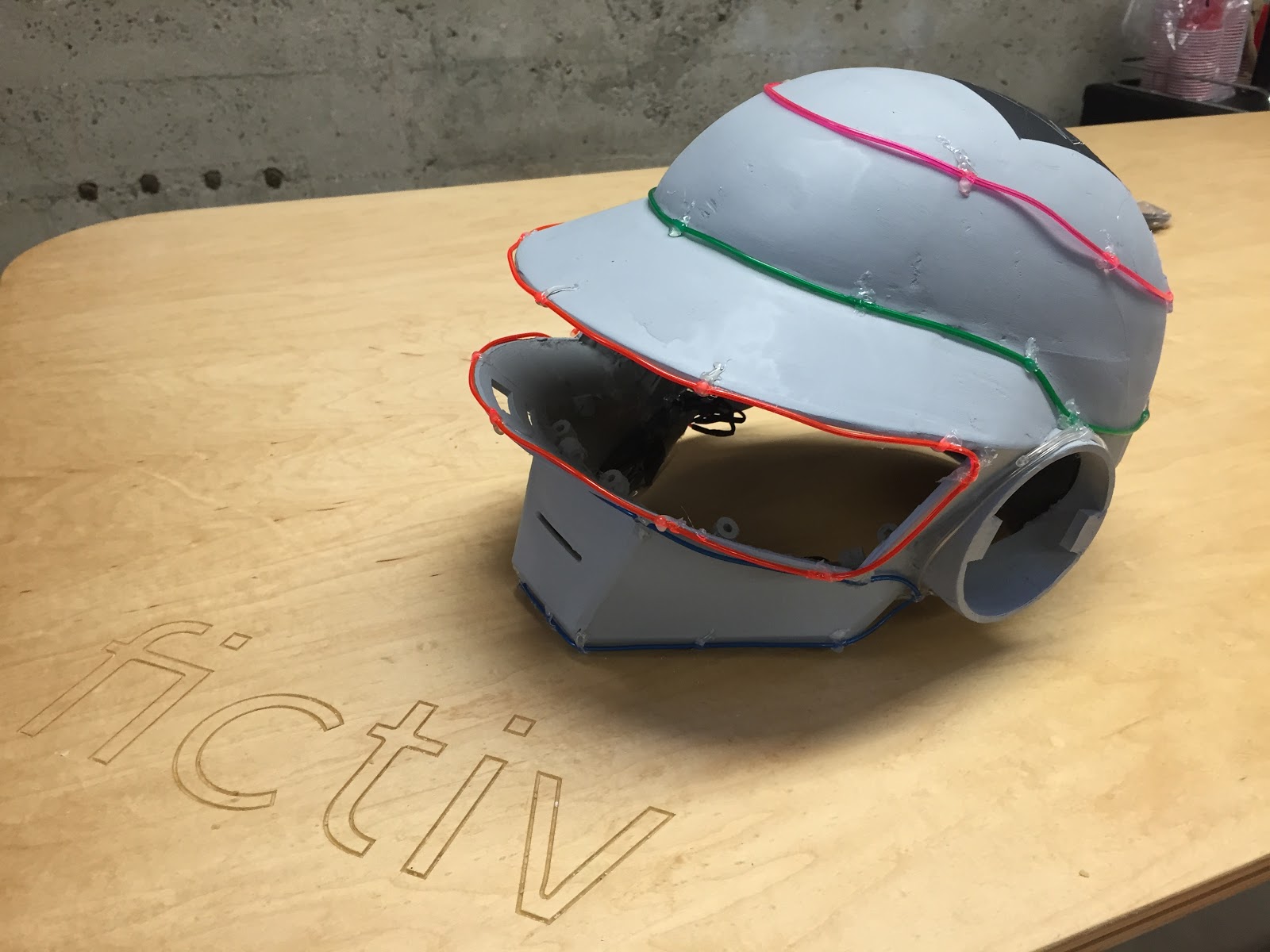
Main Takeaways
So what’s the right choice for you? Like most things, the answer is: it depends. An even better answer might be to combine multiple approaches.
For example, you might build a metal frame utilizing cnc aluminum extrusions and skin it with laser cut panels. With a frame and skin approach, the box becomes very modular, allowing individual panels to be replaced and updated on an as-needed basis.
The hardware development process is very iterative, involving multiple prototypes of increasing quality and complexity as the project progresses. Using one or many of the processes outlined above can help you progress efficiently from idea to product, even when dealing with large scale parts.
Browse our site to learn more about Fictiv’s CNC Machining Service, then create an account and upload your designs to get an instant quote and free DFM feedback today!