Time to read: 4 min
Plastic injection molding can produce anywhere from a few hundred to a few million parts. To ensure that parts are produced consistently, with minimal defects, and at the lowest possible cost, designers should follow some established guidelines. Wall thickness is a key consideration critical to the success of your injection molding project.
Download Fictiv’s Injection Molding Design Guide
What is Wall Thickness in Injection Molding?
Injection molded parts can have a shell-like structure with molded surfaces and supports. Examples of these supports include walls, ribs, and gussets. The image below shows an example where the external walls on semi-rounded parts are especially easy to see.
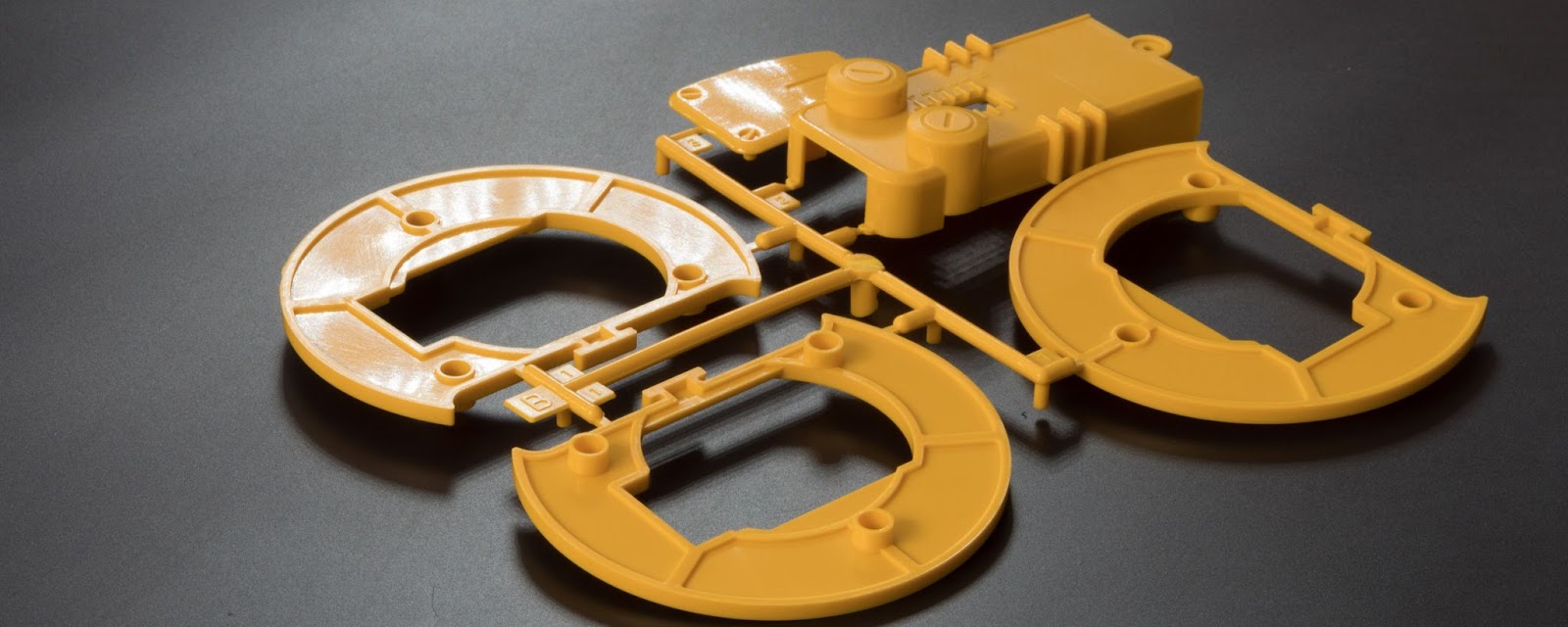
Wall thickness in injection molded parts generally ranges from 1 to 5 mm. The recommended thickness depends on the plastic material, the part’s requirements, and factors such as mold flow. For the best results, a part’s walls should be fairly consistent — that means avoiding designs with widely different walls thicknesses.
Note, however, that walls are tapered. In other words, a wall doesn’t have the exact same thickness from the base to the top. Typically, the base of the wall is slightly thicker and tapers at a draft angle of at least 0.5 degrees. Without draft, parts won’t eject cleanly from the mold and are susceptible to damage, so applying a draft angle to vertical walls and surfaces is critical.
What is the Significance of Wall Thickness in Product Design?
During product design, the significance of wall thickness is about reducing material usage while improving part quality and production speed.
- Reduced Raw Material: Optimal wall thickness can reduce the amount of plastic needed and the weight of the molded part — in many cases, thicker walls can be replaced with thinner ones.
- Part Quality: Designing injection molded parts with wall thickness problems can result in defects like sinkholes, warping, and short shots. These problems increase rejection rates and, ultimately, the total cost of your parts.
- Production Speed: Thicker walls take longer to cool than thinner walls, but adequate cooling is critical for injection molding success. Consequently, wall thickness affects cooling rates and, ultimately, injection molding cycle times.
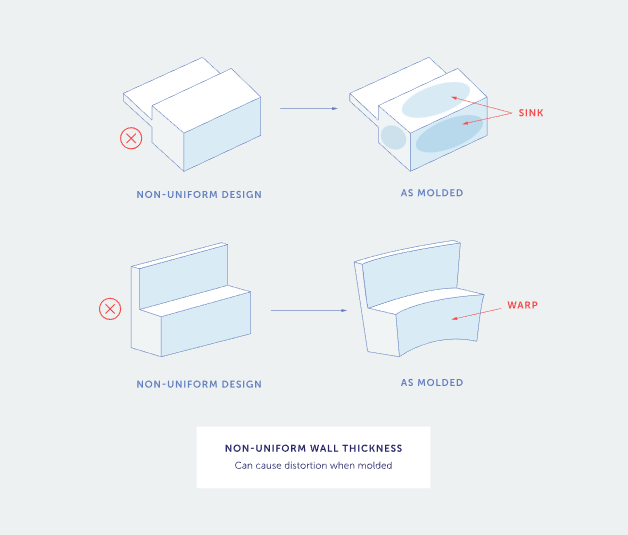
What is Uniform Wall Thickness?
Uniform wall thickness does not necessarily mean that every wall must have the same exact thickness. Some thickness variations are acceptable within limits. Generally, the thickness of a wall should be no less than 40% to 60% of adjacent walls because when thickness transitions aren’t gradual, part defects such as warping occur. Also, note that ribs and supporting walls do not need to be the same thickness as the main walls.
How to Design for Uniform Wall Thicknesses
Typically, injection molded parts are designed using CAD (Computer-Aided Design) software and those designs follow specific DFM (Design for Manufacturing) principles. Most modern CAD packages have a powerful set of tools with features that assist with the design of parts for injection molding. These features make it easy to modify wall thicknesses and to apply draft angles.
Selecting the Optimal Wall Thickness
For injection molding plastics, optimal wall thickness is given as a range of measurements in inches (in) and millimeters (mm). However, these numbers are a broad range — for best results, you need to work with a skilled injection molding manufacturer, like Fictiv, who can provide you with DFM feedback and insights gleaned from experience.
This table shows recommended wall thicknesses for some common injection molding materials.
Resin | Recommended Wall Thickness | |
in | mm | |
ABS | 0.045–0.140 | 1.14–3.56 |
Acetal | 0.030–0.120 | 0.76–3.05 |
Acrylic | 0.025–0.150 | 0.64–3.81 |
Liquid Crystal Polymer | 0.030–0.120 | 0.76–3.05 |
Long-Fiber Reinforced Plastics | 0.075–1.000 | 1.91–25.4 |
Nylon | 0.030–0.115 | 0.76–2.92 |
Polycarbonate | 0.040–0.150 | 1.02–3.81 |
Polyester | 0.025–0.125 | 0.64–3.18 |
Polyethylene | 0.030–0.200 | 0.76–5.08 |
Polyethylene Sulfide | 0.020–0.180 | 0.51–4.57 |
Polypropylene | 0.025–0.150 | 0.64–3.81 |
Polystyrene | 0.035–0.150 | 0.89–3.81 |
What is the Minimum Injection Molding Wall Thickness?
Minimum injection molding wall thickness refers to the thinnest wall recommended for a given type of plastic. There are several factors to consider when specifying this dimension. For example, it’s important to define the expected loads to which the part will be subjected — cosmetic parts are exposed to different loads than one used as a push-button. Some designers start by using the lowest possible wall thickness for the selected material, then perform a finite element analysis (FEA) using previously-defined load cases. The results of the FEA will provide a good indication of whether the thickness of the wall is sufficient. If the wall is too thin, you can adjust its thickness or select a different material. 1 mm is usually the thinnest that part walls get, although minimum wall thickness can be thinner for some materials.
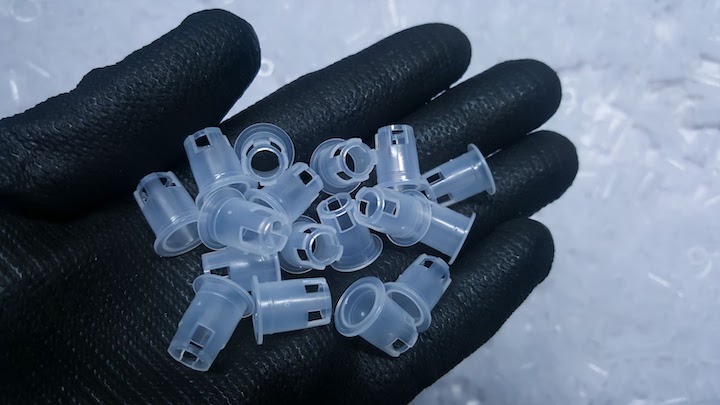
What is the Maximum Injection Molding Wall Thickness?
Maximum injection molding wall thickness refers to the thickest wall that is recommended for a specific type of plastic. There are several factors to consider when specifying this dimension. In general, excessively thick walls are not recommended because they often result in part defects. Sometimes, however, thicker walls are needed because of high loads exerted on the part, thermal insulation requirements, or simply to make the part feel heavier and more substantial.
Most injection moldable plastics have an upper limit which, if exceeded, can cause issues such as underfilling, warping, and excessive dimensional deviations. However, as a general rule, the maximum wall thickness should be limited to 5 mm. As with minimum wall thickness, the maximum wall thickness is a function of the plastic material being molded.
Choosing the Correct Wall Thickness for Injection Molding
Choosing the optimal wall thickness for an injection molded part can be a balancing act between part cost, strength, cycle times, and other factors. To effectively balance all of these requirements, it takes expert knowledge and real-world experience.
When you ask Fictiv for an injection molding quote, you’ll receive free DFM feedback. And, the report doesn’t merely indicate whether or not your part can be injection molded — you’ll receive recommendations about how to improve your design to accelerate production and be less expensive to mold. Getting started is easy, so, create your free Fictiv account today.