Time to read: 5 min
🎵 Mm-noom-ba-deh
Doom-boom-ba-beh
Doo-boo-boom-ba-beh-beh
Pressure! Pushin’ down on me,
Pressin’ down on you, no man ask for
Under pressure! That brings a building down 🎵
We’re back with an engineering fundamentals refresh about compressive stress (and an assist from Freddie Mercury and David Bowie).
It’s never too early to get acquainted, or too late to get reacquainted with important engineering concepts, and among the most important is the concept of stress — ensuring your designed parts aren’t exposed to too much stress is critical to have a successful design.
This article discusses types of compressive stress, provides a microscopic view of how compressive stress impacts materials, and has tips for how to make your designs more stress resistant.
Pro-Tip: For more engineering fundamentals refreshers, check out:
Strength vs. Stiffness vs. Hardness
Mechanical Creep (Deformation)
Ductility, Strain, and Toughness
What is Stress?
A Macroscopic View
Let’s first look at stress with respect to how it impacts a part overall. Stress is a result of a force acting on an object over the object’s surface area. The net force acting on an isolated internal surface of an object shows up as a force distribution across the object’s surface area. You can calculate it using this simple formula:
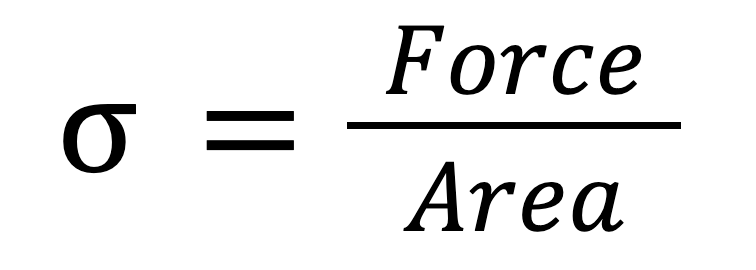
The direction of the stress matters too, with an important distinction:
- A stress acting inward into the surface is a compressive stress — which results in material compression or shortening — and is a negative quantity
- A stress acting outward from the surface is a tensile stress or normal stress — which results in material tension or elongation — and is a positive quantity
A stress can be split up into normal and tangential components, based on the angle at which the stress or the force acts upon the surface.
What is Normal Stress?
The portion of the stress vector acting normal (perpendicular) to the surface is normal stress. If normal stress acts downward on a surface, it is compressive stress — this is the stress you’re exerting on your chair or floor right now!
What is Tangential Stress?
The portion of the stress vector acting tangent (parallel) to the surface is tangential or tangential shear stress.
What are Stress Units?
Stress units are the applied force divided by the area the force is applied to:
- English Units: pounds per square inch or PSI
- SI Units: newtons per square meter or N/m2 or Pascal (Pa): 1 N/m2 = 1 Pa
Compressive Stress Equations
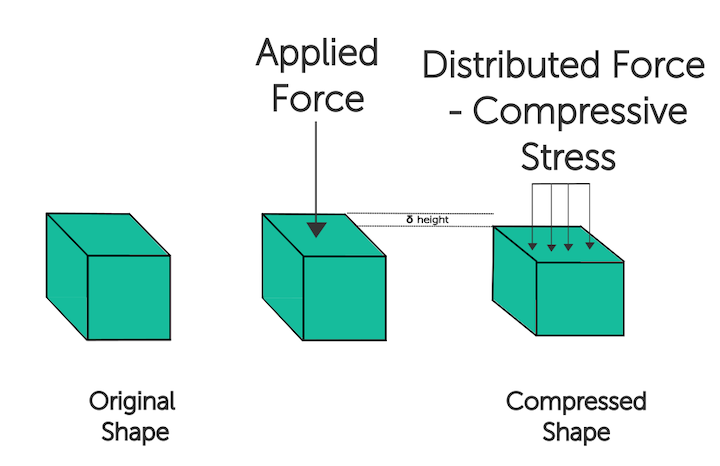
And as shown above, an applied force downward on the surface results in a distributed load, or compressive stress, that changes the height of the object (the dimension parallel to the force applied). This change in height is strain, so stress results in strain.
This relationship can be described by a material’s elastic modulus (E). In the case of compressive or tensile elasticity, the elastic modulus is known as Young’s Modulus and is a material property that measures its stiffness or ability to resist deforming when subjected to stress. It’s defined as:

Note: This relationship only exists for deformation resulting from applied stress below the material’s elastic limit or the linear range of a stress vs strain curve.
Therefore compressive stress can be defined as:

Compressive stress is dependent on the object’s geometry. The force applied to the object and the response to compressive stress is heavily dependent on Young’s Modulus or elastic modulus of a material (the ability of a material to resist deformation when subjected to stress). For example, consider what happens when a 292.50 KN (Kila-newton) weight is placed on the block illustrated below, which has a surface area of 0.5 m2. Now consider the difference between a block made of 316 stainless steel and one made of copper C101 shown in the table below
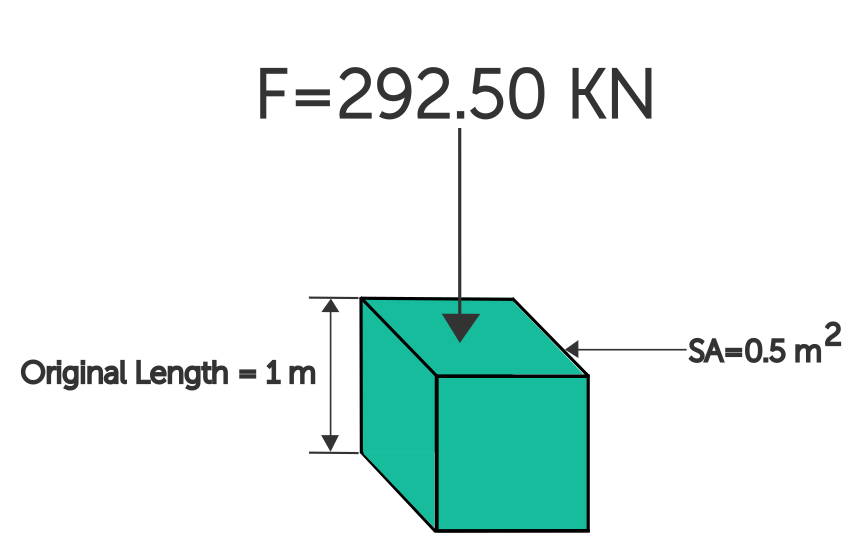
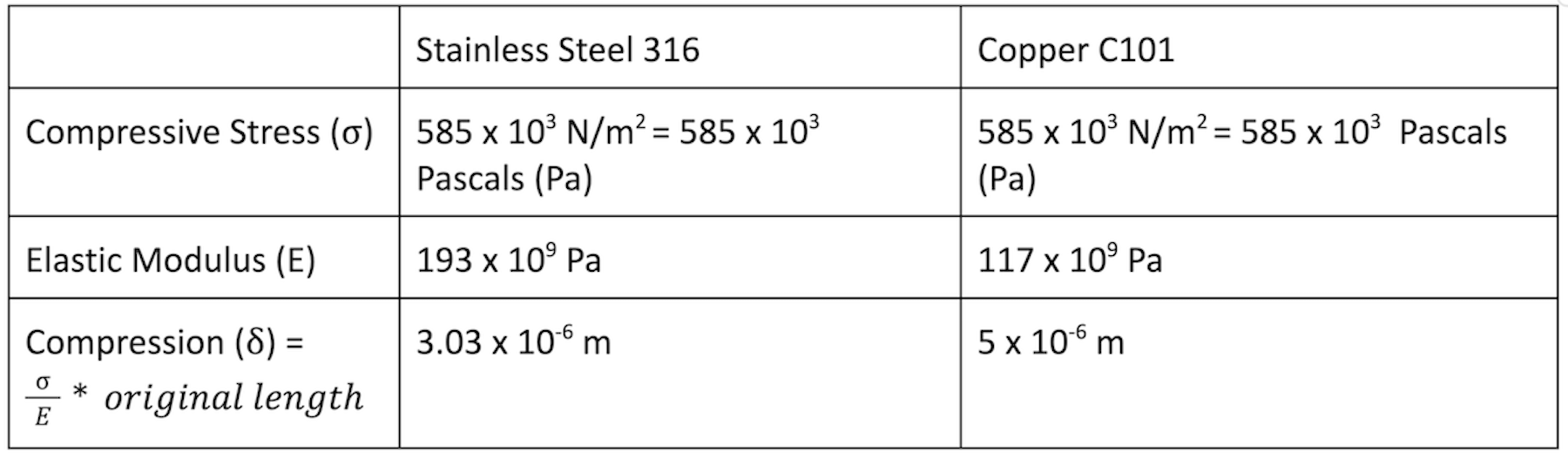
So, if geometry and loading conditions remain the same:

The Metallurgy of Stress: A Microscopic View
How an object responds or deflects due to an applied compressive force or compressive stress is dependent on the material’s elasticity. A material’s elasticity is a measure of its ability to return to its original shape after a load that caused deformation is removed, as long as the loading conditions produce stresses below the material’s elastic limit.
Elastic deformation occurs when a material returns to its original shape after being subjected to a force. An example of a material with a high elastic modulus is concrete. Concrete is utilized for construction because it can withstand high compressive loads without deforming significantly. Concrete is made of rigid molecules that have cracks all along their grain structures. So, when concrete is compressed, these voids are simply pressed together and eliminated — the material has a place to go. When concrete is subjected to tensile stress though, these voids become the location of high stress concentrations and cracks propagate.
Most polymers and rubbers have a high elasticity and are able to withstand higher stresses before deforming because their polymer chains are able to stretch when a force is applied. Metals are sometimes elastic because their crystalline structure allows for sliding, reshaping, or resizing of atoms when subjected to an applied force.
Pro-Tip: Stiffness in mechanical engineering is an indicator of the tendency for an element to return to its original form after being subjected to a force. If you’re looking for a simple way to calculate the stiffness of a cantilever beam, for example, check out our Area Moment of Inertia Calculator.
Design Tips for High Compressive Stress Applications
When your parts will be subjected to high compressive stress, consider the following:
- Since the reaction to stress is dependent on the surface area the stress is distributed across, consider increasing that surface area. Consider creative ways to increase the cross-sectional area through surface enhancement or etching.
- Choose a material with a higher elastic modulus, which will ensure your part will deflect less given the same geometry and loading conditions.
- Choose a material with a higher elastic limit to ensure the material can handle higher stress before permanent deformation occurs.
Fictiv – Your Custom Manufacturing Partner
If you’re working on something that needs to withstand compressive stress, you’ve come to the right place! Here at Fictiv, our manufacturing experts are accustomed to working with a variety of materials and can advise you on the right material for your application — especially parts destined for the most stressful conditions.
We offer CNC machining, 3D printing, injection molding, and urethane casting services, and with our free, instant DFM feedback and expert manufacturing guidance, you’ll get the high-quality parts you need, fast.
Create an account and upload your design today!