Time to read: 8 min
How do you mold metal inside of metal? High-pressure die casting (HPDC) can do this very efficiently and is widely used for the production of complex, high-precision metal components in high volume. The process is known for its rapid cycle times and ability to produce intricate shapes with excellent dimensional accuracy.
This manufacturing process is particularly well-suited for non-ferrous metals, with aluminum and zinc alloys being the most commonly used materials. Similarly to injection molding, its ability to deliver consistent results makes it especially valuable in applications where precision and surface quality are critical.
This article will review the high-pressure die casting process, discussing its applications, material considerations, advantages, and disadvantages as a manufacturing technique.
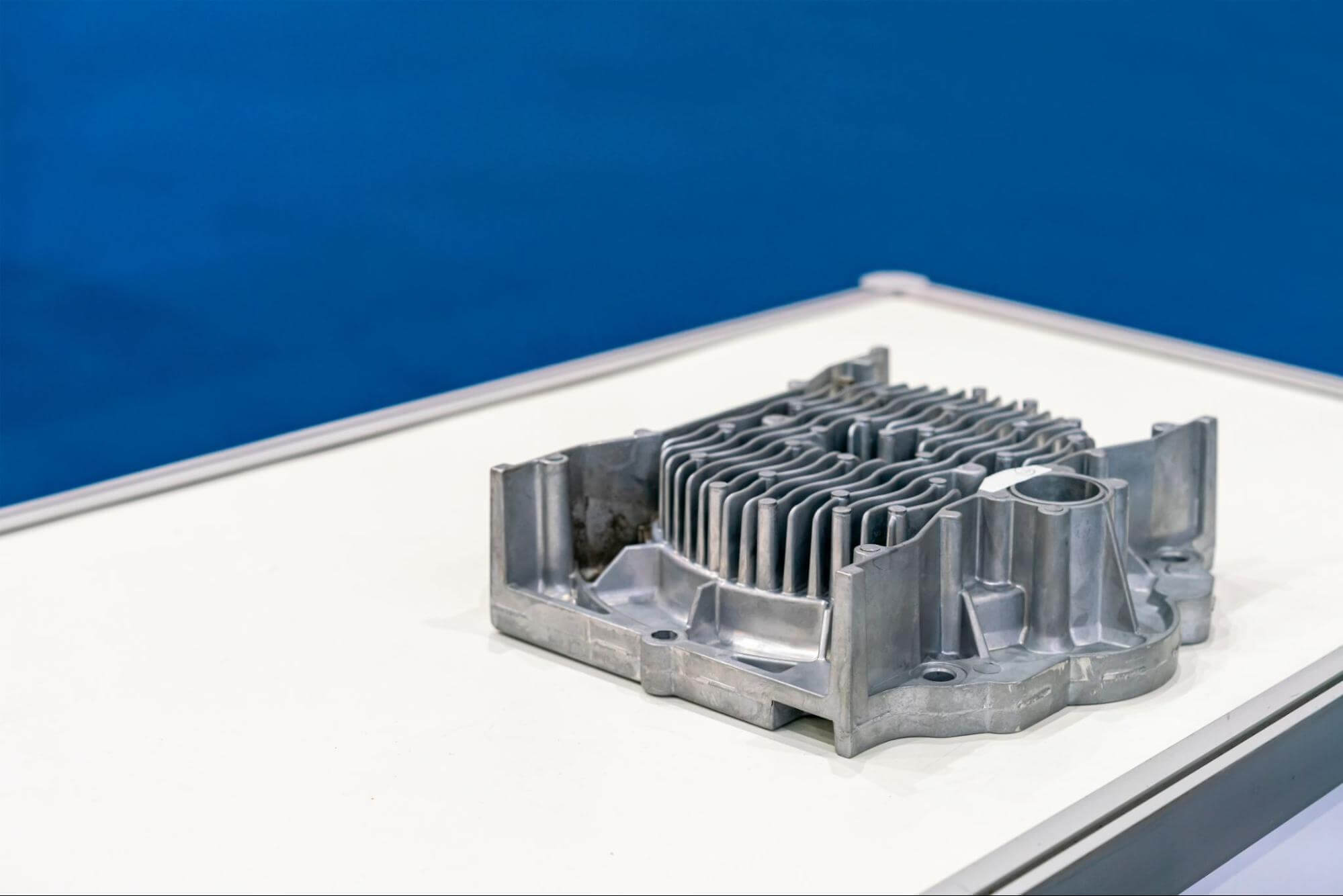
High-pressure die-cast part
What Is High-Pressure Die Casting and How Does it Work?
High-pressure die casting (HPDC) is essentially the equivalent of injection molding for metal manufacturing. It’s a manufacturing process in which molten metal is injected into a steel mold cavity at very high pressure (typically between 10,000 and 20,000 psi). This forceful injection enables the molten metal to quickly fill intricate mold features and solidify into precise, high-quality components. Hardened steel molds allow repeated use, making HPDC an ideal choice for mass production of complex parts with excellent surface finishes and dimensional accuracy.
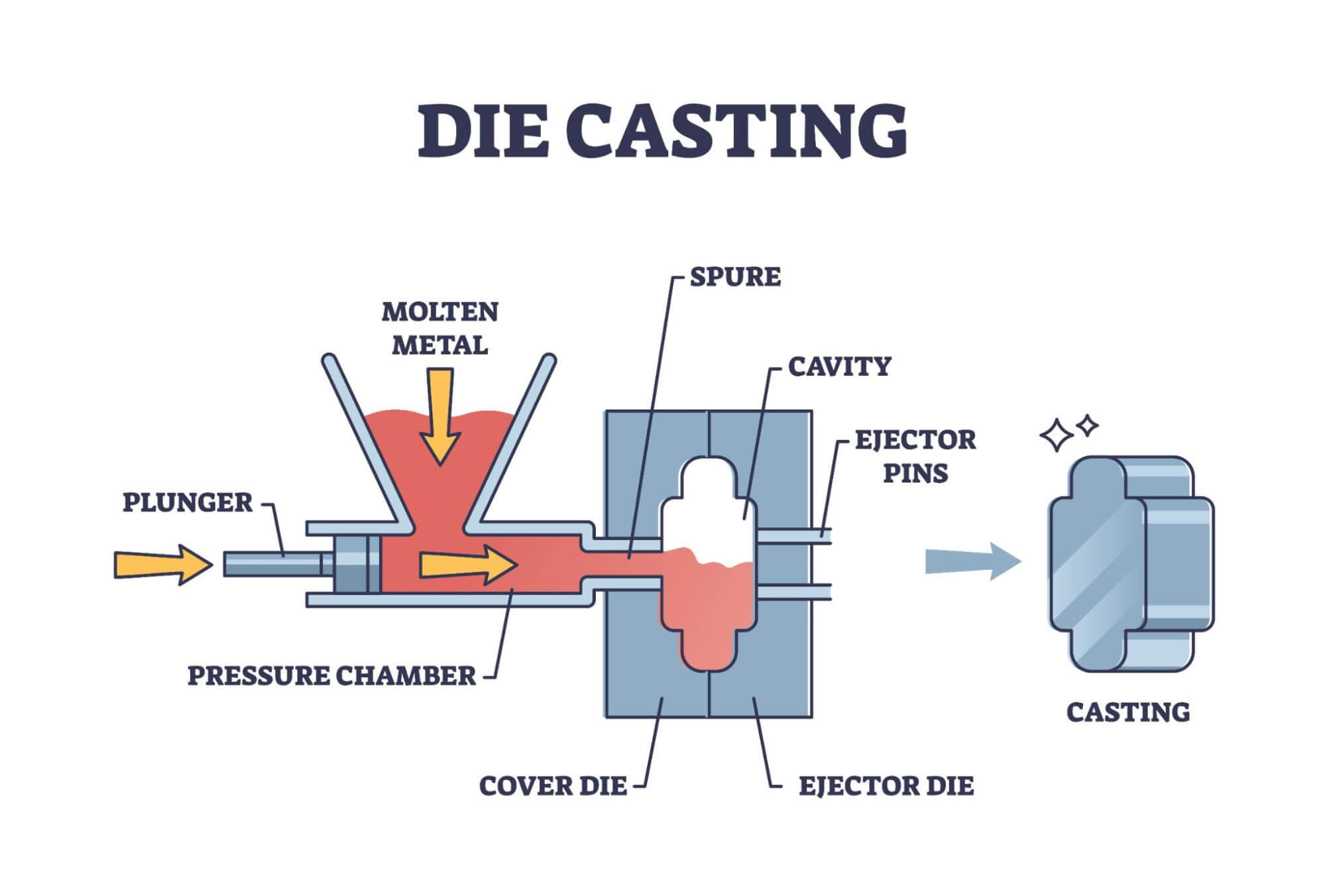
HPDC stands out for its fast cycle times and its ability to produce thin-walled, detailed parts that can hold tight dimensional tolerances. It offers better consistency and speed compared to other casting processes, which is critical for quality product development at scale. The part cost is lower at high volumes due to the cycle time, but the mold itself is typically more expensive.
High-Pressure Die Casting vs. Other Common Die-Casting Methods
Method | Pressure | Mold Type | Production Volume | Cycle Time | Consistency |
High-Pressure Die casting | 10,000-20,000 psi | Hardened steel dies (high-strength tool steel) | High | Fast (seconds) | High (excellent repeatability and tight tolerances) |
Low-Pressure Die Casting | <100 psi | Steel or cast iron dies (permanent mold) | Medium | Moderate (1-3 minutes) | Moderate to High (less precise than HPDC, but good repeatability) |
Gravity Die Casting | Atmospheric | Steel or cast iron dies (permanent mold) | Low to medium | Slower (2-5+ minutes) | Moderate (variable, depends on operator skill and cooling control) |
The High-Pressure Die Casting Process: Step by Step
The high-pressure die-casting process comprises multiple steps, yielding high-quality, repeatable products. The steps in high-pressure die casting are explained below:
1. Molten Metal Preparation
Metal ingots (commonly aluminum or zinc) are heated in a furnace until they reach the ideal casting temperature. Maintaining this temperature is crucial to achieving optimal fluidity and avoiding casting defects.
2. High-Pressure Injection
Once the metal is at the casting temperature, it is injected into a steel mold cavity at extremely high pressure, typically between 10,000 and 20,000 psi. The high injection pressure pushes the molten metal into the closed dies in a matter of milliseconds. The high-speed mold fill, in conjunction with proper gating and vent design, minimizes the likelihood of air entrapment in the solidified casting and ensures that the molten metal completely fills intricate mold details.
3. Solidification and Cooling
As molten metal enters the mold cavity, the first liquid to enter solidifies when it contacts the cold mold walls. As more liquid metal follows to completely fill the mold, heat continues to be conducted away by the mold surfaces. The entire casting solidifies rapidly, allowing premium surface finishes and tight dimensional tolerances.
4. Part Ejection
After solidification, the mold opens and the part is ejected using mechanical ejector pins mounted on a steel plate that is electrically or hydraulically actuated. These pins help release the component without damaging the delicate surfaces or compromising dimensional integrity.
5. Trimming and Finishing
Once the part is removed from the mold, any excess material or flash formed at the mold’s parting line is trimmed off. Depending on the application, additional finishing processes, such as machining, coating, or surface texturing, may be performed to meet specific quality or aesthetic requirements.
Materials Used in High-Pressure Die Casting
Multiple non-ferrous metals are suitable for HPDC. Aluminum and zinc are the most commonly used metals, due to their mechanical properties and casting characteristics.
The materials commonly used in high-pressure die casting are discussed below:
Aluminum Alloys
Aluminum alloys are prized for their light weight, strength, and corrosion resistance. These characteristics make them ideal for applications in automotive, aerospace, and consumer goods. Alloys such as A360 and A380 are frequently chosen for their balance of castability and performance.
Zinc Alloys
Zinc alloys offer exceptional fluidity, allowing them to fill even the most intricate molds with ease. Their high dimensional stability and strength at room temperature make them a popular choice for small, precise components in electronics and consumer products. Additionally, zinc supports high-speed production and longer tooling life when compared to aluminum alloy HPDC due to its relatively low melting point.
Magnesium Alloys
Magnesium is valued for its high strength-to-weight ratio and is often utilized in aerospace and portable electronics where weight reduction is critical.
Copper-Based Alloys
Copper-based alloys like brass, though less common, provide high strength and excellent thermal and electrical conductivity, which are beneficial for certain specialized HPDC applications, such as electrical switch gears, breakers, electrode plates, and more. Copper-based alloys are also biocompatible, which allows them to be used for medical applications.
Advantages of High-Pressure Die Casting
High Production Speed and Efficiency
The rapid turnaround of HPDC processes significantly reduces labor and per-part costs, especially when compared to other manufacturing methods such as CNC machining or sand casting. This is because HPDC is a largely automated process that can produce large amounts of parts while requiring little human intervention. While machining may require several steps to achieve a finished part, HDPC parts are largely complete right out of the mold.
Excellent Surface Finish and Dimensional Accuracy
HPDC produces parts with smooth surfaces and tight tolerances directly from the mold, often eliminating the need for secondary operations such as grinding or polishing. This is particularly beneficial for applications that require aesthetically pleasing cosmetic quality or for components that must fit together. Because the mold cavities are machined from hardened steel, they retain fine details well over time, ensuring repeatable quality.
Ability to Form Complex Geometries
The high pressure used during the injection phase allows molten metal to flow into intricate features and thin sections of the mold that would be difficult or impossible to fill using other casting methods. This makes HPDC especially valuable for lightweight structural components with complex internal features, such as ribbing, bosses, or undercuts. As a result, engineers can design parts with more innovative shapes without compromising manufacturability or structural integrity.
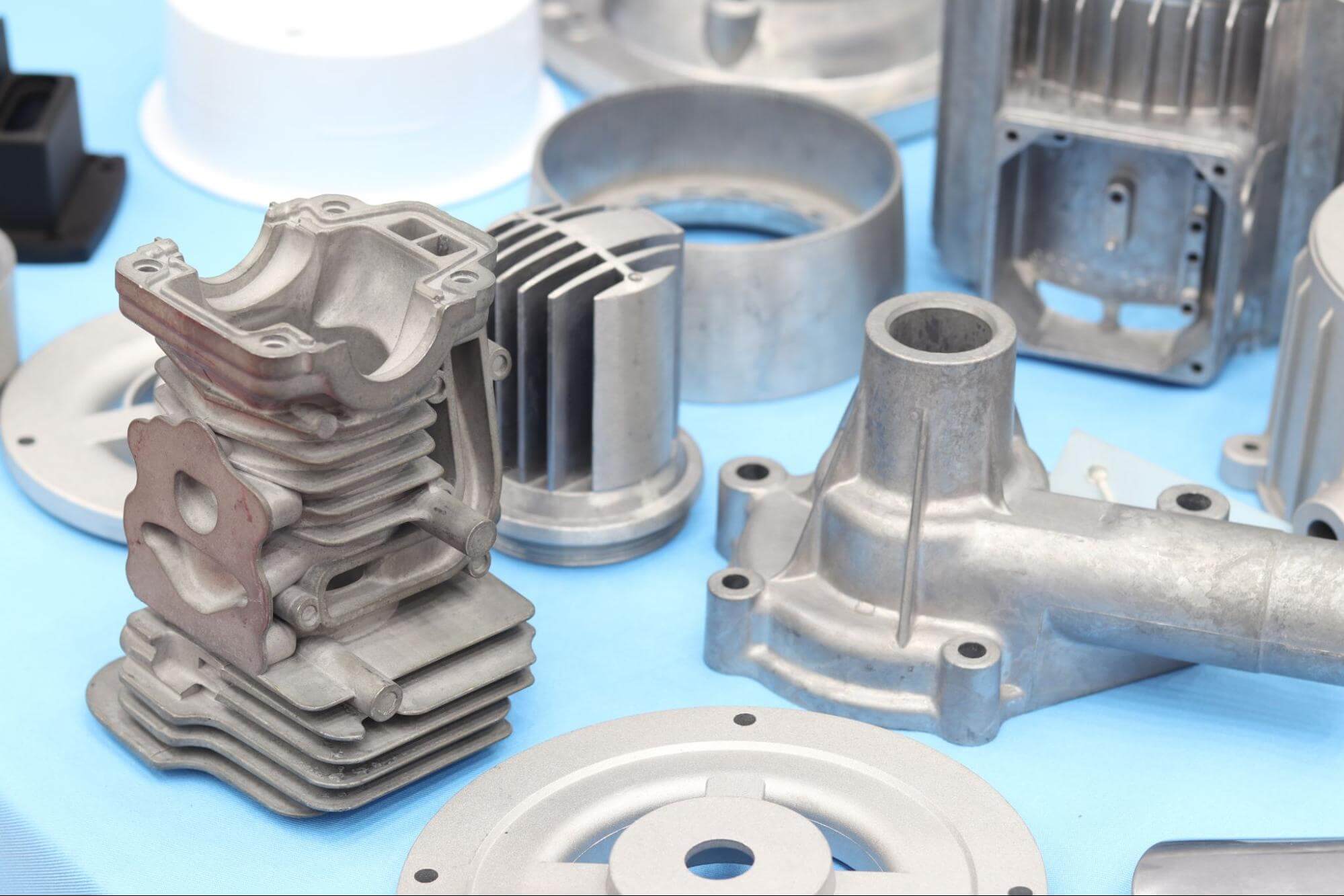
Disadvantages of High-Pressure Die Casting
High Initial Tooling Costs
A significant downside to HPDC is the substantial investment required for tooling compared to CNC tooling or investment casting tooling. The design and fabrication of steel molds involve machining and heat treatment, both of which are expensive and time-intensive. This upfront cost is only justifiable when amortized over large production runs, making HPDC less suitable for small-batch or prototyping applications. However, once the mold is in place, the cost per part drops considerably with production volume.
Potential Porosity Issues
Despite the many advantages of the process, HPDC parts are susceptible to porosity—tiny voids or pockets of trapped air or gas within the cast part or at its surface. These can be caused by turbulent flow of the molten metal during injection, or by improper venting in the mold. Porosity may compromise the mechanical strength of a part or interfere with secondary operations, such as machining or welding.
Careful mold design and correct selection of process parameters can minimize this risk. Sometimes, it may be necessary to add a vacuum assist to evacuate gas from the mold before it can be trapped. For other applications, post-casting impregnation treatments can reduce the occurrence of harmful porosity in die-cast products.
Limited to Non-Ferrous Metals
HPDC is generally restricted to casting non-ferrous metals such as aluminum, zinc, and magnesium and their alloys. This is because these materials have relatively low melting points compared to steel, the metal typically used for die casting tooling.
Ferrous metals (iron and steel) cannot be used in HPDC because of their lower flowability and higher melting temperatures near that of the tooling. Casting steel would rapidly damage or degrade the molds as a result. Therefore, HPDC is not a viable solution for parts requiring the strength and heat resistance of ferrous alloys, which must be manufactured using other methods, such as investment casting.
Applications of High-Pressure Die Casting
The repeatability of high-pressure die casting has made it indispensable for mass production across various industries, such as:
Automotive
In the automotive sector, aluminum alloy and zinc HPDC are widely used to produce engine blocks, transmission housings, and mounting brackets. These components benefit from HPDC’s ability to create lightweight yet structurally sound parts, which help enhance fuel efficiency and vehicle rideability.
Aerospace
In the aerospace industry, HPDC is used to produce lightweight structural components where the strength-to-weight ratio is a paramount consideration.
Electronics and Consumer Goods
Electronics and consumer goods also utilize HPDC for items such as laptop and smartphone housings, as well as heat sinks used in thermal management. These parts require fine details, good surface finishes, and high-volume production, all of which HPDC delivers proficiently.
Medical Equipment
Medical equipment manufacturers rely on high-pressure die casting for components that require both biocompatibility and precise dimensions. Surgical tools, diagnostic device enclosures, and other medical parts benefit from the dimensional accuracy and repeatability that the process offers.
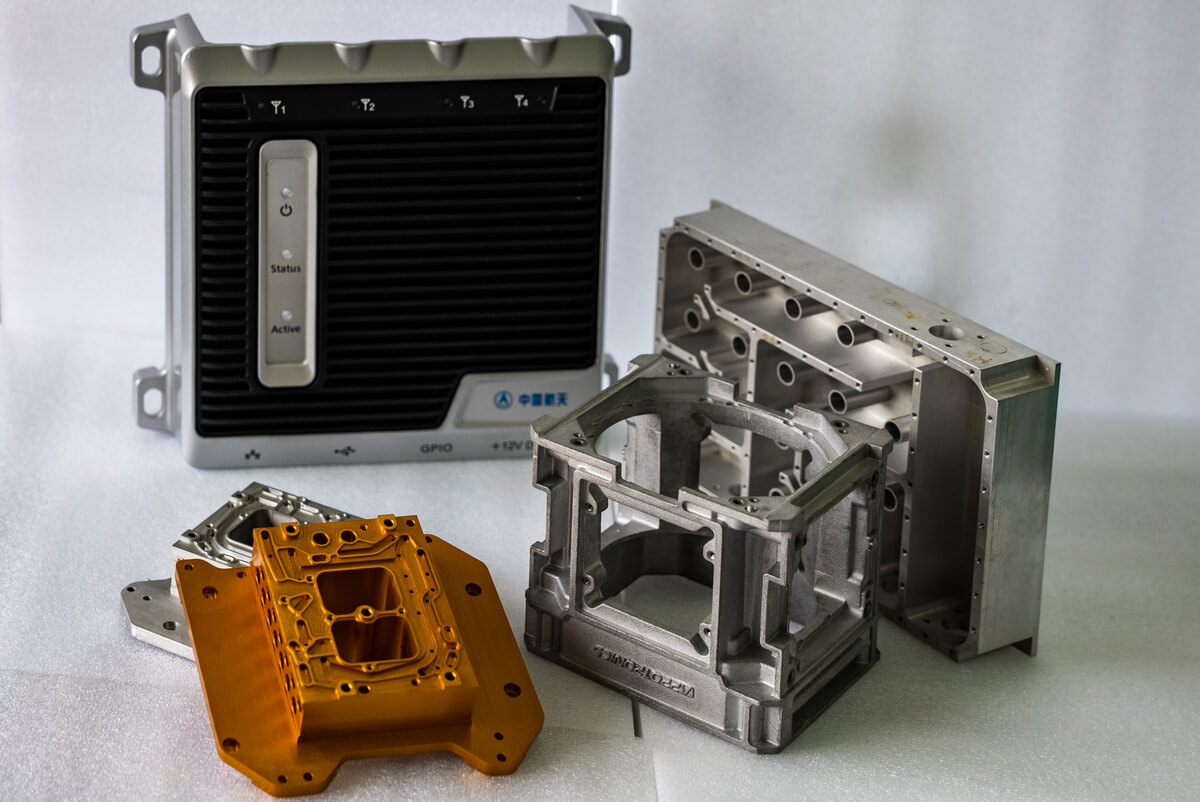
Die casting is used for consumer electronics housings and other applications.
High-Pressure Die Casting Tooling and Mold Considerations
When fabricating high-pressure die cast tools, tooling manufacturers must consider several factors to ensure equipment longevity and high-quality products, including:
Mold Material
The quality and efficiency of high-pressure die casting are directly influenced by the design and construction of the molds used in the process. These molds must endure repeated exposure to molten metal at temperatures of around 700°C and withstand injection pressures up to 140 MPa for thousands, or even hundreds of thousands, of production cycles.
To meet these demands, high-pressure die-cast molds are typically fabricated from hardened tool steels such as H13. The steel’s hardness, wear resistance, and low thermal conductivity are critical in extending mold life and ensuring consistent part quality. Together, these properties enable the mold to endure continuous abrasion and thermal stress throughout the casting process.
Cost Considerations
While the initial investment in mold design and fabrication can be substantial due to intricate designs and complex manufacturing methods like wire EDM, this cost is amortized over large production volumes. Other cost items to consider include raw material costs, furnace design, and finishing processes, among others. Each of these items must be levied effectively to balance initial cost with return.
Maintenance and Lifespan
To ensure long-term performance and reduce unplanned downtime, die casting molds require regular maintenance. This includes cleaning, lubrication, and periodic inspection for wear or thermal fatigue. Implementing preventive maintenance routines can significantly extend the life of the mold, maximize productivity, and ensure consistent part quality across multiple production runs.
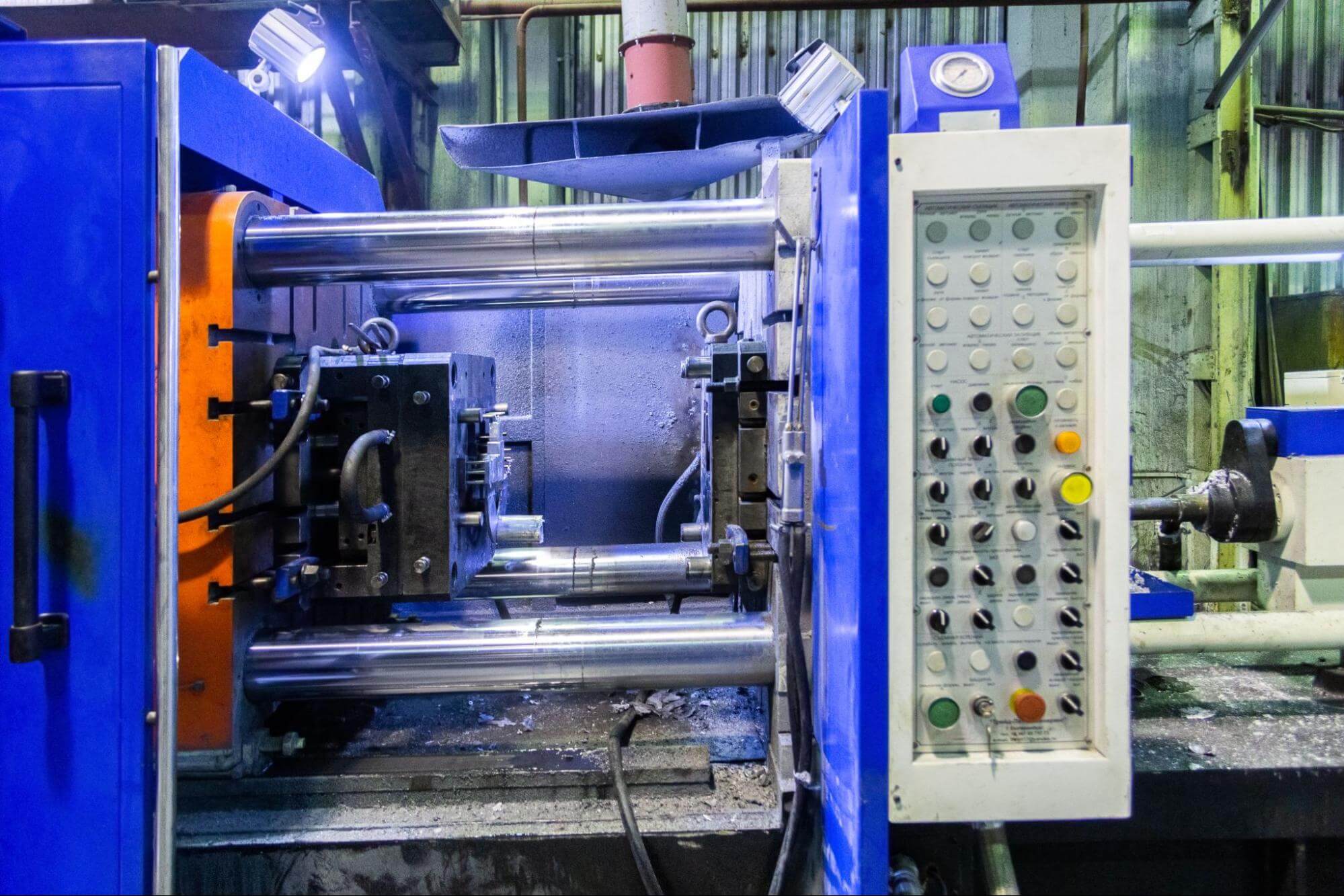
Future Trends and Innovations in High-Pressure Die Casting
High-pressure die casting is evolving rapidly with the integration of AI and automation, which help optimize process parameters, reduce defect occurrence, and boost production efficiency. Smart sensors and real-time monitoring enable predictive maintenance and greater control over quality.
Advances in material science are also expanding the capabilities of HPDC. New aluminum and magnesium alloys offer improved strength, corrosion resistance, and reduced weight, making them ideal for industries such as automotive, aerospace, and medical devices.
On the sustainability front, HPDC is becoming more eco-friendly. Many operations now recycle scrap metal in closed-loop systems and use cleaner lubricants to reduce waste and energy consumption. As demand grows for greener and more efficient manufacturing, HPDC continues to adapt, positioning itself as a key technology for the future.
Why High-Pressure Die Casting Is Key to Mass Production, High-Precision Manufacturing
High-pressure die casting remains a cornerstone of modern manufacturing that enables unmatched speed, precision, and repeatability. With broad applications from automotive components to medical devices, HPDC continues to evolve with smart technologies and more sustainable practices. For companies seeking cost-effective production and high precision, HPDC is a proven pathway to success.
Looking to streamline your production process with top-tier casting capabilities? Explore Fictiv’s high-pressure die-casting services and get a quote today for rapid, high-quality parts delivered at scale. Visit Fictiv’s Platform to start your project with expert support and advanced manufacturing tools.