Time to read: 4 min
Forging is a basic cycle in metalworking that permits manufacturers to shape and change unrefined substances into accurately designed parts. Hot forging and cold forging are the two basic methods, and each offers unmistakable benefits and is fit for specific applications.
This article discusses hot and cold forging, their disparities, applications, and a rubric for choosing the right method for your application. By understanding these fundamental processes, makers and architects can make informed material choices that will enhance the quality of their work.
Hot Forging vs. Cold Forging Overview
Forging is a method used to shape and frame metal parts that includes applying mechanical force to a workpiece to disfigure it plastically and change its shape and properties. As a rule of thumb, metals with a higher formability ratio are more suited for hot forging.
Hot Forging
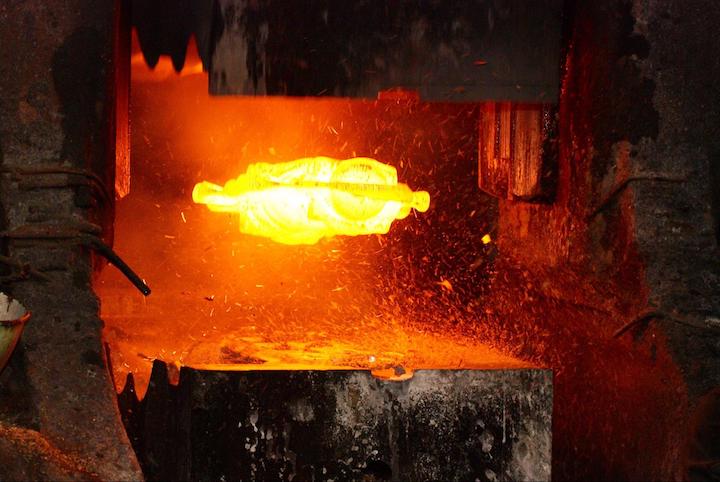
Hot Forging Definition
Hot forging, or hot working, includes shaping metal at raised temperatures, usually between 700°C and 1,200°C. The metal is heated to provide flexibility and make it more bendable.
Hot Forging Process
- Heating: The metal workpiece is heated in a furnace until it is malleable — the temperature differs depending on the material.
- Deformation: The heated material is then positioned in a die or mold, and a compressive force is applied via a press or sledge that deforms the material into the desired shape.
- Cooling: After the forging process, the workpiece is cooled — frequently in controlled conditions — to prevent issues related to cooling the material too quickly.
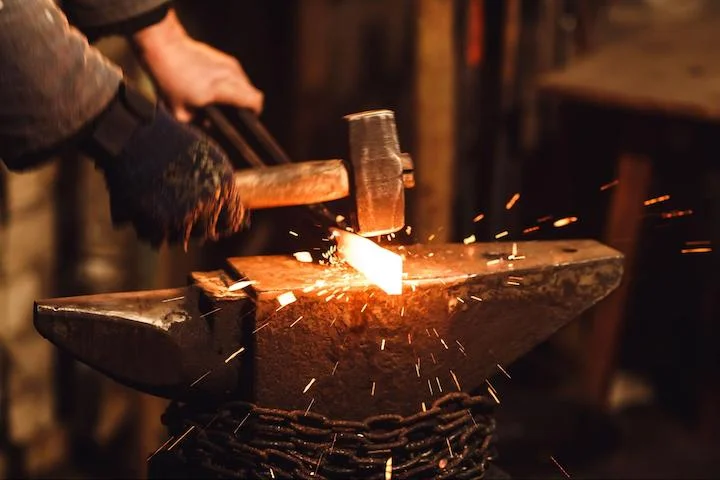
Hot Forging Advantages and Applications
- Improved Ductility: High temperatures make materials more malleable, so it is simpler to shape complex parts.
- Reduced Work Hardening: Elevated temperatures limit the probability of work solidifying, which can happen in cold forging.
- Enhanced Microstructure: Grain structure refinement and further developed mechanical properties result from recrystallization during hot forging.
The following are some common uses for hot forged parts:
- Aviation: Motor and landing gear components
- Automotive: Associating poles, driving rods, and gears
- Heavy Machinery: Shafts, pinion wheels, and parts for modern apparatus
Cold Forging
Cold Forging Definition
Cold forging, or cold working, involves molding metal at or close to room temperature. Through this process, the material holds its unique glass-like structure, which results in expanded hardness and rigidity. The process is not like hot fashioning because the metal isn’t warmed, instead it’s worked in its room-temperature state, below its recrystallization state.
Cold Forging Process
- Lubricant Treatment: parts may be treated with lubricant before forging so they don’t adhere to the die.
- Deformation: The workpiece is put in a die, and a compressive force is applied, squeezing it into a secondary die at a temperature below the austenite phase (these parts are sometimes called a press and die). The absence of heat requires higher forces. The compressive force may be hydraulic, pneumatic, or mechanical.
- Finishing: Cold-forged parts frequently require extra machining or finishing to achieve desired aesthetics. Sometimes, there is flash that remains from excess material spilling over the die during forging. This material must be trimmed away.
Cold Forging Advantages and Applications
- Higher Precision: You can achieve tighter tolerances with higher precision using cold forging.
- Improved Surface Finish: The shortfall of scale or oxidation frequently produces a smoother surface than hot forging.
- Material Savings: Cold forging requires less material volume which consequently also reduces built-up stress and excess material flash.
The following are some common uses for cold forged parts:
- Hardware: Nuts, fasteners, screws, and different clasps.
- Automotive: Heading, pinion wheels, and transmission parts.
- Parts with Fine Details: alternators, gears, starter motor components, flywheels.
When to Use Hot and Cold Forging
- Material Selection: Materials can be more suited for hot or cold forging. For example, aluminum and magnesium are usually cold-forged, while steel is frequently hot-fashioned.
- Intricacy of Design: Hot forging generally works better for complex shapes because of the expanded malleability of hot materials. Cold forging is more reasonable for easier shapes with tight tolerances.
- Production Volume: High-volume production frequently uses cold fashioning because of its effectiveness and negligible material waste.
- Cost Contemplations: Cold forging might have higher beginning tooling costs; however can prompt reserve funds in material use. In addition, cold forging doesn’t require heat so it costs less over time.
- Material Properties: Think about the ideal mechanical properties of the end result. Hot forging might be important to accomplish explicit grain designs and properties.
Both hot and cold forging are critical to the metalworking business. The decision between them relies upon variables like material, intricacy of the part, production volume, and desired properties. Understanding the subtleties of each method are key to choosing what’s best for your particular applications, so you get superior-grade, accurate parts.
While hot and cold forging are critical to manufacturing, many designs are too complex and require higher precision than are achievable with forging. CNC machining can achieve incredible precision, and the skilled machinists at Fictiv can machine even the most complex geometries out of a variety of materials. Plus, our manufacturing experts can help with material selection and refine your designs through detailed DFM feedback — so you get great results, fast!

Sign up for a free account and see how beneficial our manufacturing services and expert guidance can be for you!