Time to read: 7 min
While many engineers and product designers are well-versed in traditional injection molding and silicone compression molding, liquid silicone rubber (LSR) injection molding is a specialized technique that’s often overlooked, despite offering significant advantages.
LSR molding enables the production of complex, flexible parts with consistent wall thickness, excellent biocompatibility, and the ability to overmold onto other substrates. Though the process is more complex—requiring precise temperature control, specialized equipment, and careful attention to flash—it opens the door to high-performance components that meet stringent durability and aesthetic requirements in medical, automotive, and consumer applications.

Diagram of LSR Injection Molding. Image credit: PRM-Taiwan
What Is Liquid Silicone Rubber (LSR)?
LSR is a two-part thermoset elastomer known for its excellent performance in demanding environments. It is a versatile and biocompatible material made up of two liquid components: the base and the catalyst.
These are mixed in a precise 1:1 ratio just before processing. Once combined, a chemical reaction begins that causes the material to cross-link, or cure, especially when exposed to heat. This reaction transforms the liquid mixture into a solid, ready for high-performance use.
Unlike thermoplastics, which melt and solidify through physical changes (temperature and pressure), LSR undergoes a permanent chemical transformation during curing, creating strong, stable molecular bonds. The result is a rubber-like material that offers excellent flexibility and resilience even under extreme conditions.
The composition of LSR is as follows:
- Component A: Contains a platinum-based catalyst.
- Component B: Contains a cross-linker (commonly methyl hydrogen siloxane) + an alcohol inhibitor.
- The base polymer consists of long polysiloxane chains that can be reinforced with treated silica.
LSR requires cool storage and mixing to maintain stability before processing. Once prepared, it is injected into heated mold cavities, where it cures rapidly through a vulcanization process that permanently sets the material.
LSR is ideal for many demanding applications due to its unique combination of properties:
- Highly flexible and elastic, staying soft and rubbery even in extreme temperatures, and it bounces back well after stretching or compression
- Stands up to water, acids, alkalis, and many solvents, remaining stable even when exposed to UV light, ozone, or other harsh conditions
- Maintains its strength and shape over time across a wide thermal range, typically from -50 °C to +250 °C
- Non-toxic, hypoallergenic, and safe for direct skin contact and medical use
- Incredibly durable
- Resists fatigue and weathering with ease
LSR vs. Traditional Silicone vs. TPE
Property | LSR (Liquid Silicone Rubber) | Traditional Silicone (HCR: High Consistency Rubber) | TPE (Thermoplastic Elastomer) |
Form | Liquid, flows easily | Solid, gum-like | Thermoplastic pellets |
Processing | Injection molding, fast cycle | Compression or transfer molding | Injection molding |
Curing | Thermoset (heat-activated) | Thermoset (heat and pressure) | Thermoplastic (no curing) |
Heat Resistance | Excellent | Excellent | Moderate |
Chemical Resistance | High | High | Moderate |
Elastic Recovery | Very High | High | Moderate |
Biocompatibility | Excellent | Excellent | Variable |
Recyclability | Limited recyclability | Limited recyclability | Recyclable |
Table 1: Comparison Table Between LSR, Traditional Silicone, & TPE
The LSR Injection Molding Process
The LSR injection molding process starts with precise metering and thorough mixing of components. The homogenized mixture is then injected under high pressure into a closed, heated mold, where it cures rapidly due to LSR’s thermosetting nature—enabling faster cycle times than thermoplastics. After curing, the part is ejected; in some cases, post-curing is performed to enhance mechanical strength or chemical resistance for critical applications like medical or food-grade parts.
This process depends on specialized equipment and automation to ensure quality and efficiency. Metering pumps deliver accurate proportions, static mixers create a uniform blend, and cold-runner molds keep the injected material cool until inside the mold. Automated demolding systems further optimize cycle times and reduce labor costs, making it ideal for high-volume production.
LSR Molding vs. Thermoplastic Injection Molding
Aspect | LSR Injection Molding | Thermoplastic Injection Molding |
Material Behavior | Thermosetting (cures with heat) | Thermoplastic (melts and cools) |
Mold Temperature | Heated mold | Cooled mold |
Material State | Liquid | Solid pellets |
Shrinkage | Lower shrinkage | Higher shrinkage |
Demolding | Often automated, draft angles recommended but not as necessary | Typically requires draft angles |
Reprocessing | Not reprocessable | Can be reprocessed |
Table 2: LSR vs. Thermoplastic Injection Molding
Advantages of LSR Injection Molding
Exceptional Durability & Repeatability
LSR parts maintain consistent mechanical properties over time, ensuring high reliability and minimal variation across large production runs.
Performance in Harsh Environments
LSR withstands extreme temperatures (typically -50 °C to +250 °C), resists UV and ozone exposure, and offers excellent chemical and moisture resistance, making it ideal for demanding applications.
Biocompatibility
LSR is inherently nontoxic and hypoallergenic, meeting strict regulatory standards for use in the food industry, medical devices, implants, and baby care products.
Complex Design Capability
The flow characteristics of LSR allow for the molding of intricate, thin-walled, and microscale features with high dimensional precision, reducing the need for secondary processing.
Efficient Production
The fully automated injection molding process supports rapid cycle times, minimal material waste, and scalability for high-volume manufacturing, reducing overall production costs.
Design Considerations for LSR Molding
LSR’s unique material properties require specific design considerations to ensure optimal performance, manufacturability, and cost efficiency. Table 3 below outlines key guidelines and considerations for designing parts:
Category | Consideration | Details |
Key Design Guidelines | Uniform Wall Thickness | Ensures consistent curing and reduces internal stresses |
Avoid Sharp Corners | Promotes material flow and minimizes stress concentrations | |
Undercuts & Gating Strategies | Minimize or design around undercuts; strategically place gates for optimal flow and fill | |
Shrinkage and Tolerance Planning | Material Shrinkage | LSR typically shrinks 2–3% post-molding |
Tolerance Design | Design for tight tolerances using tool compensation | |
Surface Finish and Texturing | Mold Texture Replication | Excellent at capturing fine details, suitable for matte or gloss finishes |
Potential Disadvantage | Flash Formation | Increased flash due to LSR’s low viscosity; trimming may be required post-molding, although removal is generally easier than thermosets |
Table 3: Design Considerations for LSR Injection Molding
Tolerances and Quality Control in LSR Molding
Here’s a concise breakdown of the key points related to tolerances and quality control in LSR molding:
Consistent Material Mixing and Molding Conditions
Consistent material mixing and precise molding conditions are crucial for ensuring the quality of parts. LSR comes as a two-part system that must be mixed in a strict 1:1 ratio—any inconsistencies in mixing can lead to curing issues, tacky surfaces, poor mechanical strength, or even part failure. Also, molding conditions such as temperature, pressure, and cure time must be carefully controlled. Any variation in these factors can negatively impact the final product’s dimensional stability, surface finish, and overall physical properties.
Common Tolerances for LSR Parts
Typically range from ±0.1 mm to ±0.2 mm for standard applications. Several factors influence these tolerances, including the part geometry, the precision of the tooling used, material shrinkage during curing, the balance of the mold cavities, and proper venting. These variables must be carefully managed to ensure the desired level of accuracy and consistency in the final parts.
Inspection Techniques for Soft, Flexible Materials
Inspecting soft, flexible materials like LSR requires specialized techniques to ensure part quality and performance. Visual inspection is commonly used to detect surface imperfections such as flashing, voids, short shots, flow lines, and discoloration, quickly assessing the part’s external condition.
For more precise measurements, non-contact methods such as laser scanners, vision systems, or optical comparators are employed to assess the part’s dimensions. In some cases, custom fixtures or 3D-printed jigs are used to secure parts during measurement, ensuring accuracy and consistency.
Functional testing is essential to evaluate the mechanical properties and performance of LSR parts. Compression, tensile, or elongation tests help assess material strength, while leak or pressure testing is used for sealing components. For parts with complex geometries or internal defects, advanced techniques like X-ray or CT scanning can provide in-depth analysis to ensure integrity throughout the entire component.
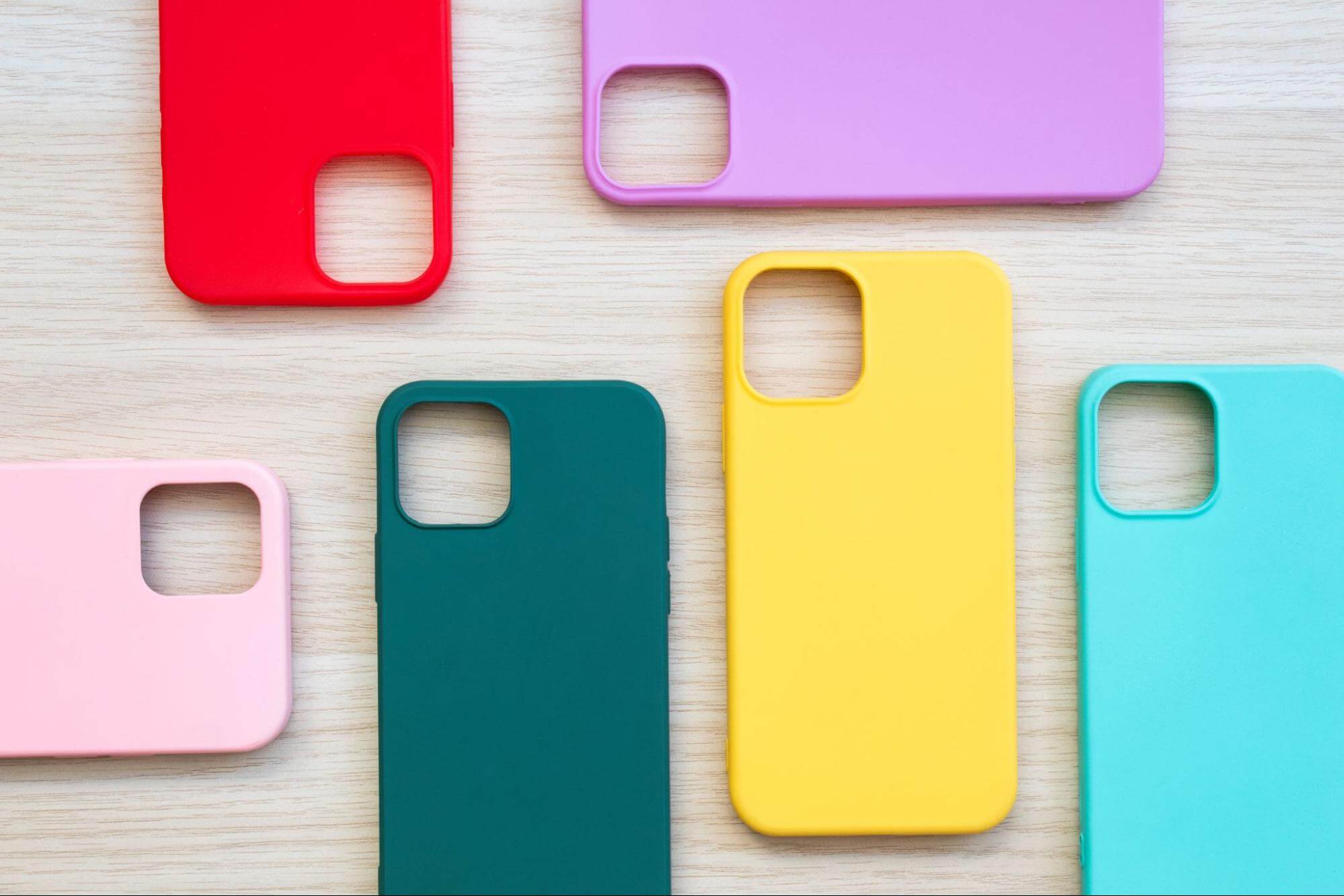
LSR Applications and Industries
LSR is used across a wide range of industries due to its unique combination of characteristics, including:
Medical Industry
LSR is highly valued in the medical field due to its biocompatibility, chemical resistance, and flexibility. It complies with stringent FDA and ISO standards. Key applications include seals and gaskets (ensure fluid or airtight barriers, especially in surgical tools and diagnostic equipment), valves (respiratory and infusion devices), and wearable health devices (bands and sensor housings).
Automotive Industry
In the automotive sector, LSR’s thermal stability, weather resistance, and durability make it ideal for safety-critical parts and components exposed to prolonged heat. Some applications include o-rings (sealing for engines and transmissions), connectors for electrical systems, and grommets to protect wiring and cables.
Consumer Products
LSR is popular in consumer goods thanks to its versatility, design flexibility, and safe skin contact properties. Key applications include kitchenware (spatulas, ice cube trays), toys, phone accessories (soft cases, button covers), and wearable technology (smartwatch bands and fitness tracker casings).
Industrial Applications
LSR is used in industrial environments where high performance, durability, and precision are required in challenging conditions. Some key applications are sealing systems, electronics enclosures, electricals (LSR is an electrical insulator), and fluid control components.
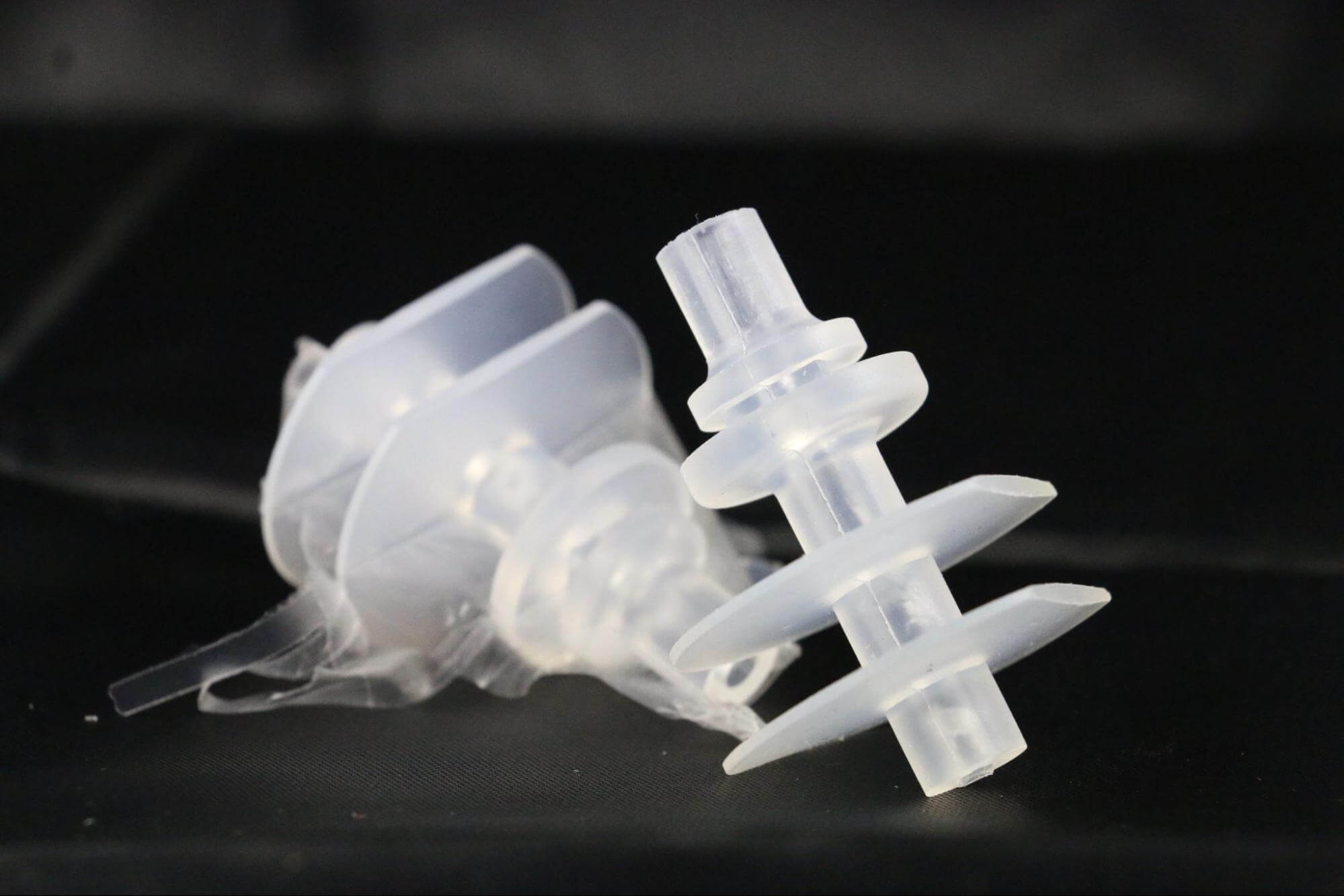
This silicone medical valve was injection molded and then cryogenically deflashed. Image Credit: Nitrofreeze
LSR vs. Other Molding Techniques
Table 4 provides a clear comparison between LSR molding and other common silicone molding techniques, highlighting the key differences, advantages, and best-use scenarios:
Feature | LSR Molding | Compression Molding | Transfer Molding | LSR Overmolding |
Material State | Liquid (2-part mix) | Solid preform | Solid preform | LSR (liquid) over insert |
Automation | High | Low to Medium | Medium | Medium to High |
Cycle Time | Fast | Slow | Medium | Medium |
Part Complexity | High | Medium | Medium | High |
Precision | Very High | Medium | High | High |
Elasticity | Excellent | Good | Good | Excellent |
Tooling Cost | High | Low | Medium | High |
Volume Suitability | High | Low to Medium | Medium | Medium to High |
Uses | Seals, gaskets, medical, etc | Large rubber parts | Grommets, connectors | Soft-touch grips, sealing |
Table 4: LSR vs. Other Molding Techniques
Fictiv for Silicone Injection Molding Services
Fictiv offers end-to-end silicone injection molding services, focusing on rapid prototyping using production-grade liquid silicone rubber. Our expertise includes material selection support and automated Design for Manufacturability (DFM) analysis, helping ensure efficient, high-quality production. We’re equipped to handle projects at any stage from initial prototyping to full-scale manufacturing.
Fictiv supports the complete product life cycle, with capabilities including 3D printing, urethane casting, traditional and specialized injection molding techniques such as overmolding, gas-assist molding, and in-mold decorating, as well as assembly, testing, and packaging.
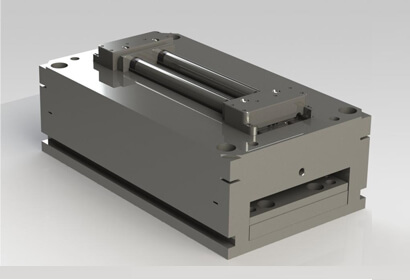
Partnering With Fictiv for LSR Molding
Liquid Silicone Rubber molding offers a powerful combination of flexibility, durability, and biocompatibility, making it ideal for a wide range of applications.
At Fictiv, we help you make smart, informed decisions about the best manufacturing method for your products. When evaluating LSR, it’s important to consider your material requirements, design complexity, regulatory compliance needs, and production volume and speed. Our experts are here to guide you every step of the way.
Get started with Fictiv today to find out if LSR is the right fit for your application.