Recently, we did a teardown of the iRobot® Braava® 380t Mopping Robot, to understand the different mechanical and manufacturing design elements that help to get you those squeaky-clean floors. Before we got started, we decided to take a step back and evaluate what features would make up a good mopping robot. The two items we narrowed in on were surface contact with the floor and navigation.
What we found were a number of decisions made to keep production costs low.
Here are the features of interest we’re drilling into for this teardown:
1. Mechanical switches
2. Suspension features
3. Manufacturing processes
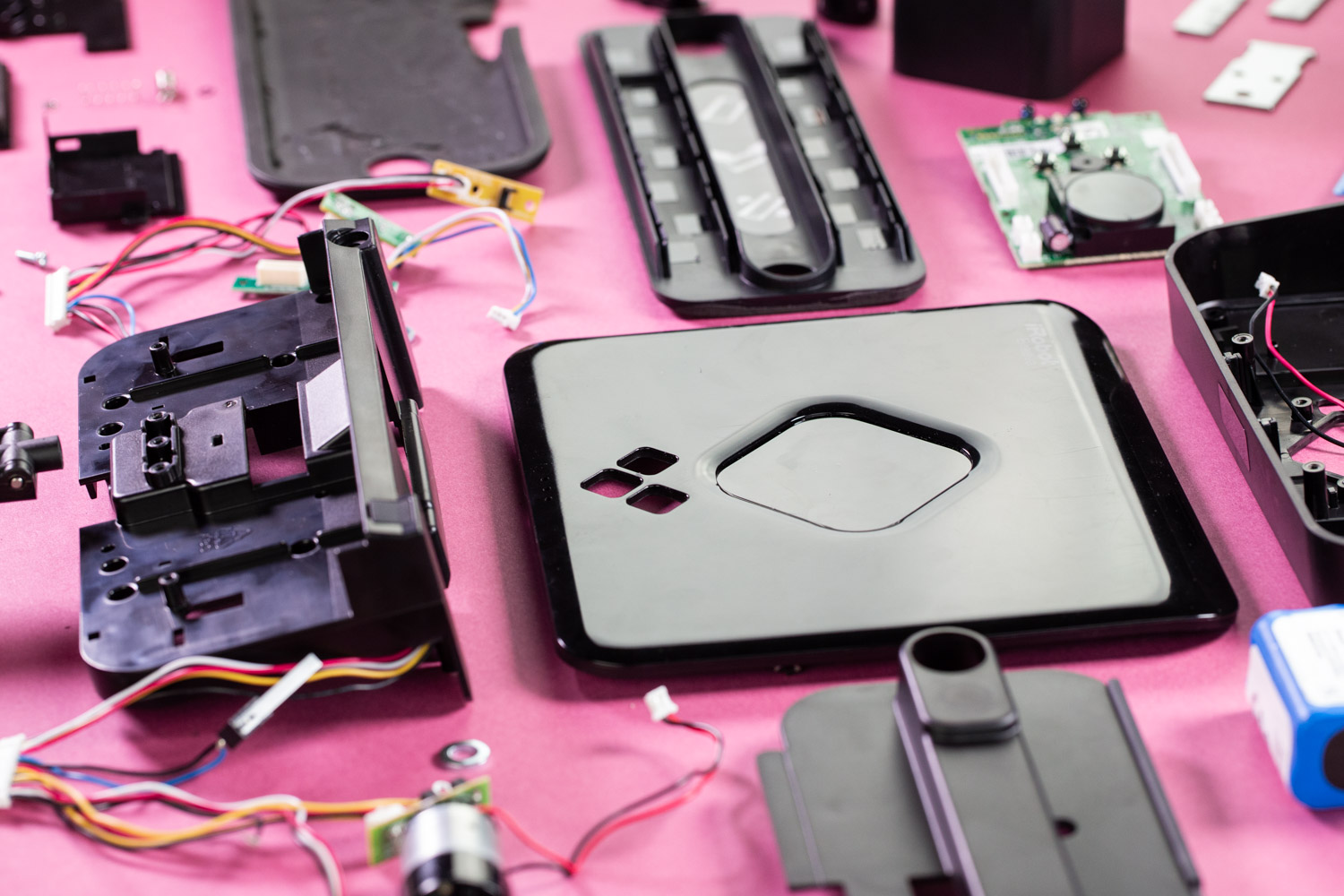
Mechanical Switches
What we noticed when opening up the enclosure was the focus on simple mechanical switches that support navigation. While the packaging emphasizes the Northstar Navigation Cubes that help wirelessly guide the Braava, internally, many of the motion controls are quite simple. While simple mechanical switches aren’t necessarily bad, it does bring up product lifecycle questions. Considering how many bumps and bruises this machine will take, will one of the mechanical switches fail?
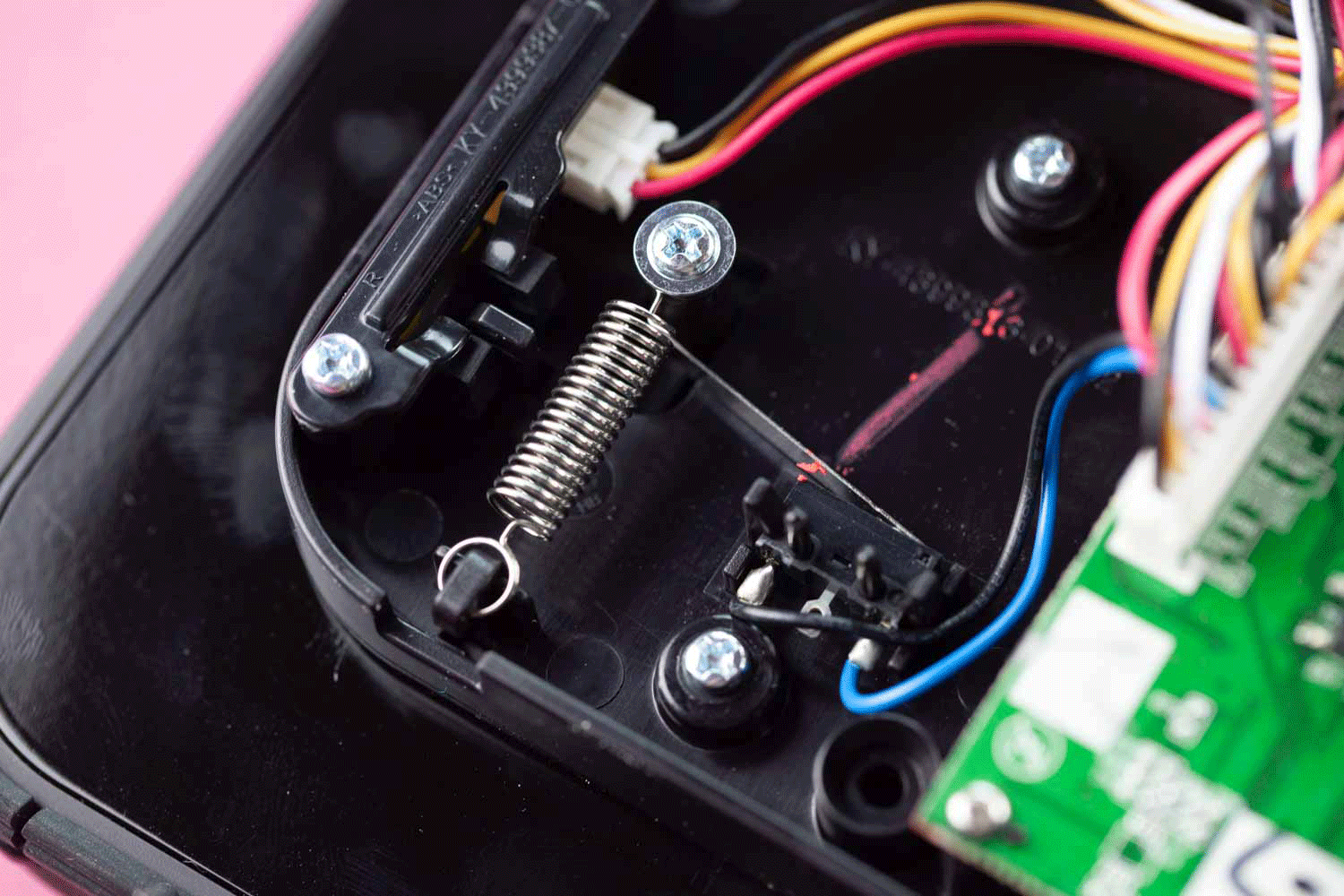
The bumper switch is a simple spring with a mechanical micro switch. When depressed (the default state), the Braava continues to move freely. When the bumper hits an obstacle, it elongates the spring and breaks the circuit in the switch, informing the robot that it’s hit an obstacle and needs to change direction.
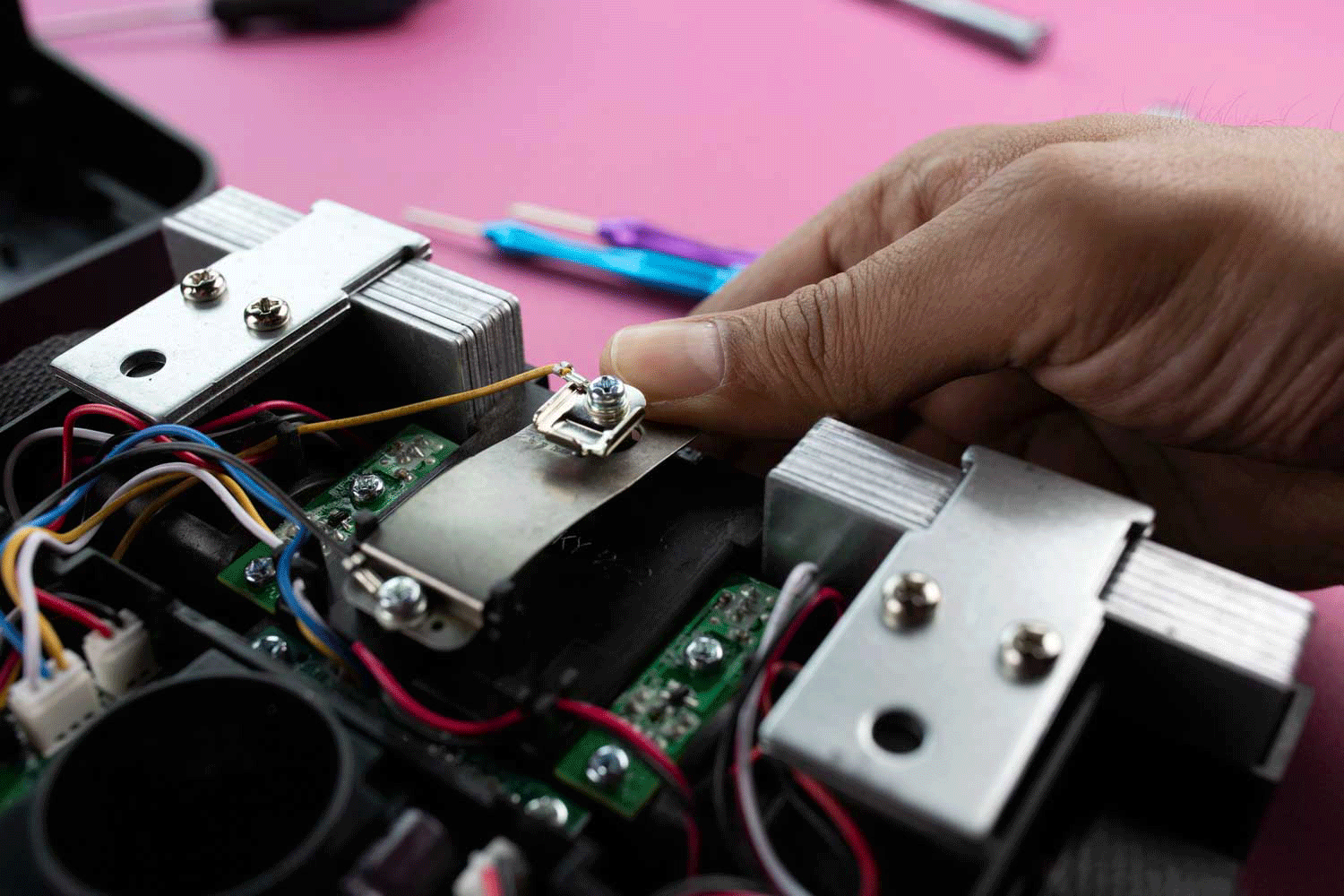
Wedge switch: Above the rear wheels is a spring steel contact switch. By default, this steel arm is pressed up against the metal plate above it, completing the circuit and telling the robot that everything is okay. When you press down on the top enclosure (or when the mopping robot wedges itself under a couch), the spring arm is depressed and loses contact with the metal plate. This tells the system that the Braava has squeezed into a spot and needs to maneuver itself backwards.
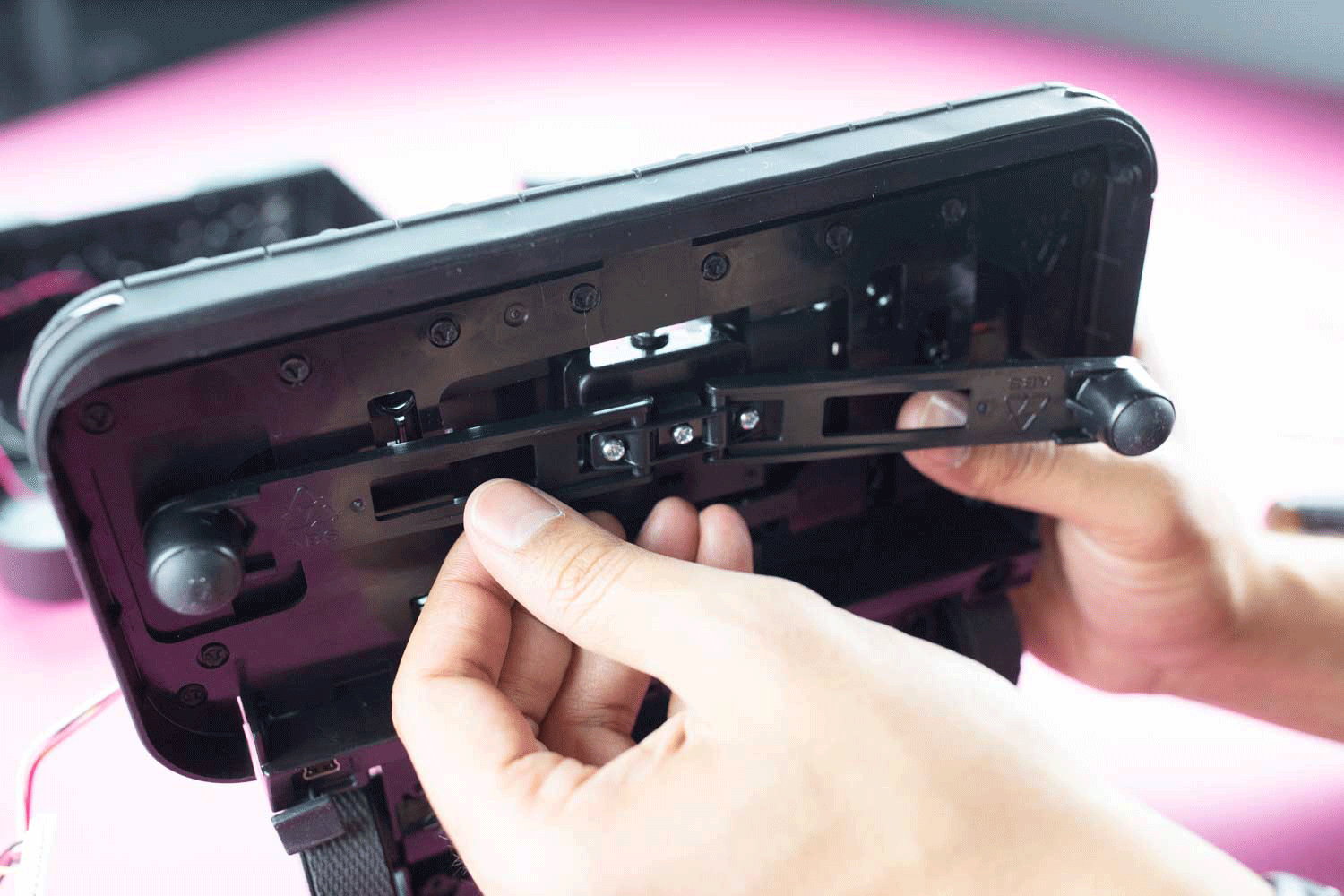
The mopping robot needs to know a way to stop when it loses contact with the floor. When it’s functioning, the floor places pressure upwards on the rubber pads, which presses arms into the enclosure. On the top side of the enclosure (not pictured), there is an IR emitter and receiver. As long as the connection between the emitter and receive is broken by the embossed feature on the back side of the arm, the Braava will continue to operate.
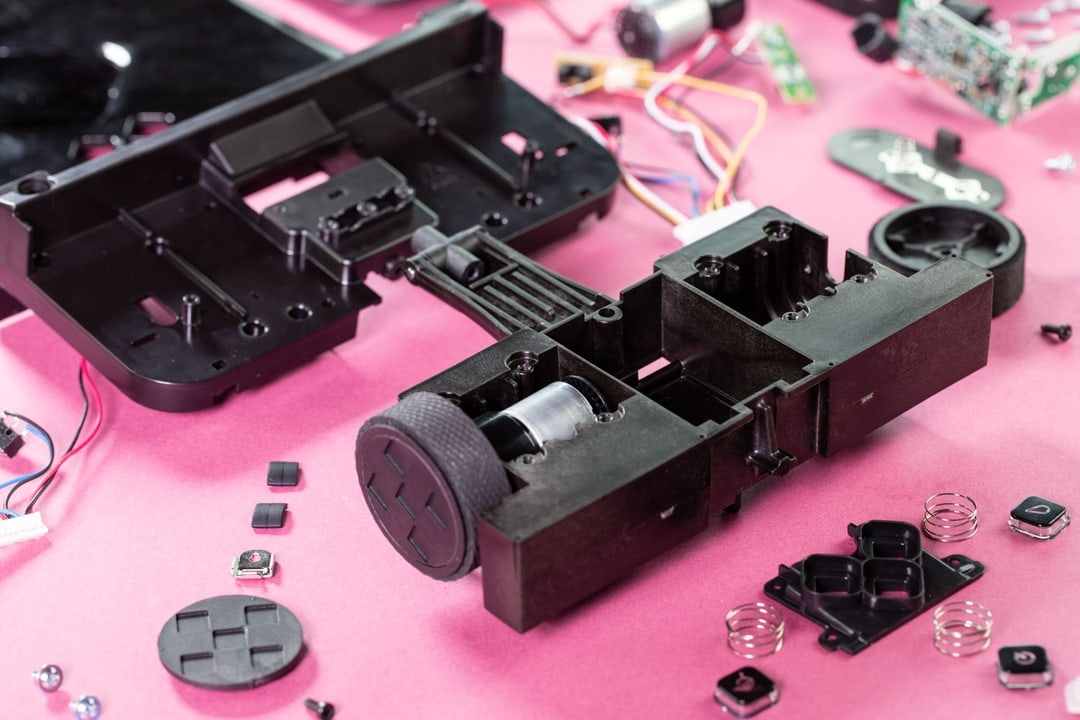
When the product is lifted (or loses contact with the ground), the arm will extend, pulling the embossed feature, which then connects the emitter and receiver, stopping the wheels.
While the Northstar Onboard Navigation system helps to ensure the Braava covers the floor area in a given room, its actual obstacle avoidance is done through a few mechanical switches and sensors. Instead of using expensive Camera Based Navigation or LiDAR technology, the Braava uses mechanical trigger switches and infrared sensors to create a cheap, yet effective, mopping robot.
Overall: Trigger switches and infrared sensors allow for the iRobot Braava to have directional navigation, avoid obstacles, and move backwards if trapped.
Suspension
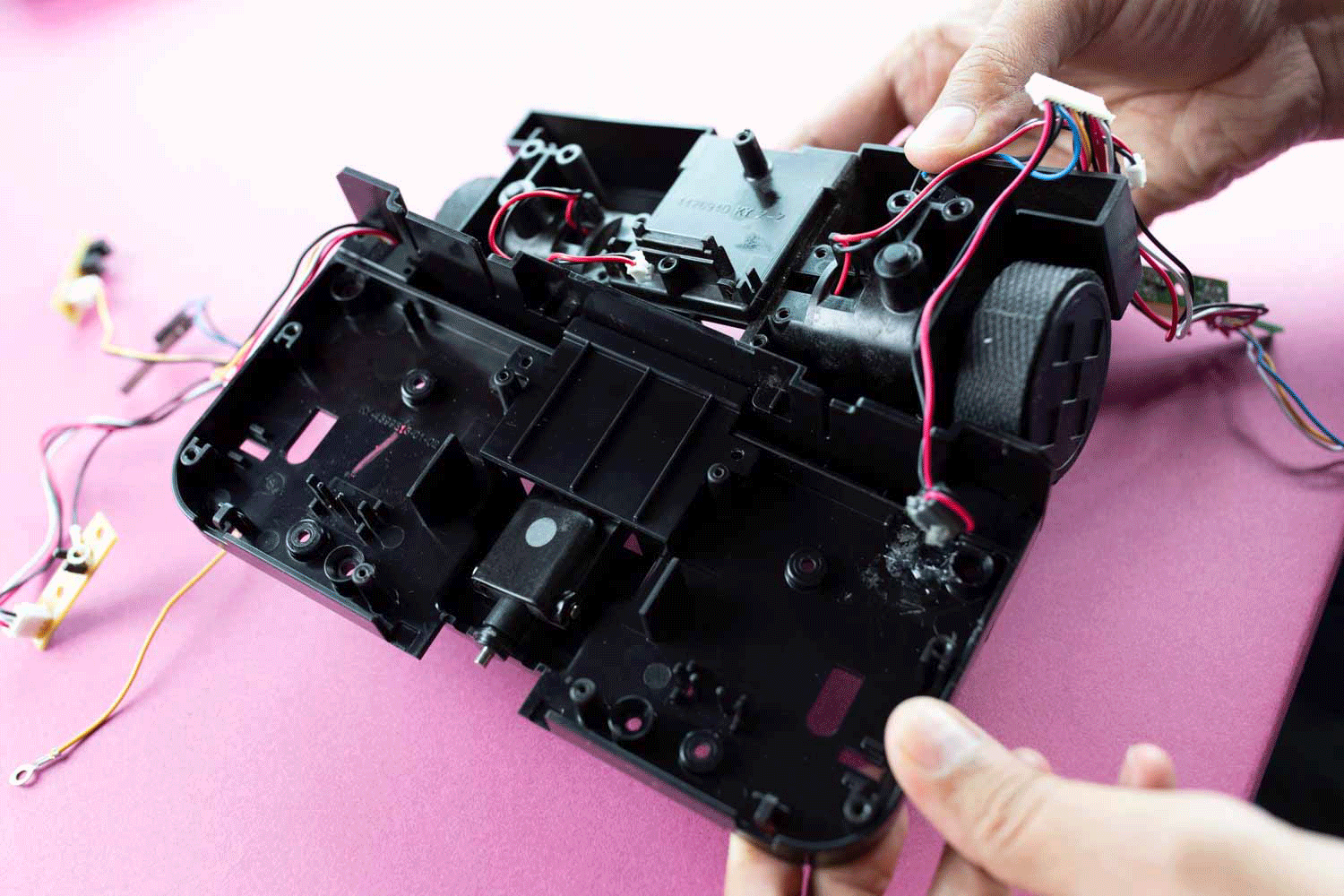
Pitch and Roll motion: To account for the changes in floor level and different types of carpeting/hardwood and ensure even and full contact with the flat mop surface, the iRobot engineers allowed freedom of motion between the back half (rear wheels) and the front half (mop). A pin and bearing assembly allows the mop to rotate side-to-side, with limits put on the amount of roll through a plastic stopper.
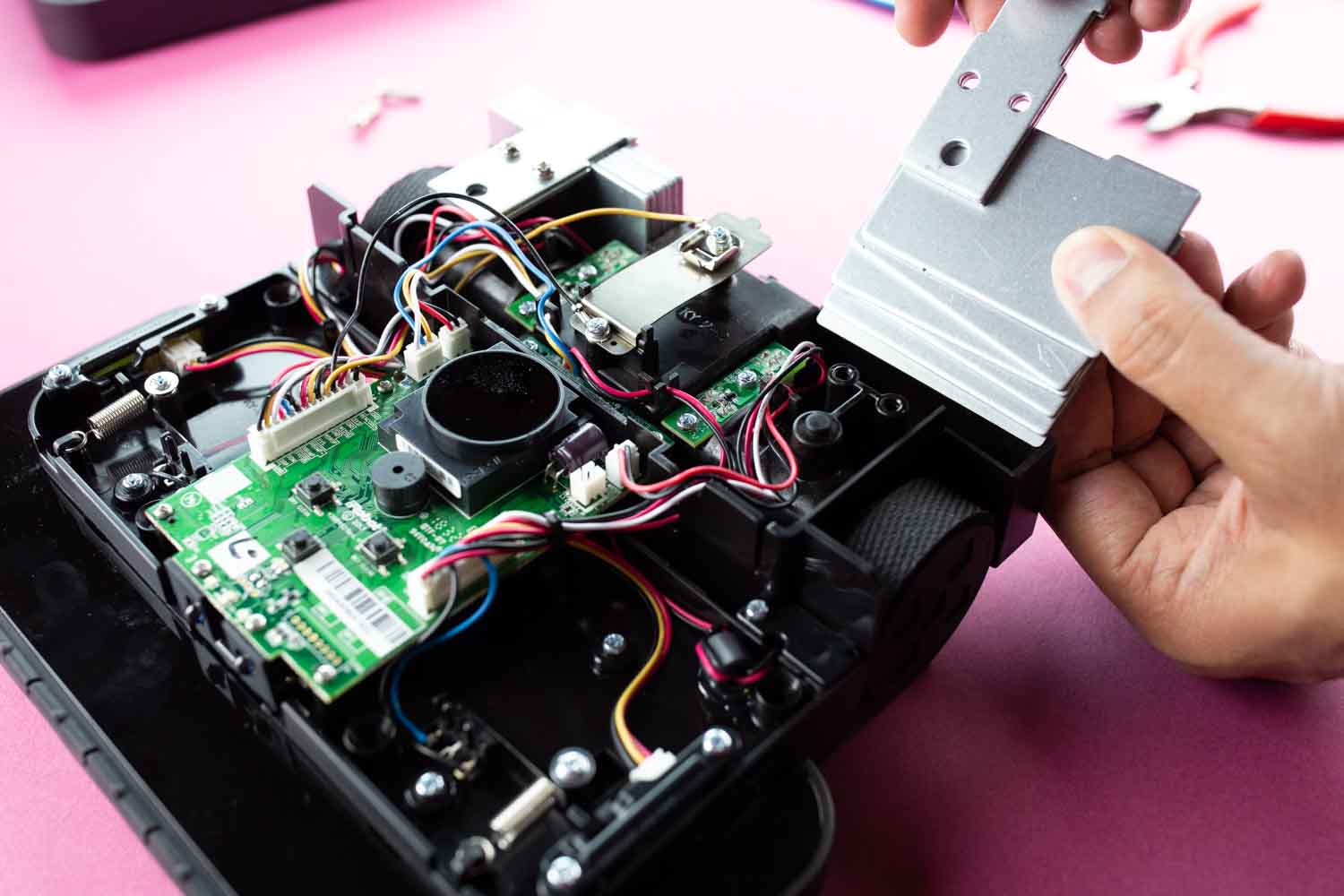
To further maintain contact with the ground, the product needs to be weighted down. Punched-out plates of steel are stacked and secured down above the rear wheels to act as ballast.
The Braava vehicle has three points of contact: two rear wheels and one large surface that acts as a mop. In order to maintain even contact with the floor, two degrees of freedom where added through a mechanical rod-and-bearing and a spring suspension. Instead of adding weight to the product by using thicker material (which increases risk or warp or sink marks) or using a more dense material (which increases cost), they simply added punched metal plates to both the mop attachments and in the main body, to ensure a good amount of force is being applied to the flow.
Overall: iRobot thoughtfully approached the suspension issue. Instead of adding to the weight with additional injection molded material, they simply added metal plates to the mop attachment and inside the main body. Force is consistently applied to keep constant contact with the ground for the Braava to do its thing (clean, mop, and sweep up debris).
Manufacturing Processes
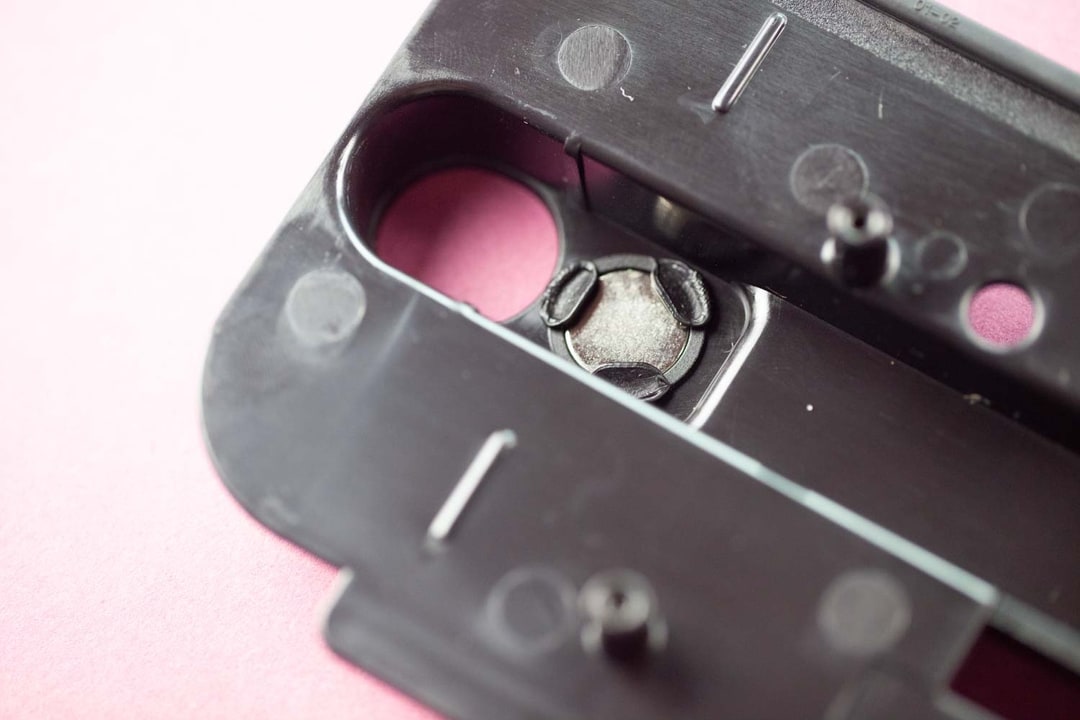
The mop attachments are held on by magnets to the bottom of the Braava. After disassembly, we see that instead of wasting time and money on overmolding in the magnets (which is difficult, because it’s likely a steel injection moulding tool), the magnet was installed via heat-staking after production.
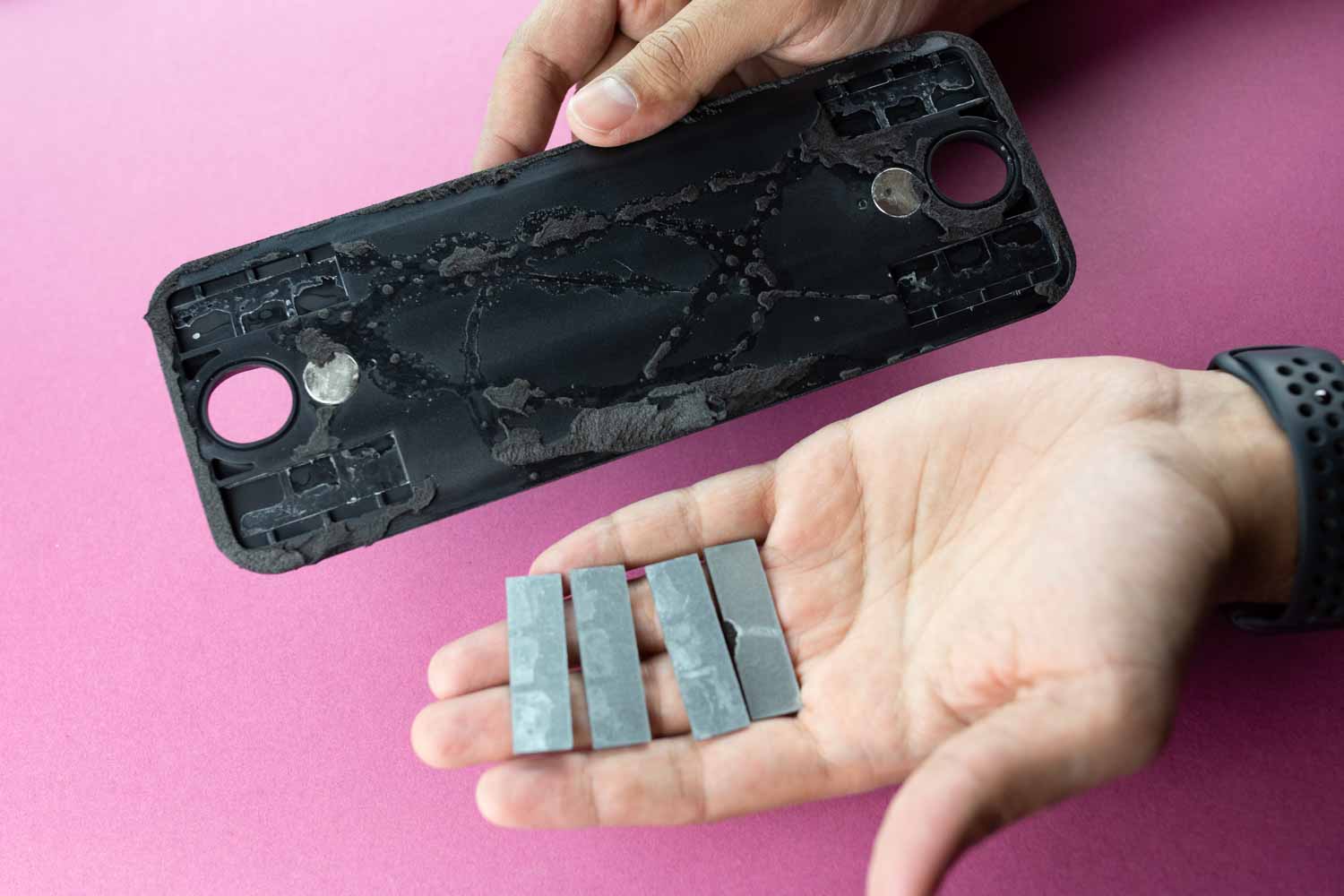
The mop half of the body also contains weights to ensure a good amount of force is placed on the floor while cleaning. Additionally, the foam pad, which acts as a barrier between the plastic to prevent scuffing on the floor, is assembled post-manufacturing with glue.
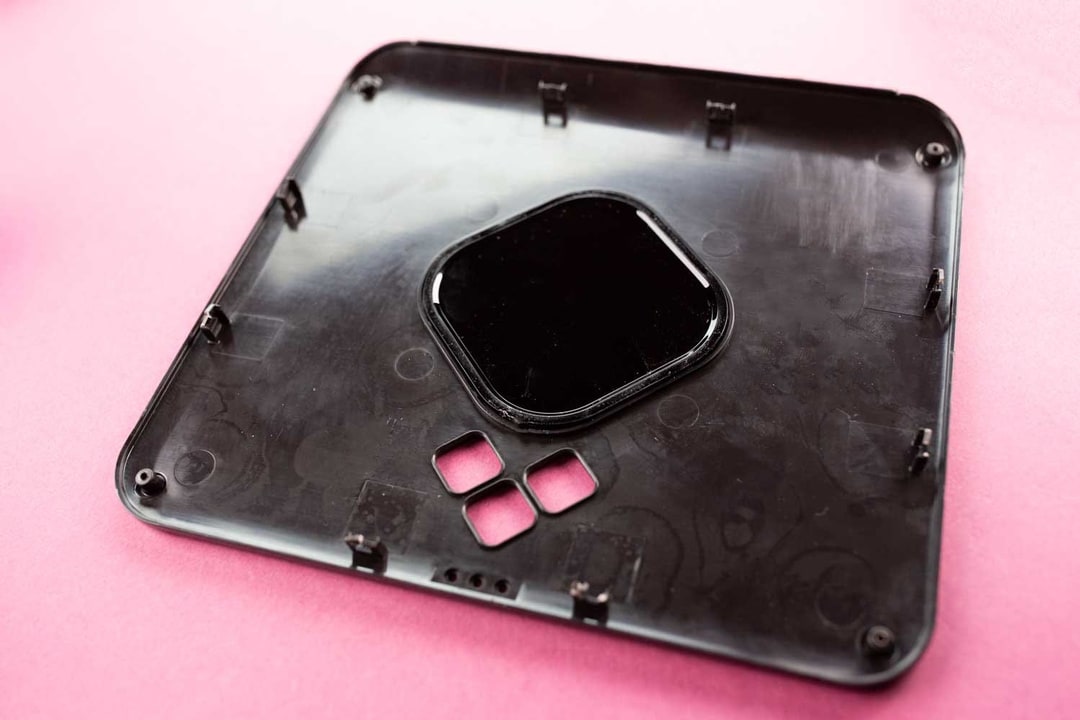
We also noticed that the product primarily uses ABS for all the plastic parts. While a PC or PC/ABS would have improved the strength, impact resistance, and weight of the product, ABS was a cheaper option. They compensated for the weight loss of the material by adding in steel weights throughout the product. While the extra impact resistance would be nice, the mechanical switches on this product are more likely to fail before the enclosure material begins to wear.
Rather than dealing with expensive or complex tooling, the engineers opted to simplify some of the assembly by doing it by hand. We see this in the heat-staked magnets and the glued-on foam barrier for the mop attachment. The main body is made of ABS, which keeps it low-cost. Around the edges, they applied a light texture and foam bumpers to help cover up some of the inevitable scuff marks. To allow for the IR signal to pass from the navigation cube to the receiver onboard the Braava, they assembled a Polycarbonate top via snap hooks. This assembly was not meant to be repaired or taken apart, and we broke every snap fit while prying off the polycarbonate top.
Overall: Simple materials and processes result in a simple, effective, and robust iRobot. The team seems to have anticipated which simple features and design additions, like bumpers and a foam barrier, would be the most useful, at the lowest cost. It also appears that they developed the product in a way that requires little human intervention.
Main Takeaways
The Braava is thoughtfully designed to be an effective iRobot sweeper/cleaner. Simplified assembly processes avoid high-cost processes. The design team seems to have considered the most important aspects of a robot cleaner and acted on it in an efficient and straightforward way, including bumpers to make sure it can navigate a living area without damaging furniture; weight to ensure proper cleaning and mopping; and practical, effective switches that get the job done.
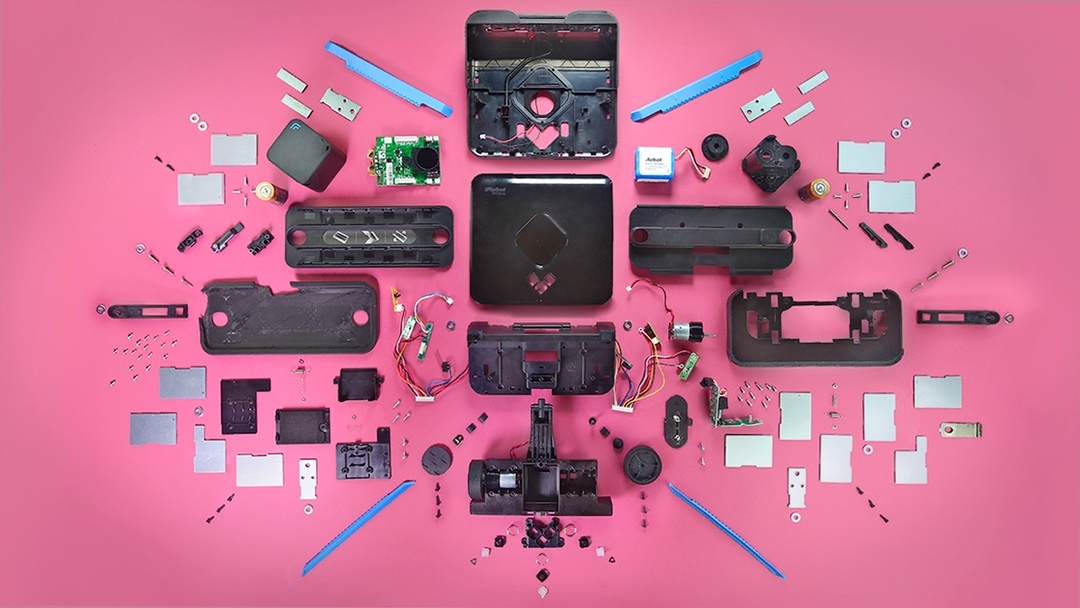