Time to read: 5 min
Styrene acrylonitrile (SAN) is a copolymer, or polymer blend, that combines the properties of styrene and acrylonitrile. Styrene contributes to SAN’s transparency, stiffness, and excellent processability. Acrylonitrile imparts SAN’s hardness, rigidity, and resistance to heat and chemicals.
Because of its exceptional properties, injection molded SAN is considered to be a specialty plastic rather than a commodity material. SAN is more expensive than polystyrene, acrylic, and polyvinyl chloride, three injection molding resins that are used for similar applications.
SAN is normally unfilled, but reinforced grades are also available. Brands of SAN resins include HYRIL®, KIBISAN®, Luran®, and Lustran®. Applications for injection molded SAN include battery housings, autoclavable medical devices, electronic enclosures, water filters, automotive components, and appliances.
If you’re considering SAN plastic for your injection molded parts, this article will discuss what you need to know about this injection molding material, including:
- advantages
- disadvantages
- properties
- design guidelines
- processing requirements
Fictiv works with a carefully vetted network of SAN injection molders who can support you from prototyping through production. When you request a quote for our plastic injection molding services, you’ll also receive design for manufacturing (DFM) assistance from our engineering experts. Create a free Fictiv account to get started.
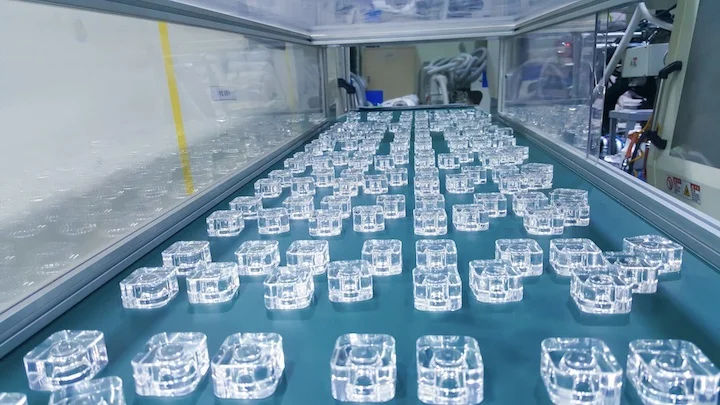
Advantages of SAN
The advantages of styrene acrylonitrile (SAN) for injection molding include dimensional stability, flow properties, transparency, chemical resistance, and colorability.
Dimensional Stability
SAN has excellent dimensional stability. Injection-molded parts that are made of this material tend to maintain their shape and size, even when subjected to varying temperatures and humidity levels.
Flow Properties
SAN flows readily and can fill complex molds and intricate geometries for the production of detailed and intricate parts.
Transparency
The natural transparency of SAN makes this injection molding resin a good choice for applications that require clear or translucent parts. Because SAN has high light transmittance, it’s also a good choice for optical or display components.
Chemical Resistance
Injection-molded SAN resins can resist a wide range of chemicals, including dilute acids and bases. SAN has excellent resistance to aliphatic and chlorinated hydrocarbons, various fats, oils, and household detergents.
Colorability
SAN resins can be pigmented to achieve specific visual effects, meet branding requirements, and support larger product designs.
Disadvantages of SAN
Despite its advantages, SAN isn’t the best choice for some types of injection molded parts. For example, it has limited heat and impact resistance, can degrade or discolor when exposed to sunlight, and is relatively expensive.
Limited Heat Resistance
The maximum use temperature for injection-molded SAN parts is 55°C. That’s lower than for some other engineering plastics.
Limited Impact Resistance
SAN lacks the impact resistance of some other injection molding materials, including commodity plastics like ABS.
UV Sensitivity
Exposure to prolonged sunlight or UV radiation, such as from UV disinfection lighting, can cause injection molded SAN to discolor and degrade. However, the addition of a UV stabilizer to the resin can help prevent UV damage.
High Cost
Because it’s a specialty material, SAN is more expensive than commodity polymers like acrylic, which is sometimes used instead.
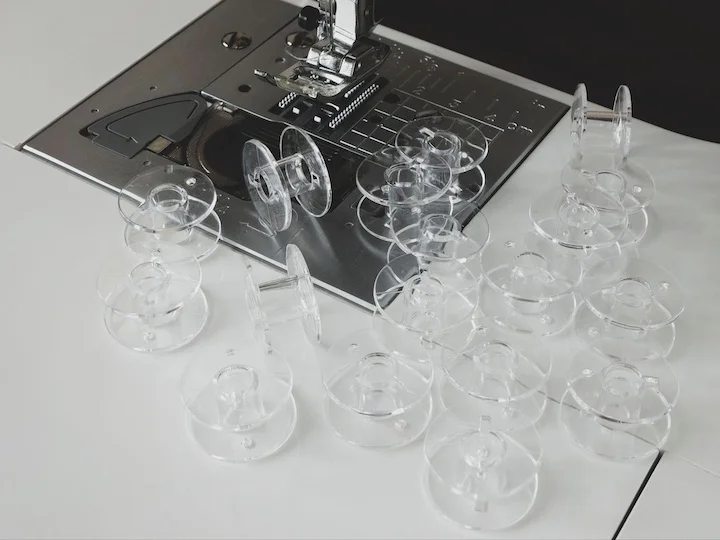
Properties of Injection Molded SAN
Before deciding to use injection molded SAN, designers must consider its physical, mechanical, and processing properties, which are listed in the table below:
Property | Value | |
Physical | Density | 0.901–1.36 g/cm3 |
Moisture Absorption at Equilibrium | 0.200–0.300% | |
Linear Mold Shrinkage | 0.00200–0.00700 cm/cm | |
Melt Flow | 0.900–120 g/10 min | |
Mechanical | Hardness, Rockwell R | 77.0–127 |
Tensile Strength, Ultimate | 16.6–113 MPa | |
Tensile Strength, Yield | 25.8–85.5 MPa | |
Modulus of Elasticity | 2.90–3.80 GPa | |
Izod Impact, Notched | 0.101–5.69 J/cm | |
Electrical | Electrical Resistivity | 1.00e+13–1.00e+16 ohm-cm |
Dielectric Constant | 2.70–3.10 | |
Thermal | Thermal Conductivity | 0.113–0.195 W/m-K |
Deflection Temperature at 0.46 MPa (66 psi) | 78.9–120 °C | |
Deflection Temperature at 1.8 MPa (264 psi) | 52.8–104 °C | |
Glass Transition Temp, Tg | 102–104 °C | |
Optical | Refractive Index | 1.56–1.57 |
Transmission, Visible | 80.0–91.0% | |
Processing | Processing Temperature | 180–280 °C |
Nozzle Temperature | 204–229 °C | |
Melt Temperature | 160–260 °C | |
Mold Temperature | 20.0–98.0 °C | |
Injection Velocity | 200 mm/sec | |
Drying Temperature | 71.1–85.0 °C | |
Injection Pressure | 4.90–137 MPa |
Table 1. Properties of SAN
Design Guidelines for SAN Injection Molding
SAN parts that are poorly designed can exhibit injection molding defects. Fictiv’s injection molding experts can help you refine your designs so that you get great results, and check out our free Injection Molding Design Guide to use as a reference for your next project.
Download the Injection Molding Design Guide
The following sections examine some SAN-specific design considerations.
Wall Thickness
The recommended wall thickness for injection-molded SAN parts ranges from 0.85 to 3.80 mm. As with other types of plastics, apply a uniform wall thickness to avoid potential part defects. If thicker walls are required in some areas, make the transition gradual. Avoid excessively thick walls because they tend to cause internal voids and sink marks.
Radii
When maintaining a uniform wall thickness is impossible, using rounded corners and smooth transitions is essential. These design elements reduce stress concentrations and eliminate stress risers, which can lead to part failure. Make internal radii at least half of the wall thickness. Make external radii larger than the inside radius plus the wall thickness.
Draft Angles
Applying a draft angle, or taper, to the walls of injected molded SAN parts makes it easier to eject them from the mold. Generally, 1° to 2° of draft is recommended.
Bosses
Although SAN has excellent dimensional stability, its limited impact resistance may require the use of bosses. These part features add structural integrity, promote part alignment, and support the use of fasteners. Best practice is to make the thickness of a boss less than 60% of the wall thickness. Doing so will help to prevent sink marks from shrinkage as the plastic cools.
Ribs
Ribs enhance structural integrity and increase load-bearing capacity. Because SAN has limited impact resistance, consider whether your part design needs ribs and where to locate them. Also, remember to incorporate fillets at the bottom of ribs and apply a radius of 0.25T-0.5T (where T is the nominal wall thickness). To help prevent sink marks, limit rib height to 2.5T.
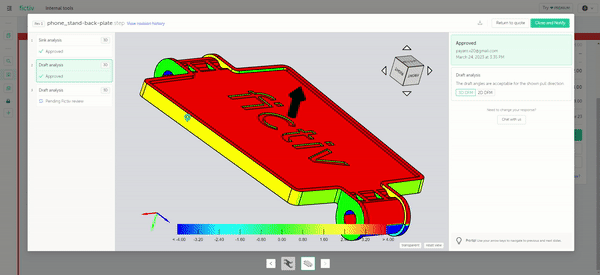
SAN Processing Guidelines
SAN injection molders need to follow specific processing guidelines for best results. Because adherence to these guidelines is beyond a part designer’s immediate control, it’s critical to work with an experienced injection molder like those in Fictiv’s carefully vetted network.
Temperature Control
SAN flows readily and has a melt temperature that ranges from 200°C to 270°C. A temperature that is too low may lead to incomplete melting and poor part quality, while temperature that is too high may cause discoloration or a reduction in mechanical properties.
Injection Speed and Pressure
Injection speed and pressure vary depending on the complexity of the part. Typically, however, SAN requires high speeds and a material injection pressure ranging from 35 to 130 MPa — to avoid problems like shearing and surface defects, balance speed against pressure.
Moisture Content
SAN resins absorb only low levels of moisture, but drying is still recommended to achieve optimal results, because if a SAN resin is overly moist, voids or blisters may occur. In general, SAN should be dried at 80° C for 2 to 4 hours prior to molding.
Succeeding with SAN Injection Molding
SAN is a popular injection molding plastic, but a manufacturing-ready design and a skilled production partner are necessary to get good results. Fictiv has the engineering experts and global manufacturing network you need to get quality injection-molded SAN parts. From prototyping through production, we’re here to help you succeed.
Create your free Fictiv account and request an injection molding quote today — we mold complex parts at ridiculous speeds!