Time to read: 8 min
It’s usually not the most organized, clean, or well-lit area in a machine shop, but it is critical in supporting machining operations. In manufacturing facilities equipped with them, the toolroom is a designated space that engineers and expert machinists use to create and maintain tooling. This area is typically separate from the main production floor and serves as a storage, production, and maintenance hub for crucial tools like jigs, fixtures, and dies. When these tools are utilized in a production run and subsequently returned, the toolroom becomes the go-to place for inspecting and repairing them. While some machine shops outsource tool maintenance and/or manufacturing, an on-site toolroom enables optimized productivity and customizability in manufacturing processes.
The tooling manufactured and maintained in a toolroom isn’t your typical hammers and wrenches; we’re talking about sophisticated, high-value, precision assemblies integrated into production machinery. Think progressive stamping tools, die sets for metal shaping, various CNC tooling, and mold assemblies for plastic injection molding.
Inevitably, these tools endure the wear and tear of daily use and occasionally face unexpected damage. That’s where the toolroom comes to the rescue. Tool and die makers work magic to repair or create replacement parts for these essential tools in a toolroom. Among the lineup of machines you’ll find in a toolroom—lathes, saws, grinders—there’s one standout player: the toolroom mill. This versatile machine takes center stage, with the precision and power to restore damaged tools and fabricate new components.
This article will discuss the toolroom mill, its indispensable role in precision manufacturing, and its essence, functionality, and significance within the manufacturing landscape.
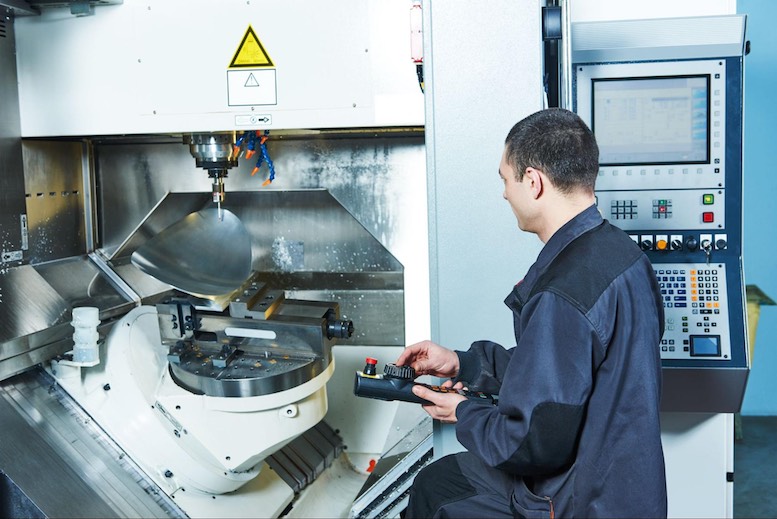
What Is a Toolroom Mill?
A toolroom mill, or a toolroom milling machine, is commonly found in toolrooms. Toolrooms are segregated areas in manufacturing facilities where tools such as jigs, fixtures, and dies are machined, stored, inspected, and repaired. These tools are typically complex and expensive assemblies used in production machinery on the shop floor, such as progressive stamping tools, die sets, and mold assemblies. Watch just how versatile toolroom mills are and check out this inspiring engineer’s story in this video:
Machining Race Car Parts on a Haas CNC Toolroom Mill in a Home Garage Shop
The purpose of a toolroom mill is to provide a machine tool within the toolroom for the repair and production of replacement parts for these tools. A toolroom mill is operated by specially trained machinists, often referred to as tool and die makers, who use the machine to restore and maintain tool functionality.
What sets a toolroom mill apart is its unique characteristics and features. These machines typically have a smaller footprint than standard milling machines, designed to produce precision work on a reduced scale. They can create one-off parts, similar to a job shop specializing in prototyping. Another distinguishing feature of a toolroom mill is that it is predominantly utilized to machine extremely hard metals. For example, steel, such as low-carbon steel and solid carbide, is commonly utilized for CNC tooling.
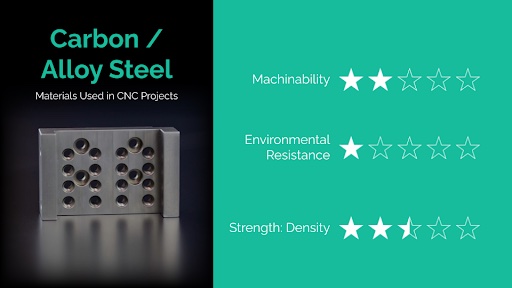
Pro-Tip: To learn more about the most commonly utilized CNC materials, check out CNC Materials Series: Common Materials Used in CNC Projects
Toolroom mills can be standard milling machines or small vertical machining centers (VMCs) with automatic tool changers (ATCs). Their small footprint makes them ideal for toolrooms where space is limited. Precision is a key requirement for tool and die work, so a toolroom mill consistently holds tight tolerances. Despite their precision, toolroom mills are affordable for minor operations, and options like manual or CNC (Computer Numerical Control) modes provide flexibility for different machining tasks.
What Is the Purpose of a Toolroom Mill?
The purpose of a toolroom mill is to provide a dedicated machine for precision machining tasks in toolrooms. Here are some specific purposes and applications of a toolroom mill:
- Tool and Die Manufacturing: Toolroom mills are essential for tool and die making, which involves the production and maintenance of tools, dies, and molds used in manufacturing processes. These machines allow machinists to create, repair, and modify tools with exceptional precision, ensuring the accuracy and quality of the finished products.
- Prototyping: Toolroom mills are often used for prototyping new products or components. They enable machinists to quickly fabricate prototypes based on design specifications, allowing for iterative testing, refinement, and validation before full-scale production. Toolroom mills’ high precision and versatility make them ideal for creating one-off or low-volume prototypes.
- Precision Machining: Toolroom mills excel at precision machining tasks that require tight tolerances, intricate geometries, and fine surface finishes. They can accurately machine complex parts and components used in aerospace, automotive, electronics, and medical devices.
- Repair and Maintenance: In toolrooms, tools, dies, jigs, and fixtures often undergo wear and tear or accidental damage during production runs. Toolroom mills provide the means to repair or replace these components, extending their lifespan and ensuring their continued functionality.
- Customization and Modification: Toolroom mills allow for the customization and modification of existing tools and components. Machinists can use these machines to adapt tools and dies to specific production requirements or optimize their performance by leveraging the precision and flexibility of toolroom mills.
- Small-Scale Production: While toolroom mills primarily serve toolroom operations, they can also support small-scale production runs. These machines can produce limited quantities of precision components, enabling manufacturers to efficiently fulfill specialized orders or address low-volume production needs.
What Are the Essential Features of a Toolroom Mill?
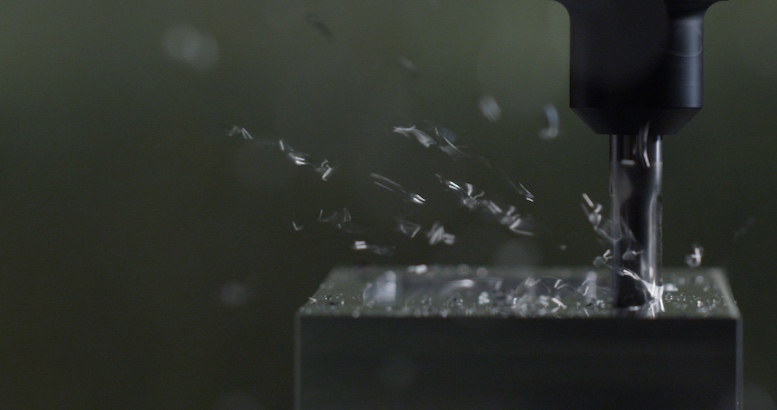
When considering the purchase of a toolroom mill, it is crucial to consider the available space, the nature of the anticipated work, and the intended operators. Keeping these factors in mind, here are the key features to look for:
- High Precision and Accuracy: Toolroom mills are expected to deliver precise and accurate machining results. To expertly purchase a toolroom mill, look for machines with high-quality linear guideways, precision ball screws, and rigid construction to ensure consistent accuracy. Toolroom mills should be built with high-quality components and should be able to hold tight tolerances to ensure accurate and repeatable machining results.
- Compact Size: Toolroom mills are typically designed to be compact and space-saving, making them suitable for toolrooms and smaller workshop environments. The machine should have a small footprint while providing sufficient workspace for the intended machining tasks.
- Versatile Machining Options: Toolroom mills should offer versatile machining options for various applications, which helps to further strengthen the agility of a toolroom. Look for machines that can perform various machining operations such as milling, drilling, tapping, and even limited turning, if required. Also, look for a machine with flexibility in manual and CNC operation. The versatility of having a 3-axis CNC capability for intricate fixtures and molds and the convenience of a manual mill for tasks like tapped holes or quick slots significantly enhance a machinist’s productivity.
- User-Friendly Controls and Interface: The control interface of the toolroom mill should be intuitive and user-friendly. It should provide easy programming options, a clear display, and straightforward navigation for manual and CNC modes. A shallow learning curve ensures that novice and experienced machinists can quickly grasp and operate the CNC toolroom mill effectively.
- Tooling Options: Toolroom mills are compatible with various cutting tools, including end mills, drills, reamers, and special tooling for specific applications.
- Table Movement: Toolroom mills typically have a movable table that can be adjusted in multiple directions (X, Y, and Z axes), enabling the machining of complex geometries. A 4th-axis rotary table expands the possibilities for machining intricate components.
- 4th-Axis Capability: In addition to the standard X, Y, and Z-axis movements, the inclusion of a 4th-axis rotary table provides expanded machining options for intricate and complex parts.
- Coolant System: A built-in coolant system is crucial for maintaining optimal temperatures during machining, preventing tool failure, and efficiently removing chips from the workpiece.
- Taper Spindle: An R8 taper, commonly found on Bridgeport-type mills, offers a wider selection of tooling options, including end mills and chucks, often at a more affordable price.
- Conversational Programming: Many CNC controls include conversational programming, enabling machinists to create operations using G-code through a question-and-answer format. This feature mimics the approach of a manual machinist, facilitating ease of use and programming efficiency.
What Are the Advantages and Disadvantages of a Toolroom Mill?
Toolroom mills have some advantages and disadvantages that are important to consider. Both the advantages and disadvantages are listed in the sections below.
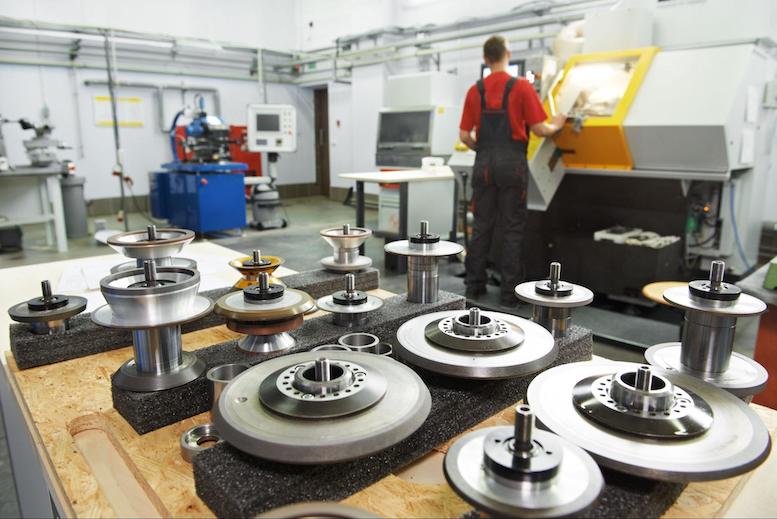
Advantages of Toolroom Mills:
The advantages of toolroom mills are as follows:
- Precision and Accuracy: Toolroom mills are designed to provide high precision and accuracy in machining operations. They can achieve tight tolerances, ensuring the production of precise and high-quality components.
- Versatility: Toolroom mills offer versatility in terms of the range of materials they can handle and the variety of machining operations they can perform. They are suitable for machining metals, plastics, and composites, making them adaptable to different manufacturing requirements.
- Compact Size: Toolroom mills are generally smaller and more compact compared to full-size milling machines. This allows them to fit into limited spaces such as toolrooms or small workshops.
- Flexibility: Many toolroom mills offer both manual and CNC modes of operation. This flexibility allows operators to choose the most suitable mode based on the complexity of the task and their expertise.
- Cost-Effectiveness: Toolroom mills are often more affordable than larger milling machines, making them a cost-effective option for toolrooms, small-scale production, and prototyping. They provide excellent value for their precision and functionality.
Disadvantages of Toolroom Mills:
While a toolroom mill offers certain advantages over a full-size milling machine, it also comes with a few drawbacks:
- Limited Size: Toolroom mills are typically smaller than larger milling machines. This limited size may pose challenges when machining larger or bulkier workpieces. Additionally, their smaller size can reduce rigidity, affecting the ability to take deep cuts or handle heavy-duty machining tasks.
- Production Capacity: While toolroom mills can handle small-scale production, they may not be suitable for high-volume production due to their smaller size and potentially slower production rates. Larger milling machines with higher production capacities are more suitable for large-scale manufacturing.
- Learning Curve: Operating toolroom mills may require specialized training and knowledge. The learning curve can be steep for operators unfamiliar with CNC programming and machining and for those who perform manual machining.
Importance of Toolroom Mills
A toolroom mill is vital in manufacturing facilities, particularly within toolrooms where precision and versatility are paramount. Its compact size, high precision, and CNC capabilities offer a range of advantages. Toolroom mills enable the efficient repair and production of complex tools, jigs, and fixtures, ensuring the smooth operation of production machinery. However, it’s important to consider the limitations of toolroom mills, such as their smaller size and potential material constraints.
Manufacturers can make informed decisions when incorporating toolroom mills into their operations by understanding the essential features and carefully assessing specific machining requirements. Whether used for prototyping, small-scale production, or tool maintenance, a well-equipped and properly utilized toolroom mill can contribute to enhanced productivity, accuracy, and cost-effectiveness in various manufacturing settings.
Fictiv – Sourcing Simplified
Regardless of what CNC machined components you need, Fictiv has you covered. Our manufacturing ecosystem provides much more than your typical outsourced manufacturing company. We offer instant online quotes via our intelligent platform, which partners you directly with world-class CNC machine shops. Our expert supplier quality processes vet all of our manufacturing partners. Our flexible pricing structure allows you to ensure your budget constraints are met while providing you with fast parts that have tight tolerances. In addition, we deliver high quality by providing services such as hand metrology, laser, and CMM inspection.
We also offer 40% faster lead times vs. the industry average!
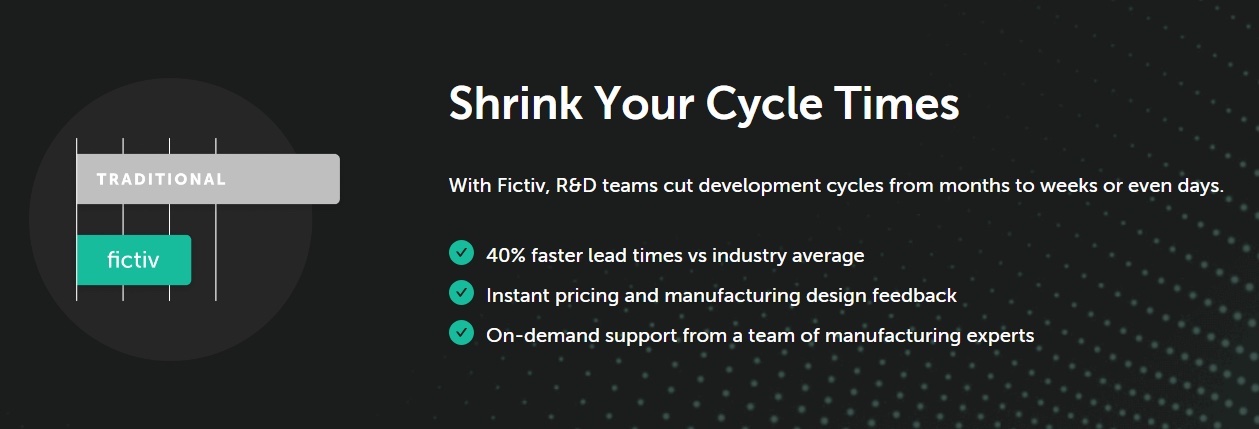
Upload your parts to get an instant online CNC quote today and see how our innovative manufacturing ecosystem can revolutionize your business.