Time to read: 5 min
Injection molding and vacuum thermoforming are both used to produce plastic parts. Both processes apply heat to plastics, create parts from some of the same types of materials, and use molds. Injection molding and vacuum thermoforming are also similar in that they both require draft angles and can support undercuts, ribs, bosses, and textures on finished parts. For both processes, rounded corners (radii) that reduce stress concentrations are recommended and post-processing may be required.
Despite these similarities, there are important differences between injection molding and vacuum thermoforming, beginning with how each process works. These differences extend to materials and tooling, and support design complexity and high production volumes. If you’re wondering whether injection molding or vacuum thermoforming is the right choice for your part design, keep reading to learn more.
And if you’re going to be using injection molding, check out our free design guide for tips and best practices.
Download Fictiv’s Injection Molding Design Guide
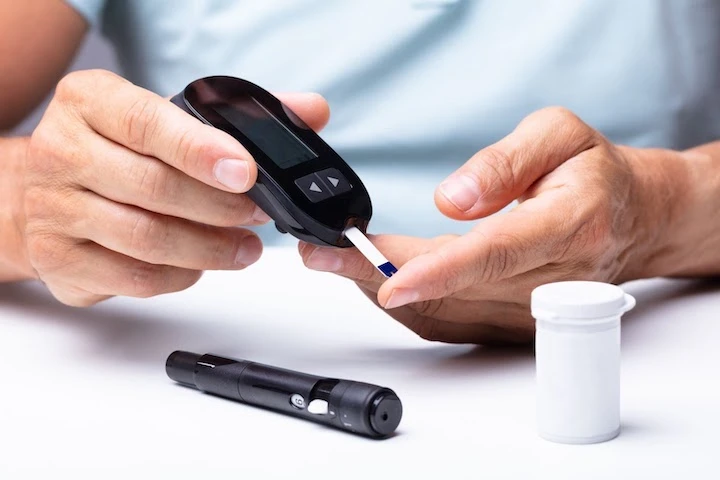
Some examples of injection molded parts
How does injection molding work?
Plastic injection molding begins when plastic pellets or granules are poured into a hopper, then dispensed into a barrel where the material is heated and melted into a liquid. A large reciprocating screw then pushes this molten material toward the tip of the barrel while raising the plastic’s pressure and temperature. When enough material and pressure build-up, a ram pushes the screw toward the mold. This forces a “shot” of plastic out of the barrel via a nozzle and sprue and into a system of runners (channels cut into the mold).
From the runners, the molten material passes through one or more gates, which are openings in the mold cavity whose location, size, and shape have a significant effect on the final part. Injection molds can feature one cavity or multiple cavities, each of which can be used to create a single part. A clamping unit keeps the mold closed during injection and subsequent cooling. When the part is ready, the mold is opened and the part is extracted, sometimes with mechanical devices such as sliders and lifters. If injection molded parts require finishing, post-processing techniques such as gate trimming and heat staking can be used.
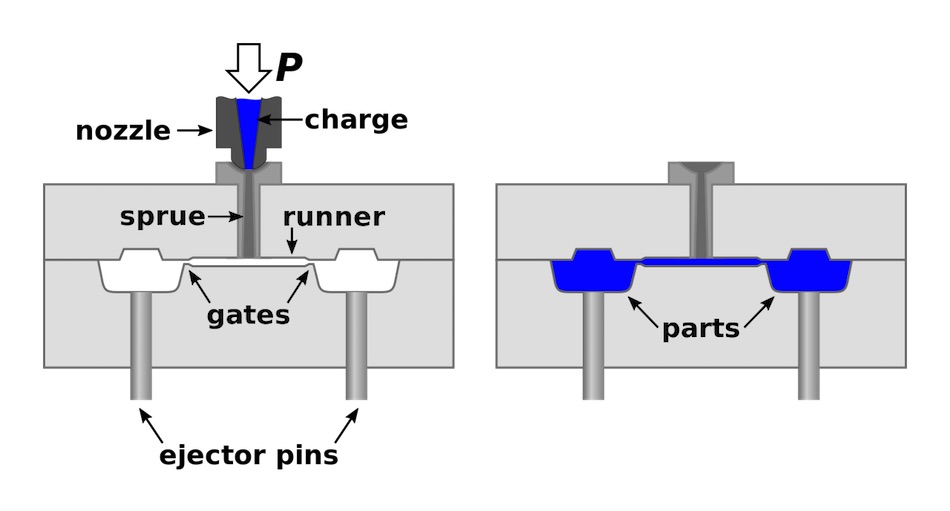
The injection molding process uses more complex molds than vacuum forming
How does vacuum thermoforming work?
With vacuum forming, a plastic sheet is clamped in place and heated until it becomes soft and pliable. This sheet is then stretched across a mold with the shape of the part. The mold is then covered and the air is evacuated between the heated sheet and the mold to create a vacuum. This low-pressure condition causes the plastic sheet to sag, pull against the mold, and form the part’s final shape. After the part cools, it’s removed from the mold and excess plastic is trimmed, either by hand or with CNC or robotic equipment.
Because the plastic in the corners and at the top edges of the mold stretches the most, this material is also the thinnest. To promote a more uniform thickness, straight vacuum forming can be supplemented with billow forming and plug assists. With billow forming, a stream of air is applied to the softened sheet so that it’s blown into a bubble with roughly the same surface area as the plastic part. The air is then evacuated from beneath the mold to create a vacuum that pulls the sheet against the mold’s walls. A plug assist can be used to pre-stretch the heated sheet prior to the creation of vacuum pressure.
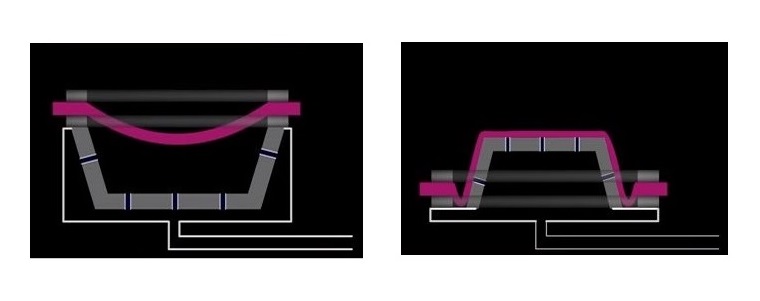
The vacuum thermoforming process uses plastic sheets instead of pellets or granules
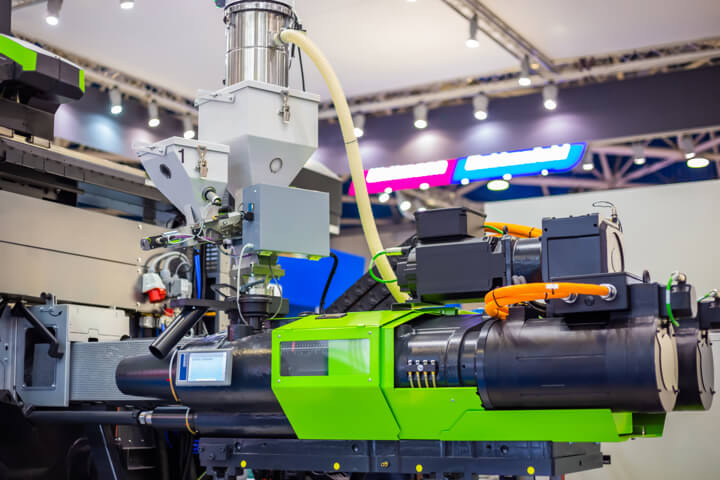
A plastic injection molding machine
How do these plastics manufacturing processes compare in terms of materials and tools?
Broadly speaking, injection molding isn’t limited to plastics and includes rubber injection molding, liquid silicone rubber (LSR) molding, and metal injection molding (MIM). Vacuum-forming materials are limited to plastics, and to thermoplastics in particular. By contrast, the injection molding process can be used with either thermosets or thermoplastics, materials that can be repeatedly heated and melted. Injection molding also supports the use of glass-filled and fiberglass-filled polymers.
Like vacuum forming, plastic injection molding uses commonly available plastic materials such as acrylic, polypropylene, polyethylene, polystyrene, and polyvinyl chloride – just to name a few. In addition to these commodity materials, designers can choose specialty plastics in fireproof, food-safe, or biocompatible grades for both injection molding and vacuum thermoforming.
Importantly, vacuum forming and injection molding differ in terms of tooling. Vacuum molds are either convex (male) or concave (female). With convex or male molds, the plastic sheet is placed over the tooling. With concave or female molds, the plastic sheet is placed inside the mold instead. Typically, convex molds are used when the inside dimensions of the part are especially important. By contrast, concave molds are used when the part’s outer dimensions are more important that its inner dimensions.
Vacuum forming is the simplest type of thermoforming, a family of processes that includes plastic pressure forming and twin sheet thermoforming, and uses tools that are relatively simple and inexpensive. In addition to wooden patterns and epoxy molds, temperature-controlled aluminum tools are used. By contrast, injection molds can be made of aluminum, soft or semi-hardened steels, or hardened steels. These harder tooling materials support both higher volumes and greater design complexity.
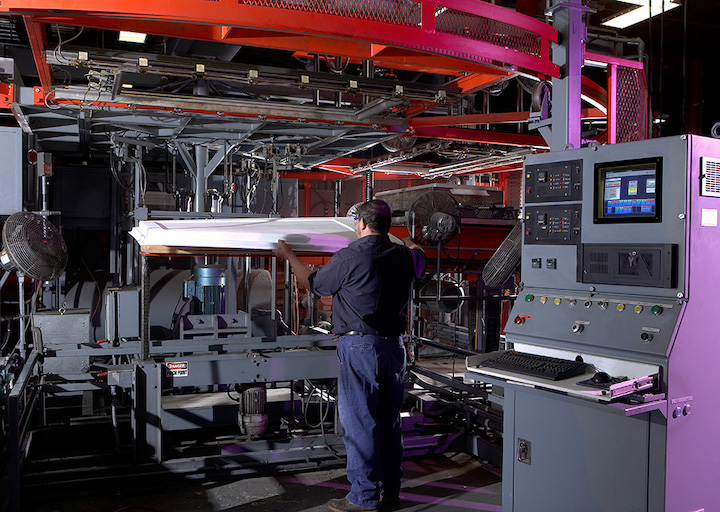
A vacuum-forming machine
How do injection molding and vacuum forming compare in terms of complexity and volume?
Injection molding is better suited for products with intricate designs and tighter tolerances. In part, that’s because stretching the plastic sheet during vacuum forming is less controlled, and the shaping of the part occurs in only one direction. Although vacuum forming can achieve thinner walls and larger parts, it’s limited to hollow parts and simpler shapes such as panels or blister packs. By contrast, injection molded parts can have just about any shape, including solid products like threaded plastic fasteners, and can produce small parts and fine details.
Injection molding also supports the use of multiple materials, such as silicone that’s over-molded onto harder plastic. Examples include clips, snap fits, living hinges, and parts embossed with text. With its tighter control of processing parameters, injection molding also supports greater part-to-part consistency, which makes it a better choice for higher production volumes.
Compared to vacuum molds, injection molds cost more, but last longer. For smaller production runs, such as 250 to 300 parts per year, vacuum forming is especially cost-effective. Because they’re simpler, vacuum molds also take less time to produce. With the right manufacturing partner, however, injection molding can support not only high-volume production runs but prototyping and low-volume production. Typically, injection molds for high volumes are made from hardened steels. By contrast, low-volume molds are made of aluminum or soft or semi-hardened steel.
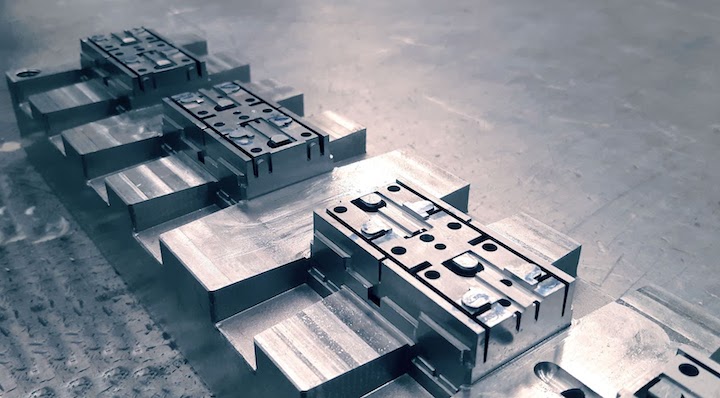
Fictiv offers cost-effective steel molds for lower production volumes
Get Complex Parts Fast – and in Any Volume
Regardless of the number of parts you need to produce, it’s important to get design for manufacturing (DFM) assistance as soon as possible during the design process, especially with complex parts. A good plan and skilled production partner are critical to get good results, and Fictiv has the global manufacturing network and production experts you need to get quality injection molded parts, no matter how complex your designs.
When you create a Fictiv account and upload your part design, you’ll receive more than just a quote for your injection molded parts. You get DFM feedback and expert manufacturing guidance to ensure the success of your project, from prototyping through production.