Time to read: 8 min
Urethane casting vs. injection molding is a comparison between two ways to mold parts.
Urethane casting is for early-stage prototyping, low-volume production runs from 1 to 100 parts, and for bridging the gap between low-volume and high-volume production. It uses soft tooling, typically made from silicone rubber, and relatively inexpensive production molds. Part details are readily achievable, but material selection is limited to polyurethanes, a group of polymers.
Injection molding is for later-stage prototyping, low-volume production runs from 100 to 10,000 parts, and high-volume manufacturing. Because this process uses hard tooling made of aluminum or steel, injection molds are relatively expensive and time-consuming to produce. However, metal tooling lasts longer and can produce parts with finer details and tighter tolerances. In addition, injection molding supports a broader range of materials and part sizes.
This article compares urethane casting vs. injection molding in detail so that you can make the best choice for your next project.
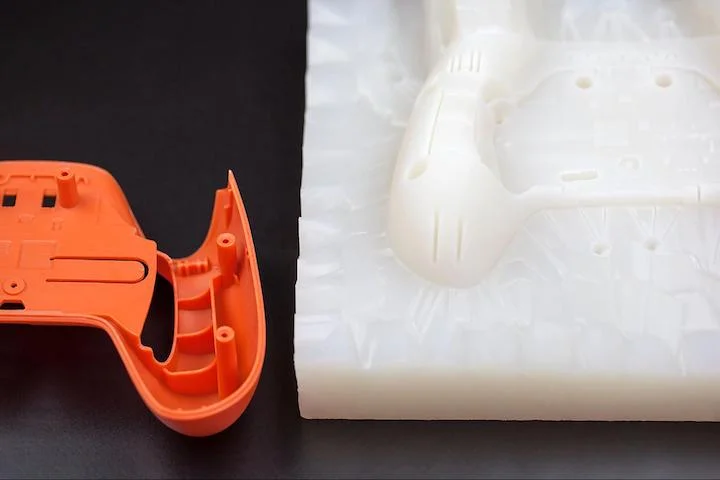
Urethane Casting: A Closer Look
Urethane casting uses polyurethane resins and a production mold that is based on a tool called a “master pattern.” The following sections cover core concepts, including the advantages and disadvantages of urethane casting.
Polyurethane Resins
Polyurethane resins are produced by mixing various materials together. The mechanical properties of your molded parts depend on the specific resin formulation. For example, to reduce friction, a molder may include slip additives.
Master Pattern and Production Molds
Production tooling is cast with silicone, but based on a master pattern that is milled, machined, or 3D printed. This master pattern, a replica of the end-use part, can be made of plastic or another relatively inexpensive material. Because silicone molds can withstand only about 25 shots per cavity, your project may require several molds based on a master pattern.
Pour and Cure Processing
Parts production begins when the polyurethane resin is poured, or cast, into a production mold. The resin is then allowed to cure so that it acquires its final end-use properties. Some resins take longer than others, but most cure at room temperature. Because urethanes shrink during curing, part designers and mold makers must account for dimensional changes.
Advantages of Urethane Casting
The advantages of urethane casting begin with tooling. Silicone molds cost much less than the steel and aluminum tools used in injection molding. This makes urethane casting a cost-effective choice across low part volumes and when design changes are expected, such as during early-stage prototyping. Urethane casting is also cost-effective if you need bridge tooling.
The silicone molds in urethane casting take less time to produce than machined metal tools in injection molding. Therefore, urethane casting supports faster design iterations. Some master patterns are made with CNC machining, but many are drilled, milled, or 3D printed instead.
Part designers also like how urethane casting is both flexible and forgiving. Although a uniform wall thickness is recommended, it’s not a strict design requirement. Plus, urethane casting does not require draft, and undercuts are easy to achieve. There are design rules for ribs and bosses, but that’s also the case with injection molding.
For more design information, refer to these free resources.
Download the Urethane Casting Design Guide
Download the Injection Molding Design Guide
Disadvantages of Urethane Casting
Polyurethanes are versatile and let a molder tailor a compound’s properties to the specific application. However, urethane casting is limited to polyurethanes, polymers with minimal resistance to heat, solvents, and weathering. In other words, urethane casting might not be able to meet some of your requirements for end-use parts.
That could be a problem if you need part samples made of the same material you plan to use during production. Because polyurethanes have a relatively high coefficient of thermal expansion, a part with a 0.005” tolerance at room temperature could become out of tolerance when heated by as little as 30 degrees.
Although urethane casting is cost-effective at low volumes, it’s not a good choice for large-scale manufacturing and often requires post-processing. Silicone molds deteriorate after several uses, and mold-making of any type incurs labor costs. The pour-and-cast process used in urethane casting also tends to limit the maximum part size.
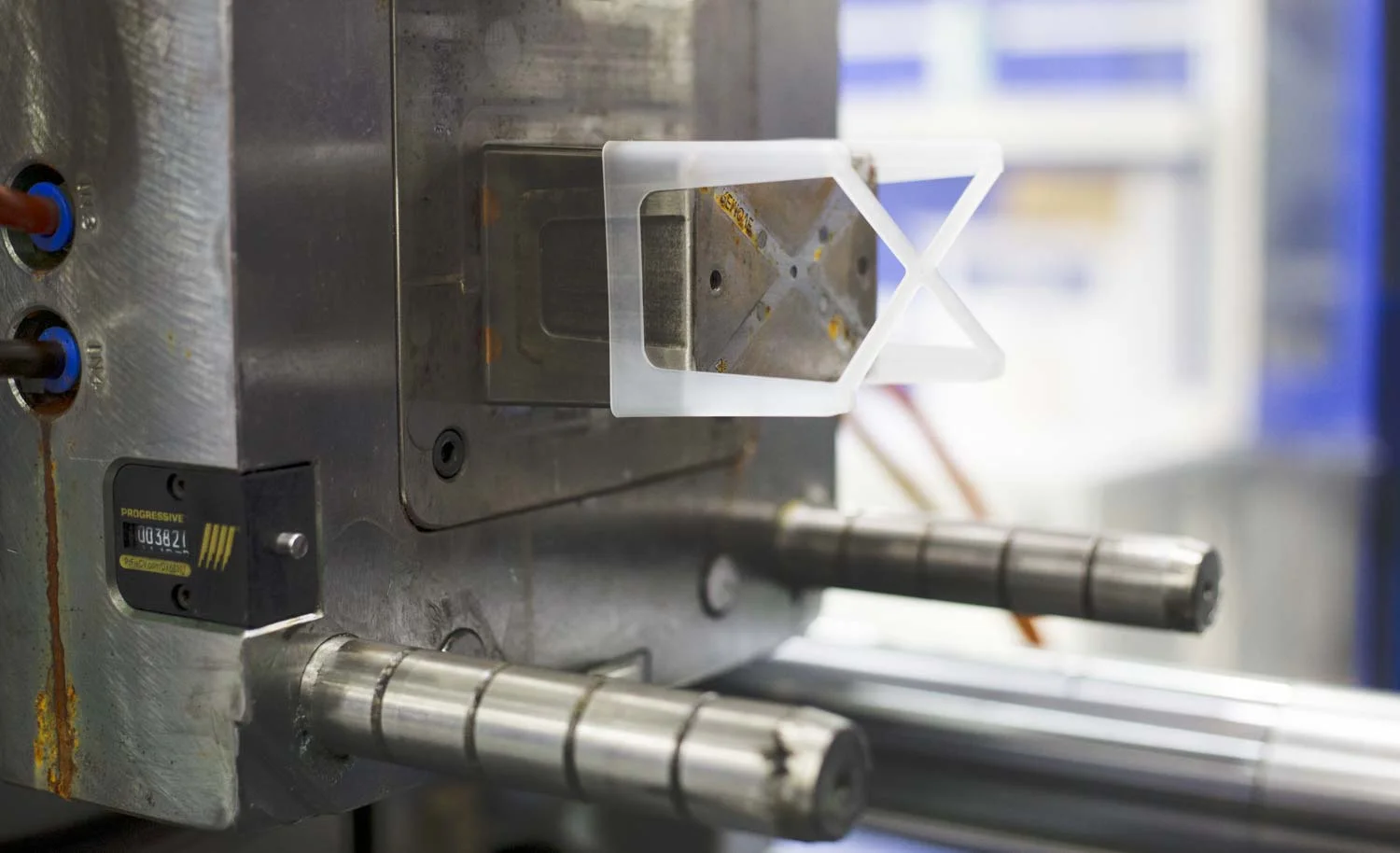
Injection Molding: A Closer Look
Injection molding uses thermoplastic resins, a mold, and a machine or press. Like urethane casting, this process has advantages and disadvantages.
Thermoplastic Resins
Thermoplastic resins soften to a liquid in high heat and then harden when cooled. There are hundreds of different thermoplastics available, and each have different end-use properties and processing requirements.
Most thermoplastic resins are supplied as pellets and are fed into a part of the injection molding machine called the hopper. These plastic pellets are melted inside a heated barrel with a rotating screw. This prepares the thermoplastic material for injection into the mold.
Steel vs. Aluminum Molds
Injection molds include a core and a cavity held together between metal plates and other mold components. The core is the raised, or convex, part of the mold. The cavity is the recessed, or concave, part of the mold filled with molten plastic.
Most injection molds are made of steel or aluminum. Steel is harder than aluminum, but some steels are harder than others. The reason that hardness is essential is because it affects tool life. Harder molds also support finer details and tighter tolerances.
Standalone Molds vs. MUD Inserts
Part designers can choose standalone molds that include the core, cavity, and all of the other tooling components that are required for injection molding. This includes the metal plates that provide a framework for mounting the mold within the machine.
MUD inserts, or master unit die (MUD) molds, are also an option. These universal frames fit into the injection molding press and hold a removable insert. MUD molds reduce tooling costs because only a removable core and cavity must be machined.
Injection Molding Machines
Injection molding machines work with heat and pressure. After the thermoplastic pellets are melted inside the heated barrel, the rotating screw pushes, or injects, molten material into the cavity of the mold, which remains clamped shut.
After injection, the molten plastic is held under pressure so that it flows and fills the mold completely. The thermoplastic material then cools and solidifies. The mold is opened, and the finished part is ejected with pins and, sometimes, additional mechanisms.
Advantages of Injection Molding
The advantages of injection molding begin with its support for low-volume and high-volume production. This means you can design parts for a single process from late-stage prototyping through initial production and then mass production.
Designers also like how injection molding supports a wide range of materials, including less expensive commodity plastics and more expensive specialty plastics and polymer blends. This versatility lets you select a material based on your specific application.
The ability to use the same material from prototyping through low-volume and high-volume production is also attractive, especially if you need samples made from the polymer you plan to use during production. This is often the case with medical devices and products.
Although injection molds cost more than the silicone molds used in urethane casting, hard tooling lasts longer and can produce thousands of parts before requiring repairs. Because injection molding is fast, parts production is also rapid – even at high volumes.
In addition, designers like the finer details, tighter tolerances, and wide range of surface finishes that injection molding can achieve. Injection molding can also support larger part sizes. Ultimately, the main size limitation is the size of the injection molding machine itself.
Finally, designers appreciate how injection molding generates less waste. If there are defective parts, a molder can regrind, melt, and reuse the material. In addition to reducing waste, this helps limit a project’s material costs.
Disadvantages of Injection Molding
The disadvantages of injection molding begin with tooling since hard molds cost more than soft ones. Even when MUD inserts are used, some metal machining is still required. This contributes to high startup costs and can make low-volume production cost-prohibitive.
Compared to urethane casting, injection molding also has longer lead times. Although injection molding produces parts quickly, hard tooling takes longer to make. Injection molds also require testing, which adds costs and extends project timelines.
Finally, injection molding has stricter design guidelines than urethane casting. Modifying the design of an injection molded part may also mean creating a new mold, which adds time and expenses to a project.
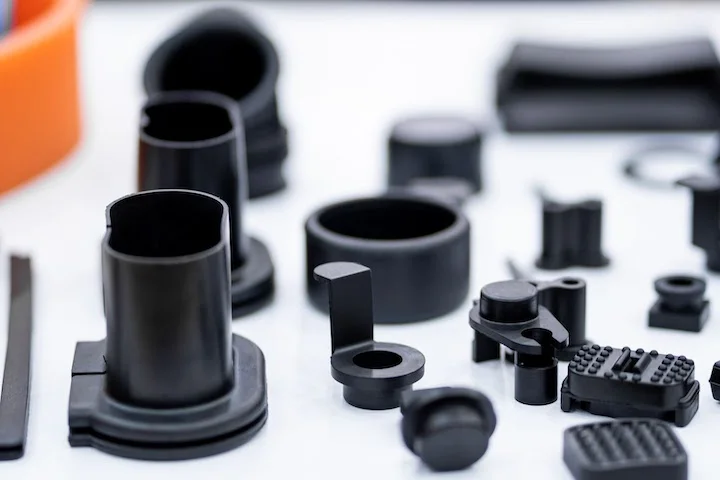
Urethane Casting vs Injection Molding: Key Considerations
Now that you know more about the differences between urethane casting and injection molding, what’s the right choice for your project? Remember to consider all of these factors.
- Applications
- Part Volumes
- Lead Times
- Costs
- Tolerances
- Wall Thicknesses
- Undercuts
- Materials
The following sections explain.
Applications
Injection molding can produce high volumes of parts, including components with tight tolerances. That makes it a good choice for automotive and aerospace parts, electronic components, and medical devices. Urethane casting is limited to lower part volumes, typically with less complexity.
Volumes
Injection molding supports a broader range of part volumes. Typically, urethane casting is used for quantities from 1 to 100 parts. By contrast, injection molding can produce part volumes from 100 to 100,000. Note, however, that high-volume injection molding requires hardened steel tooling, which is more expensive than the soft and semi-hardened steels in low-volume injection molds.
Lead Times
Urethane casting can produce part samples in just a few weeks. Silicone molds can be cast quickly, but urethane casting can’t mold many parts per day. With Fictiv, designers can get injection molded part samples in as little as two weeks, and from tooling made of soft or semi-hardened steel rather than aluminum.
Cost
Urethane casting’s tooling costs range from several hundred to several thousand dollars. The tools for injection molding are more expensive, even when MUD inserts are used. However, urethane casting’s per-part costs are higher because this pour-and-cast process is labor-intensive. By contrast, injection molding is machine-based and highly automated.
Tolerances
Urethane casting’s tolerances are typically +/-.010” for the first inch and +/-.005” for every subsequent inch. Injection molding offers tighter tolerances with +/-.005” for the first inch and +/-.002” for every subsequent inch. The relative softness or hardness of the mold material is the primary driver of these differences.
Wall Thicknesses
In both urethane casting and injection molding, maintaining a consistent wall thickness helps to ensure part-to-part consistency, stress distribution, and a reduced risk of defects. With injection molding, however, designers need to determine the minimum and maximum wall thickness for the specific injection molding material since different thermoplastics shrink at different rates. Urethane casting is more forgiving, but it has a similar range of wall thicknesses (1 to 5 mm).
Undercuts
Undercuts are protrusions or indentations in a part that can complicate its removal from a mold. Because urethane casting uses flexible silicone molds, it’s possible to slightly stretch or bend the tool to release a part with undercuts. That’s not the case with the hard tools in injection molding. Injection molding can support undercuts, but using ejection mechanisms (such as lifters and sliders) adds costs.
Materials
Urethane casting is limited to polyurethanes, polymers that can’t match the characteristics of some injection molded plastics. However, both molding processes support the use of materials with FDA-approved formulas. They also support the use of color matching and textured finishes.
Get the Molded Parts You Need
Like all manufacturing processes, urethane casting and injection molding have pros and cons. Fictiv is staffed with engineering experts who can recommend the right process. We also work with a carefully vetted network of manufacturing partners and offer both molding services.
No matter what you decide, you’ll get design for manufacturing feedback along with your quote.Are you ready to get started? Create your free Fictiv account and upload your part drawing.