Time to read: 5 min
Injection molding undercuts are part features that can complicate or prevent the release of injection molded parts. Examples include indentations such as side holes, vents, or slots, and protrusions such as screw threads, snaps, or latches. Often, part features like these are found in consumer electronics, automotive, and medical products.
Undercuts support design complexity, but complexity adds costs to injection molding. Consider the example of a simple straight-pull mold. An undercut that interferes with the separation of the core and cavity may require the use of a slider, lifter, or hand-loaded insert to release the part. Each of these devices adds costs to your project.For part designers, it’s worth eliminating unnecessary undercuts. Yet, it’s also important to optimize your design so that necessary undercuts are easier, and therefore more cost-effective to produce. Fictiv provides design for manufacturability (DFM) feedback that includes design solutions for undercuts and advice about undercut best practices. The process begins when you request an injection molding quote, so create a Fictiv account to get started.
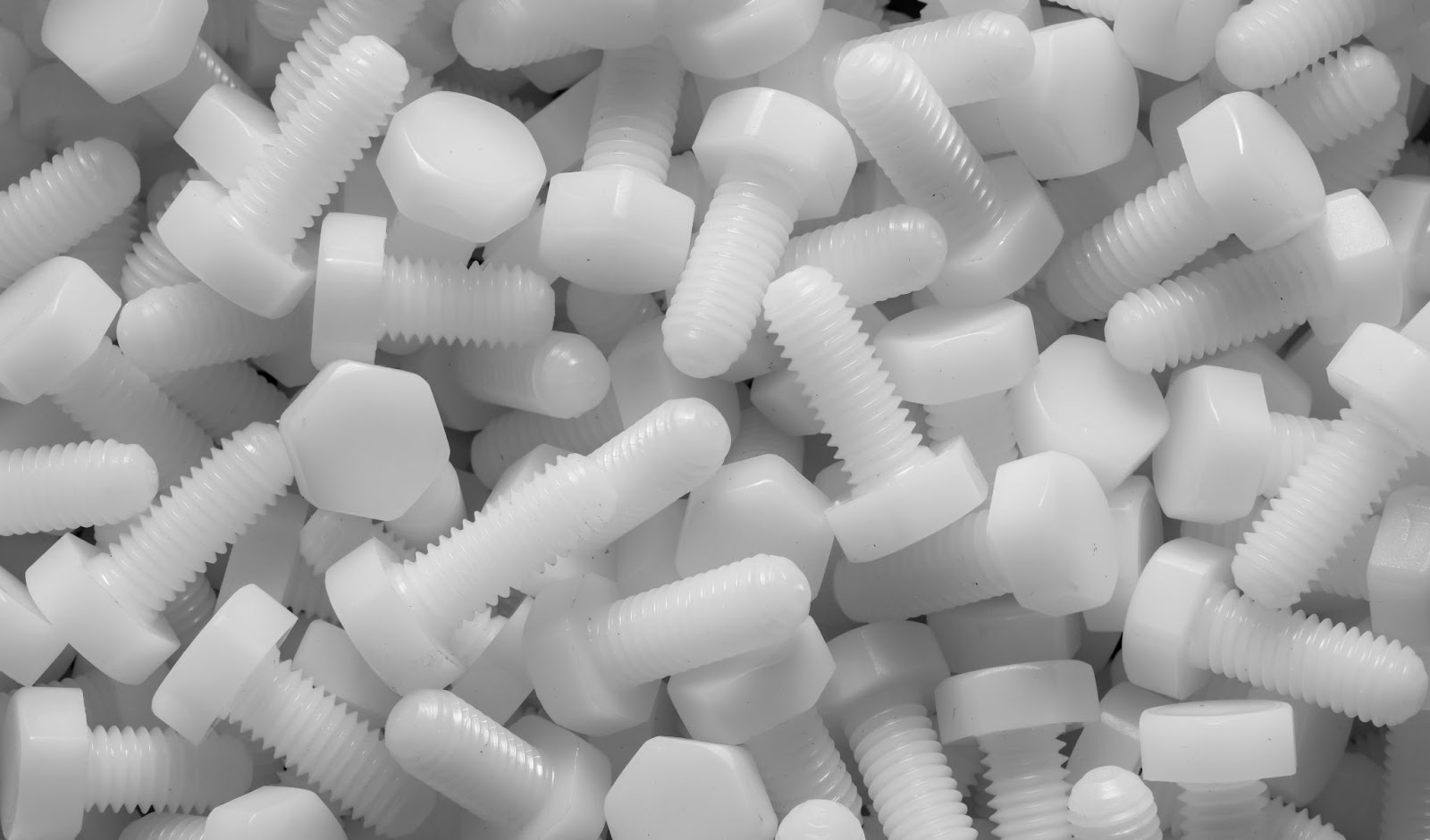
Why are undercuts used in injection molding?
Injection molding undercuts increase complexity and cost, but they can also support and enhance functionality. From product assembly to fluid flow, and from wire management to user convenience, undercuts are used to create part features such as:
- Threads for plastic fasteners
- Interlocks for clam-shell housings
- Conduits in barbed hose fittings
- Slots for buttons on smartphone cases
- Outlets for plastic hydraulic manifolds
- Locking tabs for automotive taillights
- Holes for wire or cable pass-throughs
Undercuts are also used for coring, the process of eliminating plastic material from thick sections to avoid longer cooling times and minimize the risk of sink marks and warping. Coring reduces material usage and weight, and also creates ribs and distinct walls that can support parts mating within a larger assembly. Coring can also be used to create angled supports around injection molded bosses that provide channels for screws.
Often, undercuts are used to produce valuable design elements like:
- Interlocking features such as snaps and latches that replace metal fasteners
- Side holes that provide access to ports or buttons inside enclosures
- Barbed fittings that control airflow and create a seal between a tube and fitting
- Vertical threads that secure connections, withstand stress, and bear light loads
If your part design includes essential undercuts, Fictiv’s DFM feedback can share undercut best practices so that it’s as simple and cost-effective as possible to manufacture your parts. Undercuts always increase complexity, however, and design solutions for essential undercuts vary. If an undercut is non-essential, Fictiv can also share alternative design solutions for undercuts as part of our expert DFM feedback.
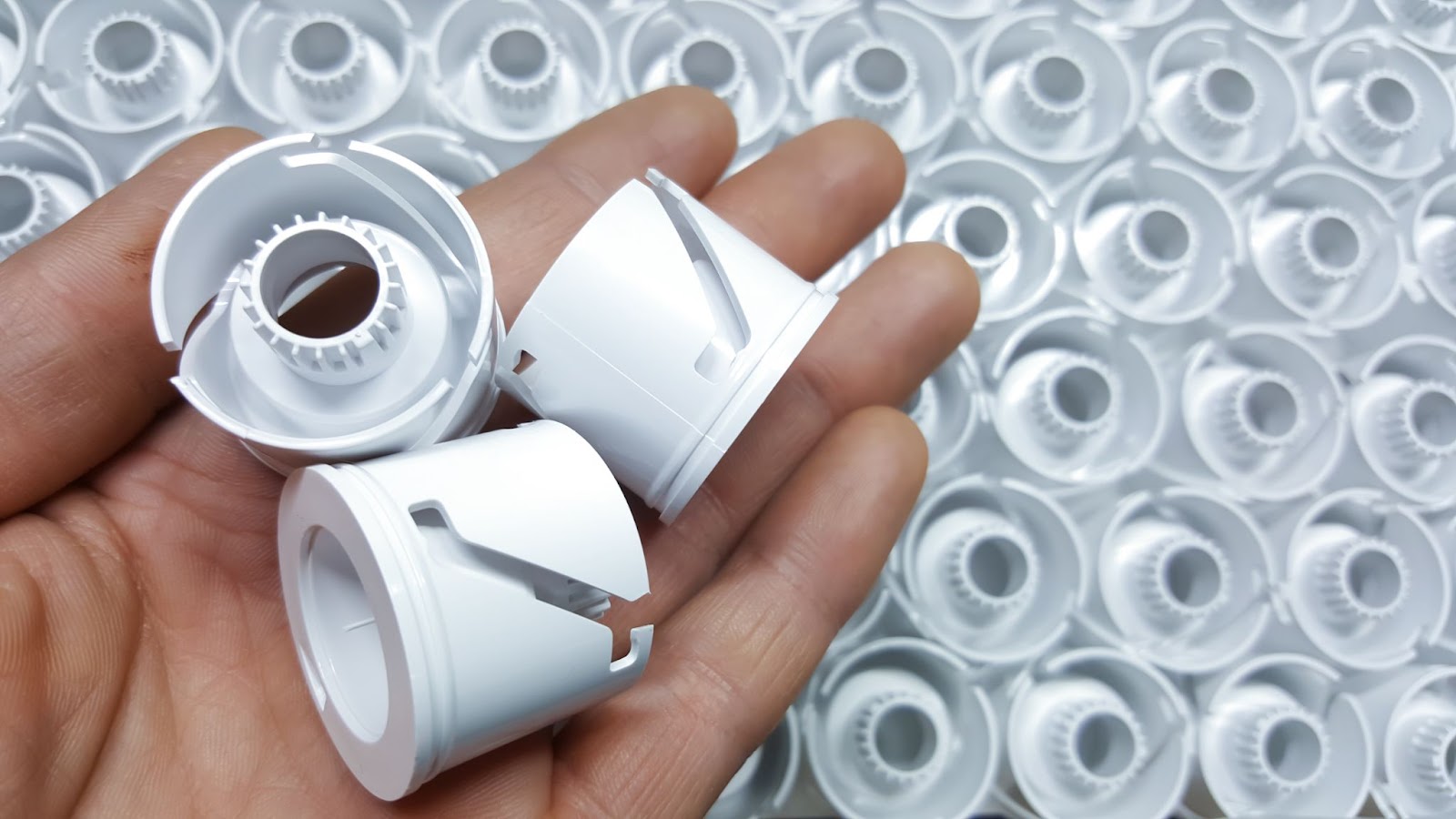
How to use undercuts successfully in injection molded parts
There are many ways to mold parts with undercuts, including:
- Parting line adjustment
- Side actions
- Bump-offs
- Sliding shut-offs
- Hand-loaded inserts
- Secondary operations
The best solution for each part varies and is a function of part design, geometry, material selection, production volume, and other factors (including cost). As part of the DFM feedback we provide, Fictiv can help you to choose the right approach for essential undercuts.
Parting Line Adjustment
The parting line is where the two halves of an injection mold separate to release the part. This line can be down the middle of the part, but that’s not always the case because of part geometry and material flow. Moving the mold’s parting line to intersect with the undercut is sometimes the easiest part-release solution, but injection molded parts still need enough draft, or taper, to avoid scraping during ejection.
Side Actions
Side actions are used with cylindrical components where the mold separates horizontally along the part. Cam pin slides are the most common type of side action and have an angled pin that withdraws from a sliding body after the part cools. Side actions allow undercuts to be ejected freely, but they tend to work better with plastic materials that won’t stick when the pin retracts.
Bump-offs
Injection molding bump-offs allow a part to deform just enough to exit the mold, but without experiencing damage or wear. The leading edge of the undercut needs to have a smooth radius — otherwise, the plastic part can get stuck during release. Although some injection molding materials aren’t compressible enough to support bump-offs, plastic resins like polyethylene and TPE are good candidates.
Sliding Shutoffs
Sliding shutoffs, or telescoping shutoffs, can be used to create holes in injection molded parts. A “telescope” is machined into one half of the mold and extends into the other half so that as molten plastic enters, certain part regions are shut-off. Both the part and the mold require sufficient draft, so for best results, add a minimum of three degrees to the top side or vertical.
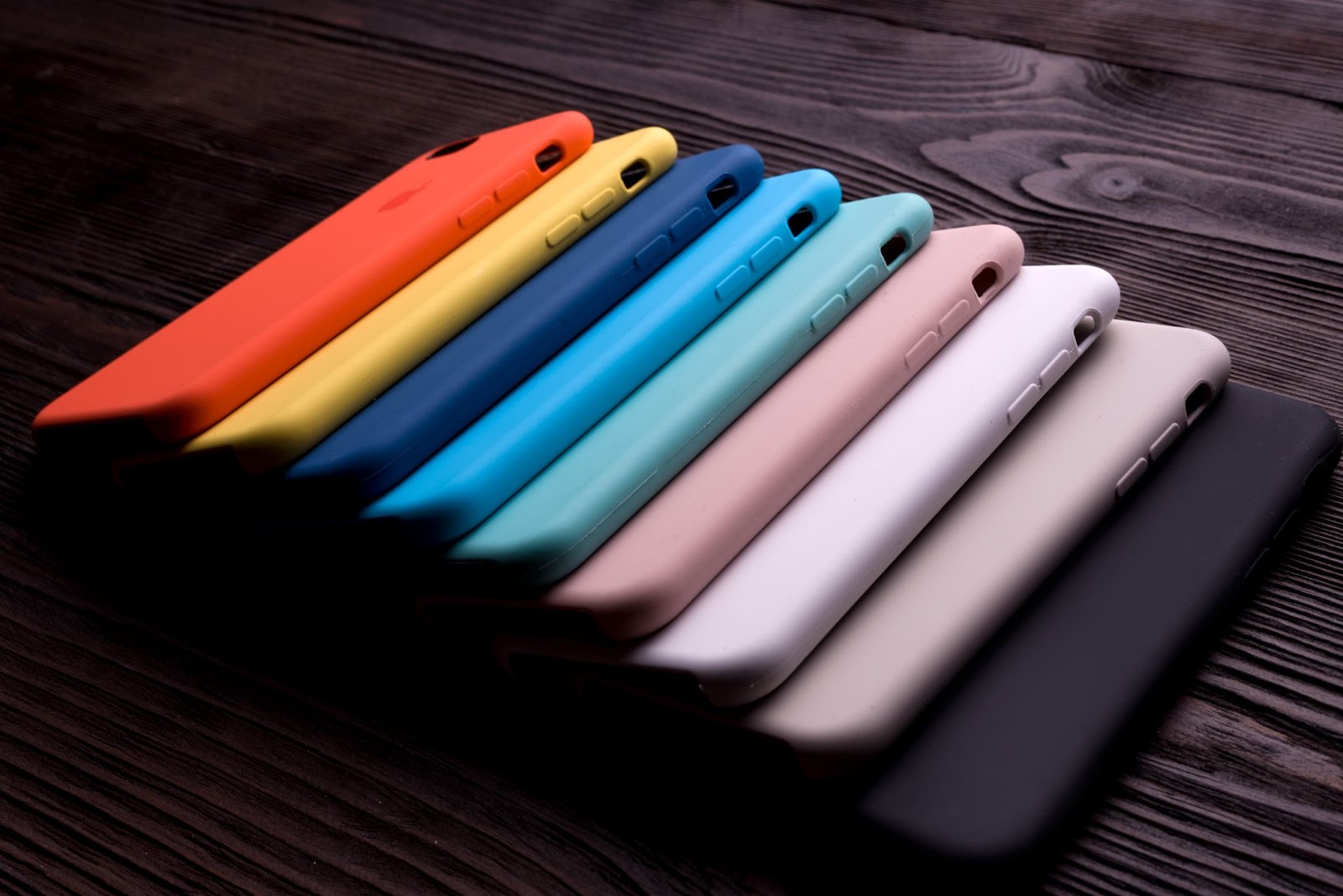
Hand Loaded Inserts
Hand loads, or hand-load inserts, are another way to release undercuts. Unlike sliders or lifters, handloads aren’t automated devices. Instead, these inserts are placed manually into a mold before the cavity is filled. This hand-loaded piece is ejected with the finished part and removed so it can be reinserted during the next injection molding cycle. Generally, hand-load inserts are used for lower part volumes because they cost less than automated mechanisms.
Secondary Operations
Secondary operations don’t require changes to a mold or its features but can also support the use of injection molding undercuts. For example, instead of using sliding shut-offs to create a hole in a part, a finished component can be put into a drill press or milling machine instead. Sometimes, a secondary operation is the most cost-effective solution for prototyping or very low production quantities.
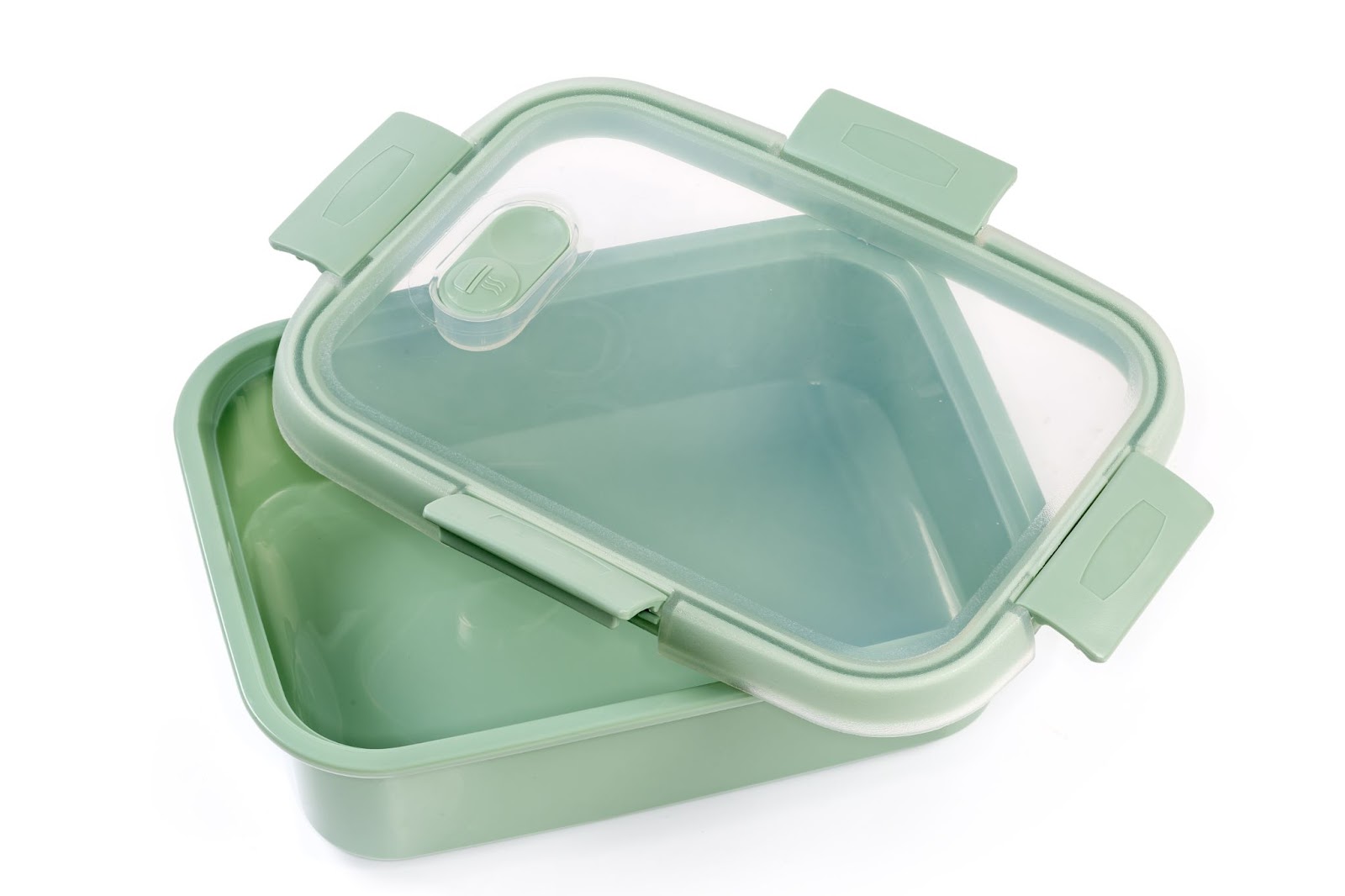
Get a Quote and Get DFM Feedback for Undercuts
Fictiv provides designers with DFM feedback about undercuts and other challenging part features. Regardless of your order quantity, we can help you to reduce costs and shorten timelines. So, whether you need help with essential undercuts or assistance with eliminating unnecessary ones, Fictiv is the right choice. As your operating system for custom manufacturing, Fictiv has the resources, know-how, and manufacturing network to make your next injection molding project a success. Learn more about our injection molding services and create an account to get a quote today.