Time to read: 6 min
Overmolding is a manufacturing process that molds a polymer over a substrate. It eliminates the need for parts assembly after molding, and allows designers to leverage the individual properties of multiple materials. Plastic overmolding is used to produce the handles on metal-bladed screwdrivers, but can also be used in products that don’t contain any metal parts at all. In medical applications, for example, silicone or thermoplastic elastomers (TPE) can be overmolded onto thermoplastic substrates.
For part designers, it’s important to select overmold and substrate materials that bond well together because overmolding isn’t just about layering one material on top of the other. Whether the bonds are chemical or mechanical, the materials must remain securely connected. Part designers also must understand the purpose of the overmold design. For example, adding grip and comfort to a handle made of a strong and impact resistant substrate material that’s otherwise slippery and uncomfortable to hold.
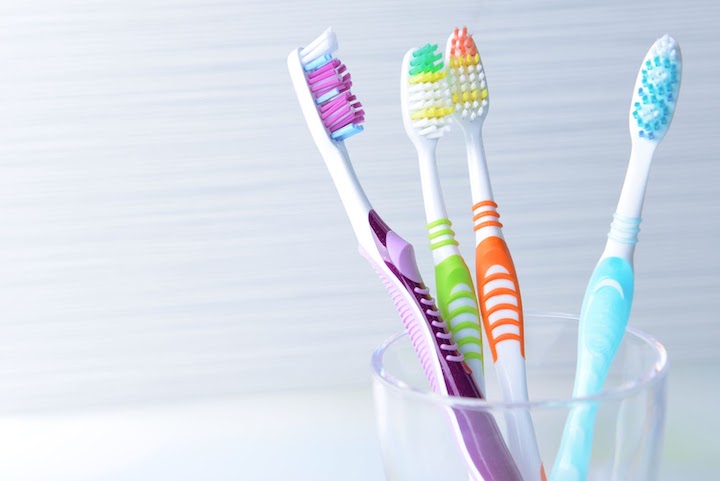
Toothbrushes are an example of plastic overmolding.
Selecting overmold and substrate materials that meet an application’s requirements is essential, but part features such as undercuts and surface finish can also support overmolding success. Additionally, designers must determine whether to use two-shot molding or pick-and-place molding. Just like the materials you can select and the features you can incorporate, each overmolding process has its advantages, disadvantages, and tradeoffs.Fictiv helps with this decision-making process through our expert design for manufacturing (DFM) feedback. You won’t have to wait until tools are cut (and costs incurred), and you’ll receive DFM feedback right when you receive our response to your request for a quote. Keep reading to learn more about overmolding part design or create a Fictiv account to start your next injection molding project with us.
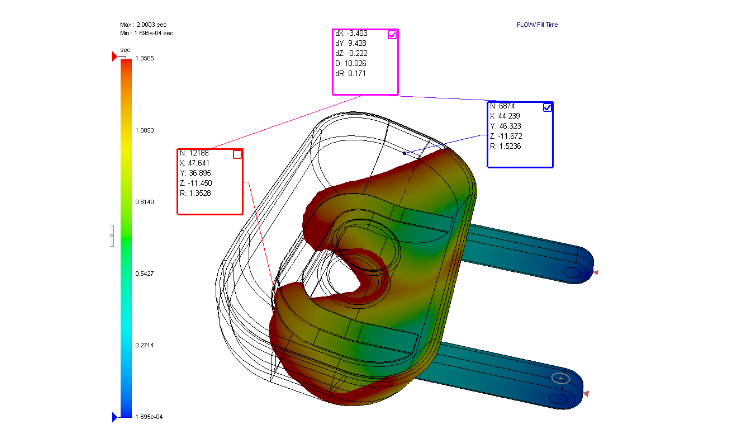
CAD software can support overmolding part design. Image Credit: Solidworks
Material Selection and Chemical vs. Mechanical Bonds
Plastic overmolding can bond two different thermoplastics together. Depending on your application’s requirements, these materials can include common injection molding plastics or specialty plastics and polymer blends. The substrate and overmold can be different polymers or different versions of the same material. For example, a medical device may use a clear polycarbonate lens as the substrate and a tinted polycarbonate housing as the overmold.
Overmold materials also include thermoplastic elastomers (TPEs), which are rubber-like compounds that are processed like thermoplastics. Thermoplastic rubber (TPR), as this category is also known, can be further divided into subcategories that include thermoplastic vulcanizates (TPVs), thermoplastic copolyesters (TPC), and thermoplastic polyurethanes (TPUs). These softer and more flexible materials can overmold harder plastics such as acrylonitrile butadiene styrene (ABS), polypropylene (PP), or polycarbonate (PC).
The table below contains some examples of specific brands of TPEs, including TPC, TPV, and TPU materials. The letter C indicates that the overmolding bonds are chemical and the letter M indicates when the bonds are mechanical. Chemical and mechanical bonding are not mutually exclusive, however, and can complement each other.
Substrate Material | |||
Overmold Material | ABS | PC | PP |
TPE – Versaflex | C | C | C |
TPC – Hytrel | C | C | M |
TPV – Santoprene | M | M | C |
TPU – Texin | C | C | M |
Table 1: Overmold materials, substrate materials, and bond types
Chemical Bonding
Chemical bonds occur at the molecular level and are a function of how well the overmold material wets the substrate. Wetting refers to the ease with which the overmold contacts the substrate’s surface and spreads out. Without a high enough surface energy, it’s more difficult for the substrate to attract the overmold material so that it spreads evenly (like a glass of spilled milk) instead of as droplets (like beads of water on a freshly waxed car).
The table below shows the surface energy in dynes/cm for some common injection molding materials. These values are typical and may vary with specific formulations, depending on additives and fillers.
Plastic Material | Surface Energy |
nylon 6/6 | 46 |
polycarbonate (PC) | 46 |
polyvinyl chloride (PVC) | 39 |
acrylic (PMMA) | 39 |
acrylonitrile butadiene styrene (ABS) | 35 |
polyethylene (PE) | 30 |
polypropylene (PP) | 30 |
polystyrene (PS) | 34 |
polyethylene (PE) | 30 |
polypropylene (PP) | 30 |
Table 2: Surface energy for some common injection molding materials
As a general rule, the surface energy of the substrate needs to exceed that of the overmold material. Because thermoplastic elastomers have relatively low surface energy, they can readily overmold most of the plastics in the table above. By contrast, silicones have relatively high surface energy and are more difficult (though not impossible) to overmold onto thermoplastic substrates.
With especially challenging material combinations, a substrate may require flame, corona discharge, or plasma treatment to increase the substrate’s surface energy. These surface treatments improve wettability, but they can also result in higher material costs. Alternatively, or in addition to chemical bonding, part designers can incorporate part features called undercuts. Examples include indentations — such as side holes, vents, and slots — and protrusions like screw threads, snaps, and latches.
Mechanical Bonding
Mechanical bonding depends on the physical geometry at the interface of the substrate and the overmold. Consider the example of a substrate with holes that are wider at the bottom for a dovetail effect. When the overmolding material flows into these undercuts, it cools and locks into place. Mechanical bonding can also be achieved by increasing the interface’s surface area with grooves or bosses. If the substrate is a porous material, then it already contains tiny holes into which the overmold can flow.
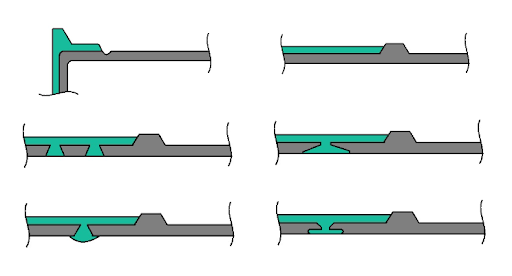
This diagram shows several examples of interlocks.
Wrapping the overmolded material around the substrate also supports mechanical bonding. Using a rougher surface finish rather than a smooth, polished one helps, too. No matter which bonding technique you choose, make sure that the edges of the overmolded material are not exposed. Otherwise, peeling may occur. The proper part design will ensure that the edges are covered, but it’s also important to work with an experienced injection molder. Fictiv vets all of our manufacturing partners carefully so that you can get perfect plastic prototypes and low, medium, or high production volumes as needed.
Two-Shot Molding vs. Pick-and-Place Molding
Chemical and mechanical bonding are important, but so is your choice of an overmolding process: two-shot molding or pick-and-place molding.
Two-Shot Molding
Two-shot molding, or double-shot molding, is a two-step continuous process that first molds a substrate, then overmolds that substrate with a different material. The entire process uses a single mold and is fully automated. In other words, an injection molding machine with multiple barrels shoots two different resins into the same mold. Because the tooling is more expensive, two-shot molding is generally used for high-volume production runs of 10,000 parts or more.
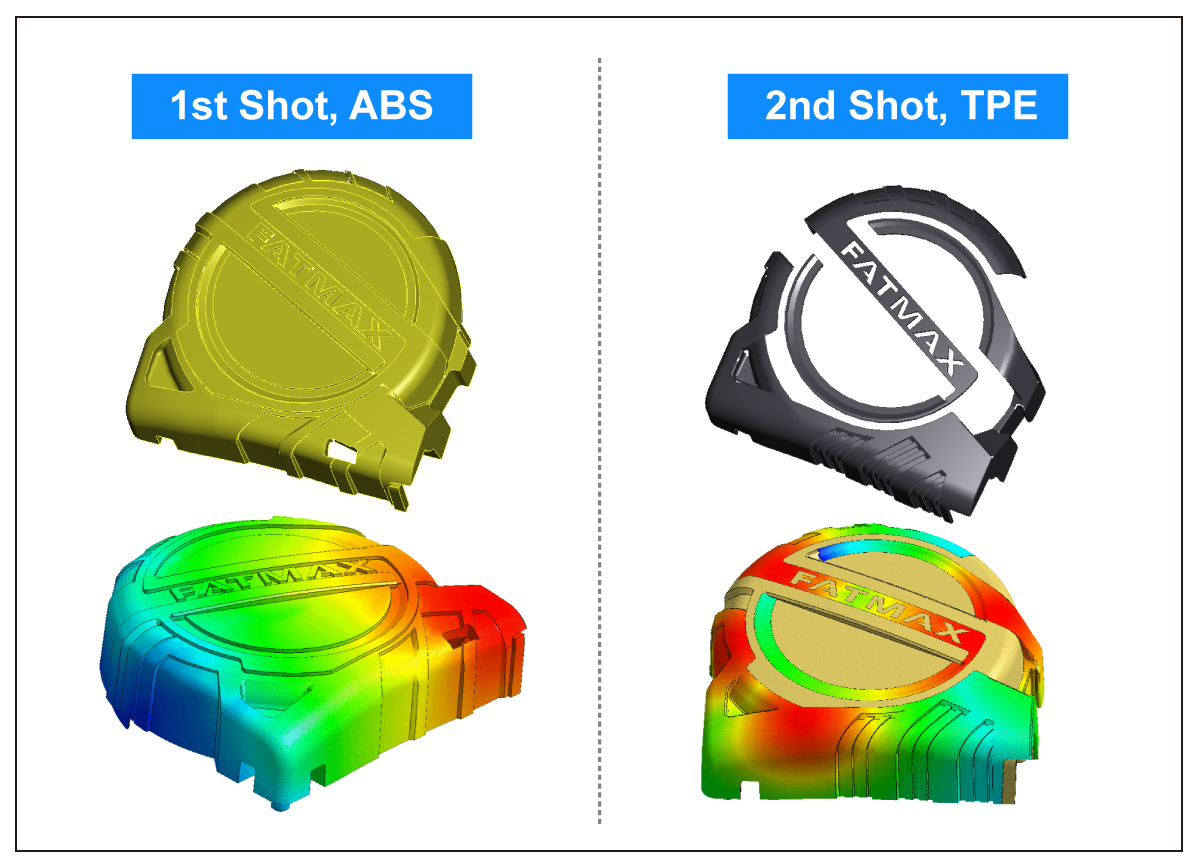
Mold filling analysis was used to produce this two-shot molded part. Image Credit: Moldex3D
Pick-and-Place Molding
Pick-and-place molding is used mainly for prototyping and for low-volume production of fewer than 10,000 parts. This overmolding process uses two molds, but the tooling is less complex and therefore less expensive. During pick-and-place molding, the first mold is used to produce the substrate part. This can be done individually (via manual overmolding) or in batches. Then, a worker places the substrate part or parts into the second mold. Resin is then injected onto the substrates to produce the finished parts.
The table below compares these two processes.
Two-Shot Molding | Pick-and-Place Molding | |
Automation level | Fully automated | Manual work required |
Number of molds | One mold | Two molds |
Tooling costs | More expensive | Less expensive |
Cost-effective for prototyping | No | Yes |
Cost-effective for production | High (>10,000 parts) | Low (<10,000 parts) |
Table 3: Two-shot molding vs. pick and place molding
Get Help with Overmolding Part Design
Do you need help with part design for overmolding? Whether you’re overmolding silicone or nylon, evaluating surface energy and bond strength, or considering design features such as undercuts and rougher surface finishes, Fictiv provides the kind of DFM feedback you need.
Sourcing Simplified – Start Your Next Project With Fictiv
For all your injection molding needs, Fictiv has you covered. Our injection molding experts are well-versed in overmolding and can help dial in your designs to get great results. We produce custom mechanical parts in a variety of materials and we simplify part sourcing with intelligent, streamlined, automated workflows. Fictiv is your operating system for custom manufacturing that makes part procurement faster, easier, and more efficient. If you need assistance dialing in your tolerances or selecting the proper materials for your next project, create an account and upload your designs today. We’re here to help, so discover what our instant quote process, design for manufacturability feedback, and intelligent platform can do for you.