Time to read: 6 min
PVC injection molding is a manufacturing process for producing parts from polyvinyl chloride (PVC), one of the world’s most commonly used plastics. PVC does not absorb moisture and has good chemical resistance. Although it’s not recommended for high-temperature applications, PVC is considered to be flame-resistant because it’s self-extinguishing.
There are two main types of PVC: flexible and rigid. Flexible PVC contains plasticizers, chemicals that impart greater elasticity. Flexible PVC is also softer and more supple than rigid PVC, which is extremely dense for plastic and both hard and impact-resistant. Rigid PVC comes in both unplasticized (PVC-U) and modified (PVC-M) grades.
If you’re considering PVC injection molding for your next project, keep reading to learn more about this commodity plastic, including:
- Advantages of PVC
- Disadvantages of PVC
- PVC Injection Molding Applications
- Properties of Injection Molded PVC
- Design Guidelines for PVC Injection Molding
- PVC Processing Guidelines
- Potential Alternatives to PVC Plastic
- Succeeding with PVC Injection Molding
Then, create a free Fictiv account and upload your part drawing. Along with design for manufacturing (DFM) assistance from our engineering experts, you’ll gain access to our carefully vetted network of manufacturing partners. Why search for a PVC injection molder on your own when you can get expert DFM feedback and leverage the power of Fictiv?
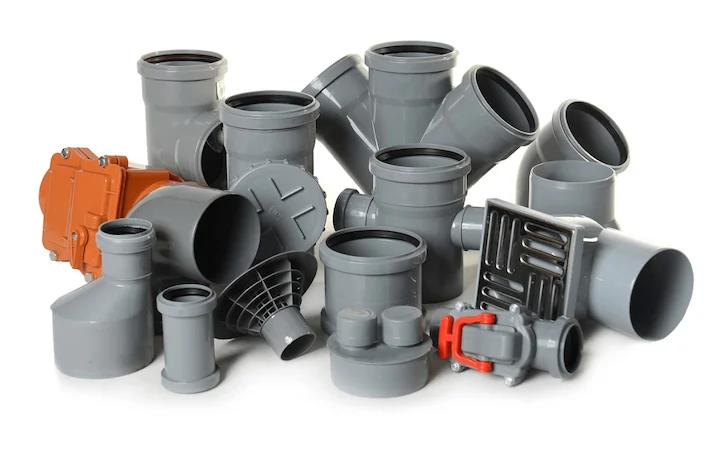
Advantages of PVC
Injection-molded PVC provides important advantages.
Cost-Effective
PVC is a commonly used injection molding material that is less expensive than specialty plastics and polymer blends. PVC pellets are also available in lower minimum order quantities (MOQs) than specialized materials.
Chemical Resistant
PVC is chemically resistant to many acids, bases, salts, fats, and alcohols. It also resists diesel fuel and nitric acid (<70% concentration). Strong concentrated acids at temperatures higher than 60°C can damage injection molded PVC, however.
Electrical Insulator
PVC behaves as an electrical insulator because of its dielectric strength, which is measured as the maximum voltage required to produce a dielectric breakdown through a material. Because PVC is also flame and water-resistant, this injection molded plastic is a good choice for electrical applications like equipment housings.
Disadvantages of PVC
Despite its advantages, PVC has some disadvantages that part designers need to consider.
Poor Heat Stability
PVC can resist temperatures up to 60°C but begins to degrade when it’s exposed to high heat. When it’s overheated, injection molded PVC can decompose into harmful by-products like hydrochloric acid (HCL), a highly corrosive chemical.
Low Heat Deflection Temperature
PVC has a relatively low heat deflection temperature. Temperatures higher than 82°C cause injection molded PVC to deform under load. Consequently, PVC is unsuitable for some load-bearing applications
Loss of Strength
Flexible PVC can experience a significant reduction in material properties over time. Rigid PVC that lacks resistance to ultraviolet (UV) light is also subject to material degradation. Painting can add a protective coating to PVC parts, but clear PVC may yellow with long-term exposure to the sun.
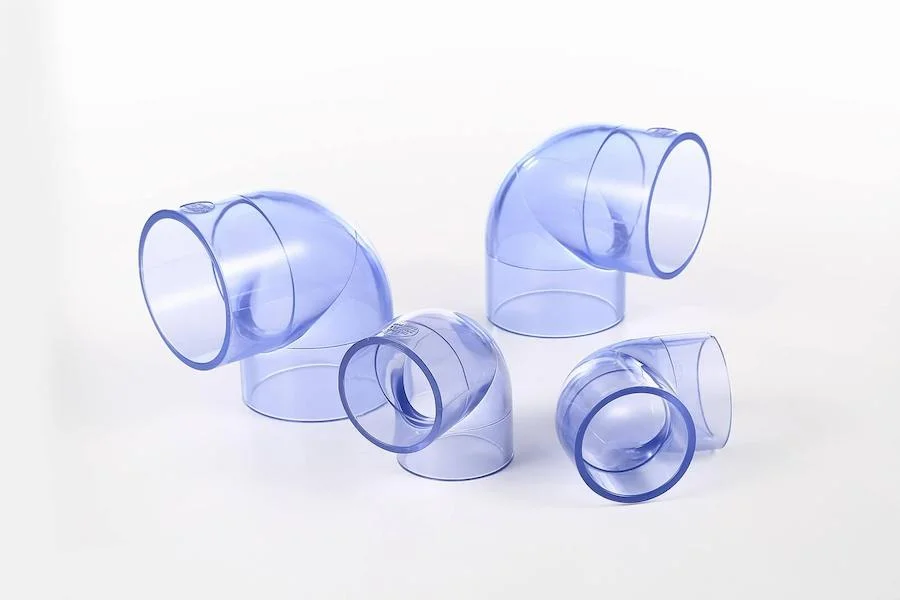
PVC Injection Molding Applications
Injection molded PVC is used by the healthcare, building and construction, and consumer goods industries.
Healthcare Applications
- Medical tubing
- Anesthesia masks
- Oxygen masks
- Catheters
Building and Construction Applications
- Pipes
- Valves
- Window profiles
- Gutters
Consumer Goods
- Handles
- Enclosures
- Furniture
- Light shades
Properties of Injection Molded PVC
The table below contains typical physical, mechanical, and electrical properties of injection-molded PVC.
Physical | Density (g/cm3) | 1.16 to 1.65 |
Linear Shrinkage (cm) | 0.000500 to 0.0120 | |
Mechanical | Tensile Strength at Yield (MPa) | 3.45 to 73.1 |
Elongation at break (%) | 2 to 330 | |
Flexural Modulus (GPa) | 0.220 to 6.43 | |
Flexural Yield Strength (MPa) | 50.7 to 104 | |
Electrical | Dielectric Constant | 2.98 to 8.00 |
Table 1: Properties of PVC
Design Guidelines for PVC Injection Molding
PVC parts that are poorly designed are more prone to injection molding defects. When you work with Fictiv, however, you’ll get DFM feedback that can help minimize risk. To learn about part design, download our free “Injection Molding Design Guide” to use as a reference.
Download the Injection Molding Design Guide
The following sections examine injection molding design considerations for PVC parts.
Wall Thickness
Whenever possible, apply a uniform wall thickness throughout your part. If you need to use a greater thickness in some areas, make a gradual transition from thinner to thicker sections. Do not use transitions that are greater than 10% to 15% of the nominal wall thickness. Generally, the recommended minimum wall thickness for injection-molded PVC ranges between 1.27 and 6 mm.
Shrinkage
Injection molded parts shrink as they cool. Compared to other plastics, PVC has a relatively low shrinkage rate (0.2% to 0.5%). The exact percentage depends on the grade of PVC that you select, as well as the specific processing conditions. If parts shrink unevenly during cooling, warping may occur. To limit the risk of defects, reduce the wall thickness and the size of the mold gate area.
Radii
Sharp corners are difficult to injection mold. They’re also more prone to stress concentrations that can result in part failure. Apply radii to the inside and outside corners of your injection molded PVC part, and make the radii at least 25% of the wall thickness. For maximum part strength, apply a radius equal to 75% of the wall thickness.
Draft Angle
Draft is an angle or taper that you apply to the vertical walls of parts so that they eject cleanly from the injection mold. Design your PVC parts with draft angles between 0.5% and 1%. The larger the part length, the larger the draft angle. Using molds with polished surfaces can also make part ejection easier.
Part Tolerance
Tolerances are acceptable variations in size for overall dimensions and part features. As a rule, parts with tighter or finer tolerances are more expensive because they have stricter injection mold and processing requirements.
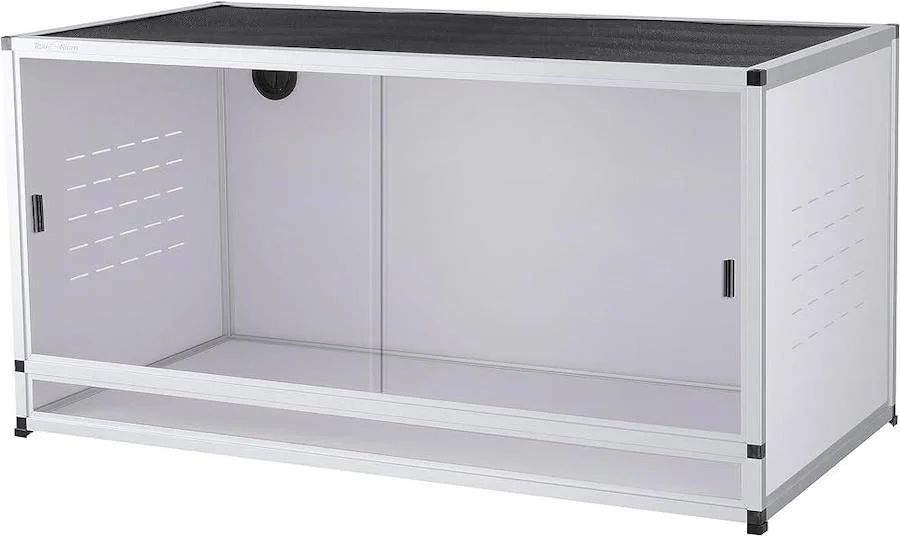
PVC Processing Guidelines
Adherence to PVC processing guidelines is beyond a part designer’s immediate control. Therefore, it’s important to work with an experienced PVC injection molder. The following processing parameters are especially important.
Moisture
PVC does not readily absorb moisture; however, small amounts of moisture can collect on pellet surfaces. Unless this moisture is removed, PVC parts may exhibit cosmetic defects. In general, an injector molder needs to dry PVC to a moisture content of 0.3% at a temperature between 24 and 32°C.
Temperature Control
PVC pellets are melted at temperatures as high as 195°C, but the exact temperature depends on the specific grade. Accurate temperature control is important because excessively high temperatures will result in severe material degradation. Typically, mold temperatures are kept between 20°C and 60°C.
Injection Pressure
The optimum injection pressure depends on several factors, including part design and PVC grade. For best results, injection molders need to maintain pressures between 20 and 40% of the maximum allowable injection pressure. Generally, a back pressure of between 0.4 and 0.7 MPa is used.
Injection Speed
To avoid surface defects, molders need to inject PVC at moderate speeds. Note, however, that speeds vary with part geometry. For example, thicker parts should be filled more slowly than thinner parts.
Potential Alternatives to PVC Plastic
PVC might not be the best material for your application. If that’s the case, you could consider HDPE or PP plastic instead. Fictiv’s injection molding services work with both of these materials.
HDPE
HDPE injection molding uses high-density polyethylene (HDPE), a cost-effective thermoplastic with good tensile strength and high impact resistance. This commodity plastic also has strong moisture resistance and is relatively easy to mold.
PP
Polypropylene injection molding uses a commodity thermoplastic (PP) with excellent resistance to moisture, good fatigue strength, and a low coefficient of friction. Polypropylene is also recyclable and provides chemical resistance.
Succeeding With PVC Injection Molding
PVC is a cost-effective injection molding material with attractive material properties, but a manufacturing-ready design and a skilled production partner are critical. Fictiv has the engineering experts and manufacturing network you need to get quality parts fast. From prototyping through production, we’re here to help you succeed.
Create your free Fictiv account and request an injection molding quote today — we mold complex parts at ridiculous speeds!