Time to read: 5 min
What does the word “production” mean to you? An engineer at a large consumer goods company might think of multi-cavity injection molding tools that cast parts day and night, and assembly lines that run multiple shifts. On the other hand, an engineer that works at a medical equipment company might think about getting a few cast urethane tools made. Production volumes vary greatly by industry and product and there’s no one-size-fits-all approach.
Since Fictiv’s platform hosts hundreds of different machines and materials across a range of fabrication technologies, we spend a lot of time researching and vetting production technologies to deliver the best value for our customers and help them to scale efficiently from prototyping to production.
In this 2-part series, we’ll share our point of view on best practices, as well as technology recommendations, for manufacturing at different volumes. This article will focus on manufacturing at low volumes of 10 – 100 units and in the next article we’ll cover best practices for manufacturing 100 – 1000 units and 1000 – 10,000 units. Be sure to subscribe so you don’t miss a post!
Best Practices for Manufacturing 10 – 100 Units
Two common use cases for manufacturing 10-100 units are:
- Field testing units, prior to a large production run
- Small-batch, made-to-engineer products
These use cases often have cosmetic and durability requirements that cannot be satisfied with common 3D printing technologies, like FDM and Polyjet.
Many consumer hardware startups make 50 to 100 looks-like, works-like prototypes for beta testing in the field, which is an excellent way to validate your design before heading into volume production.
At 10-100 units, the toughest part can be outsourcing assembly. Therefore, most companies assemble in-house or get on-demand temporary contractors to help out. We recommend you keep the assembly process simple, create crystal clear work instructions, and avoid specialized assembly processes, such as ultrasonic welding.
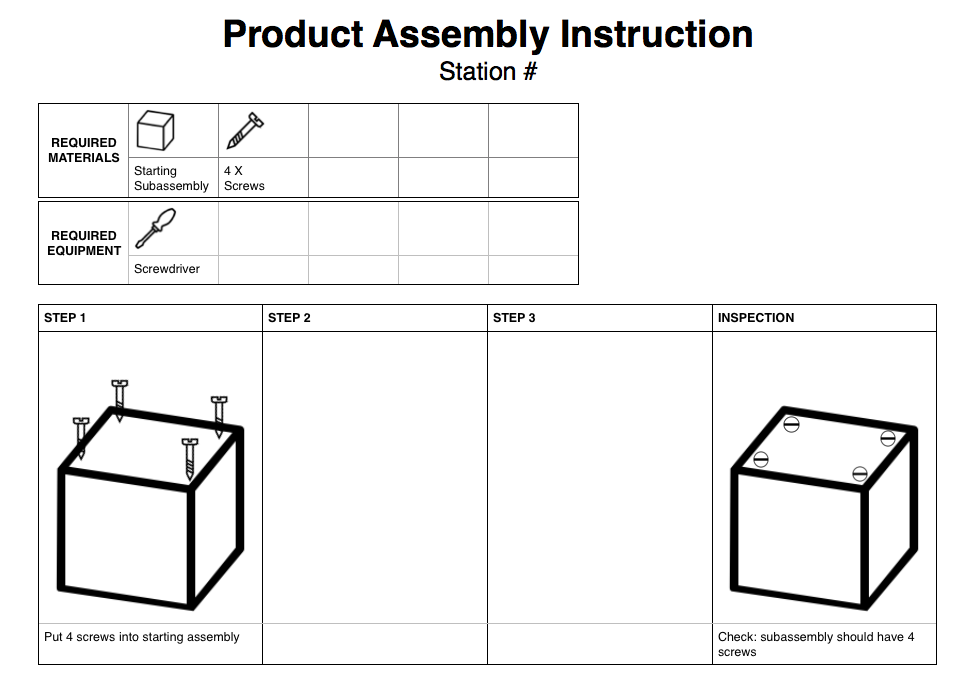
Check out our article on Secrets from a Factory Assembly Line for more tips and best practices here.
Selective Laser Sintering (SLS) 3D Printing for Manufacturing 10 – 100 Units
In the additive space, SLS 3D printing is a great choice for low-volume production, due to large build volumes and relative ease of cleaning. Beyond 100 units, SLS can still be a good option for producing small, complex internal components. One of the most interesting production applications of SLS Nylon that we’ve seen is designer eyewear:
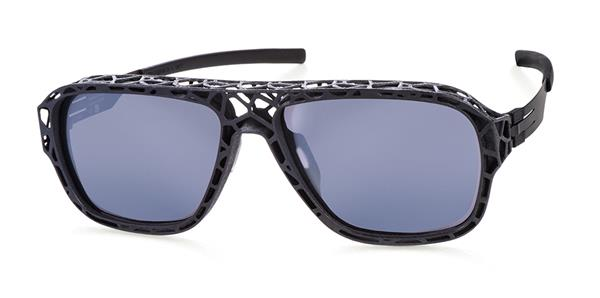
Materials for SLS 3D Printing
The most common plastic for SLS 3D printing is Nylon 12, but glass or carbon fibers can be added for additional strength (contact us for a custom quote here). These specialized material combinations are best suited for production volumes, due to material waste per batch of prints.
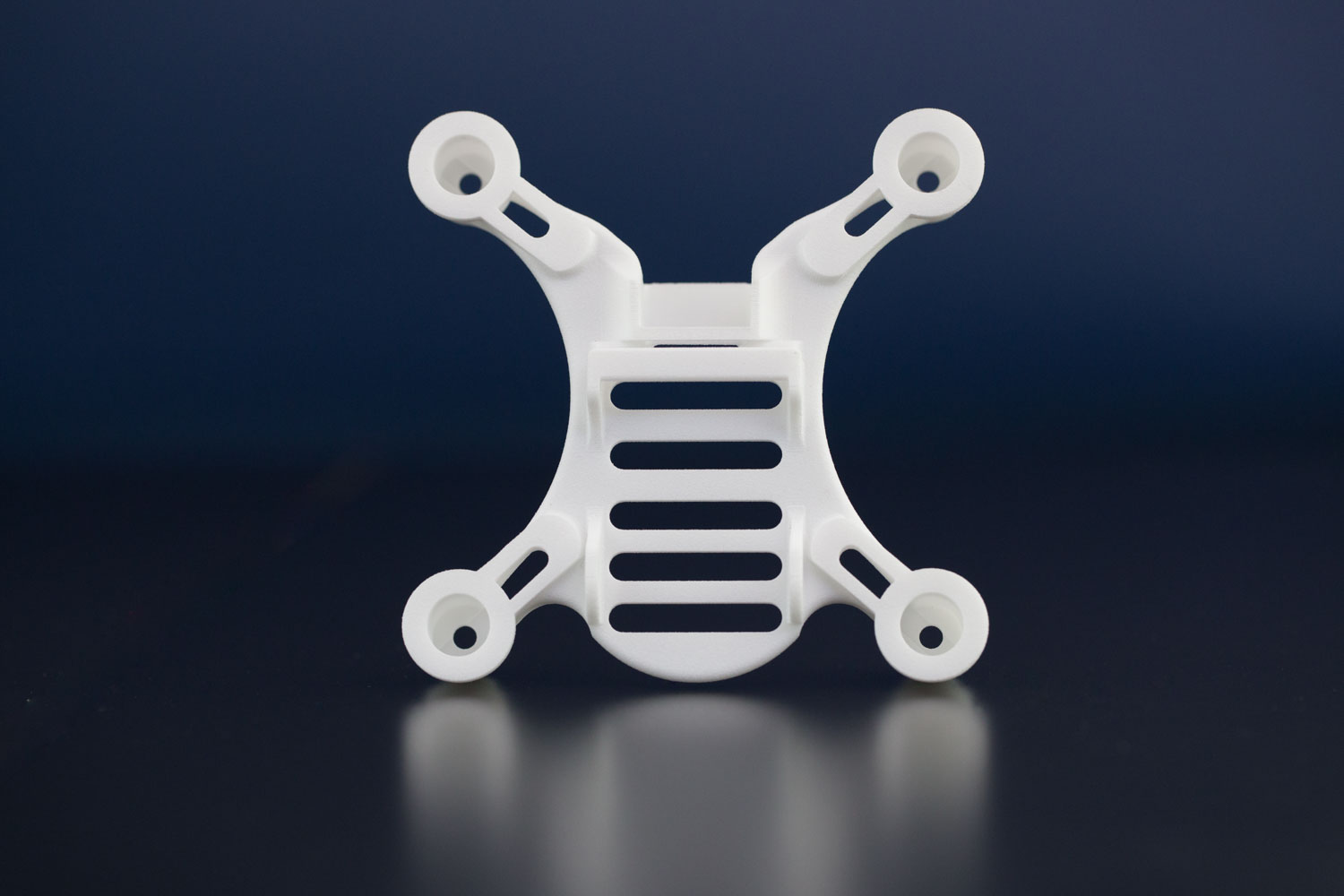
Material Finish for SLS Nylon
SLS Nylon is naturally white or off-white and can be painted and dyed easily. While the as-printed finish is an eggshell texture, parts can also be tumble polished to a smooth finish upon request.
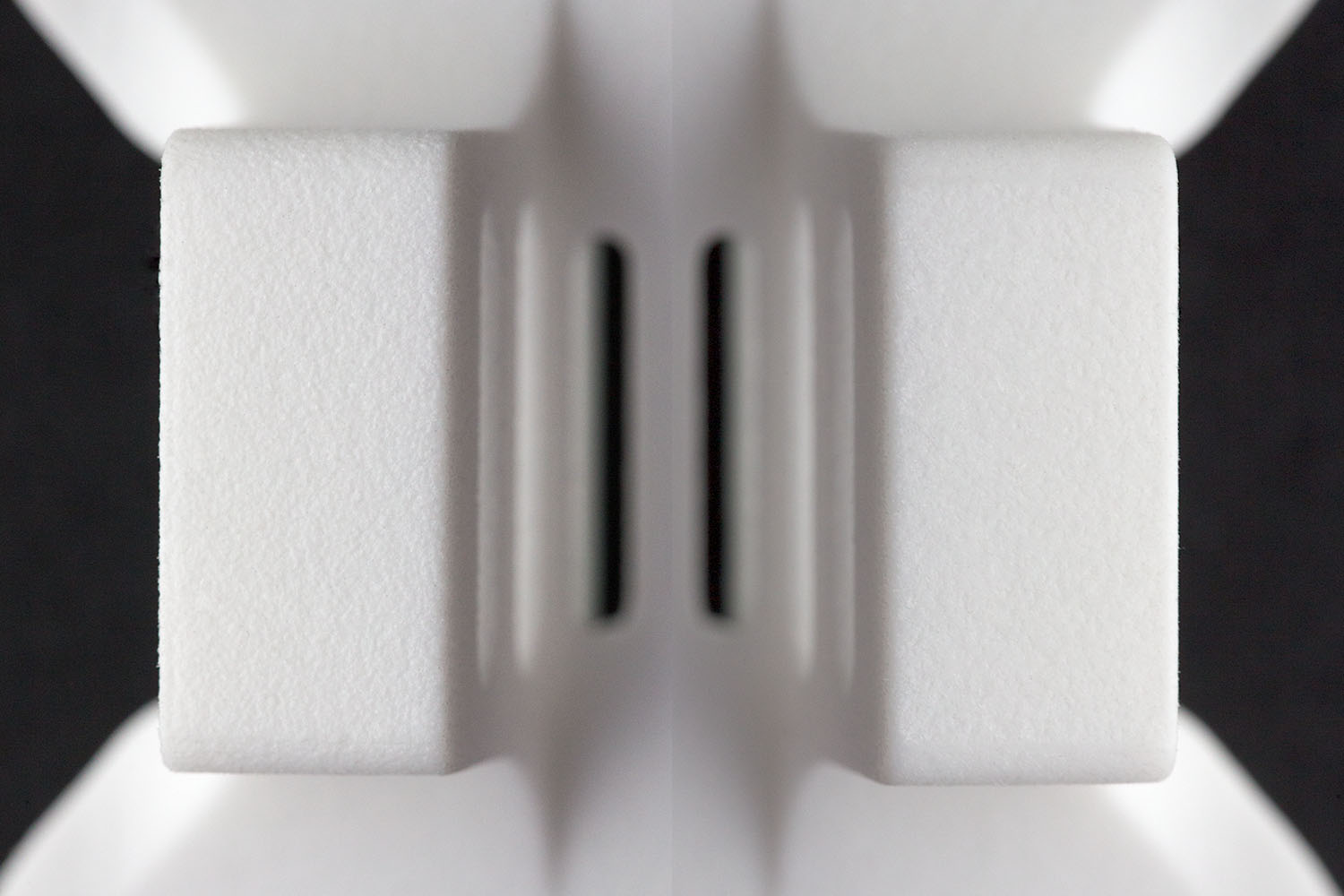
Note that the most economical order quantity will fill an entire layer of a build tray. For reference, Fictiv’s tray sizes are:
- 280 mm x 280 mm
- 340 mm x 340 mm
- 700 mm x 380 mm
CNC Milling / Turning for Manufacturing 10 – 100 Units
While it’s an expensive process for one-offs due to high setup costs, CNC machining is economical for small batch volumes. The unit cost usually starts leveling off above 50 units per batch, unless the initial tooling and setup costs are very high. The optimal batch volume is easy to determine — in your final quote request (Fictiv estimates are instant), you can always ask us for this information and we can break down your costs into setup and per-part cost. To get instant estimates + free DFM feedback for CNC machining, create your account here.
Material & Finish Options for CNC Machining
There are lots of material choices for CNC machining across metals and plastics, as well as finishing options for corrosion protection and cosmetic enhancement. You can find information for Fictiv’s range of CNC materials and finishing options, including high-res photography, videos, material datasheets, and design recommendations in the Fictiv Capabilities Guide.
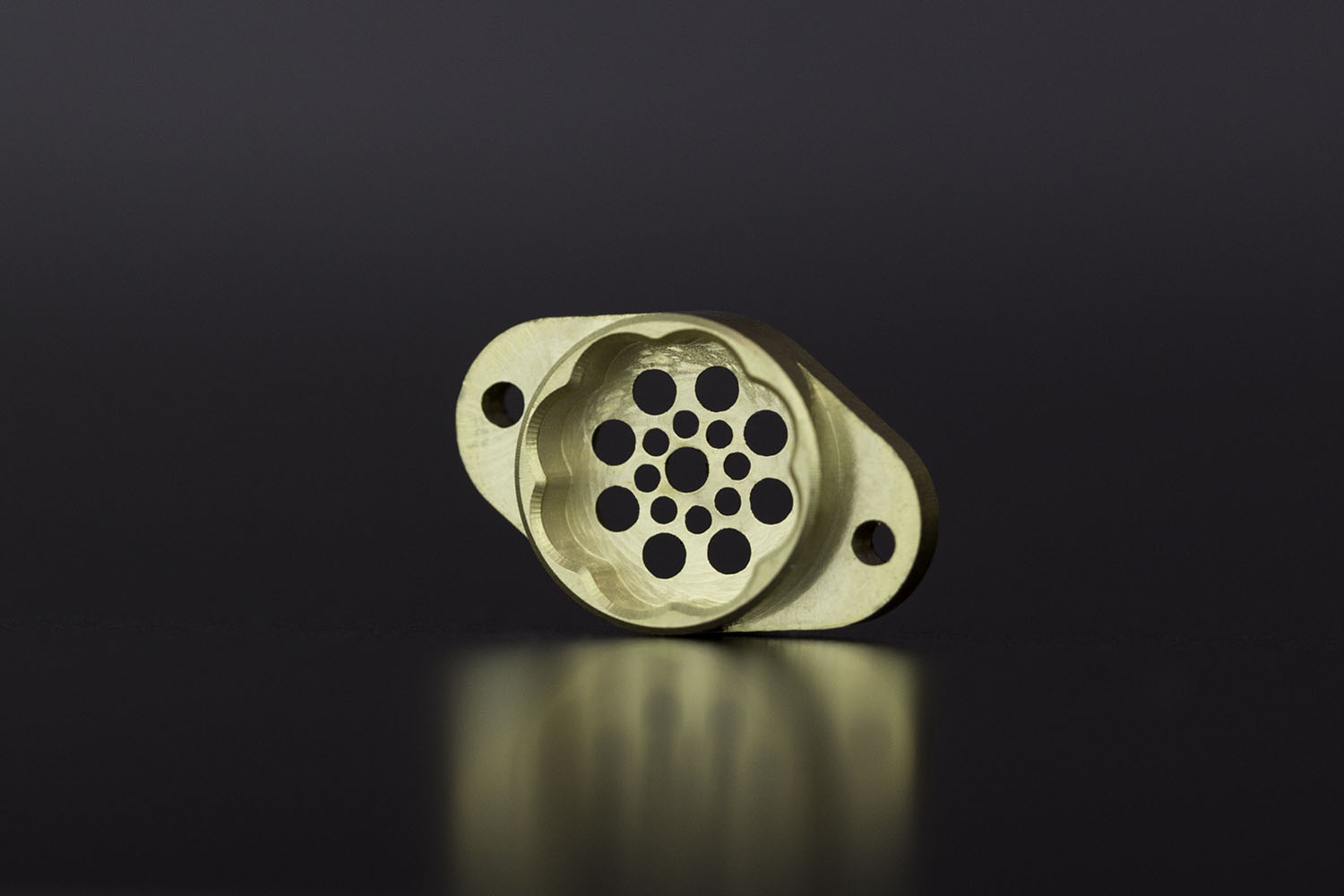
Cost Drivers for CNC Machining
Beyond the set up costs, the main cost drivers for CNC machining are:
- Material cost
- Cycle time (mostly comprised of cutting time)
To keep your unit cost down:
- Use low-cost materials such as aluminum or ABS plastic
- Minimize 3D contour machining
- Design your part to allow for the use of large cutters (put largest allowable radius on those inside corners!)
For more CNC machining design tips to help you reduce costs and translate design intent into machinable parts, check out our Engineer’s Guide to CNC Machining for Prototyping Hardware.
Urethane Casting for Manufacturing 10 – 100 Units
Urethane cast parts made from a silicone mold can often rival or exceed injection molding in quality, while being much more forgiving with geometry.
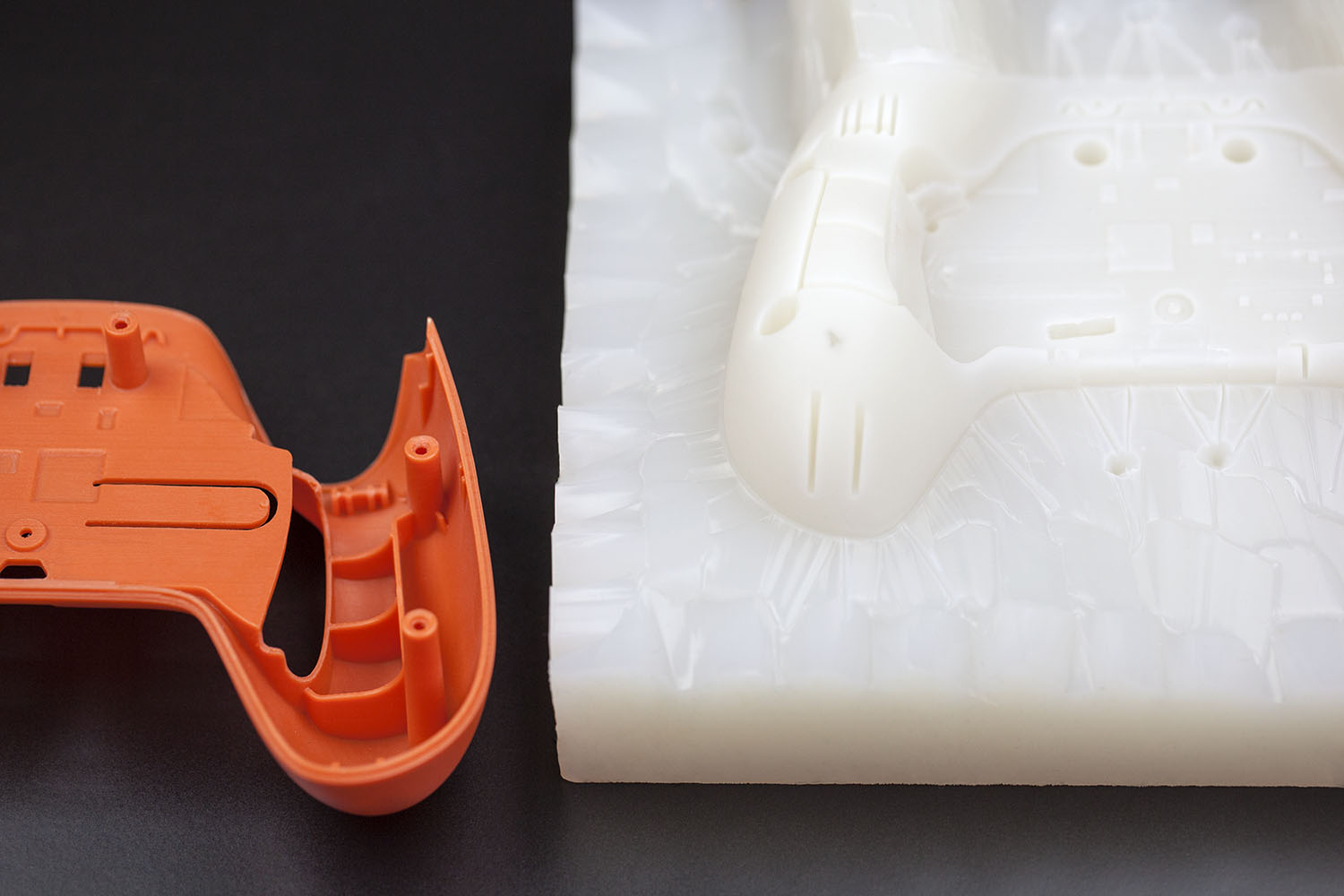
Material Options for Urethane Casting
Fictiv offers four materials for urethane casting (2 rigid plastics and 2 elastomers):
- ABS-Like Rigid Plastic – A general-purpose opaque material that simulates ABS thermoplastic. Good for most hardware product enclosures.
- Acrylic-Like Rigid Plastic – A stiff, transparent material for simulating acrylic (PMMA). Good for see-through applications such as light guides.
- Opaque Elastomer – Simulates all kinds of rubber-like materials such as TPE, TPU, and silicone rubber. Great for wearables, gaskets, and overmolds. Available from Shore 20A to Shore 90A in 10A increments.
- Waterclear Elastomer – Simulates all kinds of rubber-like materials such as TPE, TPU, and silicone rubber. Great for wearables, gaskets, and overmolds. Available from Shore 20A to Shore 90A in 10A increments.
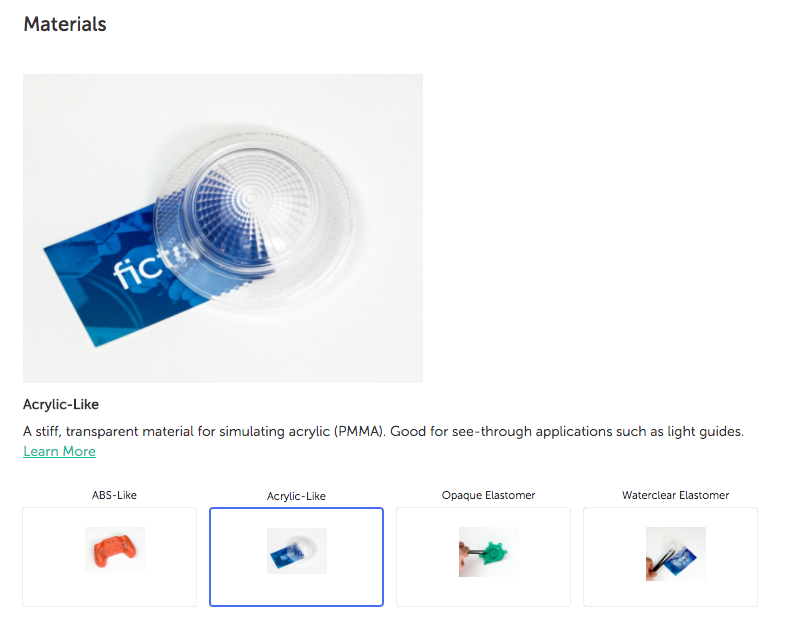
Design Considerations for Urethane Casting
If your parts are designed for injection molding, urethane casting is the perfect substitute at low volume. The most economic order quantities are in multiples of 20. For tips on how to design parts specifically for this process, check out Fictiv’s free Urethane Casting Design Guide.
Sheet Metal Forming for Manufacturing 10 – 100 Units
Sheet metal processes, such as punching and bending, are suitable for low volumes. To keep costs low, design with standard punch shapes in mind and avoid custom tooling.
Above 100 units, the pricing starts to make sense for custom punches and progressive die stamping.
Main Takeaways
There are lots of great fabrication options for manufacturing at low volumes from 10 – 100 units. If you still have questions, reach out to us at help@fictiv.com, or take advantage of our in-app chat feature, where you can chat live with a real engineer in < 5 mins.
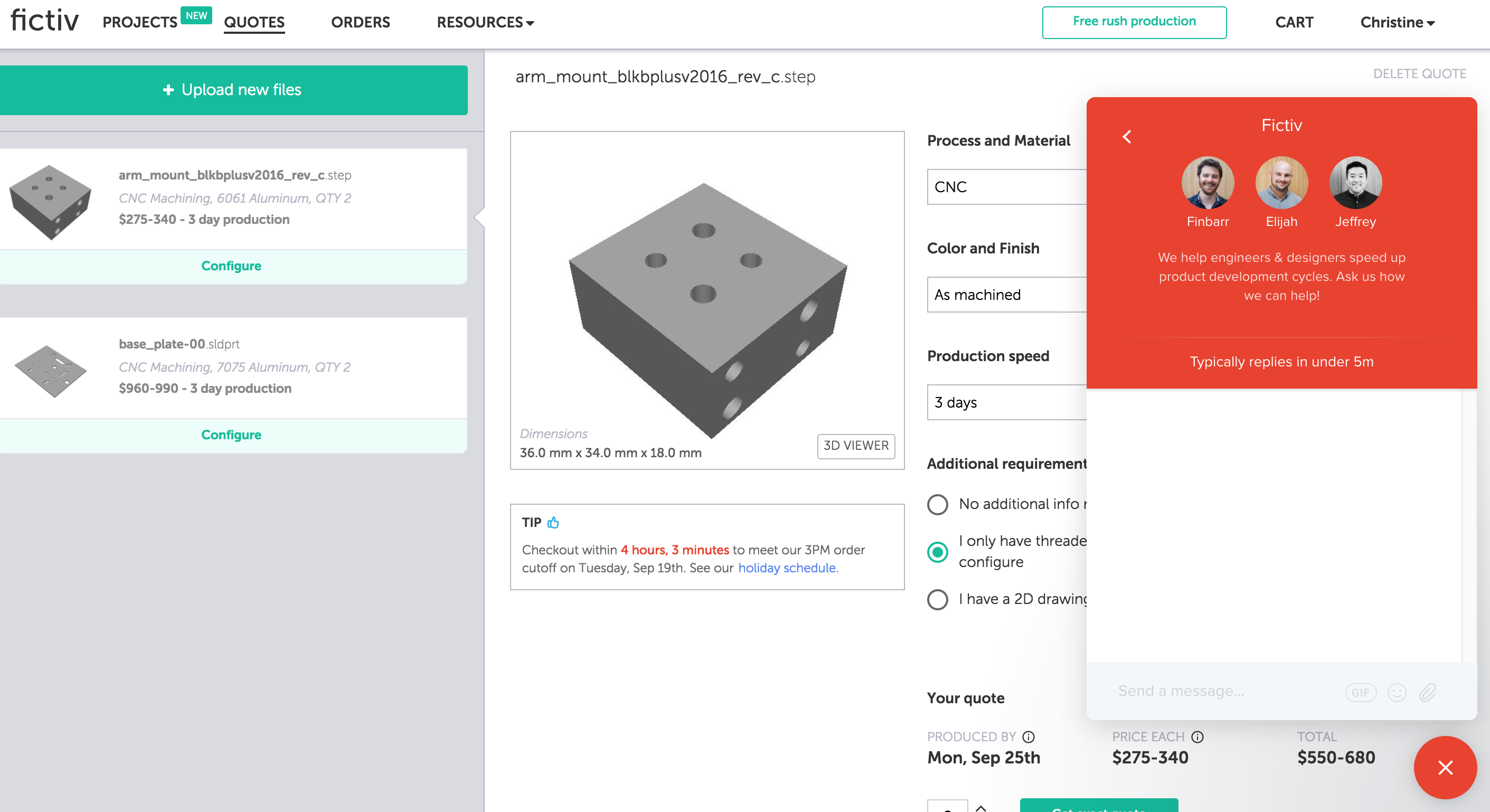